- お役立ち記事
- Know-How for Utilizing the Backgauge System in Press Brakes
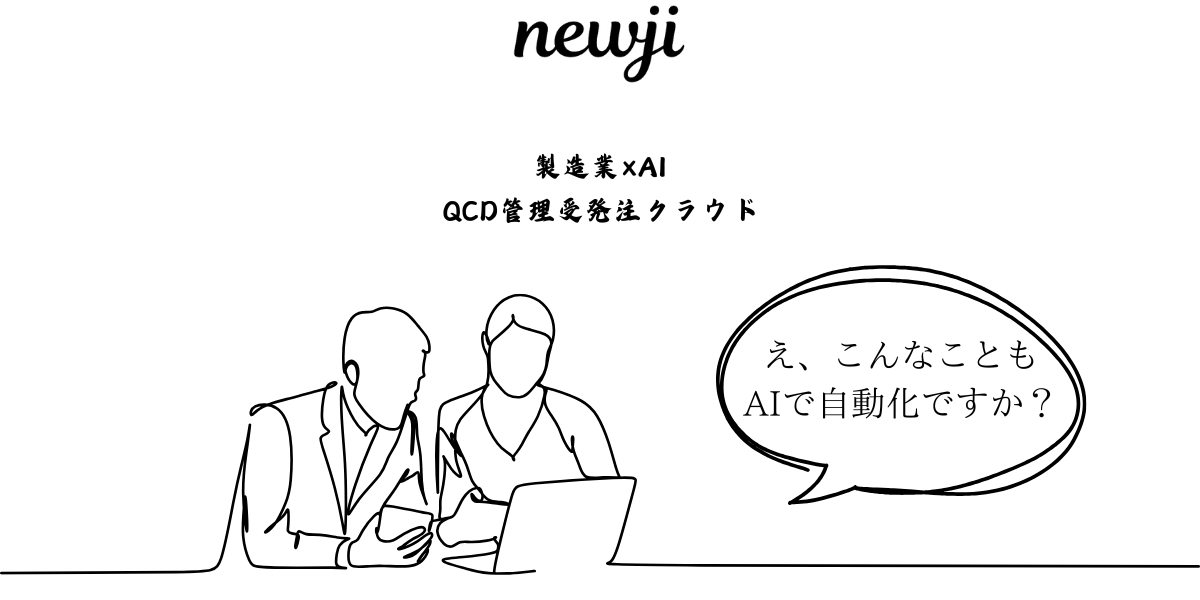
Know-How for Utilizing the Backgauge System in Press Brakes
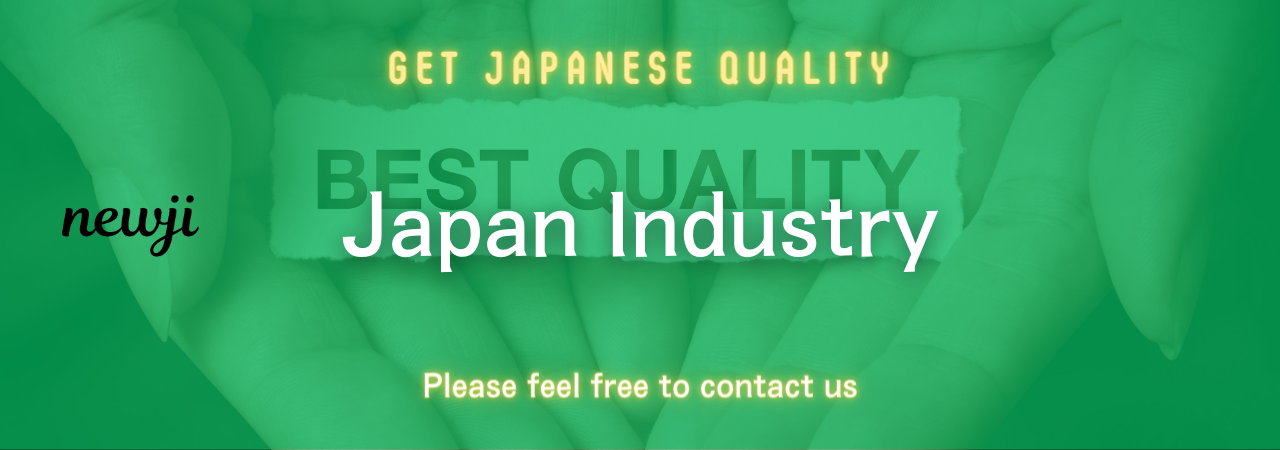
When it comes to achieving precision in metal forming, the backgauge system in press brakes plays a crucial role.
Understanding how to utilize this system effectively can greatly enhance the quality and efficiency of your work.
Whether you are a seasoned professional or a beginner in metal fabrication, this guide provides essential tips and insights on maximizing the functionality of the backgauge system in press brakes.
目次
The Basics of the Backgauge System
The backgauge system is a critical component of a press brake, used to position and align metal sheets accurately.
It ensures that each bend is made in the correct place, helping to achieve consistent and precise results.
Primarily, the backgauge serves as a reference point, guiding the metal sheet to the desired position before the press brake forms the bend.
Types of Backgauge Systems
Backgauge systems come in a variety of designs, each with its own set of features.
**Manual Backgauges**: These are controlled manually and are generally used for simpler tasks or in smaller workshops.
They require the operator to adjust the position by hand, relying on measurements and visual inspection.
