- お役立ち記事
- Key Points to Consider When Implementing Vacuum Molding Technology
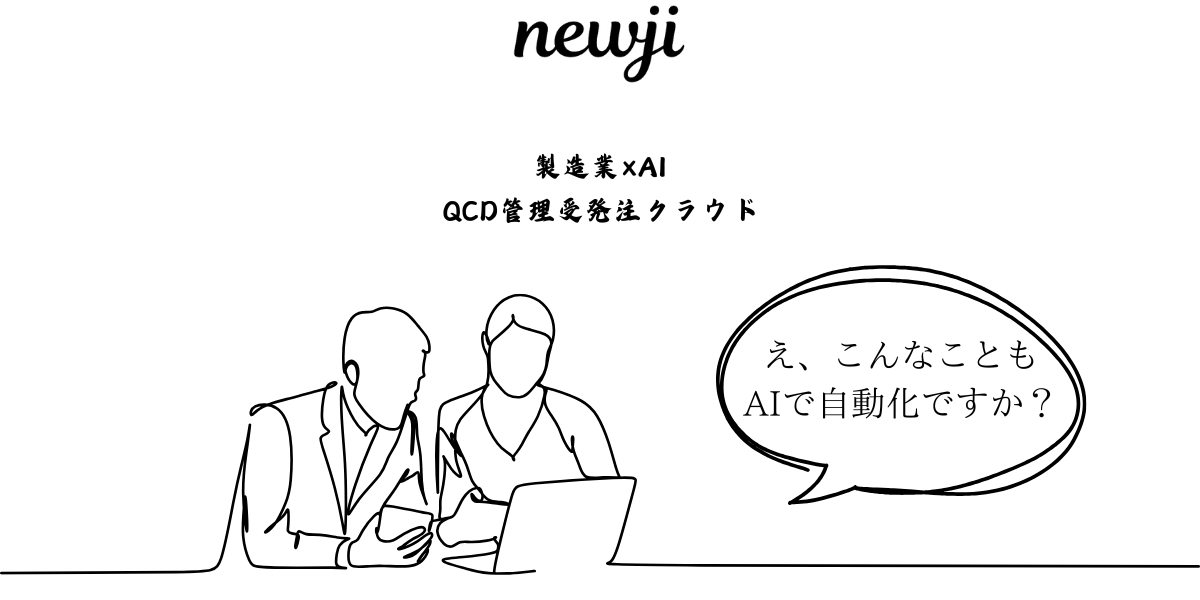
Key Points to Consider When Implementing Vacuum Molding Technology
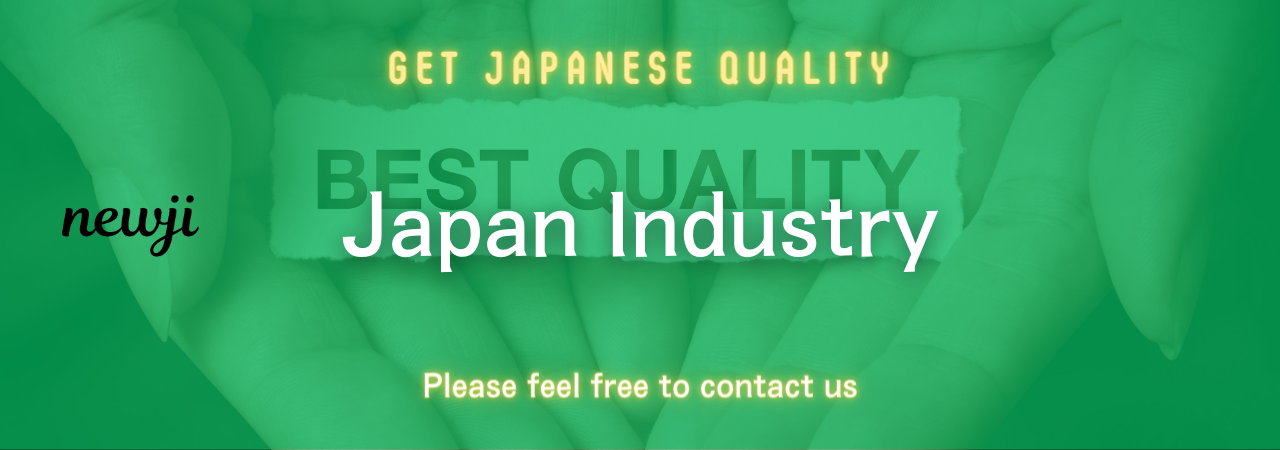
目次
Understanding Vacuum Molding Technology
Vacuum molding technology is a manufacturing process that utilizes vacuum pressure to form and shape plastic materials into desired shapes and structures.
Unlike other molding processes, vacuum molding is particularly useful for producing large, intricate parts with excellent surface detail and minimal waste.
The process involves heating a plastic sheet until it becomes pliable, placing it over a mold, and then drawing out the air between the sheet and the mold using vacuum pressure, causing the plastic to conform to the mold shape.
This technology is widely used in various industries, from automotive and aerospace to consumer goods and medical devices.
Before delving into the key points for implementing vacuum molding, it’s crucial to grasp its advantages, limitations, and applications.
