- お役立ち記事
- Importance of Inventory Management for Optimizing Purchasing Management in SMEs
月間73,982名の
製造業ご担当者様が閲覧しています*
*2025年1月31日現在のGoogle Analyticsのデータより
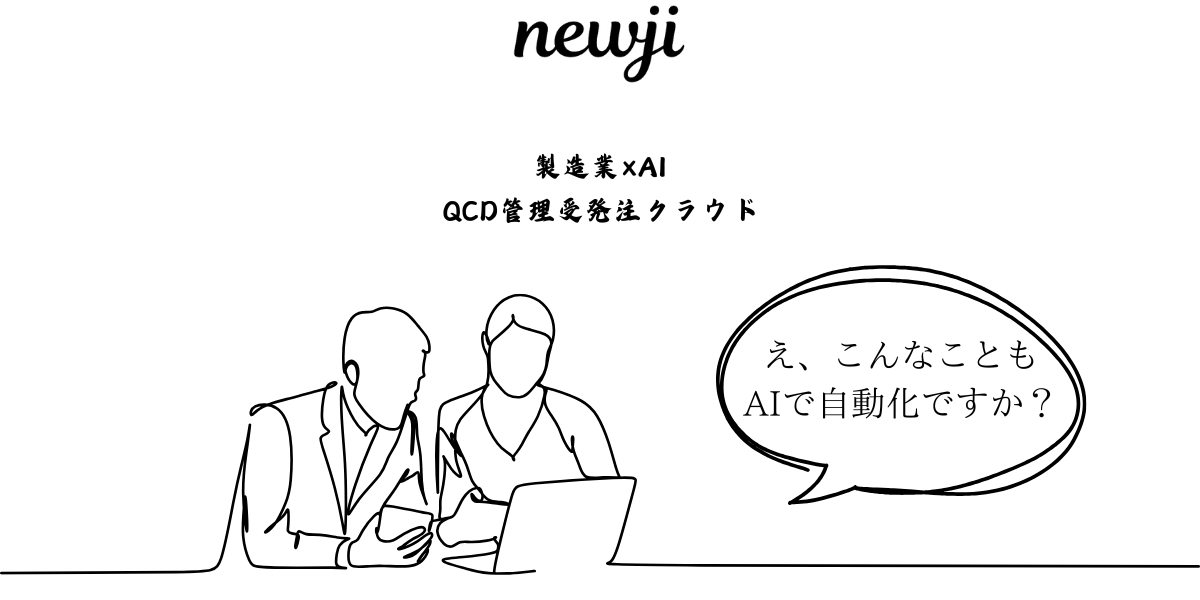
Importance of Inventory Management for Optimizing Purchasing Management in SMEs
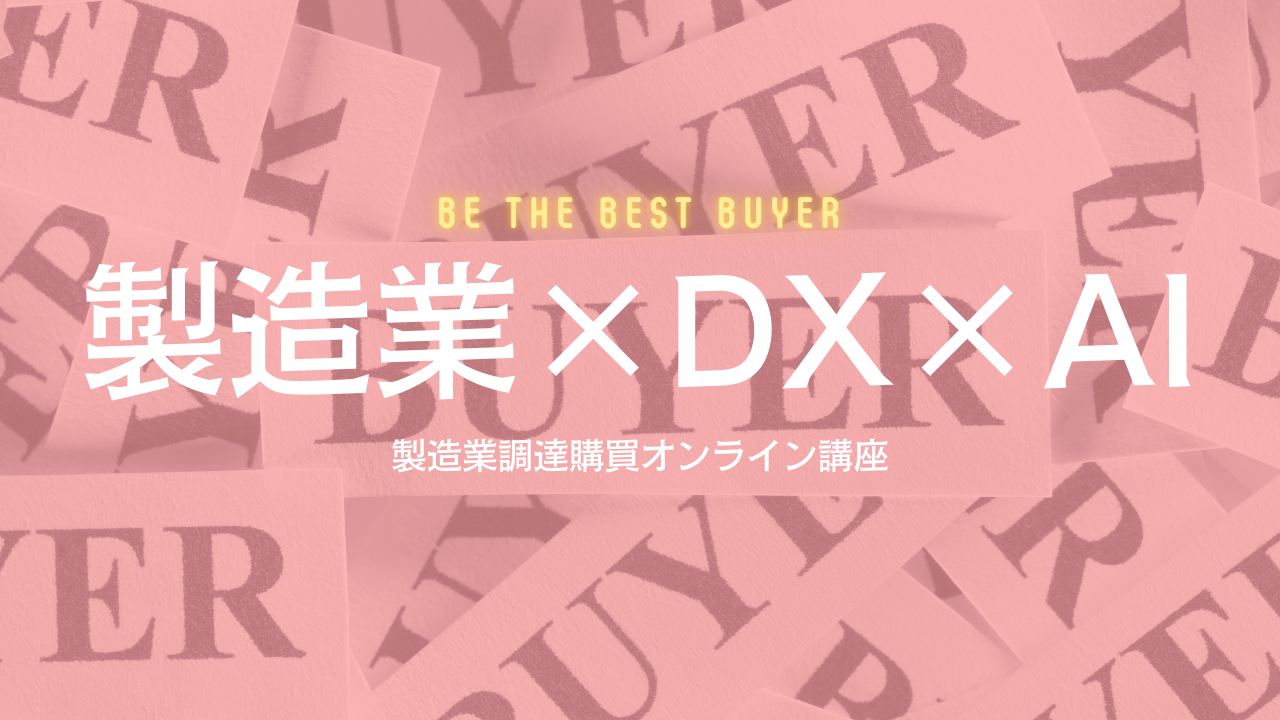
Effective inventory management is crucial for small and medium-sized enterprises (SMEs) looking to optimize purchasing and reduce costs. Proper tracking and planning of stock levels allows businesses to purchase only what is needed, when it is needed, avoiding overstock of slow-moving items and stock-outs of popular products. With tight budgets and limited resources compared to larger companies, SMEs require optimized purchasing to minimize wasted spending and maximize customer satisfaction.
