- お役立ち記事
- In-Mold Decorating (IMD) in Injection Molding
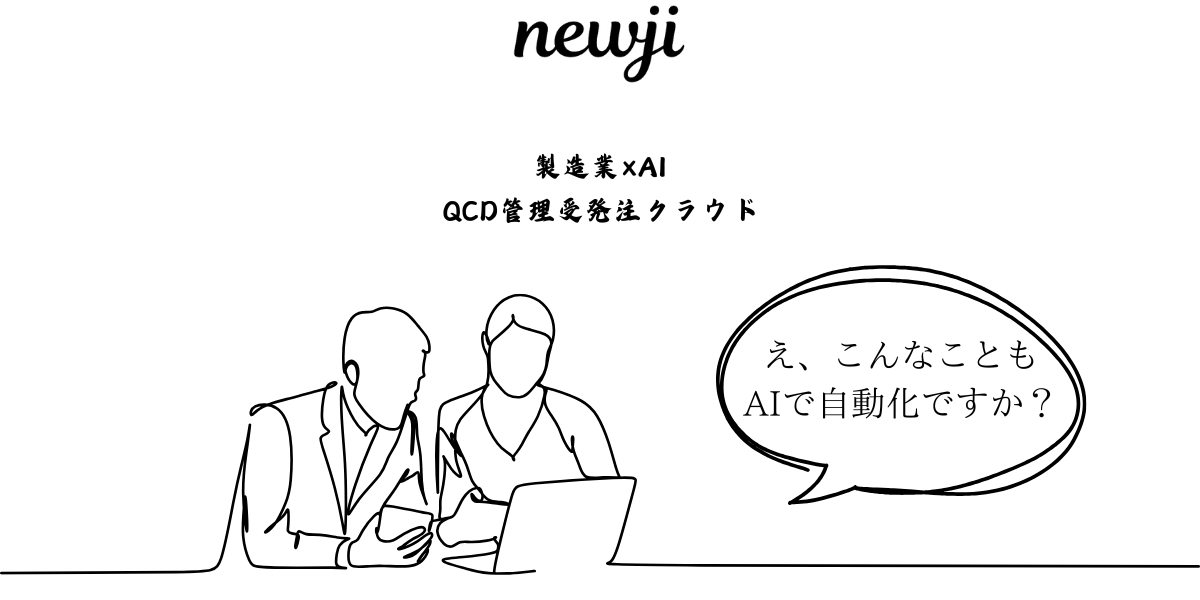
In-Mold Decorating (IMD) in Injection Molding
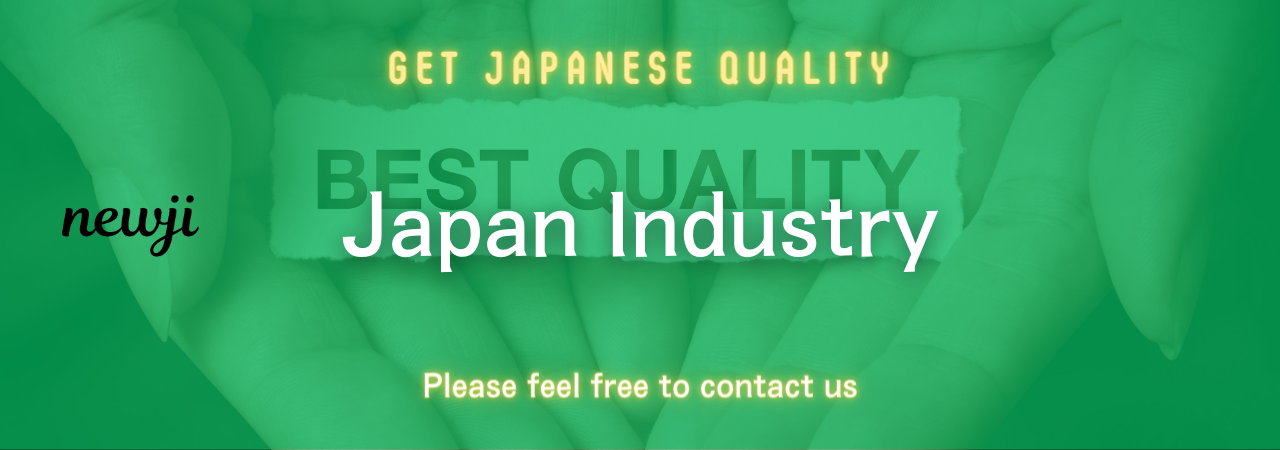
In the rapidly advancing world of manufacturing, one of the most intriguing innovations is In-Mold Decorating (IMD) in injection molding. This technology has revolutionized the production of highly aesthetic, durable, and intricately designed plastic components. IMD integrates decoration and functionality during the molding process, eliminating the need for secondary operations such as printing, painting, or labeling. It offers endless possibilities for product customization, thereby catering to various industries from automotive and electronics to household appliances and consumer goods.
What is In-Mold Decorating (IMD)?
IMD, or In-Mold Decorating, is a sophisticated process that involves placing a decorative film or label inside a mold before injecting plastic resin into it. The decoration permanently fuses to the plastic part as it cools and hardens within the mold. This results in a finished product with high-quality graphics, textures, and logos already in place.
The process begins with the creation of the decorative film. This film is typically made of a durable, heat-resistant material designed to withstand the injection molding process. Depending on the complexity and requirements of the design, the film can include various colors, patterns, textures, and even functional elements like touch-sensitive areas.
