- お役立ち記事
- How to Manufacture Strong, Durable Products Using ABS Resin
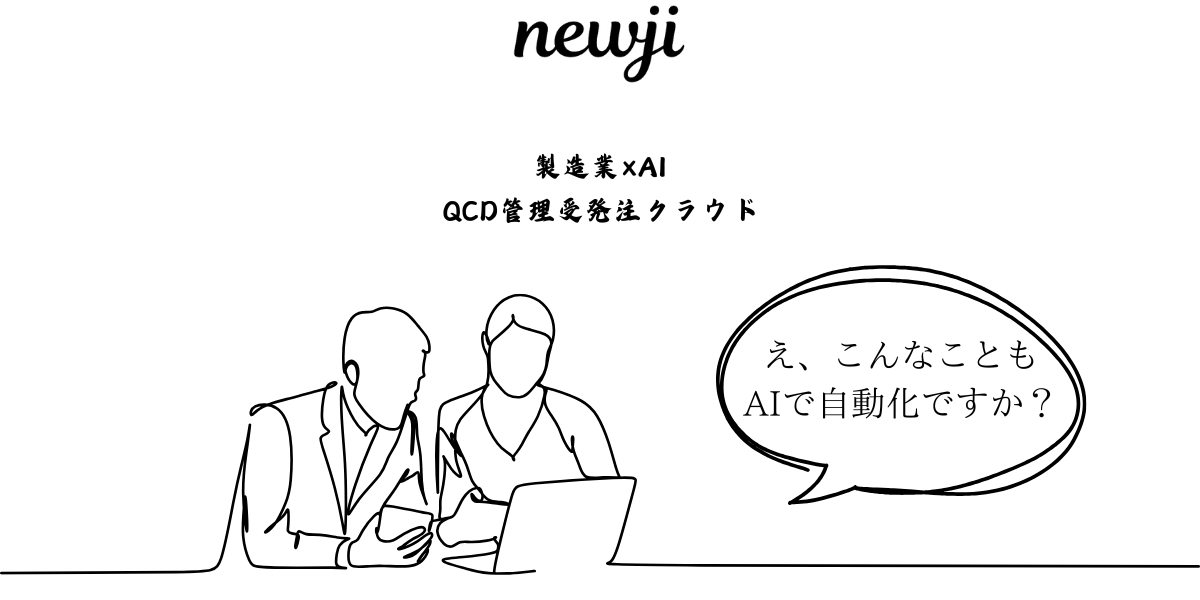
How to Manufacture Strong, Durable Products Using ABS Resin
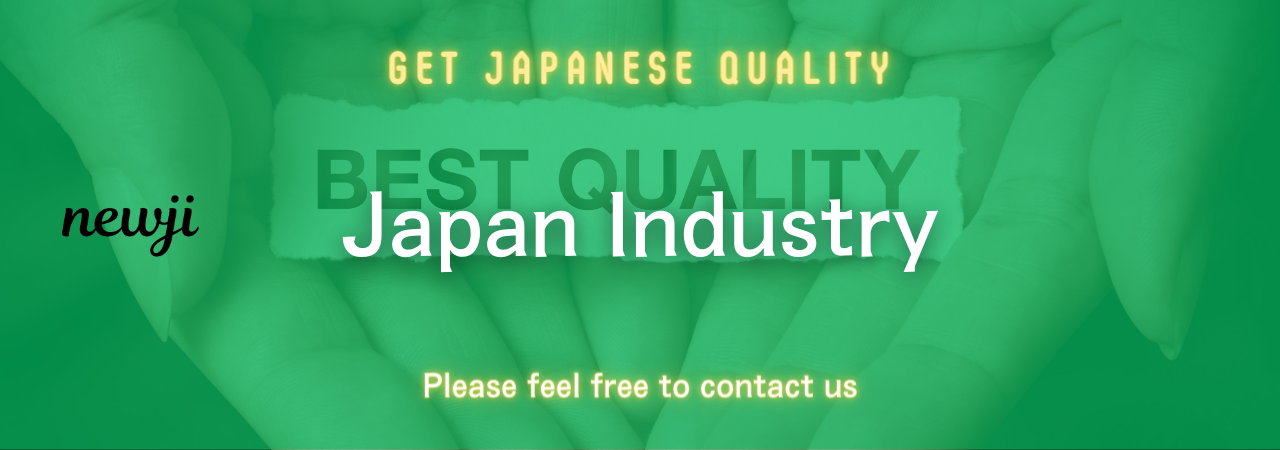
目次
Understanding ABS Resin
ABS (Acrylonitrile Butadiene Styrene) resin is a popular thermoplastic polymer known for its strength, durability, and versatility.
It is commonly used in a variety of applications, including automotive parts, consumer electronics, and household goods.
The versatility of ABS makes it a preferred choice in manufacturing, as it can be easily molded and customized for specific needs.
Understanding the properties and potential of ABS resin is crucial for creating strong and durable products.
Characteristics of ABS Resin
There are several characteristics that make ABS resin an attractive material for product manufacturing.
