- お役立ち記事
- Key Points for Compliance with Global Standards and Certification in Quality Assurance in Manufacturing
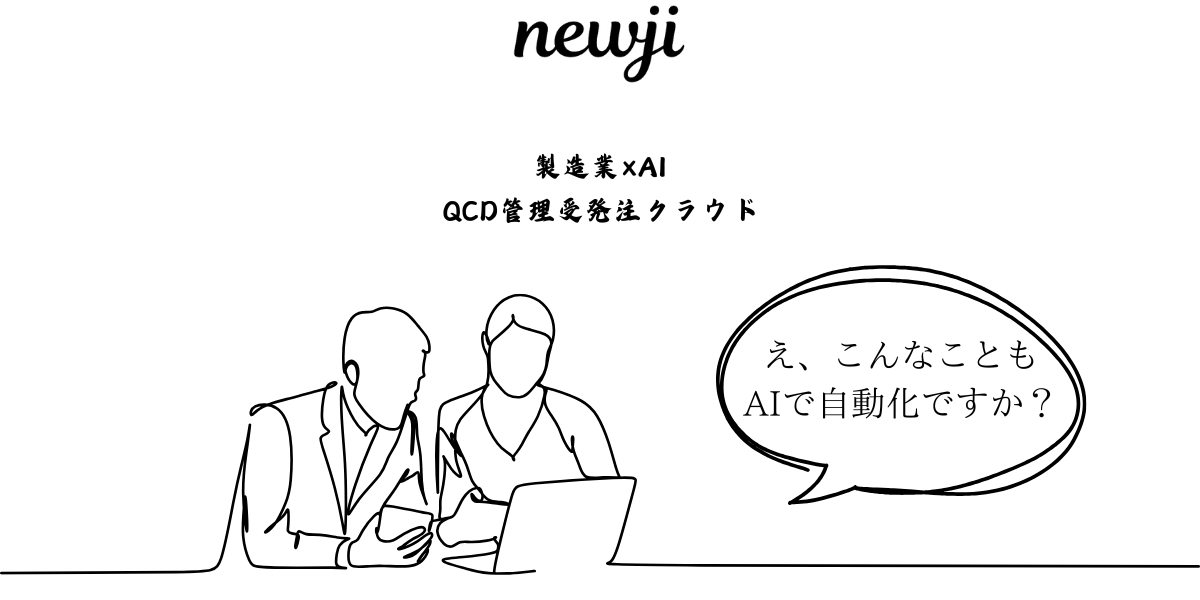
Key Points for Compliance with Global Standards and Certification in Quality Assurance in Manufacturing
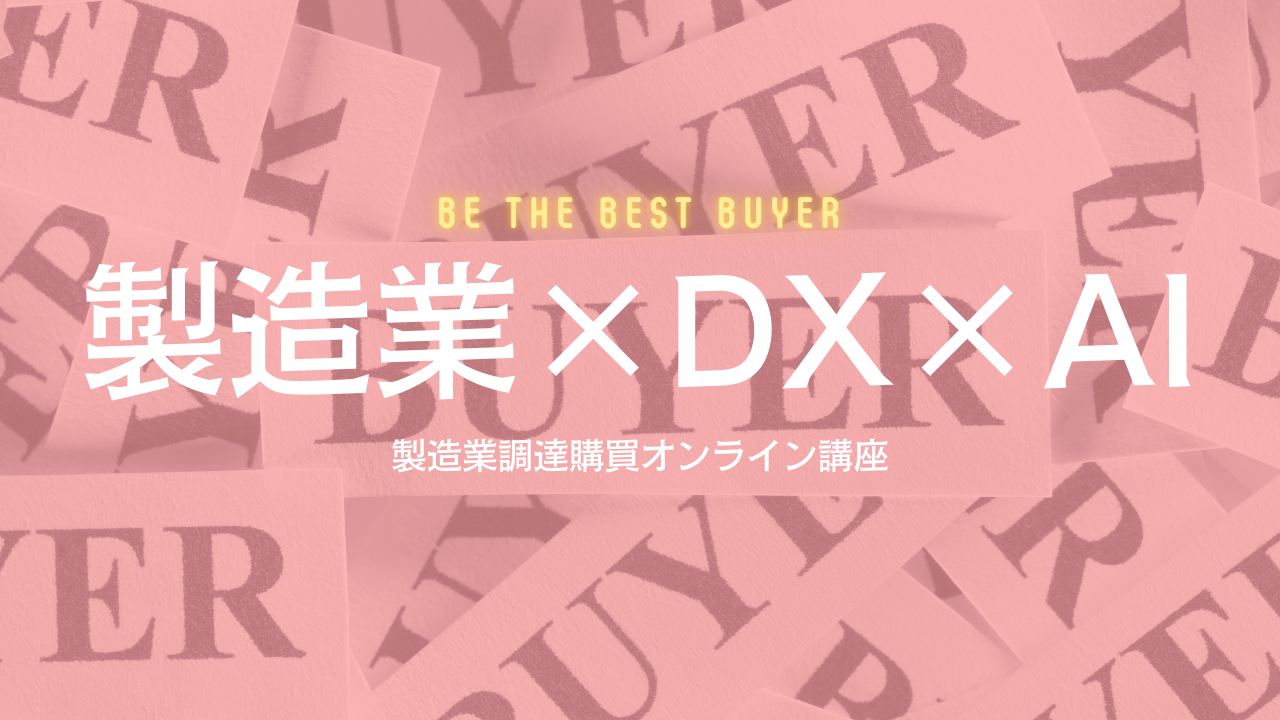
Over the past few decades, globalization has led to an increasing need for standards and certifications in quality assurance across many industries. Manufacturing is one such industry where compliance with global standards has become critical for companies to remain competitive in the global marketplace. Some key points to keep in mind regarding global standards and certification in manufacturing quality assurance include:
Establish robust quality management systems. Quality management systems like ISO 9001 provide a framework for manufacturers to establish processes for consistent product and service quality. They ensure that customer requirements are determined and met, and that risks to quality are identified and mitigated. Management reviews and internal audits help identify gaps and drive continuous improvement. Certification to ISO 9001 or another recognised standard demonstrates a commitment to quality that customers value.