**CNC Backgauges**: Computer Numerical Control (CNC) backgauges are automated and allow for precise adjustments through a computer interface.
These systems are ideal for high-precision tasks and repetitive operations, reducing the margin of error significantly.
**Hydraulic Backgauges**: These systems use hydraulic power to achieve movements and adjustments.
They offer robust performance and can handle heavier workloads than manual or CNC systems.
Setting Up the Backgauge System
Correctly setting up your backgauge system is essential for ensuring accurate bends.
The setup process varies depending on whether you are using a manual, CNC, or hydraulic system.
Manual Backgauge Setup
For manual systems, begin by measuring the distance from the die to the backgauge fingers.
Use a tape measure or a caliper for precision.
Adjust the backgauge fingers to the desired position, ensuring they are firmly secured.
CNC Backgauge Setup
If you are using a CNC backgauge, the setup process involves entering the required dimensions into the control panel.
Input the distance and angles as per your job requirements.
The CNC system will automatically position the backgauge based on the programmed settings.
Hydraulic Backgauge Setup
For hydraulic systems, the setup often involves both manual input and automated adjustments.
Consult the machine’s manual for specific instructions, as each model may have unique requirements.
Effective Utilization Techniques
Correctly utilizing the backgauge system can significantly impact your productivity and the quality of your work.
Here are some techniques to ensure you get the most out of your backgauge system.
Regular Calibration
Regular calibration of your backgauge system is essential for maintaining precision.
Calibration involves checking and adjusting the backgauge to ensure it provides accurate measurements and positioning.
For CNC systems, follow the manufacturer’s guidelines for calibration intervals.
For manual systems, periodic checks with measuring tools are necessary.
Material Considerations
Different materials behave differently under pressure.
Ensure that your backgauge settings consider the type of material you are working with.
Heavier and thicker materials may require different positioning and pressure settings compared to lighter, thinner sheets.
Program Optimizations for CNC Systems
When using CNC backgauge systems, optimizing your programs can lead to better efficiency and accuracy.
Review your program settings regularly and make adjustments based on the specific requirements of each job.
Utilize simulation features if available to predict and correct potential issues before they occur on the actual workpiece.
Maintenance Tips
Maintaining your backgauge system is crucial for its longevity and performance.
Here are some maintenance tips to keep in mind:
Regular Cleaning
Dust and debris can affect the accuracy of your backgauge system.
Ensure that the backgauge and its components are regularly cleaned.
For CNC and hydraulic systems, check the manufacturer’s recommendations for cleaning procedures.
Check for Wear and Tear
Inspect the backgauge components for signs of wear and tear.
Replace worn parts promptly to avoid compromising the system’s accuracy.
Regularly check screws and bolts to ensure they are tight and secure.
Lubrication
For hydraulic backgauge systems, proper lubrication is essential.
Follow the lubrication schedule advised by the manufacturer to keep the system running smoothly.
Ensure that only recommended lubricants are used to avoid damaging the components.
Common Issues and Troubleshooting
Even with proper setup and maintenance, you may encounter some common issues with your backgauge system.
Inaccurate Positioning
If you notice that the backgauge is not positioning accurately, first check for any mechanical obstructions or debris.
For CNC systems, verify the program settings and recalibrate if necessary.
System Jams
System jams can occur due to foreign objects or metal shavings getting caught in the backgauge tracks.
If a jam occurs, power off the machine and carefully remove any obstructions.
Hydraulic Leaks
Hydraulic systems may occasionally develop leaks.
Inspect the hydraulic lines and fittings regularly and replace any damaged parts promptly.
Leaks can affect the performance and accuracy of the backgauge.
Conclusion
Mastering the use of the backgauge system in press brakes requires a combination of proper setup, regular maintenance, and effective utilization techniques.
By paying attention to these key areas, you can ensure that your press brake delivers precise and consistent results every time.
Whether you are using a manual, CNC, or hydraulic backgauge system, understanding its functionalities and limitations will help you maximize its potential.
資料ダウンロード
QCD調達購買管理クラウド「newji」は、調達購買部門で必要なQCD管理全てを備えた、現場特化型兼クラウド型の今世紀最高の購買管理システムとなります。
ユーザー登録
調達購買業務の効率化だけでなく、システムを導入することで、コスト削減や製品・資材のステータス可視化のほか、属人化していた購買情報の共有化による内部不正防止や統制にも役立ちます。
NEWJI DX
製造業に特化したデジタルトランスフォーメーション(DX)の実現を目指す請負開発型のコンサルティングサービスです。AI、iPaaS、および先端の技術を駆使して、製造プロセスの効率化、業務効率化、チームワーク強化、コスト削減、品質向上を実現します。このサービスは、製造業の課題を深く理解し、それに対する最適なデジタルソリューションを提供することで、企業が持続的な成長とイノベーションを達成できるようサポートします。
オンライン講座
製造業、主に購買・調達部門にお勤めの方々に向けた情報を配信しております。
新任の方やベテランの方、管理職を対象とした幅広いコンテンツをご用意しております。
お問い合わせ
コストダウンが利益に直結する術だと理解していても、なかなか前に進めることができない状況。そんな時は、newjiのコストダウン自動化機能で大きく利益貢献しよう!
(Β版非公開)