- お役立ち記事
- How to launch a “productivity improvement project” in which management and the field work together
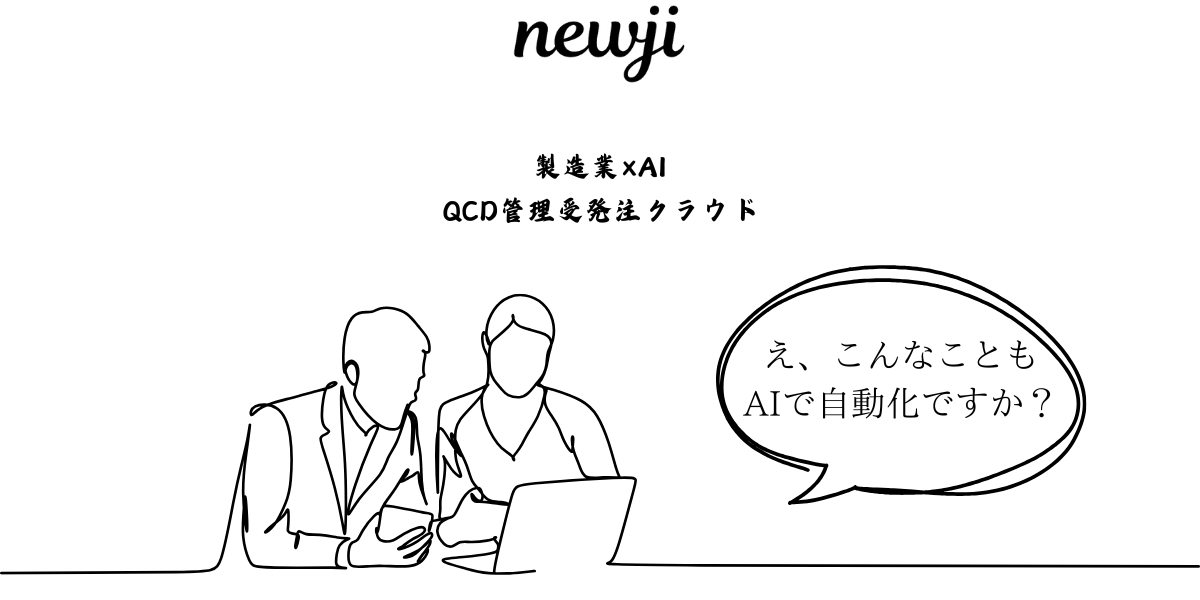
How to launch a “productivity improvement project” in which management and the field work together
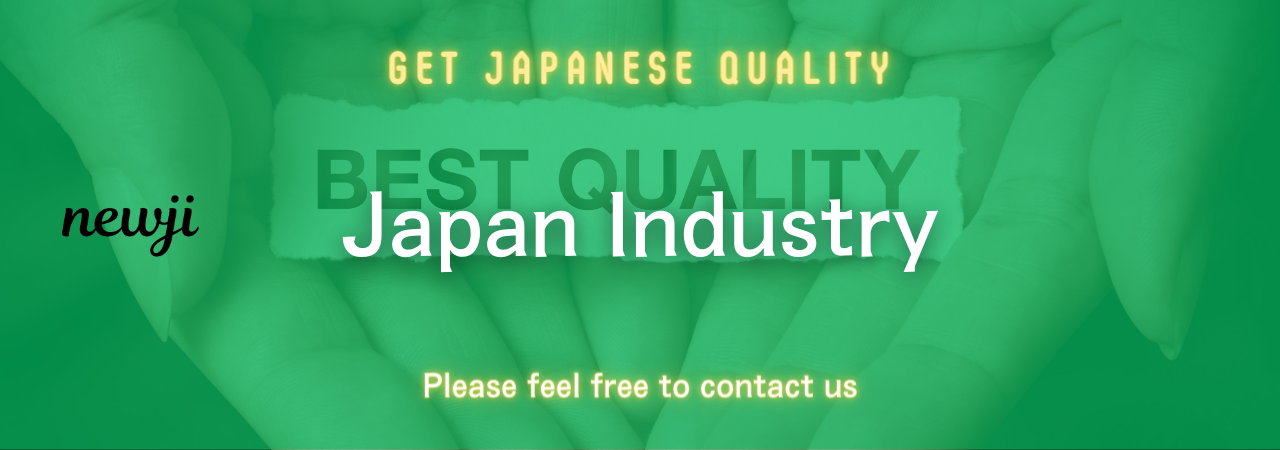
目次
Understanding Productivity Improvement Projects
Launching a productivity improvement project is an essential step for any organization aiming to enhance its efficiency and performance.
Such a project involves a collaborative effort between management and the workforce, creating a cohesive environment where everyone is aligned towards common goals.
The core objective is to streamline processes, reduce waste, and improve overall productivity.
To successfully launch such a project, it is crucial to understand what this entails and how both management and employees play significant roles.
