- お役立ち記事
- How to review suppliers to reduce costs throughout the supply chain
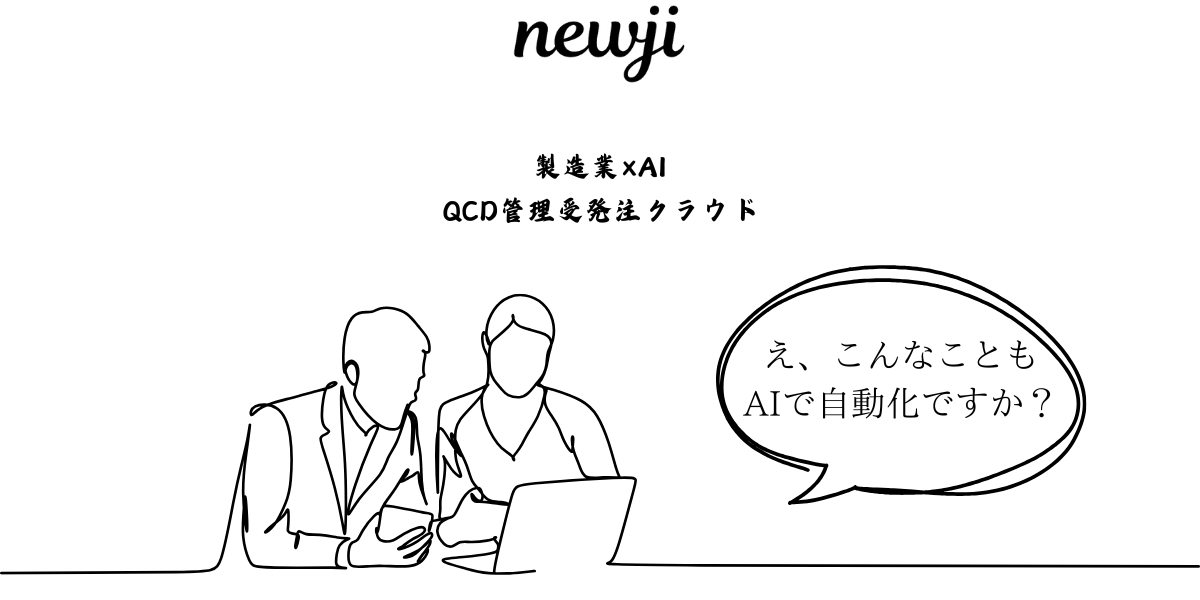
How to review suppliers to reduce costs throughout the supply chain
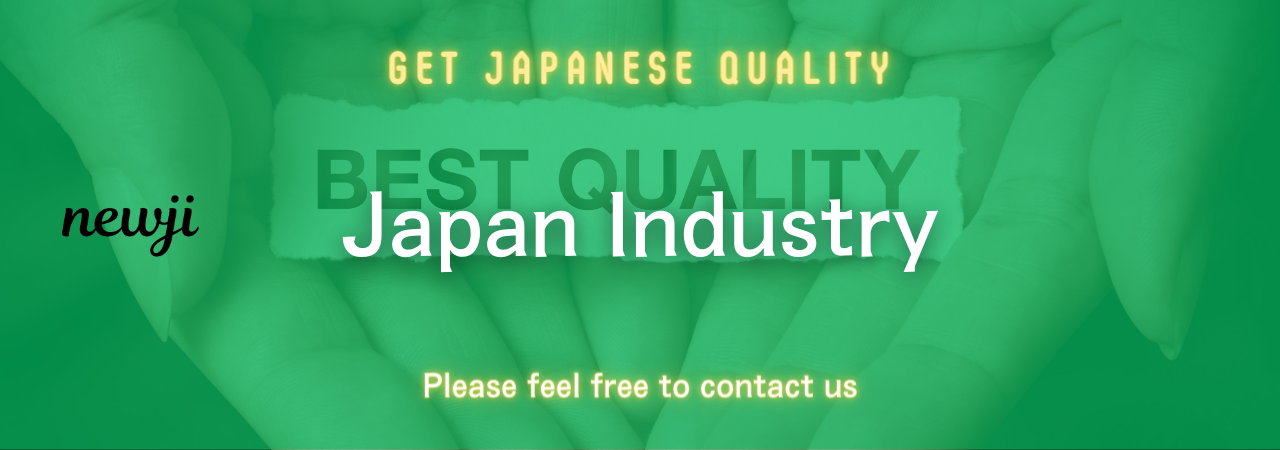
目次
Understanding the Importance of Supplier Reviews
In any business, maintaining a streamlined supply chain is crucial for reducing costs and ensuring that products or services reach customers efficiently.
One of the key components of an effective supply chain is the supplier.
By thoroughly reviewing suppliers, businesses can identify inefficiencies, negotiate better terms, and ultimately reduce overall costs.
This process helps businesses remain competitive and improve their bottom line.
What Is a Supplier Review?
A supplier review is a systematic assessment of a supplier’s performance and capabilities.
The goal is to understand the supplier’s ability to deliver quality products or services in a timely and cost-effective manner.
The review process can involve evaluating various aspects, such as delivery times, pricing, product quality, customer service, and compliance with agreements.
Regular supplier reviews can help businesses identify potential issues before they escalate, ensuring smoother operations.
