- お役立ち記事
- Innovation for the Future The Frontiers of Manufacturing DX
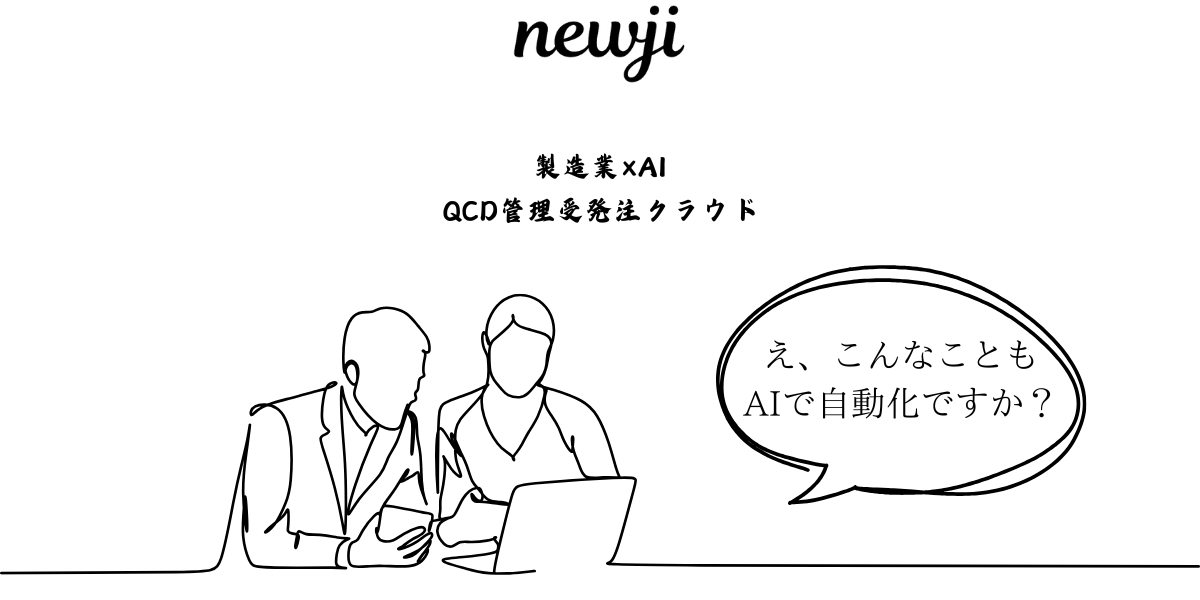
Innovation for the Future The Frontiers of Manufacturing DX
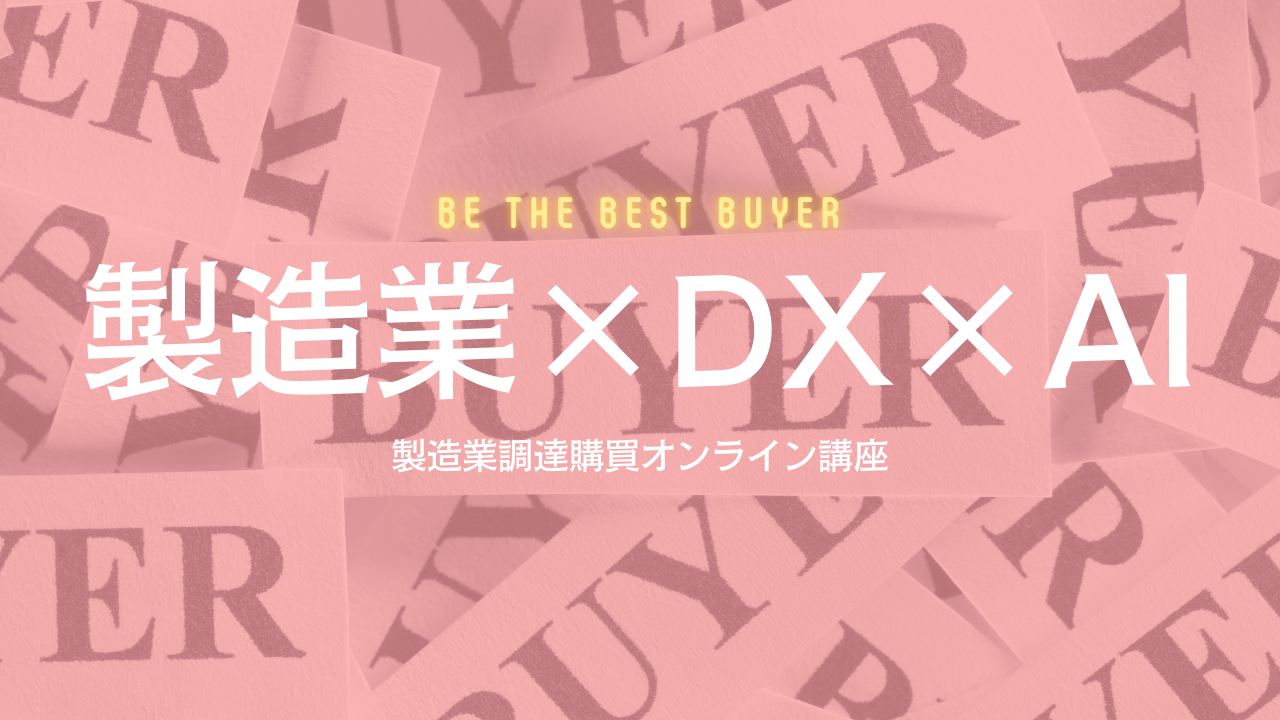
The manufacturing industry is on the cusp of tremendous change. New technologies are emerging that promise to revolutionize how goods are designed, produced, and delivered. This confluence of innovation goes by many names – the Fourth Industrial Revolution, Industry 4.0, digital transformation – but they all point to the same profound shifts currently reshaping manufacturing. Forward-thinking companies already see the writing on the wall: adapt or get left behind.