The Role of Management
Management plays a pivotal role in initiating and guiding productivity improvement projects.
They are responsible for setting the overall goals and objectives of the project.
This includes identifying key areas where improvements are necessary and coordinating with various departments to ensure these goals are met.
Effective communication is vital—management should consistently convey the importance of the project and how it contributes to the organization’s success.
Engaging the Workforce
Engaging employees is essential for the success of any productivity improvement project.
The workforce often has firsthand experience with the company’s processes and can provide valuable insights into areas that need improvement.
Management should encourage employee participation, seeking their feedback and ideas.
By involving employees in decision-making, organizations can foster a sense of ownership and motivation, leading to a more effective implementation of improvement strategies.
Steps to Launch a Productivity Improvement Project
1. Clearly Define Objectives
The first step in launching a productivity improvement project is to clearly define the objectives.
What specific outcomes are you aiming for?
It’s essential to have measurable goals, such as reducing processing time by a certain percentage or increasing production output.
Having clear objectives ensures that everyone involved understands what the project is working towards.
2. Analyze Current Processes
Before making improvements, it’s important to thoroughly analyze current processes.
This involves mapping out existing workflows and identifying any bottlenecks or inefficiencies.
By understanding the current state of affairs, organizations can pinpoint exactly where changes are needed, enabling more targeted improvements.
3. Foster a Collaborative Culture
A successful productivity improvement project requires collaboration between management and staff.
Encouraging an open culture where ideas can be exchanged freely is crucial.
Facilitate regular meetings and brainstorming sessions where everyone can share suggestions and feedback.
Such collaboration ensures that solutions are practical and acceptable to all involved parties.
4. Implement the Right Tools and Techniques
Utilizing the right tools and techniques can greatly enhance productivity improvement efforts.
This may involve investing in technology that automates repetitive tasks or adopting methodologies like Lean or Six Sigma to streamline operations.
Choosing the appropriate tools and techniques depends on the specific needs of the organization and the nature of the project itself.
5. Monitor and Adjust
Once new strategies are implemented, continuous monitoring is essential.
Regularly gauge the success of the changes through set metrics and key performance indicators (KPIs).
If objectives are not being met, be prepared to adjust plans accordingly.
This adaptive approach helps in sustaining improvements and overcoming unforeseen challenges.
Overcoming Common Challenges
Resistance to Change
One of the most common challenges in productivity improvement projects is resistance to change.
Employees may be comfortable with existing processes and reluctant to adopt new methods.
To tackle this, it’s crucial to communicate the benefits of the project clearly and involve employees in the change process.
Offering training sessions can also smoothen the transition by boosting confidence in new methodologies.
Lack of Resources
Another potential challenge is a lack of resources, including time, manpower, and financial investment.
Management should ensure that adequate resources are allocated to the project to prevent it from stalling.
Prioritizing tasks and focusing on high-impact areas can also help in managing resource limitations effectively.
Maintaining Momentum
Keeping the momentum going is essential for the success of a productivity improvement project.
As initial enthusiasm wanes, it’s vital to keep the team engaged and motivated.
Providing regular updates on progress and celebrating successes can help maintain interest and commitment from all parties involved.
Conclusion
Launching a productivity improvement project requires thorough planning, clear communication, and genuine collaboration between management and the workforce.
By setting clear objectives, analyzing current processes, fostering collaboration, and effectively implementing changes, organizations can achieve significant improvements in productivity.
Recognizing potential challenges and addressing them proactively further ensures the success of the project.
Ultimately, a well-implemented productivity improvement project can drive an organization towards greater efficiency, competitiveness, and long-term success.
資料ダウンロード
QCD調達購買管理クラウド「newji」は、調達購買部門で必要なQCD管理全てを備えた、現場特化型兼クラウド型の今世紀最高の購買管理システムとなります。
ユーザー登録
調達購買業務の効率化だけでなく、システムを導入することで、コスト削減や製品・資材のステータス可視化のほか、属人化していた購買情報の共有化による内部不正防止や統制にも役立ちます。
NEWJI DX
製造業に特化したデジタルトランスフォーメーション(DX)の実現を目指す請負開発型のコンサルティングサービスです。AI、iPaaS、および先端の技術を駆使して、製造プロセスの効率化、業務効率化、チームワーク強化、コスト削減、品質向上を実現します。このサービスは、製造業の課題を深く理解し、それに対する最適なデジタルソリューションを提供することで、企業が持続的な成長とイノベーションを達成できるようサポートします。
オンライン講座
製造業、主に購買・調達部門にお勤めの方々に向けた情報を配信しております。
新任の方やベテランの方、管理職を対象とした幅広いコンテンツをご用意しております。
お問い合わせ
コストダウンが利益に直結する術だと理解していても、なかなか前に進めることができない状況。そんな時は、newjiのコストダウン自動化機能で大きく利益貢献しよう!
(Β版非公開)