- お役立ち記事
- Improving Energy Efficiency by Optimizing Drive Units in Extrusion Molding
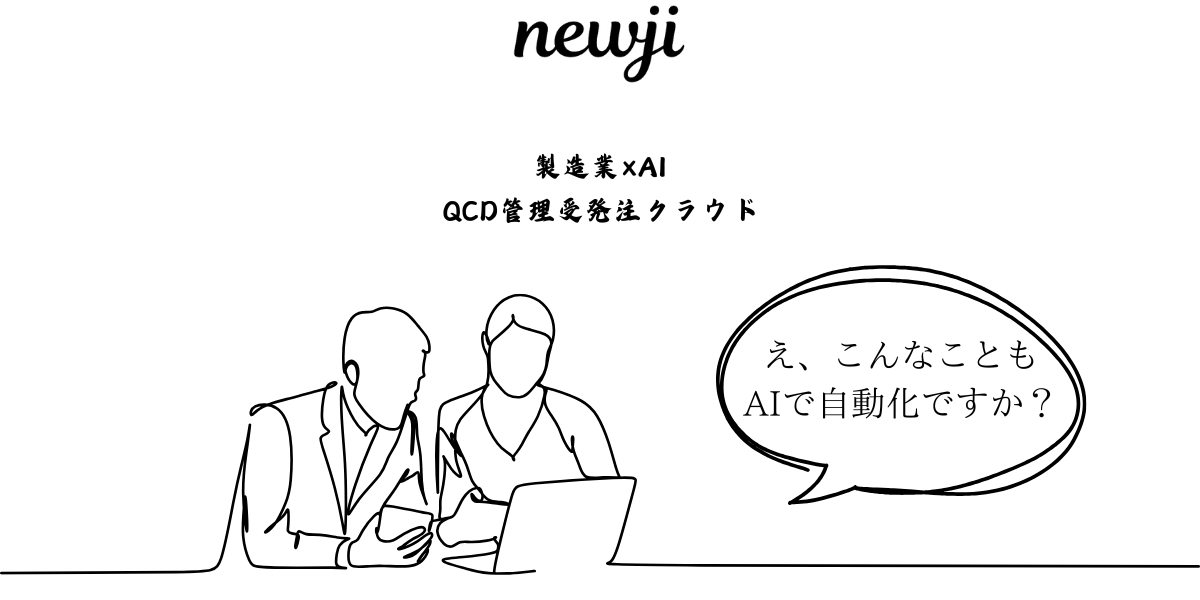
Improving Energy Efficiency by Optimizing Drive Units in Extrusion Molding
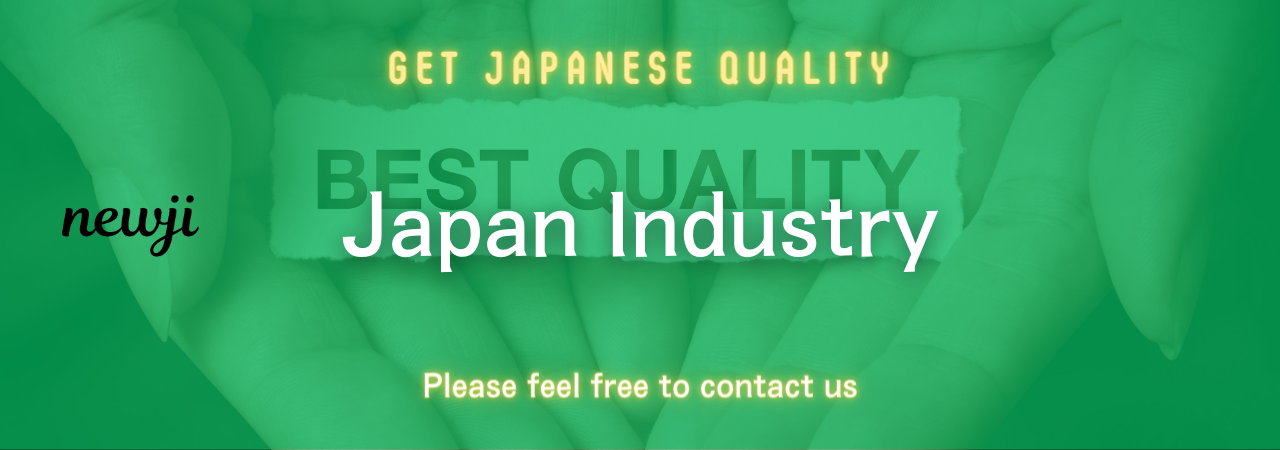
Extrusion molding is a widely used manufacturing process that shapes material by forcing it through a die.
This method is fundamental in producing numerous items, from plastic pipes to complex profiles.
However, like any industrial process, it consumes a significant amount of energy.
In the face of rising energy costs and environmental concerns, optimizing drive units in extrusion molding can lead to substantial improvements in energy efficiency.
In this article, we will explore various strategies and techniques to enhance the energy performance of these systems.
目次
Understanding Drive Units in Extrusion Molding
Drive units are the heart of the extrusion molding process.
They convert electrical energy into mechanical energy, driving the screw that pushes the material through the die.
The efficiency of these drive units directly impacts the overall energy consumption of the extrusion process.
Types of Drive Units
There are primarily two types of drive units used in extrusion molding:
Electric drives and hydraulic drives.
Electric drives are more popular due to their higher efficiency and precision.
Hydraulic drives, on the other hand, are traditionally known for their robust performance and suitability for heavy-duty applications.
