- お役立ち記事
- Increasing workplace efficiency through “work standardization”—Manual preparation method based on management guidance
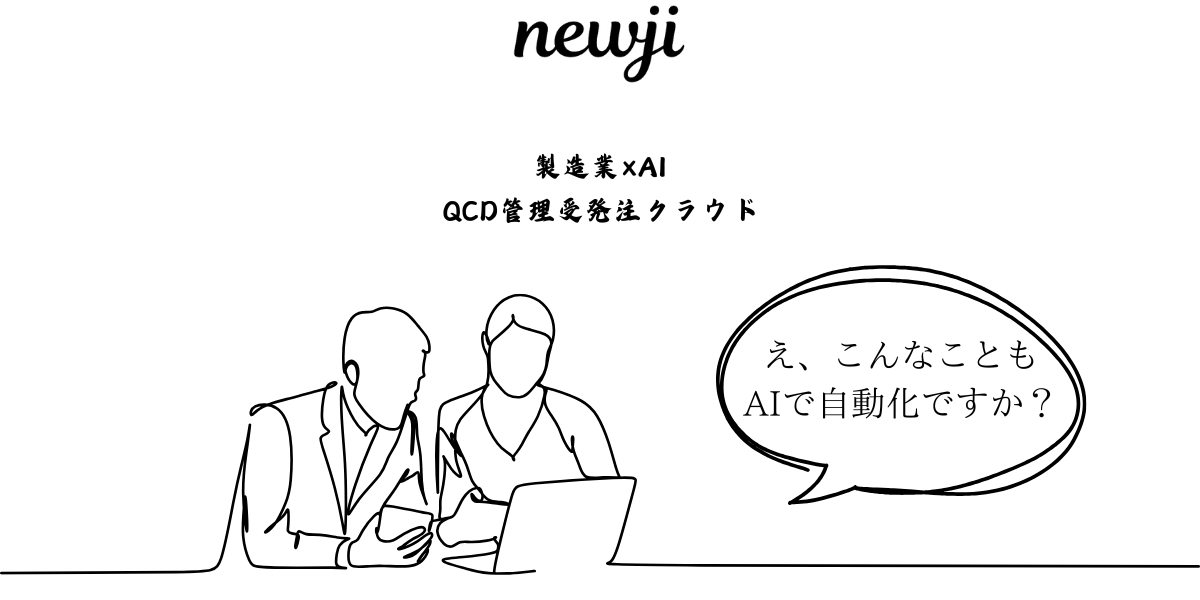
Increasing workplace efficiency through “work standardization”—Manual preparation method based on management guidance
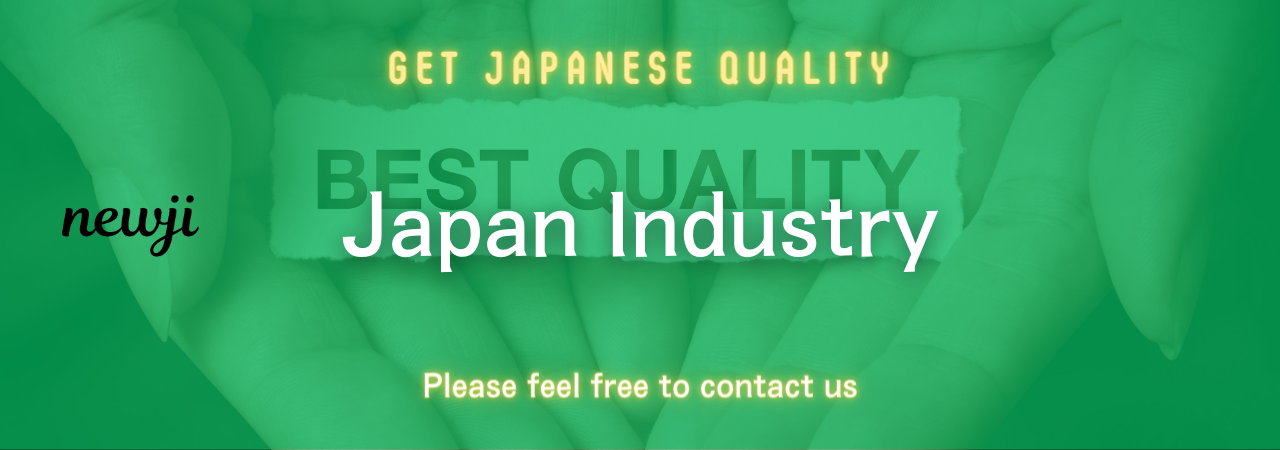
目次
Understanding Work Standardization
Work standardization is a key concept in modern management practices, aimed at increasing efficiency and productivity within an organization.
It involves creating a set of guidelines or procedures that define the most efficient way to perform a task.
These standards are designed to minimize variation and ensure consistency across all operations.
When employees follow standardized procedures, it results in a more uniform workflow, reducing the risk of errors and increasing overall workplace efficiency.
This approach allows organizations to streamline operations, make better use of resources, and improve the quality of their products or services.
The Importance of Management Guidance
Management guidance plays a crucial role in successfully implementing work standardization.
