- お役立ち記事
- Introduction of Digital Twin Technology and Production Process Optimization Strategies for Manufacturing Sales
Introduction of Digital Twin Technology and Production Process Optimization Strategies for Manufacturing Sales
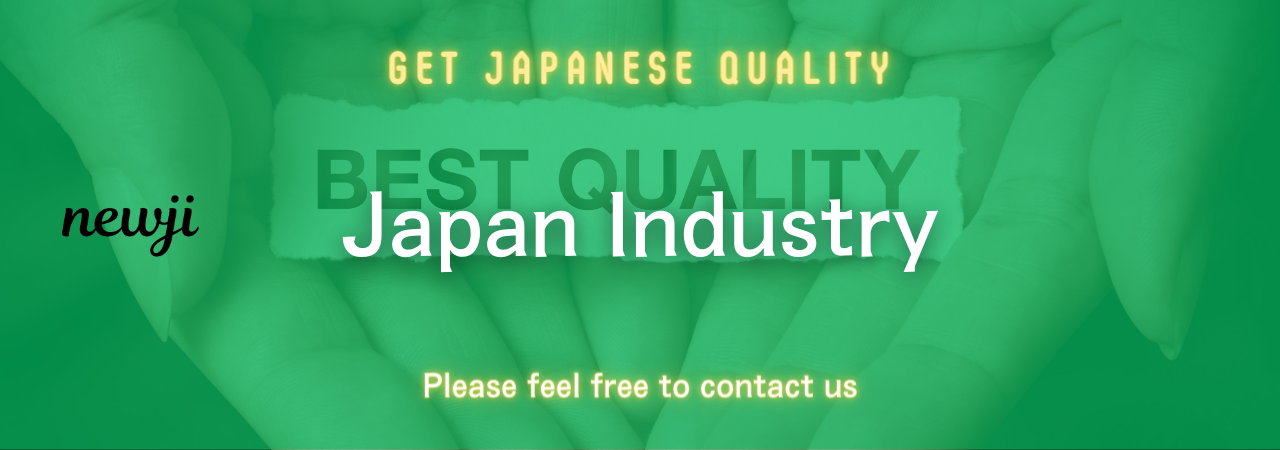
In today’s world, manufacturing companies face fierce competition and must continuously improve production processes to stay ahead.
Digital Twin Technology (DTT) has emerged as an innovative approach that can help optimize manufacturing processes, reduce costs, and improve product quality.
This article will introduce you to Digital Twin Technology and explore some production process optimization strategies that can benefit manufacturing sales.
目次
What is Digital Twin Technology?
Digital Twin Technology refers to the virtual representation of a physical object, process, or system.
It involves creating a digital copy, or “twin,” that simulates the real-world counterpart in real time.
This twin model is continuously updated with data from sensors and other sources, providing a dynamic and accurate representation of the physical entity.
How Digital Twin Technology Works
Digital Twin Technology relies on data collected from sensors, IoT devices, and other sources embedded in the physical system.
This data is then processed and used to create a digital replica that mirrors the physical object’s state, behavior, and environment.
The digital twin can analyze historical data, predict future performance, and identify potential issues before they occur.
Applications of Digital Twin Technology
Digital Twin Technology is used in various industries, including aerospace, automotive, healthcare, and manufacturing.
In manufacturing, it is employed to monitor production lines, optimize maintenance schedules, and improve overall efficiency.
Benefits of Digital Twin Technology in Manufacturing
Digital Twin Technology offers several benefits to manufacturing companies.
Understanding these advantages can help illustrate how DTT can play a crucial role in optimizing production processes.
Enhancing Product Development
Digital twins enable manufacturers to create virtual prototypes of products before actual production begins.
This allows for testing and refining designs without the need for physical prototypes.
As a result, development cycles are shortened, and product quality is improved.
Predictive Maintenance
By continuously monitoring the condition of machines and equipment through their digital twins, manufacturers can predict when maintenance is needed.
This helps prevent unexpected breakdowns, reduce downtime, and extend the lifespan of machinery.
Improving Production Efficiency
Digital twins provide real-time insights into production processes, allowing for better decision-making.
Manufacturers can identify bottlenecks, optimize workflows, and implement process improvements to enhance overall efficiency.
Reducing Costs
With the ability to anticipate maintenance needs and optimize production processes, digital twins help reduce operational costs.