Keeping accurate inventory records is the first step towards better purchasing decisions. Businesses should use an inventory management system to continuously update stock levels as items are received and sold. An ideal system makes it easy to count physical inventory and record changes in stock in real-time. This provides up-to-date information on what products are in stock, what quantities are available, and when replenishment orders should be placed. Armed with accurate stock data, purchasers can avoid unnecessary rush orders or running out of popular items.
Businesses should also track the rate at which each product is selling. By analyzing sales history and patterns, purchasers gain insights into what types of items customers want the most. They can then prioritize fast-selling core products that drive the bulk of revenue and adjust reordering thresholds appropriately. For slower items, maximum and minimum stock levels help prevent overstock while maintaining adequate supply. Monitoring sell-through rates also reveals underperforming products that may not be worth reordering. This information supports optimized purchasing decisions centered around customer demand.
Forecasting sales volumes and trends allows SMEs to estimate future inventory needs. Predictive analytics applied to historical sales and market data generates forecasts that purchasers can use to plan future orders in advance. By ordering larger batch sizes just before estimated peaks in demand, businesses take advantage of quantity discounts from suppliers. They also avoid rushing smaller emergency orders when stock runs low. Accurate forecasting is essential for optimized purchasing that synchronizes replenishment with anticipated needs.
Monitoring supplier lead times is another key aspect of improved inventory management. By knowing how long it takes from order placement to delivery, purchasers can plan order dates further in advance to seamlessly refill stock without risk of shortages. Especially for international orders with long transit periods, lead time tracking prevents stock-outs by informing replenishment schedules. Build schedules factor in supplier performance to maintain adequate inventory cushions based on real fulfillment timeframes. This provides a buffer against unforeseen delays.
Conducting regular inventory cycle counts helps keep stock records up-to-date and identify any discrepancies between the book balance and physical count. Zeroing in on the root causes of variances, such as data entry errors, product damage, or theft, prevents replenishment errors. Regular cycle counting ensures inventory records used for purchasing match actual on-hand quantities. Automating cycle counts with mobile devices also increases efficiency by streamlining the process. Timely reconciliation of records to the real stock prevents purchasing the wrong amounts of items.
Optimizing ordering policies to maximize discounts is another money-saving tactic. Most suppliers offer volume discounts for larger orders or frequent customers. By batching items from multiple suppliers together and negotiating terms, purchasers may qualify for better pricing. Approving special purchase orders during price reductions or promoting leftover seasonal stock also trims costs. Efficient inventory turns combined with strong supplier relationships based on consistent large orders earns maximum discounts on total purchasing spend.
Implementing efficient inventory management strategies allows SMEs to optimize purchasing based on real demands and inventory positions. By keeping records accurate, analyzing usage patterns, forecasting needs, monitoring lead times, and qualifying for supplier discounts, businesses minimize overstocks and understocks. This reduces costs of excess inventory carrying and emergency reorders while maintaining high in-stock levels. When purchasing is synchronized with sales through optimized inventory management, SMEs satisfy customers cost-effectively with the right products available at the right times.
資料ダウンロード
QCD管理受発注クラウド「newji」は、受発注部門で必要なQCD管理全てを備えた、現場特化型兼クラウド型の今世紀最高の受発注管理システムとなります。
ユーザー登録
受発注業務の効率化だけでなく、システムを導入することで、コスト削減や製品・資材のステータス可視化のほか、属人化していた受発注情報の共有化による内部不正防止や統制にも役立ちます。
NEWJI DX
製造業に特化したデジタルトランスフォーメーション(DX)の実現を目指す請負開発型のコンサルティングサービスです。AI、iPaaS、および先端の技術を駆使して、製造プロセスの効率化、業務効率化、チームワーク強化、コスト削減、品質向上を実現します。このサービスは、製造業の課題を深く理解し、それに対する最適なデジタルソリューションを提供することで、企業が持続的な成長とイノベーションを達成できるようサポートします。
製造業ニュース解説
製造業、主に購買・調達部門にお勤めの方々に向けた情報を配信しております。
新任の方やベテランの方、管理職を対象とした幅広いコンテンツをご用意しております。
お問い合わせ
コストダウンが利益に直結する術だと理解していても、なかなか前に進めることができない状況。そんな時は、newjiのコストダウン自動化機能で大きく利益貢献しよう!
(β版非公開)