- お役立ち記事
- Key Quality Control Points to Prevent Grinding Issues
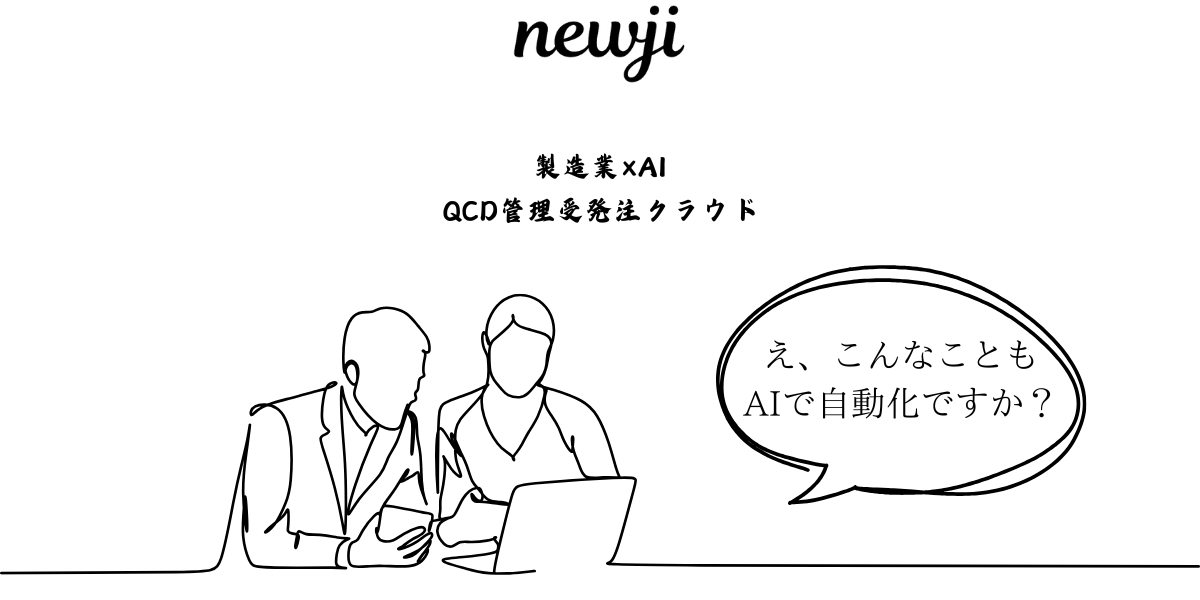
Key Quality Control Points to Prevent Grinding Issues
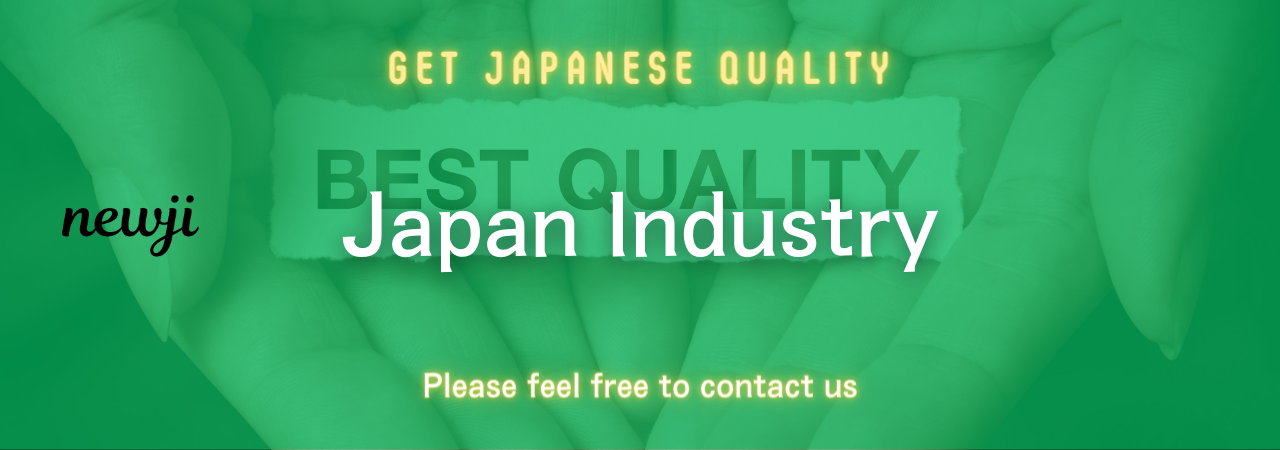
Quality control is essential in any manufacturing process, but it’s especially vital when it comes to grinding.
Grinding plays a key role in shaping and finishing materials, ensuring the final product meets required specifications.
However, without proper quality control measures, grinding issues can arise, leading to subpar products and increased costs.
In this article, we will discuss key quality control points to prevent grinding issues.
By following these guidelines, manufacturers can achieve better consistency and quality in their products.
目次
Understanding the Importance of Grinding
Grinding is a critical process in the manufacturing industry.
It involves the removal of excess material from a workpiece using a rotating abrasive wheel.
The purpose of grinding is to produce a smooth surface, achieve high precision, and meet specific dimensional standards.
Given its importance, even minor problems in the grinding process can lead to significant issues in the final product.
Therefore, it is crucial to implement stringent quality control measures to ensure the grinding process is efficient and effective.
