- お役立ち記事
- How to utilize TQM and the PDCA cycle that new leaders of quality assurance departments should know
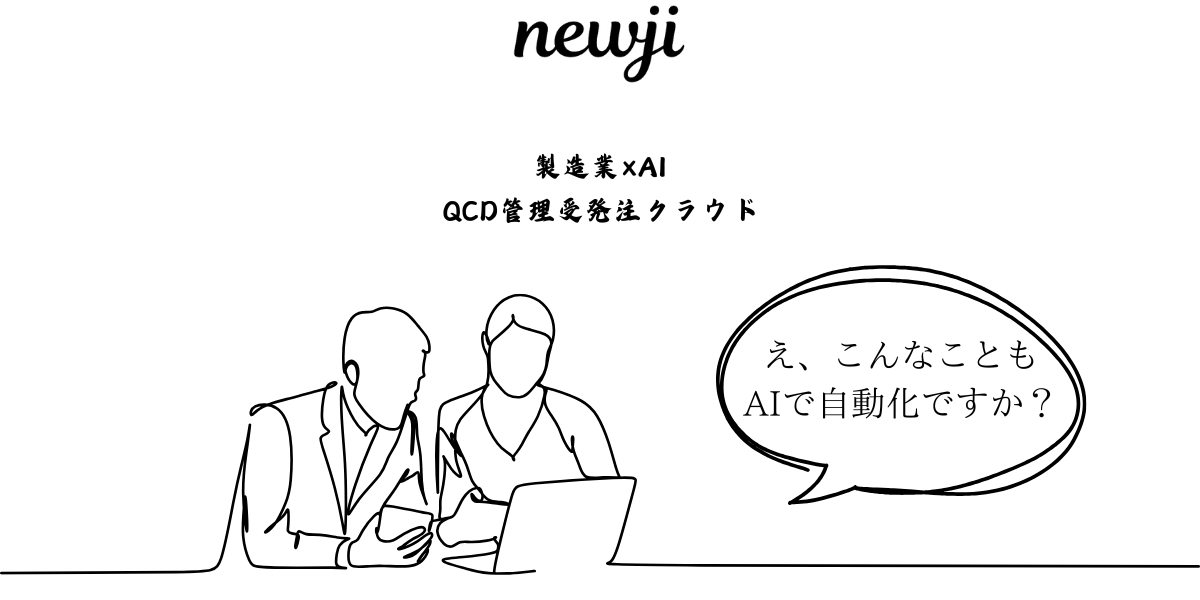
How to utilize TQM and the PDCA cycle that new leaders of quality assurance departments should know
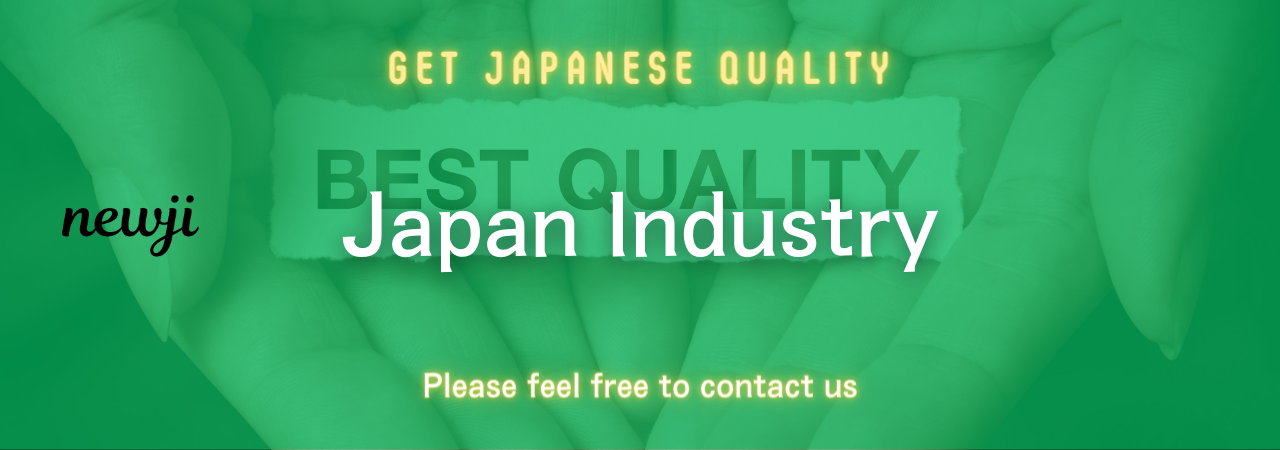
目次
Understanding Total Quality Management (TQM)
Total Quality Management, often abbreviated as TQM, is a comprehensive approach focused on improving the quality of products and services across an organization.
It emphasizes a long-term commitment to quality through the involvement of all members of an organization.
The goal of TQM is not just to improve overall quality but to enhance customer satisfaction and operational efficiencies.
TQM integrates fundamental management techniques, efficient procedures, and refined efforts to enhance performance.
