- お役立ち記事
- How to streamline purchasing operations by introducing a supplier management system
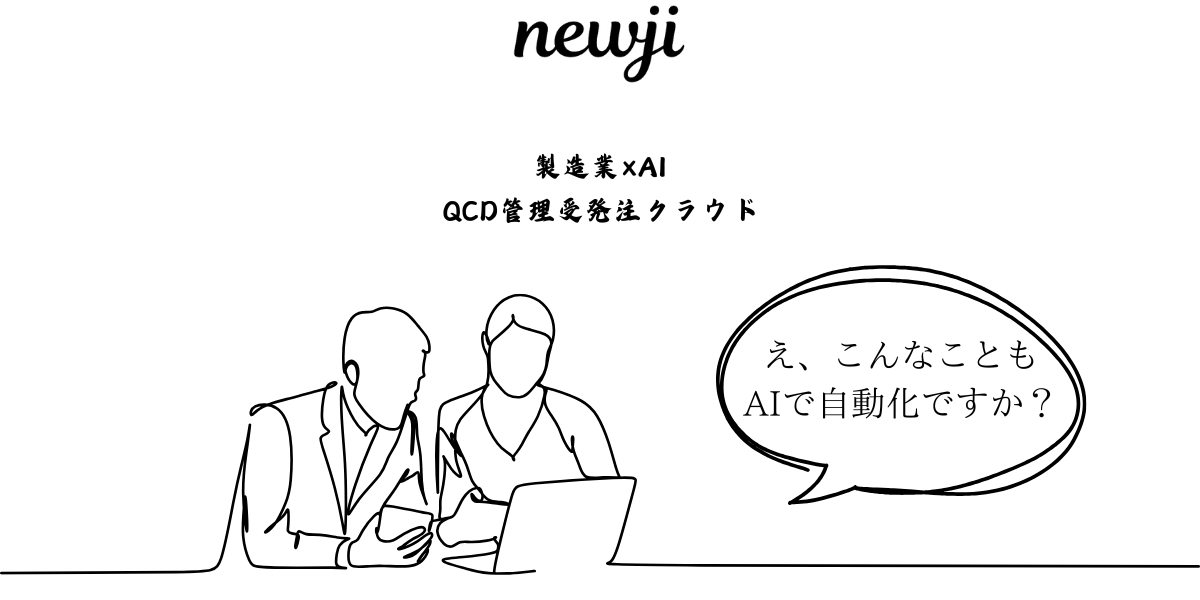
How to streamline purchasing operations by introducing a supplier management system
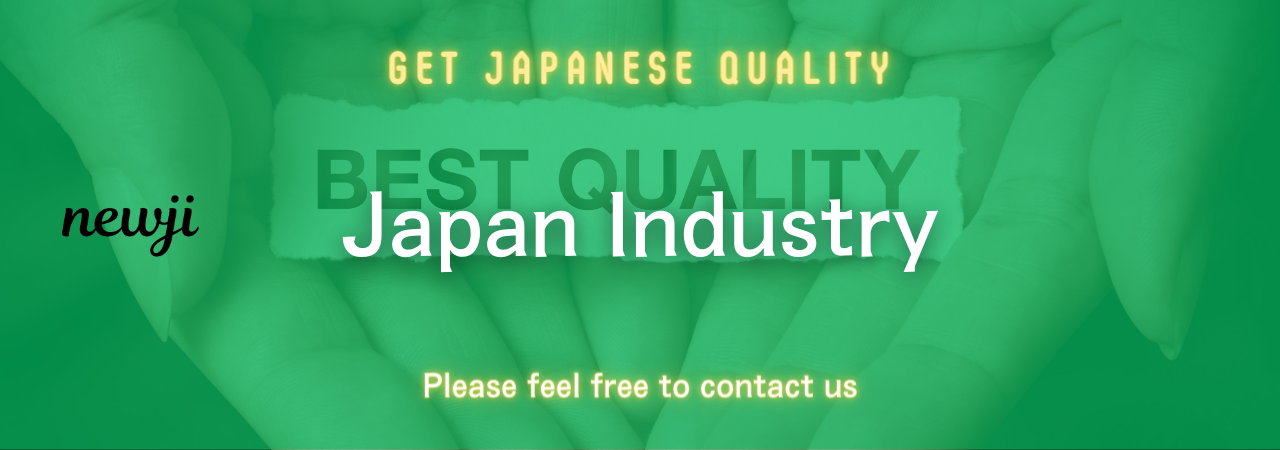
目次
Understanding Supplier Management Systems
Supplier management systems are essential tools for businesses looking to streamline their purchasing operations.
These systems offer a digital solution for managing and maintaining relationships with suppliers, ensuring that procurement processes are efficient and effective.
By implementing a supplier management system, companies can track supplier performance, manage contracts, and oversee all aspects of their purchasing operations from one centralized location.
This not only improves accountability but also optimizes the supply chain for better results.
Key Features of a Supplier Management System
A supplier management system typically includes several key features designed to enhance purchasing operations.
Key aspects include supplier database management, which allows businesses to store and categorize all necessary supplier information in one place.
This feature makes it easy to evaluate suppliers based on their performance and capabilities.