Leaders must provide clear and structured directions to develop effective standard operating procedures (SOPs).
Their role involves not just creating these guidelines but also ensuring that employees understand and adhere to them.
With strong management guidance, organizations can overcome potential resistance to change and achieve buy-in from their teams.
By communicating the benefits and objectives of standardization, management can foster a culture of continuous improvement and collaboration.
Steps to Create Effective Work Manuals
1. Identify Key Processes
The first step in work standardization is identifying processes that would benefit from standardization.
This involves analyzing current workflows and pinpointing areas where variance exists or efficiency can be improved.
Engage with employees who are closely involved in these processes, as their insights can be invaluable.
2. Gather Relevant Information
Once the processes are identified, gather all necessary information to form a comprehensive understanding of each task.
This includes involving stakeholders, such as subject matter experts and team leaders, to contribute their knowledge and expertise.
Collect data on current procedures, tools, and resources required to perform each task accurately and efficiently.
3. Draft the Procedures
Create a draft of the standard operating procedures based on the information collected.
These procedures should be clear, concise, and easy to understand, using simple language that eliminates any potential ambiguity.
Ensure that each step is detailed and sequentially outlined to guide employees through every aspect of the task.
4. Review and Refine
After drafting the procedures, it is essential to review and refine them with input from relevant stakeholders.
Gather feedback to ensure clarity, completeness, and practical applicability.
It is also crucial to test the procedures in a real-world setting to identify any gaps or areas for improvement.
5. Implement and Train
Once the procedures are finalized, implement them within the organization.
Conduct training sessions to ensure that all employees are informed about the new standards and understand how to apply them effectively.
Provide resources such as instructional videos, workshops, and hands-on training to facilitate a smooth transition.
6. Monitor and Update
Continuous monitoring and evaluation of the standardized processes are necessary to ensure they remain effective.
Regularly review the procedures and update them as needed to accommodate any changes in technology, regulations, or organizational goals.
Encourage feedback from employees to identify opportunities for further refinement and optimization.
Overcoming Challenges in Work Standardization
Implementing work standardization can encounter several challenges, including resistance to change, communication barriers, and resource limitations.
To address these, it is important to involve employees in the process from the beginning and communicate the benefits of standardization clearly.
Providing training and resources to support the transition can also help in overcoming these challenges.
Furthermore, leaders should be prepared to address any resistance by being open to feedback and making necessary adjustments.
Promoting a positive attitude towards change and emphasizing the long-term benefits of improved efficiency can encourage employee cooperation and dedication to the standardization process.
Benefits of Work Standardization
Work standardization offers numerous advantages for both employees and the organization as a whole.
Some of the key benefits include:
1. **Consistency and Quality**: Standardized procedures ensure that tasks are performed consistently, reducing variability in outcomes and enhancing the quality of products or services.
2. **Increased Efficiency**: By eliminating unnecessary steps and streamlining processes, employees can work more efficiently, saving time and resources.
3. **Enhanced Training and Onboarding**: New employees can quickly and easily learn established procedures, resulting in a faster and more effective onboarding process.
4. **Improved Communication**: Standardized processes provide a common framework for employees, facilitating clearer communication and collaboration.
5. **Reduced Errors and Risks**: With defined guidelines, the likelihood of errors and risks diminishes, leading to a safer and more reliable work environment.
Conclusion
Work standardization is a powerful tool for enhancing workplace efficiency and productivity.
By establishing clear, consistent procedures and providing strong management guidance, organizations can optimize their operations and achieve better outcomes.
Effective standardization requires careful planning, collaboration, and continuous improvement to remain relevant and beneficial over time.
Although challenges may arise during implementation, the long-term benefits far outweigh these obstacles.
Through proactive efforts and a commitment to quality, organizations can create a more efficient and harmonious work environment that supports their growth and success.
資料ダウンロード
QCD調達購買管理クラウド「newji」は、調達購買部門で必要なQCD管理全てを備えた、現場特化型兼クラウド型の今世紀最高の購買管理システムとなります。
ユーザー登録
調達購買業務の効率化だけでなく、システムを導入することで、コスト削減や製品・資材のステータス可視化のほか、属人化していた購買情報の共有化による内部不正防止や統制にも役立ちます。
NEWJI DX
製造業に特化したデジタルトランスフォーメーション(DX)の実現を目指す請負開発型のコンサルティングサービスです。AI、iPaaS、および先端の技術を駆使して、製造プロセスの効率化、業務効率化、チームワーク強化、コスト削減、品質向上を実現します。このサービスは、製造業の課題を深く理解し、それに対する最適なデジタルソリューションを提供することで、企業が持続的な成長とイノベーションを達成できるようサポートします。
オンライン講座
製造業、主に購買・調達部門にお勤めの方々に向けた情報を配信しております。
新任の方やベテランの方、管理職を対象とした幅広いコンテンツをご用意しております。
お問い合わせ
コストダウンが利益に直結する術だと理解していても、なかなか前に進めることができない状況。そんな時は、newjiのコストダウン自動化機能で大きく利益貢献しよう!
(Β版非公開)