- お役立ち記事
- How to Manufacture Transparent Products Using Polycarbonate
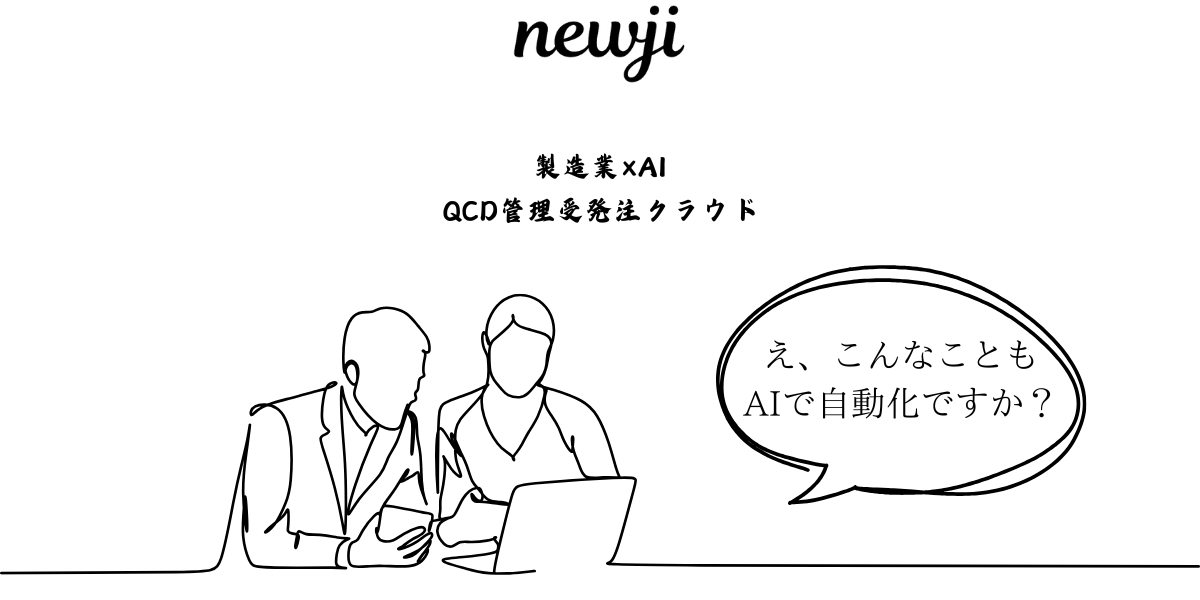
How to Manufacture Transparent Products Using Polycarbonate
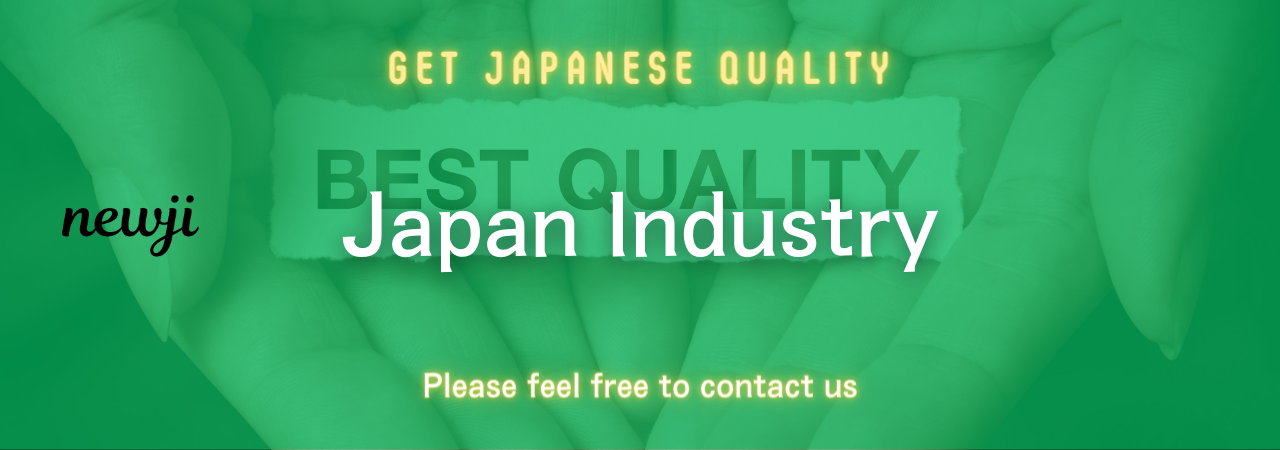
目次
Introduction to Polycarbonate
Polycarbonate is a versatile and durable plastic widely used in manufacturing transparent products.
Its unique properties make it an ideal material for applications requiring clarity and strength, from eyewear lenses to electronic enclosures.
Understanding how to manufacture transparent products using polycarbonate begins with knowing its chemical and physical characteristics that set it apart from other plastics.
Polycarbonate is a type of thermoplastic polymer known for its strength, impact resistance, and transparency.
It is lightweight yet withstands significant stress, offering a perfect balance of aesthetics and functionality.
These features make it highly desirable in industries such as construction, automotive, and consumer electronics.
Choosing the Right Grade of Polycarbonate
Selecting the appropriate grade of polycarbonate is the first critical step in manufacturing transparent products.
Polycarbonate is available in various grades, each tailored for specific applications and performance requirements.