Firstly, it offers high impact resistance, meaning it can withstand external forces without breaking.
This property is essential for products that need to endure wear and tear.
Moreover, ABS is known for its toughness, making it less likely to crack under stress.
The material also presents good thermal stability, maintaining its integrity across a wide range of temperatures, which is ideal for both indoor and outdoor use.
Additionally, the smooth finish and surface texture make it suitable for high-quality, durable consumer goods.
ABS Resin Manufacturing Process
The manufacturing process of ABS resin involves three main components: acrylonitrile, butadiene, and styrene.
These components are polymerized to create ABS resin through a process that combines their best properties.
Polymerization
Acrylonitrile provides chemical resistance and heat stability, butadiene adds tough impact resistance, and styrene contributes rigidity and gloss.
The polymerization involves emulsification, suspension, or continuous mass polymerization.
In the emulsification process, the components are suspended in water and stirred to form a latex.
For suspension polymerization, the components are mixed with a suspending agent, while continuous mass polymerization involves continuous thermal and mechanical mixing of the components.
Molding and Manufacturing
Once the ABS resin is polymerized, it can be molded into the desired shape using various methods.
Injection molding is a common technique where molten ABS is injected into a mold cavity to create complex shapes.
This method is ideal for mass production and ensures consistency in quality.
Alternatively, extrusion involves pushing the molten resin through a die to create long shapes such as pipes or sheets.
Die cutting and vacuum forming can also be used for shaping ABS resin, depending on specific product requirements.
Advantages of Using ABS Resin
The benefits of using ABS resin in product manufacturing are considerable.
One of the primary advantages is the ease of manufacturing.
The material can be easily processed at relatively low temperatures and is suitable for a variety of molding techniques.
This flexibility allows manufacturers to produce large quantities at a reduced cost and with minimal waste.
Another advantage is its ability to be recycled, positioning it as a sustainable option within the manufacturing industry.
Product Applications
ABS resin is used in a diverse array of products, highlighting its adaptability.
In the automotive industry, it is employed for making dashboards, wheel covers, and other interior parts due to its high impact resistance and lightweight properties.
For consumer electronics, ABS is commonly found in cameras, keyboards, and computer equipment, offering a balance of strength and aesthetics.
Household appliances like vacuum cleaners, kitchen utensils, and storage containers also benefit from the resilient nature of ABS.
Tips for Working with ABS Resin
To maximize the potential of ABS resin, it is essential to keep certain tips in mind during the manufacturing process.
Quality Control and Testing
Ensuring the quality of ABS resin is a critical consideration.
Proper testing should be conducted to ascertain the material’s conformity to required standards, checking for any defects in polymerization.
Quality control processes need to include thermal and impact resistance testing to guarantee the durability of the end product.
Designers and engineers should also examine any post-production issues to make iterative improvements.
Considering Environmental Factors
It is crucial to consider environmental factors when manufacturing with ABS resin.
While ABS is not biodegradable, its recyclability plays a pivotal role in sustainable practices.
Implementing recycling programs that enable reusing or reformulating ABS can reduce environmental impact.
Also, minimizing production waste by optimizing mold designs or utilizing precise cutting techniques can enhance the eco-friendly attributes of the production cycle.
Conclusion
Manufacturing strong, durable products with ABS resin involves understanding its intrinsic properties and applying them correctly during the production process.
With its impact resistance, thermal stability, and ease in molding, ABS resin provides diverse opportunities across several industries.
By incorporating quality control, recycling options, and attentive processing techniques, manufacturers can create high-quality, long-lasting products.
If harnessed effectively, ABS resin will continue to be a pivotal material, adapting to the evolving needs and innovations within the manufacturing landscape.
資料ダウンロード
QCD調達購買管理クラウド「newji」は、調達購買部門で必要なQCD管理全てを備えた、現場特化型兼クラウド型の今世紀最高の購買管理システムとなります。
ユーザー登録
調達購買業務の効率化だけでなく、システムを導入することで、コスト削減や製品・資材のステータス可視化のほか、属人化していた購買情報の共有化による内部不正防止や統制にも役立ちます。
NEWJI DX
製造業に特化したデジタルトランスフォーメーション(DX)の実現を目指す請負開発型のコンサルティングサービスです。AI、iPaaS、および先端の技術を駆使して、製造プロセスの効率化、業務効率化、チームワーク強化、コスト削減、品質向上を実現します。このサービスは、製造業の課題を深く理解し、それに対する最適なデジタルソリューションを提供することで、企業が持続的な成長とイノベーションを達成できるようサポートします。
オンライン講座
製造業、主に購買・調達部門にお勤めの方々に向けた情報を配信しております。
新任の方やベテランの方、管理職を対象とした幅広いコンテンツをご用意しております。
お問い合わせ
コストダウンが利益に直結する術だと理解していても、なかなか前に進めることができない状況。そんな時は、newjiのコストダウン自動化機能で大きく利益貢献しよう!
(Β版非公開)