- お役立ち記事
- Latest Process Improvement Techniques for Achieving Productivity Gains
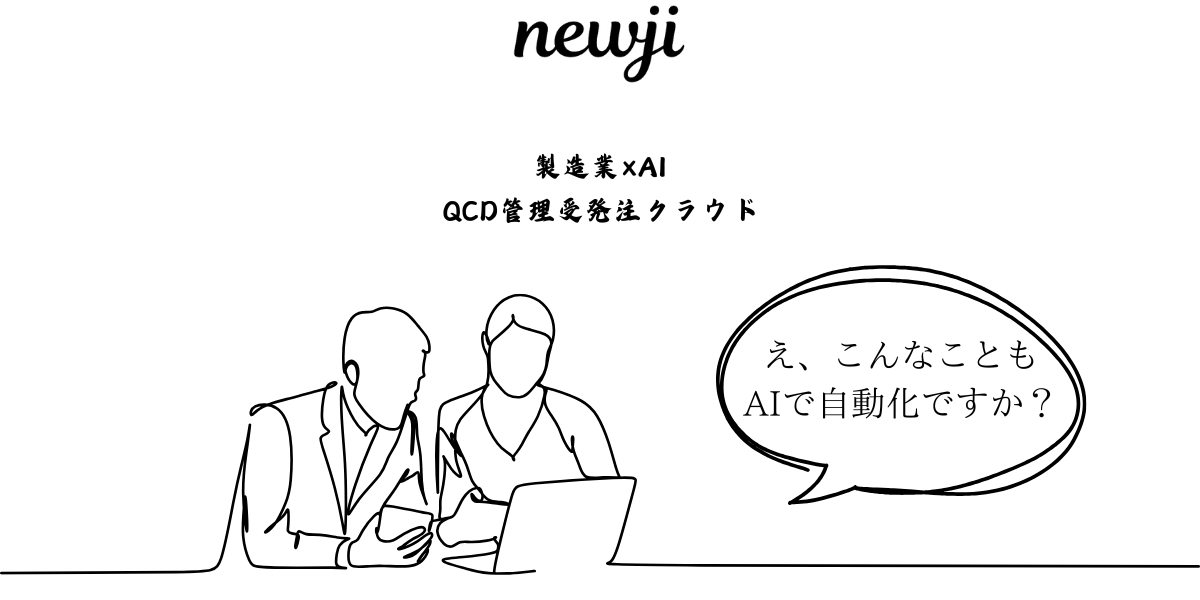
Latest Process Improvement Techniques for Achieving Productivity Gains
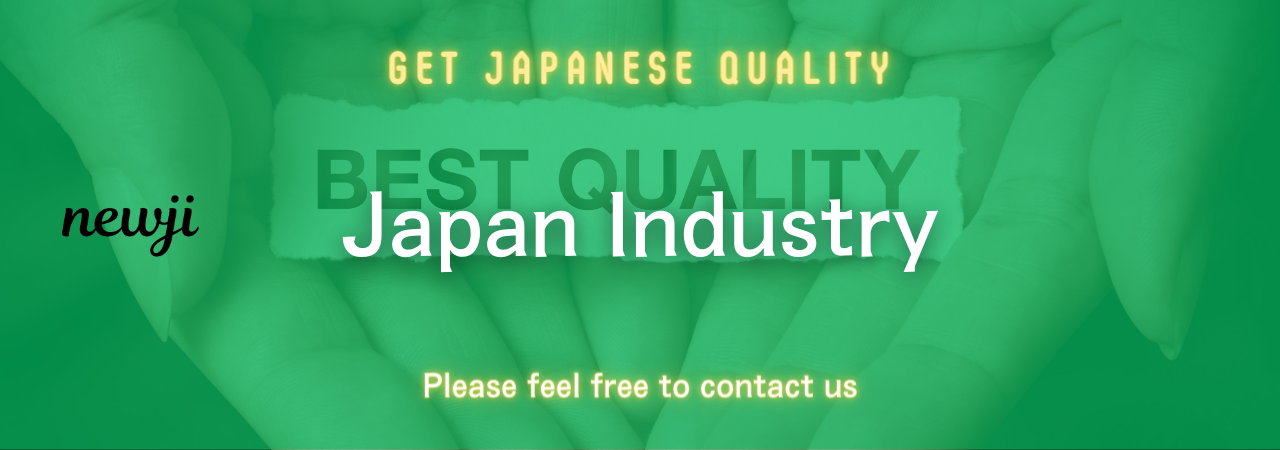
In today’s fast-paced business landscape, improving productivity is essential for maintaining a competitive edge.
Process improvement techniques are strategies and methodologies used to optimize workflow and enhance efficiency.
By implementing these techniques, businesses can streamline operations, reduce costs, and boost overall productivity.
In this article, we’ll explore some of the latest process improvement techniques that can help your organization achieve significant productivity gains.
目次
Understanding Process Improvement
Process improvement is the proactive task of identifying, analyzing, and optimizing existing business processes to enhance performance.