Advantages of Vacuum Molding
One of the main advantages of vacuum molding is its cost-effectiveness, especially for low to medium-volume production runs.
The tooling costs for vacuum molding are generally lower than those for injection molding, as molds can be made from less expensive materials like wood, resin, or aluminum.
Another significant benefit is the design flexibility that vacuum molding offers.
This process allows for the creation of complex shapes and detailed features that might be challenging or costly to achieve using other methods.
Additionally, vacuum molding results in less material waste.
Since the process involves forming a single sheet of plastic, there is minimal scrap compared to other molding techniques, where excess material needs to be trimmed off.
Vacuum molding is also capable of producing parts with excellent surface quality, making it ideal for applications requiring smooth finishes and detailed textures.
Limitations of Vacuum Molding
Despite its benefits, vacuum molding comes with certain limitations.
The process is generally limited to thin-walled parts, which might not be suitable for all applications.
The thickness of the molded parts is determined by the thickness of the initial plastic sheet, which restricts the strength and durability of the final product.
Additionally, the cycle time for vacuum molding can be longer compared to injection molding, impacting production speed.
This slower cycle time might not be suitable for high-volume manufacturing.
Another limitation is the difficulty in achieving tight tolerances and uniform wall thickness, particularly for complex shapes.
This can be a critical consideration for parts requiring precise dimensions.
Key Points to Consider for Implementation
When implementing vacuum molding technology, there are several key factors to consider to ensure the success of the manufacturing process.
Material Selection
Selecting the appropriate material is vital for the success of vacuum molding.
Common materials used include ABS, PVC, polycarbonate, and acrylic.
Each material has its own set of properties, such as heat resistance, flexibility, and durability.
Choose a material that aligns with the requirements of your project and the intended application of the final product.
Mold Design and Build
The quality of the mold directly affects the quality of the final product.
Ensure that the mold design accommodates the desired shape and complexity of the part while allowing for efficient airflow.
Materials used for mold making should be selected based on the expected production volume.
For lower volumes, wood or resin molds may suffice, while aluminum molds are better suited for higher volumes due to their durability.
Proper Venting
Proper venting is essential to ensure that air can be effectively removed during the molding process.
Insufficient venting can lead to defects such as air bubbles or incomplete part formation.
Ensure that the mold design includes adequate venting channels to facilitate smooth and consistent vacuum application.
Heating and Cooling
Uniform heating of the plastic sheet is crucial for achieving a consistent thickness and shape.
Use controlled heating systems to maintain even temperatures across the sheet.
Cooling also plays an important role in the molding process.
Adequate cooling allows the formed part to set and solidify properly, ensuring dimensional accuracy and strength.
Quality Control
Implementing stringent quality control measures is necessary to ensure that the parts produced meet the required specifications.
Regularly inspect the molds, machines, and final products for any discrepancies or defects.
Use high-precision measurement tools to verify the dimensions and surface quality of the molded parts.
Applications of Vacuum Molding
Vacuum molding technology is versatile and finds applications across various industries.
Automotive Industry
In the automotive industry, vacuum molding is often used for producing interior panels, dashboards, and door liners.
The ability to create complex shapes and detailed textures makes it ideal for custom automotive parts.
Aerospace Sector
The aerospace industry benefits from vacuum molding due to its lightweight properties and excellent surface finish.
Parts such as interior cabin components and lightweight housing structures are commonly manufactured using this process.
Consumer Goods
Many consumer goods, such as packaging, electronic housings, and household appliances, are produced using vacuum molding.
The process enables the production of aesthetically appealing and functional products with intricate designs.
Conclusion
Vacuum molding technology is a powerful and versatile manufacturing process that offers numerous advantages for producing detailed and cost-effective parts.
By understanding the key factors involved in its implementation, businesses can effectively leverage this technology to meet their production needs.
From material selection and mold design to proper venting and quality control, each aspect plays a crucial role in ensuring successful outcomes.
With its wide range of applications across various industries, vacuum molding continues to be a valuable tool in the world of manufacturing.
資料ダウンロード
QCD調達購買管理クラウド「newji」は、調達購買部門で必要なQCD管理全てを備えた、現場特化型兼クラウド型の今世紀最高の購買管理システムとなります。
ユーザー登録
調達購買業務の効率化だけでなく、システムを導入することで、コスト削減や製品・資材のステータス可視化のほか、属人化していた購買情報の共有化による内部不正防止や統制にも役立ちます。
NEWJI DX
製造業に特化したデジタルトランスフォーメーション(DX)の実現を目指す請負開発型のコンサルティングサービスです。AI、iPaaS、および先端の技術を駆使して、製造プロセスの効率化、業務効率化、チームワーク強化、コスト削減、品質向上を実現します。このサービスは、製造業の課題を深く理解し、それに対する最適なデジタルソリューションを提供することで、企業が持続的な成長とイノベーションを達成できるようサポートします。
オンライン講座
製造業、主に購買・調達部門にお勤めの方々に向けた情報を配信しております。
新任の方やベテランの方、管理職を対象とした幅広いコンテンツをご用意しております。
お問い合わせ
コストダウンが利益に直結する術だと理解していても、なかなか前に進めることができない状況。そんな時は、newjiのコストダウン自動化機能で大きく利益貢献しよう!
(Β版非公開)