- お役立ち記事
- Key Approaches to Achieve High Durability in Plating Processing
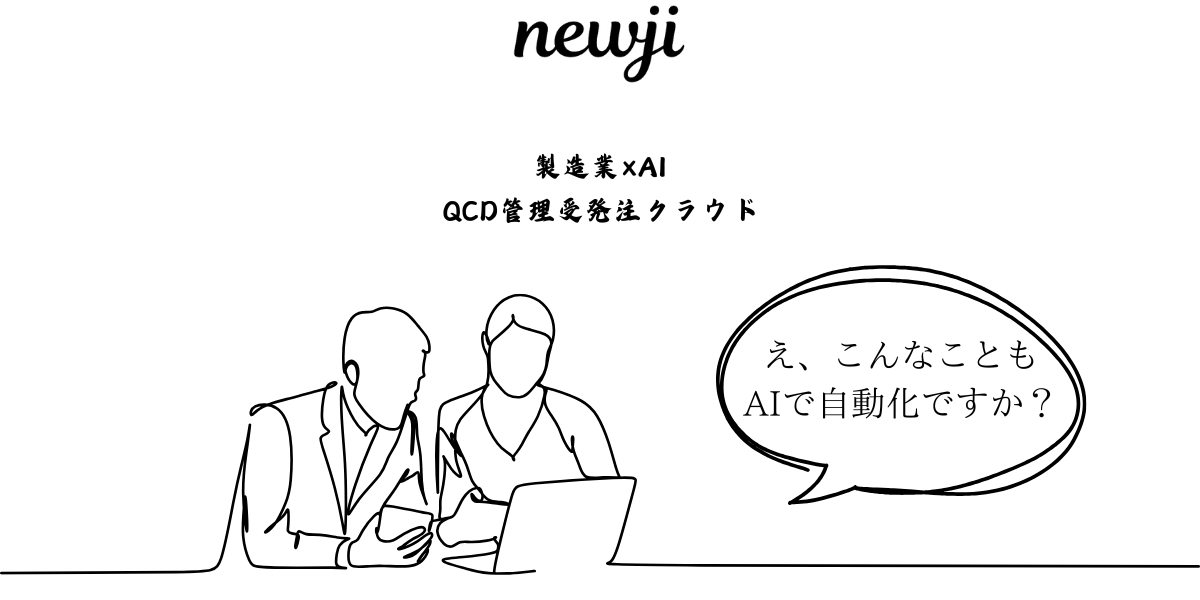
Key Approaches to Achieve High Durability in Plating Processing
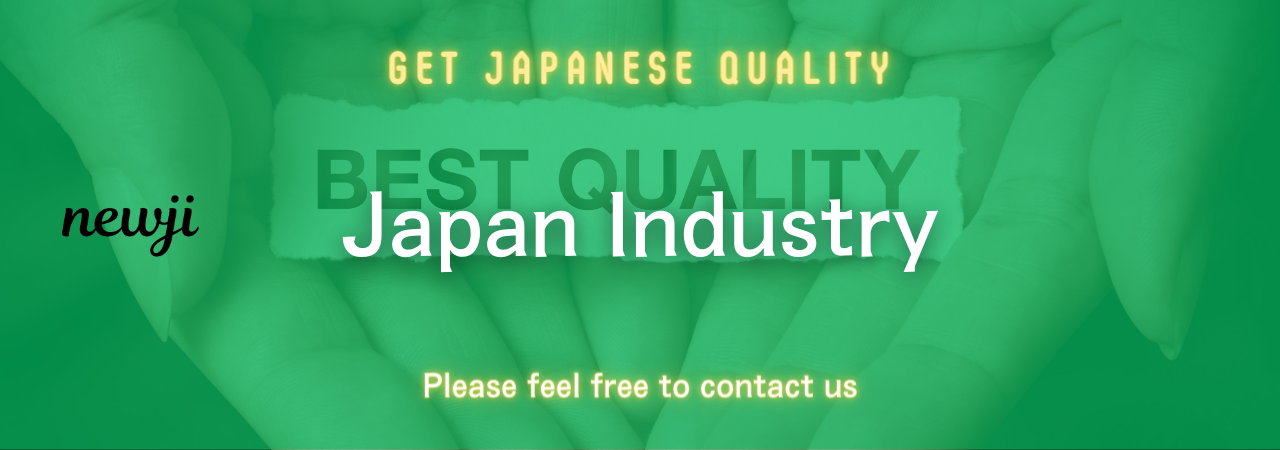
Achieving high durability in plating processing is essential for the longevity and performance of metal components.
Plating provides a protective layer that shields materials from corrosion, wear, and environmental factors.
But what are the key approaches to ensure high durability in plating?
We’ll explore some of the best practices and techniques used in the industry.
目次
Understanding Plating and Its Importance
Plating is a process where a metal coating is applied to a substrate, usually to improve its properties or appearance.
Common metals used for plating include nickel, chrome, zinc, and gold.
Plating can enhance conductivity, provide corrosion resistance, improve wear resistance, and offer aesthetic benefits.
Durable plating ensures that the plated components last longer even under adverse conditions.
Without high durability, components may fail prematurely, leading to increased costs and downtime.