Focus on risk-based thinking. Standards like ISO 9001:2015 emphasize risk-based thinking in quality management. Manufacturers must identify potential risks, assess their likelihood and impact, and put controls in place to mitigate critical risks. This could mean prioritizing resources for high-risk processes, implementing stricter controls, conducting more frequent inspections, and monitoring key risks closely with metrics. Taking a risk-based approach helps optimize quality assurance efforts.
Incorporate product safety standards. For manufacturers of consumer products, machinery, medical devices and many other goods, compliance with relevant product safety standards is essential. Examples include IEC standards for electrical equipment, ASTM standards for toys and children’s products, and ISO 13485 for medical devices. Meeting these standards helps ensure products are designed and manufactured to minimize safety risks and prevent injuries or accidents. This protects customers and builds brand trust.
Validate processes with certification. Third-party certification to recognized standards provides independent validation of a manufacturer’s quality processes and compliance claims. Customers increasingly demand certification for critical suppliers. Examples include ISO/TS 16949 (quality management for the automotive industry), ISO 22000 (food safety management), and ISO 50001 (energy management). Certification requires a rigorous external audit and re-certification cycles, keeping manufacturers on their toes to sustain compliance.
Monitor regulatory requirements. Manufacturers must keep abreast of changing regulatory quality and safety rules around the world. Examples include the FDA’s Quality System Regulation for medical devices, EU’s REACH regulations for chemical substances, NFPA standards for industrial equipment, and more. Late adoption of new rules could risk non-compliance, recalls or market access issues. Proactively monitoring regulations and factoring changes into quality systems helps minimize such risks.
Focus on people competency and training. Quality is only as good as the people implementing it daily. Manufacturers must assess competency needs, provide regular technical and compliance training to the workforce, and measure training effectiveness to close any skill gaps. Failing to empower employees with the right knowledge and skills could compromise product quality and compliance over the long run.
Collaborate with suppliers. Modern manufacturing value chains extend beyond company boundaries. Suppliers are an integral part of the overall quality system. Manufacturers must assess supplier quality capability, conduct audits, and work with suppliers to close gaps, resolve issues and drive performance improvement. Supplier quality metrics should be regularly reviewed at top management levels.
Leverage advanced quality tools. With increasing digitization and data capabilities, quality teams can employ tools like statistical process control, capability analysis, six sigma techniques, inspection automation, machine vision, predictive maintenance and more for more insightful quality oversight. Advanced analytics also help monitor for anomalies and detect quality issues early before they impact customers or compliance.
In summary, to remain competitive and meet evolving customer and compliance needs in today’s global marketplace, manufacturers must make quality assurance and compliance a top strategic priority. Adopting robust quality management systems, focusing on risk-based thinking, collaborating closely with suppliers, monitoring regulations and leveraging advanced tools can help optimize compliance with global standards and certifications in manufacturing.
資料ダウンロード
QCD調達購買管理クラウド「newji」は、調達購買部門で必要なQCD管理全てを備えた、現場特化型兼クラウド型の今世紀最高の購買管理システムとなります。
ユーザー登録
調達購買業務の効率化だけでなく、システムを導入することで、コスト削減や製品・資材のステータス可視化のほか、属人化していた購買情報の共有化による内部不正防止や統制にも役立ちます。
NEWJI DX
製造業に特化したデジタルトランスフォーメーション(DX)の実現を目指す請負開発型のコンサルティングサービスです。AI、iPaaS、および先端の技術を駆使して、製造プロセスの効率化、業務効率化、チームワーク強化、コスト削減、品質向上を実現します。このサービスは、製造業の課題を深く理解し、それに対する最適なデジタルソリューションを提供することで、企業が持続的な成長とイノベーションを達成できるようサポートします。
オンライン講座
製造業、主に購買・調達部門にお勤めの方々に向けた情報を配信しております。
新任の方やベテランの方、管理職を対象とした幅広いコンテンツをご用意しております。
お問い合わせ
コストダウンが利益に直結する術だと理解していても、なかなか前に進めることができない状況。そんな時は、newjiのコストダウン自動化機能で大きく利益貢献しよう!
(Β版非公開)