Today’s manufacturers face pressures on all sides. Customers expect hyper-personalized products tailored to their unique needs and lifestyles. Competitors continually push the boundaries of what’s possible through rapid prototyping, on-demand production, and global supply chain integration. Younger generations entering the workforce bring new expectations around environmental sustainability, workplace flexibility, and the desire for meaningful work. To keep pace in this fast-moving landscape, manufacturers must optimize operations like never before through connectivity, automation, predictive analytics and more.
This is where the promise of manufacturing digital transformation comes in. DX seeks to unify people, processes and technologies companywide through data sharing and machine learning. By linking the physical and digital worlds, manufacturers gain unprecedented insight into product design, production bottlenecks, maintenance needs, delivery logistics and much more. Strategic use of technologies like IoT sensors, augmented reality, additive manufacturing, cloud computing and big data can help optimize every step of operations from concept to customer. This elevated visibility and control empowers faster problem-solving, new revenue streams, and a more resilient business model primed for the future.
At the core of manufacturing DX are smart, connected products. IoT sensors embedded in components, sub-assemblies and finished goods collect invaluable usage and performance data during their entire lifecycles. Combined with digital twin simulations, this real-world feedback allows manufacturers to continuously analyze product behaviors, discover issues proactively, and push over-the-air software updates. Customers benefit too through personalized service, predictive maintenance notifications, and the peace of mind that comes with self-monitoring, self-healing products. As more devices and machines join the industrial internet, entire production lines and distribution networks will operate as living organisms – adaptive, self-optimizing and resilient.
Advanced robotics and automation take industrial digitization even further. Collaborative robots allow human workers and robots to safely work side-by-side on complex tasks. Advanced vision systems coupled with machine learning enable robots to identify defects, assess quality and optimize processes in ways that exceed human capabilities. Exoskeletons and powered safety gear increase worker strength and prevent injuries in hazardous applications. Additive manufacturing “printers” create high-precision parts on demand from 3D design files without molds or tooling. Together, these frontier technologies are helping automate dangerous, repetitive duties while empowering manufacturers to rapidly scale custom production runs down to the lot size of one – a perfect match for the new era of personalization.
By integrating operations end-to-end via digital threads and workflows, manufacturers can simulate products, processes, resources and partners with digital twins before committing to physical implementation. Virtual commissioning saves significant time and costs by catching issues early in design rather than late in production. Modeling factory layouts digitally maximizes material and information flows for peak efficiency. Remote technical support crosses borders via mixed-reality tools like live data overlays. Digital engineering even facilitates new business models like autonomous vehicles or personalized healthcare through iterative simulation-based validation and verification. The opportunities for innovation are almost limitless once manufacturing fully taps the combined powers of connectivity, data analytics and human-machine collaboration.
For any manufacturer committed to competitive differentiation and business resilience in the decades ahead, digital transformation is no longer optional – it’s table stakes. Forward-thinking leaders already developing comprehensive DX strategies will be best positioned to capitalize on the gains in customization, flexibility, productivity, quality and sustainability that new automation and data-driven insights can unlock. Though change inevitably brings challenges, those who embrace manufacturing’s digital frontiers will find powerful ways not only to survive but thrive in our rapidly evolving world. The factories of tomorrow are being built today – who will join the revolution?
資料ダウンロード
QCD調達購買管理クラウド「newji」は、調達購買部門で必要なQCD管理全てを備えた、現場特化型兼クラウド型の今世紀最高の購買管理システムとなります。
ユーザー登録
調達購買業務の効率化だけでなく、システムを導入することで、コスト削減や製品・資材のステータス可視化のほか、属人化していた購買情報の共有化による内部不正防止や統制にも役立ちます。
NEWJI DX
製造業に特化したデジタルトランスフォーメーション(DX)の実現を目指す請負開発型のコンサルティングサービスです。AI、iPaaS、および先端の技術を駆使して、製造プロセスの効率化、業務効率化、チームワーク強化、コスト削減、品質向上を実現します。このサービスは、製造業の課題を深く理解し、それに対する最適なデジタルソリューションを提供することで、企業が持続的な成長とイノベーションを達成できるようサポートします。
オンライン講座
製造業、主に購買・調達部門にお勤めの方々に向けた情報を配信しております。
新任の方やベテランの方、管理職を対象とした幅広いコンテンツをご用意しております。
お問い合わせ
コストダウンが利益に直結する術だと理解していても、なかなか前に進めることができない状況。そんな時は、newjiのコストダウン自動化機能で大きく利益貢献しよう!
(Β版非公開)