Additionally, contract management ensures that all agreements with suppliers are properly documented and updated in a timely manner.
Another important feature is supplier performance tracking.
This enables businesses to evaluate how well suppliers are meeting the terms of their contracts, including delivery times and product quality.
The system may also include risk management tools to identify potential issues before they become significant problems.
By analyzing supplier data, businesses can proactively address any disruptions in their supply chain.
Benefits of Implementing a Supplier Management System
Businesses stand to gain several advantages from introducing a supplier management system into their purchasing operations.
One of the primary benefits is improved efficiency.
With all supplier-related information centralized, teams can access data quickly, reducing the time spent on administrative tasks and improving decision-making processes.
Cost savings are another significant benefit.
By having a clearer view of all procurement activities, companies can identify opportunities for cost reductions, negotiate better terms with suppliers, and avoid overstocking or shortages.
These systems also enable better compliance with industry regulations because they provide a comprehensive overview of supplier certifications and qualifications.
Improved supplier relationships are a further advantage.
With a management system in place, businesses can communicate more effectively with their suppliers. This transparency often leads to stronger partnerships and improved outcomes.
Choosing the Right Supplier Management System
Selecting an appropriate supplier management system involves considering several factors.
First, assess your specific business needs.
Determine what problems you need the system to solve, and look for solutions that address these requirements directly.
Scalability is an important consideration as well; ensure that the system can grow with your business and accommodate future needs.
Another factor to consider is integration capabilities.
A supplier management system should integrate seamlessly with your existing enterprise resource planning (ERP) or other business systems.
This ensures a smooth flow of data across different departments and minimizes disruption during implementation.
Ease of use is crucial for successful adoption.
The system should be user-friendly, with intuitive navigation and clear instructions.
Training and support offerings from the vendor are also important to consider, as they can influence how quickly your teams can become proficient in using the system.
Steps to Implement a Supplier Management System
Implementing a supplier management system involves a few essential steps.
Start by conducting a needs assessment to identify the specific requirements of your organization.
This will help you choose a solution that best fits your business goals and operational needs.
Next, develop an implementation plan.
This should include a timeline, goals, and a budget.
Assign responsibilities to team members to ensure that everyone knows their roles and duties during the deployment.
Once the plan is in place, proceed with system integration.
Work with the software vendor to ensure that the system is correctly installed and configured to suit your organization’s processes.
Training is an integral part of implementation.
Provide comprehensive training sessions for all users of the system to facilitate smooth adoption.
This ensures that employees are comfortable with the new system and can leverage its full potential.
Finally, monitor and evaluate the system’s performance post-implementation.
Gather feedback from users and identify areas for improvement.
Regularly update the system to incorporate any new features or technology advancements.
Challenges in Supplier Management System Implementation
Despite the numerous benefits, implementing a supplier management system can present challenges.
One common issue is resistance to change. Employees may be reluctant to transition from familiar processes to a new system.
Clear communication and comprehensive training can help mitigate this resistance.
Data migration is another potential challenge.
Transferring existing supplier data into the new system can be complex, especially if there is a large volume of information.
Accuracy is critical during this stage to ensure that the system functions as intended.
Budget constraints might also arise, particularly for small businesses.
It’s important to consider both the initial costs and the long-term value of the system to justify the investment.
In summary, while challenges exist, they can be effectively managed with proper planning and execution.
Overcoming these obstacles paves the way for successful implementation and, ultimately, more streamlined purchasing operations.
Conclusion
The introduction of a supplier management system offers businesses a strategic advantage in streamlining their purchasing operations.
By centralizing supplier information, managing contracts, and tracking performance, these systems enhance efficiency and provide cost savings.
Choosing the right system involves careful consideration of business needs, integration capabilities, and user-friendliness.
With thoughtful implementation and attention to potential challenges, businesses can strengthen their supply chain management and build better relationships with their suppliers.
In doing so, they position themselves for sustained success in a competitive marketplace.
資料ダウンロード
QCD調達購買管理クラウド「newji」は、調達購買部門で必要なQCD管理全てを備えた、現場特化型兼クラウド型の今世紀最高の購買管理システムとなります。
ユーザー登録
調達購買業務の効率化だけでなく、システムを導入することで、コスト削減や製品・資材のステータス可視化のほか、属人化していた購買情報の共有化による内部不正防止や統制にも役立ちます。
NEWJI DX
製造業に特化したデジタルトランスフォーメーション(DX)の実現を目指す請負開発型のコンサルティングサービスです。AI、iPaaS、および先端の技術を駆使して、製造プロセスの効率化、業務効率化、チームワーク強化、コスト削減、品質向上を実現します。このサービスは、製造業の課題を深く理解し、それに対する最適なデジタルソリューションを提供することで、企業が持続的な成長とイノベーションを達成できるようサポートします。
オンライン講座
製造業、主に購買・調達部門にお勤めの方々に向けた情報を配信しております。
新任の方やベテランの方、管理職を対象とした幅広いコンテンツをご用意しております。
お問い合わせ
コストダウンが利益に直結する術だと理解していても、なかなか前に進めることができない状況。そんな時は、newjiのコストダウン自動化機能で大きく利益貢献しよう!
(Β版非公開)