Choosing the Right Plating Method
Electroplating
Electroplating is a popular method where an electric current is used to reduce dissolved metal cations, depositing them onto a conductive surface.
This method is particularly effective for achieving a uniform coating and excellent adhesion.
It’s commonly used in automotive, electronics, and jewelry industries.
Electroless Plating
Unlike electroplating, electroless plating does not require an external power source.
Instead, it relies on a chemical reduction reaction.
This method is excellent for plating non-conductive surfaces and complex geometries.
It’s widely used in industrial components, printed circuit boards, and aerospace applications.
Hot-Dip Galvanizing
Hot-dip galvanizing involves dipping the metal into molten zinc.
This forms a strong metallurgical bond that provides excellent corrosion resistance.
It’s particularly suitable for large structural components like beams and poles, providing long-lasting protection even in harsh environments.
Surface Preparation Techniques
Proper surface preparation is crucial for ensuring the durability of the plating.
Any contaminants, oxide layers, or irregularities can affect the adhesion and uniformity of the plating.
Cleaning and Degreasing
Cleaning the surface is the first step in ensuring proper adhesion.
This can involve solvent cleaning, ultrasonic cleaning, or alkaline cleaning.
Removing grease and oils ensures that the coating can bond directly to the substrate.
Surface Profiling
Creating a surface profile enhances the mechanical bond between the substrate and the plating.
Methods such as abrasive blasting, etching, or polishing can be used depending on the material and the required texture.
A good surface profile ensures that the plating adheres more effectively.
Activation
Activation is the process of treating the surface to make it more receptive to plating.
This can involve acid dips or other chemical treatments that create a clean, reactive surface.
Activation ensures that the metal ions deposit uniformly across the surface.
Choosing the Right Plating Material
The choice of plating material depends on the intended application and the desired properties.
Nickel
Nickel plating offers excellent corrosion resistance and wear resistance.
It’s commonly used in automotive, aerospace, and electronic components.
Additionally, nickel provides a smooth and aesthetically pleasing finish.
Zinc
Zinc plating is widely used for its corrosion resistance, especially in steel components.
It’s an economical choice for protecting metal parts in outdoor or moist environments.
However, it may require additional treatments like chromate conversion coating for enhanced durability.
Chromium
Chromium, or chrome plating, offers superior hardness and excellent wear resistance.
It’s used in applications where appearance and durability are both critical, such as automotive parts and decorative items.
However, chrome plating requires careful handling and environmental considerations due to its toxicity.
Controlling Plating Parameters
The conditions under which plating is carried out can significantly affect the durability of the finished product.
Temperature Control
Maintaining the appropriate temperature during plating ensures that the metal ions deposit uniformly.
Temperature variations can lead to defects or uneven plating.
Using temperature-controlled baths helps in achieving consistent results.
Current Density
In electroplating, controlling the current density is crucial.
Too high a current density can cause rough, burnished deposits, while too low can lead to poor adhesion.
Optimal current density varies with the material and application, requiring careful calibration.
Time
The plating time determines the thickness of the coating.
Ensuring the correct plating time is essential for achieving the desired durability.
Too short a time may result in an inadequate coating, while too long can lead to waste and potential issues such as stress cracking.
Post-Plating Treatments
After the plating process, certain treatments can enhance the durability and performance of the plated component.
Heat Treatment
Heat treatment can improve the hardness and adhesion of the plating.
Processes like annealing or tempering may be used depending on the plated material and application.
Passivation
Passivation involves treating the plated surface to remove free iron and enhance corrosion resistance.
This is particularly important for nickel and chrome plating.
Passivation can significantly extend the life of the plated component.
Top Coats and Sealants
Applying top coats or sealants can provide additional protection against environmental factors.
These coatings can be tailored to offer specific properties like UV resistance, moisture resistance, or additional corrosion resistance.
In conclusion, achieving high durability in plating processing involves a combination of appropriate methods, proper surface preparation, choice of materials, and controlled conditions.
By understanding and implementing these key approaches, manufacturers can ensure that their plated components perform reliably and last longer in their respective applications.
資料ダウンロード
QCD調達購買管理クラウド「newji」は、調達購買部門で必要なQCD管理全てを備えた、現場特化型兼クラウド型の今世紀最高の購買管理システムとなります。
ユーザー登録
調達購買業務の効率化だけでなく、システムを導入することで、コスト削減や製品・資材のステータス可視化のほか、属人化していた購買情報の共有化による内部不正防止や統制にも役立ちます。
NEWJI DX
製造業に特化したデジタルトランスフォーメーション(DX)の実現を目指す請負開発型のコンサルティングサービスです。AI、iPaaS、および先端の技術を駆使して、製造プロセスの効率化、業務効率化、チームワーク強化、コスト削減、品質向上を実現します。このサービスは、製造業の課題を深く理解し、それに対する最適なデジタルソリューションを提供することで、企業が持続的な成長とイノベーションを達成できるようサポートします。
オンライン講座
製造業、主に購買・調達部門にお勤めの方々に向けた情報を配信しております。
新任の方やベテランの方、管理職を対象とした幅広いコンテンツをご用意しております。
お問い合わせ
コストダウンが利益に直結する術だと理解していても、なかなか前に進めることができない状況。そんな時は、newjiのコストダウン自動化機能で大きく利益貢献しよう!
(Β版非公開)