The Process of In-Mold Decorating (IMD)
IMD utilizes a step-by-step method to ensure precise and high-quality results:
1. **Design and Creation of the Decorative Film:**
– The first step involves designing the desired graphics, patterns, or logos using specialized software. Once the design is finalized, it is printed onto a thin, durable film.
2. **Film Placement:**
– The film is then carefully placed into the open mold cavity. For more complex shapes, the film may be preformed to fit the mold precisely.
3. **Injection Molding:**
– With the film in place, the mold is closed, and molten plastic is injected into the cavity. The high temperature and pressure ensure that the decorative film bonds permanently to the plastic product.
4. **Cooling and Ejection:**
– After the plastic has cooled and solidified, the mold opens, and the finished part is ejected, complete with its integrated decoration.
Benefits of In-Mold Decorating (IMD)
IMD offers numerous advantages compared to conventional decoration methods:
1. **Durability and Resistance:**
– The integration of the decoration into the plastic part enhances durability, making it resistant to wear, scratches, and fading. This proves particularly advantageous in industries that require products to withstand harsh conditions.
2. **Aesthetic Versatility:**
– IMD allows for high-resolution graphics, intricate patterns, and even textures to be permanently incorporated into the plastic. This enables manufacturers to create visually appealing and unique products.
3. **Cost-Effectiveness:**
– Eliminating the need for secondary decoration processes such as painting or labeling reduces production costs and speeds up the manufacturing process. Additionally, IMD minimizes waste and improves overall efficiency.
4. **Design Flexibility:**
– With IMD, manufacturers can easily alter the design by simply changing the decorative film. This flexibility allows for rapid prototyping, customization, and quicker time-to-market for new products.
5. **Enhanced Functionalities:**
– IMD can incorporate functional elements such as touch-sensitive areas, breathable membranes, and anti-reflective coatings into the plastic part, further enhancing its utility and appeal.
Applications of In-Mold Decorating (IMD)
The versatility of IMD makes it suitable for a broad range of applications across various industries:
1. **Automotive Industry:**
– In the automotive sector, IMD is used to create high-quality interior components like dashboard panels, control buttons, and trim parts. The durability and customizability of IMD are ideal for these high-use, highly visible elements.
2. **Consumer Electronics:**
– In-Mold Decorating is widely used in consumer electronics to produce sleek, durable casings for smartphones, tablets, and remote controls. The ability to integrate touch-sensitive panels and other functionalities is a major advantage.
3. **Household Appliances:**
– IMD is utilized in manufacturing aesthetically appealing and functional panels, knobs, and bezels for household appliances like washing machines, refrigerators, and microwaves.
4. **Medical Devices:**
– The medical industry benefits from IMD’s ability to produce durable, easy-to-clean, and customizable devices and equipment, enhancing both functionality and appearance.
5. **Consumer Goods:**
– IMD allows for the creation of unique, attractive designs for items such as toys, sports equipment, and packaging materials, improving their marketability and user appeal.
Challenges and Future Trends
While IMD offers numerous benefits, it also presents some challenges:
1. **Complexity in Mold Design:**
– Designing molds that can accommodate intricate decorative films requires significant expertise and precision. Advanced simulation software and prototyping are often necessary to achieve optimal results.
2. **Initial Costs:**
– The initial setup costs for IMD, including the design of decorative films and specialized molds, can be higher compared to traditional methods. However, these costs are often offset by long-term savings and efficiency gains.
Looking ahead, the future of IMD appears bright, with several key trends anticipated to drive its adoption:
1. **Integration of Smart Technologies:**
– The incorporation of smart technologies such as touch sensors, light guides, and flexible displays within IMD films is likely to become more prevalent, enhancing the functionality of plastic components.
2. **Sustainable Practices:**
– With the growing emphasis on sustainability, IMD processes and materials are expected to evolve to minimize environmental impact. Innovations in recyclable films and eco-friendly resins will play a significant role.
3. **Technological Advancements:**
– Advances in printing technologies, mold design, and simulation software will further refine the IMD process, making it more accessible and efficient.
In conclusion, In-Mold Decorating (IMD) in injection molding represents a cutting-edge solution that seamlessly combines aesthetics and functionality. By eliminating the need for secondary decoration processes, IMD offers a cost-effective, versatile, and durable approach to creating visually appealing and high-performance plastic components. As technology continues to advance, IMD is poised to become an integral part of the manufacturing landscape, driving innovation and enabling the production of sophisticated, customized products across diverse industries.
資料ダウンロード
QCD調達購買管理クラウド「newji」は、調達購買部門で必要なQCD管理全てを備えた、現場特化型兼クラウド型の今世紀最高の購買管理システムとなります。
ユーザー登録
調達購買業務の効率化だけでなく、システムを導入することで、コスト削減や製品・資材のステータス可視化のほか、属人化していた購買情報の共有化による内部不正防止や統制にも役立ちます。
NEWJI DX
製造業に特化したデジタルトランスフォーメーション(DX)の実現を目指す請負開発型のコンサルティングサービスです。AI、iPaaS、および先端の技術を駆使して、製造プロセスの効率化、業務効率化、チームワーク強化、コスト削減、品質向上を実現します。このサービスは、製造業の課題を深く理解し、それに対する最適なデジタルソリューションを提供することで、企業が持続的な成長とイノベーションを達成できるようサポートします。
オンライン講座
製造業、主に購買・調達部門にお勤めの方々に向けた情報を配信しております。
新任の方やベテランの方、管理職を対象とした幅広いコンテンツをご用意しております。
お問い合わせ
コストダウンが利益に直結する術だと理解していても、なかなか前に進めることができない状況。そんな時は、newjiのコストダウン自動化機能で大きく利益貢献しよう!
(Β版非公開)