The Role of Motor Efficiency
The efficiency of the motor used in the drive unit is crucial.
High-efficiency motors convert a larger percentage of electrical energy into mechanical energy, reducing energy waste.
Using modern high-efficiency motors can lead to significant energy savings over time.
Improving Energy Efficiency
Optimizing energy efficiency in extrusion molding requires a combination of techniques and innovations.
Let’s delve into the most effective methods.
Regular Maintenance
Regular maintenance of drive units is essential for ensuring optimal performance.
Components such as bearings, lubricants, and cooling systems need to be regularly inspected and maintained.
Proper maintenance reduces the chances of mechanical failures and ensures that the drive unit operates at peak efficiency.
Upgrading to High-Efficiency Motors
Investing in high-efficiency motors can have a considerable impact on energy consumption.
Modern motors are designed to minimize energy loss, providing better performance.
While the initial investment may be higher, the long-term energy savings and improved performance make it worthwhile.
Variable Frequency Drives (VFDs)
Variable frequency drives (VFDs) are an effective way to optimize the energy efficiency of drive units.
VFDs allow for precise control of motor speed and torque.
By adjusting the motor speed to match the process requirement, VFDs help reduce energy consumption during periods of low demand.
Advanced Control Systems
Implementing advanced control systems can significantly enhance the efficiency of drive units.
These systems monitor and adjust the operating parameters in real time, ensuring that the drive unit operates within the optimal range.
Sophisticated algorithms can predict and mitigate inefficiencies, leading to better energy performance.
Heat Recovery Systems
Extrusion molding generates a significant amount of heat as a byproduct.
Implementing heat recovery systems can capture and reuse this heat, improving overall energy efficiency.
The recovered heat can be used for preheating materials or other processes, reducing the need for additional energy input.
Monitoring and Analysis
Continuous monitoring and analysis of the drive unit’s performance is essential for long-term energy efficiency.
Energy Audits
Conducting regular energy audits helps identify areas where energy is being wasted.
These audits provide insight into the efficiency of the drive units and highlight opportunities for improvement.
By addressing these inefficiencies, operators can make informed decisions on upgrades and adjustments.
Data Analytics
Harnessing the power of data analytics can provide deeper insights into the performance of drive units.
By analyzing operating data, patterns and trends can be identified.
This information can be used to optimize settings, predict maintenance needs, and improve overall efficiency.
Real-Time Monitoring
Implementing real-time monitoring systems allows operators to keep a constant check on the performance of drive units.
Any deviations or inefficiencies can be detected and corrected promptly.
This proactive approach reduces downtime and ensures that the system is always operating at peak efficiency.
The Role of Automation
Automation plays a significant role in enhancing the energy efficiency of drive units in extrusion molding.
Automated Process Control
Automated process control systems precisely regulate the various parameters of the extrusion process.
By maintaining optimal conditions, these systems reduce energy consumption and improve product quality.
Automated systems can quickly adjust to changes in demand, ensuring that the process remains efficient at all times.
Robotic Assistance
Robotic assistance in material handling and other auxiliary tasks can also contribute to better energy efficiency.
Robots are more precise and consistent than human workers, reducing wastage and improving process control.
This, in turn, results in lower energy consumption and higher productivity.
The Future of Energy Efficiency in Extrusion Molding
The industry is continually evolving, with new technologies and innovations being developed to enhance energy efficiency.
Emerging Technologies
Advancements such as artificial intelligence and machine learning are making their way into extrusion molding.
These technologies can analyze vast amounts of data to identify inefficiencies and suggest improvements.
The integration of these technologies is expected to lead to smarter and more energy-efficient drive units.
Sustainable Practices
The push towards sustainability is driving the development of greener technologies.
Manufacturers are increasingly adopting practices that reduce energy consumption and minimize environmental impact.
This includes the use of renewable energy sources and the development of more energy-efficient machinery.
Improving energy efficiency by optimizing drive units in extrusion molding is not just about cutting costs.
It’s about creating a sustainable future for the industry.
By implementing the strategies discussed, manufacturers can achieve significant energy savings, improve productivity, and contribute to a greener planet.
Continuous innovation and the adoption of emerging technologies will further drive these improvements, ensuring that extrusion molding remains a viable and efficient manufacturing method.
資料ダウンロード
QCD調達購買管理クラウド「newji」は、調達購買部門で必要なQCD管理全てを備えた、現場特化型兼クラウド型の今世紀最高の購買管理システムとなります。
ユーザー登録
調達購買業務の効率化だけでなく、システムを導入することで、コスト削減や製品・資材のステータス可視化のほか、属人化していた購買情報の共有化による内部不正防止や統制にも役立ちます。
NEWJI DX
製造業に特化したデジタルトランスフォーメーション(DX)の実現を目指す請負開発型のコンサルティングサービスです。AI、iPaaS、および先端の技術を駆使して、製造プロセスの効率化、業務効率化、チームワーク強化、コスト削減、品質向上を実現します。このサービスは、製造業の課題を深く理解し、それに対する最適なデジタルソリューションを提供することで、企業が持続的な成長とイノベーションを達成できるようサポートします。
オンライン講座
製造業、主に購買・調達部門にお勤めの方々に向けた情報を配信しております。
新任の方やベテランの方、管理職を対象とした幅広いコンテンツをご用意しております。
お問い合わせ
コストダウンが利益に直結する術だと理解していても、なかなか前に進めることができない状況。そんな時は、newjiのコストダウン自動化機能で大きく利益貢献しよう!
(Β版非公開)