It’s important to understand that TQM is not a one-time process but a continuous pursuit for excellence.
The Principles of TQM
One of the foundational principles of TQM is customer focus.
Every business, regardless of its industry, exists to fulfill customers’ needs and expectations.
Understanding what your customers want is the first step towards delivering high-quality products and services.
Leadership also plays a critical role in TQM.
Leaders must establish unity of purpose and direction in the organization.
They should create and maintain the internal environment in which people can become fully involved in achieving the organization’s objectives.
Another core principle is the involvement of people.
Employees at all levels are the essence of an organization, and their full involvement enables their abilities to be used for the organization’s benefit.
Process approach and systematic management are also pivotal, meaning processes are managed as a whole rather than in fragments.
The PDCA Cycle: A Crucial TQM Tool
The PDCA cycle, also known as the Deming Cycle, is a four-step iterative process used in business for control and continuous improvement of processes and products.
PDCA stands for Plan, Do, Check, Act.
Plan
In the planning phase, one sets objectives and processes necessary to deliver results in accordance with customer specifications and policies.
It’s crucial to identify and understand the problem, observe the situation, analyze data, and develop hypotheses about what the underlying cause of the problem could be.
This phase involves detailed planning to figure out what the best course of action might be.
Do
The ‘Do’ phase is where the plan is implemented but on a small scale to test the solution.
Implement the steps identified in the planning phase and collect data for analysis.
It’s important to document everything, including any problems that occur and reasons for them.
The goal here is to find out if the proposed change indeed leads to improvement.
Check
During the ‘Check’ phase, you compare the data before and after the process change.
Analyze the results to learn what you’ve achieved, whether the plan worked, or if there are areas requiring adjustments.
It’s crucial to review the test, analyze lessons learned, and determine whether the change served the purpose of achieving the desired goal.
Act
In the final phase, if the ‘Do’ phase was successful, you implement the change on a broader scale and continuously assess your results.
If the change did not lead to improvement, start the cycle again.
Either way, knowledge gained will be used to further refine the objectives and planning process.
Benefits of Integrating TQM with the PDCA Cycle
By integrating TQM with the PDCA cycle, organizations create a structured methodology to process and productivity improvement.
This combined approach ensures that your organization not only aims for high quality but achieves it systematically.
This integration helps in fostering a culture of continuous improvement.
Employees become more engaged in the process as they see their contributions directly lead to outcomes.
Furthermore, problems are swiftly addressed with a systematic approach to improving processes leading to overall efficiency.
Organizations adopting this framework often experience increased productivity, reduced costs, enhanced customer satisfaction, and the ability to adapt to changing market demands quickly.
Steps for New Leaders in Quality Assurance Departments
If you are a new leader in a quality assurance department, there are key steps to effectively utilize TQM and the PDCA cycle.
Prioritize Training and Awareness
Ensure all team members are trained in TQM principles and the PDCA cycle.
This ensures that everyone understands the objectives and their roles in achieving them.
Develop a Clear Vision and Objectives
Establish a strong vision and clear objectives that prioritize customer satisfaction.
Communicate these goals effectively across your team to ensure everyone is aligned.
Implement the PDCA Cycle
Incorporate the PDCA cycle into your department’s operations.
Encourage team members to actively participate in identifying areas for improvement and in planning tests aimed at improving processes.
Focus on Collaboration
Encourage collaboration between different departments.
Quality is a company-wide responsibility, so crossing departmental boundaries can open new opportunities for improvement.
Measure and Review
Consistently measure and review performance metrics against objectives.
These insights will guide decision-making and further refine processes for better outcomes.
By embedding both TQM and the PDCA cycle in your operations, you position your department to not only assure quality but to build sustainable processes that deliver constant improvements, leading to long-term success.
資料ダウンロード
QCD調達購買管理クラウド「newji」は、調達購買部門で必要なQCD管理全てを備えた、現場特化型兼クラウド型の今世紀最高の購買管理システムとなります。
ユーザー登録
調達購買業務の効率化だけでなく、システムを導入することで、コスト削減や製品・資材のステータス可視化のほか、属人化していた購買情報の共有化による内部不正防止や統制にも役立ちます。
NEWJI DX
製造業に特化したデジタルトランスフォーメーション(DX)の実現を目指す請負開発型のコンサルティングサービスです。AI、iPaaS、および先端の技術を駆使して、製造プロセスの効率化、業務効率化、チームワーク強化、コスト削減、品質向上を実現します。このサービスは、製造業の課題を深く理解し、それに対する最適なデジタルソリューションを提供することで、企業が持続的な成長とイノベーションを達成できるようサポートします。
オンライン講座
製造業、主に購買・調達部門にお勤めの方々に向けた情報を配信しております。
新任の方やベテランの方、管理職を対象とした幅広いコンテンツをご用意しております。
お問い合わせ
コストダウンが利益に直結する術だと理解していても、なかなか前に進めることができない状況。そんな時は、newjiのコストダウン自動化機能で大きく利益貢献しよう!
(Β版非公開)