Additionally, virtual prototyping and testing can save money on materials and resources during product development.
Strategies for Production Process Optimization
Optimizing production processes is essential for manufacturing companies to remain competitive.
The following strategies, employing Digital Twin Technology, can help achieve this goal.
Data-Driven Decision Making
One of the key benefits of Digital Twin Technology is the ability to collect and analyze large amounts of data in real time.
By leveraging this data, manufacturers can make informed decisions about production processes.
This helps identify inefficiencies, streamline operations, and improve overall performance.
Implementing Lean Manufacturing
Lean manufacturing focuses on minimizing waste and maximizing efficiency.
Digital twins can help identify areas where waste occurs, such as excess inventory, overproduction, or inefficient workflows.
By addressing these issues, manufacturers can reduce waste, lower costs, and improve productivity.
Optimizing Supply Chain Management
Digital twins can provide valuable insights into the entire supply chain, from raw material procurement to final product delivery.
By monitoring and analyzing supply chain data, manufacturers can identify bottlenecks, improve logistics, and ensure timely delivery of products.
This leads to a more efficient and resilient supply chain.
Enhancing Quality Control
Maintaining product quality is crucial for customer satisfaction and brand reputation.
Digital twins can monitor production processes and detect any deviations from quality standards.
This enables manufacturers to address issues promptly and maintain high-quality standards throughout the production cycle.
Customizing Production
Digital twins allow for greater flexibility in production processes, enabling manufacturers to customize products to meet specific customer requirements.
By simulating different production scenarios and adjusting parameters accordingly, manufacturers can efficiently produce customized products without compromising quality or efficiency.
Challenges and Considerations
While Digital Twin Technology offers significant benefits for manufacturing, there are some challenges and considerations to keep in mind.
Data Security and Privacy
With the increased reliance on connected devices and data collection, ensuring data security and privacy is paramount.
Manufacturers must implement robust security measures to protect sensitive information from cyber threats.
Integration with Existing Systems
Integrating Digital Twin Technology with existing production systems can be complex and challenging.
It requires careful planning and coordination to ensure seamless integration and minimal disruptions to ongoing operations.
Cost of Implementation
Implementing Digital Twin Technology can be costly, especially for small to medium-sized enterprises.
However, the long-term benefits, such as improved efficiency and reduced costs, can outweigh the initial investment.
The Future of Digital Twin Technology in Manufacturing
Digital Twin Technology is still evolving, and its potential applications in manufacturing continue to expand.
As technology advances, we can expect even more sophisticated digital twins that offer enhanced capabilities and greater accuracy.
Manufacturers that adopt Digital Twin Technology and leverage its full potential will be better positioned to thrive in an increasingly competitive market.
In conclusion, Digital Twin Technology is a powerful tool for optimizing production processes in manufacturing.
By leveraging real-time data and virtual simulations, manufacturers can make informed decisions, improve efficiency, reduce costs, and maintain high-quality standards.
As this technology continues to evolve, it will play an increasingly important role in shaping the future of manufacturing.
資料ダウンロード
QCD調達購買管理クラウド「newji」は、調達購買部門で必要なQCD管理全てを備えた、現場特化型兼クラウド型の今世紀最高の購買管理システムとなります。
ユーザー登録
調達購買業務の効率化だけでなく、システムを導入することで、コスト削減や製品・資材のステータス可視化のほか、属人化していた購買情報の共有化による内部不正防止や統制にも役立ちます。
NEWJI DX
製造業に特化したデジタルトランスフォーメーション(DX)の実現を目指す請負開発型のコンサルティングサービスです。AI、iPaaS、および先端の技術を駆使して、製造プロセスの効率化、業務効率化、チームワーク強化、コスト削減、品質向上を実現します。このサービスは、製造業の課題を深く理解し、それに対する最適なデジタルソリューションを提供することで、企業が持続的な成長とイノベーションを達成できるようサポートします。
オンライン講座
製造業、主に購買・調達部門にお勤めの方々に向けた情報を配信しております。
新任の方やベテランの方、管理職を対象とした幅広いコンテンツをご用意しております。
お問い合わせ
コストダウンが利益に直結する術だと理解していても、なかなか前に進めることができない状況。そんな時は、newjiのコストダウン自動化機能で大きく利益貢献しよう!
(Β版非公開)