Steps to Effectively Review Suppliers
1. Define Your Criteria
The first step in reviewing suppliers is to define the criteria that will guide the assessment process.
This includes identifying what aspects of the supplier relationship are most important to your business.
Consider factors like delivery reliability, product quality, pricing, communication, and any other attributes relevant to your operations.
Having a clear set of criteria will help you evaluate suppliers consistently and objectively.
2. Gather Relevant Data
Collecting data on your suppliers is the next crucial step.
Look at past performance records, including delivery times, lead times, and any instances of non-compliance.
Customer feedback and quality audits can also provide valuable insights into supplier performance.
Analyze this data to gain a comprehensive understanding of each supplier’s strengths and weaknesses.
3. Conduct Supplier Evaluations
With your criteria in place and data gathered, it’s time to conduct supplier evaluations.
This can involve site visits, discussions with supplier representatives, and reviewing documentation.
Engaging in direct communication with suppliers can reveal their commitment to meeting your needs and any challenges they may face.
During evaluations, encourage transparency and openness, as this will foster a more collaborative relationship.
Strategies for Cost Reduction Through Supplier Reviews
1. Negotiate Better Terms
Once the supplier reviews are complete, use the information to negotiate better terms.
This may involve seeking discounts, more favorable payment terms, or volume-based pricing.
Having a clear understanding of the supplier’s performance and market dynamics can strengthen your negotiating position.
2. Consolidate Your Supplier Base
Another strategy is to consolidate your supplier base, working with fewer suppliers to meet more of your needs.
This can lead to better pricing, as larger order volumes often result in discounts.
Additionally, streamlined communication and logistics with a smaller set of suppliers can reduce administrative costs.
3. Encourage Supplier Efficiency
Encouraging suppliers to improve their processes and efficiency can also lead to cost savings.
Collaborate with suppliers to explore areas where they can cut costs while maintaining quality.
This might include adopting more cost-effective materials, improving manufacturing processes, or investing in technology.
4. Leverage Supplier Innovation
Suppliers often bring innovation to the table, offering new products or services that can provide a competitive edge.
By maintaining open channels of communication and encouraging innovation, your business can benefit from new ideas that may reduce costs.
Embrace supplier suggestions for changes that could enhance the efficiency of the supply chain.
Challenges in Supplier Reviews
1. Resistance to Change
One of the challenges in conducting supplier reviews is resistance to change, both internally and externally.
Some suppliers may be resistant to altering their practices, while internal teams may be hesitant to change longstanding supplier relationships.
To overcome this, emphasize the benefits of the review process and how it contributes to cost reduction and overall business improvement.
2. Resource Constraints
Conducting thorough supplier reviews requires resources, such as time and manpower, which can strain smaller businesses.
To mitigate this, prioritize reviews based on the supplier’s impact on your business operations.
Focus efforts on critical suppliers first and gradually extend the review process to others.
In some cases, investing in supplier management software can streamline the review process.
3. Maintaining Objectivity
Ensuring objectivity during supplier reviews is essential for fair evaluations.
Biases, whether personal or organizational, can skew assessments and lead to misguided decisions.
To maintain objectivity, rely on data-driven evaluations and thoroughly documented criteria.
Involving multiple stakeholders in the review process can also provide balanced perspectives.
The Long-Term Benefits of Regular Supplier Reviews
Conducting regular supplier reviews offers long-term benefits beyond immediate cost reductions.
By fostering collaborative and transparent supplier relationships, businesses create a foundation for mutual growth and innovation.
Enhanced supplier performance leads to improved service or product quality, ultimately benefiting the end customer.
Moreover, a robust supplier base can provide businesses with more flexibility and stability in the face of market fluctuations.
In conclusion, supplier reviews are a vital aspect of managing an efficient and cost-effective supply chain.
Carefully assessing suppliers, negotiating better terms, and encouraging innovation can significantly reduce costs.
Despite inherent challenges, committing to a systematic review process brings long-term advantages, ensuring sustained competitiveness in the marketplace.
資料ダウンロード
QCD調達購買管理クラウド「newji」は、調達購買部門で必要なQCD管理全てを備えた、現場特化型兼クラウド型の今世紀最高の購買管理システムとなります。
ユーザー登録
調達購買業務の効率化だけでなく、システムを導入することで、コスト削減や製品・資材のステータス可視化のほか、属人化していた購買情報の共有化による内部不正防止や統制にも役立ちます。
NEWJI DX
製造業に特化したデジタルトランスフォーメーション(DX)の実現を目指す請負開発型のコンサルティングサービスです。AI、iPaaS、および先端の技術を駆使して、製造プロセスの効率化、業務効率化、チームワーク強化、コスト削減、品質向上を実現します。このサービスは、製造業の課題を深く理解し、それに対する最適なデジタルソリューションを提供することで、企業が持続的な成長とイノベーションを達成できるようサポートします。
オンライン講座
製造業、主に購買・調達部門にお勤めの方々に向けた情報を配信しております。
新任の方やベテランの方、管理職を対象とした幅広いコンテンツをご用意しております。
お問い合わせ
コストダウンが利益に直結する術だと理解していても、なかなか前に進めることができない状況。そんな時は、newjiのコストダウン自動化機能で大きく利益貢献しよう!
(Β版非公開)