Key Quality Control Points
Material Selection
The first step in preventing grinding issues is to carefully select the material to be ground.
Different materials have unique properties, such as hardness and toughness, which can affect the grinding process.
Using the appropriate material for the specific application is essential to avoid issues during grinding.
Conducting a thorough analysis of the material’s properties before starting the grinding process can significantly reduce the likelihood of problems.
This involves testing the material’s hardness, microstructure, and chemical composition to ensure it is suitable for grinding.
Grinding Wheel Selection
Choosing the right grinding wheel is another critical quality control point.
Grinding wheels come in various shapes, sizes, and materials, each designed for specific grinding tasks.
Selecting the wrong grinding wheel can lead to poor performance, increased wear, and potential damage to the workpiece.
To select the appropriate grinding wheel, consider the following factors:
– Material of the workpiece
– Type of grinding (surface, cylindrical, etc.)
– Desired surface finish and precision
– Wheel speed and feed rate
Consulting with grinding wheel manufacturers and experts can also help in making an informed decision.
Machine Calibration and Maintenance
Regular calibration and maintenance of grinding machines are crucial to preventing grinding issues.
Machines that are not properly calibrated can produce inaccurate results, leading to defective products.
Similarly, worn-out or poorly maintained machines can cause inconsistencies in the grinding process.
Implementing a routine maintenance schedule for grinding machines can help identify and address potential issues before they become problematic.
This includes checking and replacing worn-out parts, lubricating moving components, and calibrating the machine to ensure it operates within acceptable tolerances.
Coolant Selection and Management
Coolant plays a vital role in the grinding process by reducing heat and friction, which can cause damage to the workpiece and grinding wheel.
Using the right type of coolant and maintaining proper coolant levels is essential for effective grinding.
Selecting a suitable coolant depends on several factors, including the material being ground, grinding speed, and the desired surface finish.
Regularly monitoring coolant levels and maintaining the correct concentration also help prevent issues such as overheating and surface burns.
Operator Training
Well-trained operators are critical to ensuring the grinding process runs smoothly.
Operators need to be knowledgeable about the grinding machinery, materials, and techniques.
They should also be capable of identifying potential issues and taking corrective actions when necessary.
Investing in regular training sessions for operators can improve their skills and knowledge, leading to a more efficient grinding process.
Training should cover machine operation, proper setup, maintenance procedures, and safety protocols.
Monitoring and Inspection
In-process Monitoring
In-process monitoring is a proactive approach to identifying and addressing grinding issues as they occur.
This involves continuously monitoring the grinding process for any signs of problems, such as excessive vibration, noise, or temperature changes.
Using advanced monitoring systems, such as sensors and software, can provide real-time data on the grinding process.
This data can help operators make informed decisions and take corrective actions promptly, reducing the likelihood of defects.
Post-Grinding Inspection
Conducting a thorough inspection of the workpieces after grinding is essential to ensuring quality.
This involves checking for any surface defects, dimensional inaccuracies, and other issues that may have arisen during the grinding process.
Utilizing precision measurement tools, such as micrometers and surface roughness testers, can help in accurately assessing the quality of the workpieces.
Documenting the inspection results and analyzing them can also provide valuable insights for continuous improvement.
Continuous Improvement
Quality control is an ongoing process, and continuous improvement is key to maintaining high standards in grinding.
By regularly reviewing and analyzing the grinding process, manufacturers can identify areas for improvement and implement necessary changes.
Gathering feedback from operators and customers can also provide valuable insights into potential issues and areas for enhancement.
Implementing a culture of continuous improvement within the organization can lead to better quality products and more efficient processes.
Conclusion
Preventing grinding issues through effective quality control measures is essential for achieving high-quality products in the manufacturing industry.
By focusing on key points such as material selection, grinding wheel choice, machine calibration, coolant management, and operator training, manufacturers can minimize defects and improve the grinding process.
Additionally, implementing in-process monitoring and post-grinding inspection can help in identifying and addressing issues promptly.
Emphasizing continuous improvement ensures that the grinding process remains efficient and effective, leading to better products and satisfied customers.
資料ダウンロード
QCD調達購買管理クラウド「newji」は、調達購買部門で必要なQCD管理全てを備えた、現場特化型兼クラウド型の今世紀最高の購買管理システムとなります。
ユーザー登録
調達購買業務の効率化だけでなく、システムを導入することで、コスト削減や製品・資材のステータス可視化のほか、属人化していた購買情報の共有化による内部不正防止や統制にも役立ちます。
NEWJI DX
製造業に特化したデジタルトランスフォーメーション(DX)の実現を目指す請負開発型のコンサルティングサービスです。AI、iPaaS、および先端の技術を駆使して、製造プロセスの効率化、業務効率化、チームワーク強化、コスト削減、品質向上を実現します。このサービスは、製造業の課題を深く理解し、それに対する最適なデジタルソリューションを提供することで、企業が持続的な成長とイノベーションを達成できるようサポートします。
オンライン講座
製造業、主に購買・調達部門にお勤めの方々に向けた情報を配信しております。
新任の方やベテランの方、管理職を対象とした幅広いコンテンツをご用意しております。
お問い合わせ
コストダウンが利益に直結する術だと理解していても、なかなか前に進めることができない状況。そんな時は、newjiのコストダウン自動化機能で大きく利益貢献しよう!
(Β版非公開)