For transparent products, manufacturers often choose optical grade or UV-stabilized polycarbonate.
Optical grade polycarbonate is specifically designed to offer high optical clarity, reducing distortion when light passes through.
It is typically used in applications like eyewear lenses, camera lenses, and other precision optical products.
UV-stabilized polycarbonate is ideal for outdoor applications where products may be exposed to sunlight.
This grade contains additives that enhance its resistance to UV radiation, preventing yellowing and degradation.
Selecting the right grade ensures that the product meets both the visual and functional demands of its intended use.
Design Considerations for Transparent Products
When designing transparent products using polycarbonate, several factors must be considered to optimize performance and aesthetics.
First, think about the shape and thickness of the product.
The design should accommodate the need for transparency without compromising on structural integrity.
Thickness plays a crucial role in both clarity and strength.
Although polycarbonate is robust, thicker materials provide better impact resistance.
However, excessive thickness can lead to optical distortions, so finding a balance is essential.
Additionally, surface finishes can influence transparency.
A smooth finish is generally preferred for maximum clarity, while certain textures can diffuse light and create an attractive aesthetic.
Molding and Forming Techniques
One of the significant advantages of polycarbonate is its ease of molding and forming, allowing manufacturers to create complex shapes and detailed designs.
Several techniques are commonly used to process polycarbonate for transparent applications.
Injection Molding
Injection molding is a popular method for manufacturing transparent products with polycarbonate.
It involves injecting molten polycarbonate into a mold cavity, where it cools and solidifies.
This process is excellent for high-volume production of precision parts, such as lenses or transparent enclosures.
Extrusion
Extrusion is another technique where polycarbonate is melted and forced through a die to create long, continuous shapes like sheets or tubes.
These extruded products can be further refined or cut to length for various applications, such as windows or barriers.
Thermoforming
Thermoforming involves heating a flat sheet of polycarbonate until it becomes pliable, then stretching or molding it over a shaped form.
This method is ideal for producing large, lightweight transparent items like skylights or protective covers.
Finishing and Post-Processing
After forming, the final touches are critical to ensuring the transparency and quality of the product.
Finishing processes can include annealing, which involves slowly heating and cooling the product to relieve internal stresses, reducing the risk of warping or cracking.
Polishing can also enhance clarity.
Manual or automated polishing removes surface irregularities, providing a smooth, highly transparent finish suitable for optical applications.
Coatings and treatments may be applied for additional benefits such as anti-scratch properties, anti-fog, or UV protection.
These enhancements ensure the longevity and usability of the product in its intended environment.
Quality Control and Testing
Maintaining high quality is vital in production, especially for transparent products where defects are more noticeable.
Quality control ensures consistency and reliability, with several tests typically performed during and after manufacturing.
Visual inspections identify surface defects like scratches, bubbles, or warps that could compromise transparency.
Optical tests measure light transmission and distortion, ensuring the product meets the required standards for visual clarity.
Mechanical tests can assess the product’s impact resistance, tensile strength, and thermal stability.
By comprehensively evaluating the product’s performance, manufacturers can ensure it meets both industry standards and customer expectations.
Applications of Transparent Polycarbonate Products
The versatility of polycarbonate makes it suitable for a wide range of applications.
In the automotive industry, polycarbonate is used for headlamp lenses and interior panels, benefiting from its impact resistance and clarity.
In construction, polycarbonate serves as an excellent alternative to glass for skylights, windows, and insulating panels, offering superior impact resistance and thermal insulation.
Moreover, the electronics industry uses polycarbonate for protective housings and covers due to its durability and aesthetic transparency.
Conclusion
Manufacturing transparent products from polycarbonate combines material selection, precise design, and expert processing techniques.
Choosing the correct grade of polycarbonate and thoughtfully designing the product lay the groundwork for success.
Adopting suitable molding and forming methods, along with attentive finishing and quality control, further enhances the final product’s performance and visual appeal.
With these steps, polycarbonate continues to be a material of choice for transparent applications across numerous industries, meeting the demand for both aesthetic and functional high-performance plastics.
資料ダウンロード
QCD調達購買管理クラウド「newji」は、調達購買部門で必要なQCD管理全てを備えた、現場特化型兼クラウド型の今世紀最高の購買管理システムとなります。
ユーザー登録
調達購買業務の効率化だけでなく、システムを導入することで、コスト削減や製品・資材のステータス可視化のほか、属人化していた購買情報の共有化による内部不正防止や統制にも役立ちます。
NEWJI DX
製造業に特化したデジタルトランスフォーメーション(DX)の実現を目指す請負開発型のコンサルティングサービスです。AI、iPaaS、および先端の技術を駆使して、製造プロセスの効率化、業務効率化、チームワーク強化、コスト削減、品質向上を実現します。このサービスは、製造業の課題を深く理解し、それに対する最適なデジタルソリューションを提供することで、企業が持続的な成長とイノベーションを達成できるようサポートします。
オンライン講座
製造業、主に購買・調達部門にお勤めの方々に向けた情報を配信しております。
新任の方やベテランの方、管理職を対象とした幅広いコンテンツをご用意しております。
お問い合わせ
コストダウンが利益に直結する術だと理解していても、なかなか前に進めることができない状況。そんな時は、newjiのコストダウン自動化機能で大きく利益貢献しよう!
(Β版非公開)