It involves making systematic changes to workflows, eliminating inefficiencies, and ensuring that resources are utilized effectively.
With the right approach, process improvement can lead to better quality products or services, increased customer satisfaction, and a more engaged workforce.
Lean Methodology
What is Lean?
Lean methodology is a popular approach focused on minimizing waste and maximizing value.
It originated from the Toyota Production System and has since been adopted by various industries.
The primary goal of Lean is to create more value for customers with fewer resources.
Key Principles of Lean
1. **Value Identification**: Understand what the customer perceives as value and focus on activities that contribute to this value.
2. **Value Stream Mapping**: Visualize the entire process to identify areas of waste and inefficiency.
3. **Flow Optimization**: Ensure that the process flows smoothly without interruptions or bottlenecks.
4. **Pull System**: Produce only what is needed when it is needed, rather than producing in anticipation of demand.
5. **Continuous Improvement**: Encourage a culture of ongoing improvement by regularly reviewing and refining processes.
Six Sigma
What is Six Sigma?
Six Sigma is a data-driven methodology aimed at improving the quality of processes by identifying and removing causes of defects.
It uses a set of quality management tools, including statistical analysis, to achieve this goal.
Six Sigma is particularly effective in environments where precision and accuracy are critical.
The DMAIC Framework
Six Sigma projects typically follow the DMAIC framework, which stands for:
1. **Define**: Identify the problem and set clear objectives for improvement.
2. **Measure**: Collect data to understand the current performance and quantify the problem.
3. **Analyze**: Identify root causes of the problem using data analysis techniques.
4. **Improve**: Develop and implement solutions to address the root causes.
5. **Control**: Monitor the improvements to ensure that they are sustained over time.
Agile Methodology
What is Agile?
Agile methodology is a flexible and iterative approach to project management and process improvement.
It emphasizes adaptability, collaboration, and customer feedback.
Originally developed for software development, Agile principles are now applied to various business processes.
Core Principles of Agile
1. **Customer Collaboration**: Engage with customers frequently to gather feedback and ensure that their needs are met.
2. **Incremental Delivery**: Deliver small, usable increments of the final product, allowing for continuous improvement.
3. **Cross-Functional Teams**: Foster collaboration among team members with diverse skills and expertise.
4. **Responding to Change**: Be flexible and ready to adapt to changes as new information emerges.
Kaizen
What is Kaizen?
Kaizen is a Japanese term meaning “continuous improvement.”
It is a philosophy that encourages all employees, regardless of their role, to continuously seek ways to improve processes.
Kaizen is not limited to major changes; it also emphasizes small, incremental improvements.
Implementing Kaizen
1. **Empower Employees**: Encourage every employee to identify inefficiencies and suggest improvements.
2. **Focus on Small Changes**: Implement small, manageable changes that can lead to significant improvements over time.
3. **Regular Review**: Schedule regular review sessions to assess progress and identify new opportunities for improvement.
Business Process Reengineering (BPR)
What is BPR?
Business Process Reengineering involves fundamentally rethinking and redesigning business processes to achieve dramatic improvements in performance.
It is a more radical approach compared to other methodologies and often involves significant changes to organizational structure and workflows.
Steps in BPR
1. **Identify Processes for Redesign**: Focus on processes that have the most significant impact on business performance.
2. **Analyze Current Processes**: Understand how the existing processes work and identify areas of inefficiency.
3. **Develop New Processes**: Design new, more efficient processes that better meet business objectives.
4. **Implement Changes**: Roll out the new processes and make any necessary adjustments based on real-world performance.
5. **Monitor and Optimize**: Continuously monitor the new processes and make improvements as needed.
Conclusion
Implementing the latest process improvement techniques is crucial for achieving productivity gains in any organization.
By adopting methodologies such as Lean, Six Sigma, Agile, Kaizen, and Business Process Reengineering, businesses can streamline their operations, reduce waste, and better utilize their resources.
The key to successful process improvement lies in creating a culture of continuous improvement and empowering employees to participate actively in the process.
By doing so, organizations can achieve sustainable growth and remain competitive in an ever-evolving marketplace.
資料ダウンロード
QCD調達購買管理クラウド「newji」は、調達購買部門で必要なQCD管理全てを備えた、現場特化型兼クラウド型の今世紀最高の購買管理システムとなります。
ユーザー登録
調達購買業務の効率化だけでなく、システムを導入することで、コスト削減や製品・資材のステータス可視化のほか、属人化していた購買情報の共有化による内部不正防止や統制にも役立ちます。
NEWJI DX
製造業に特化したデジタルトランスフォーメーション(DX)の実現を目指す請負開発型のコンサルティングサービスです。AI、iPaaS、および先端の技術を駆使して、製造プロセスの効率化、業務効率化、チームワーク強化、コスト削減、品質向上を実現します。このサービスは、製造業の課題を深く理解し、それに対する最適なデジタルソリューションを提供することで、企業が持続的な成長とイノベーションを達成できるようサポートします。
オンライン講座
製造業、主に購買・調達部門にお勤めの方々に向けた情報を配信しております。
新任の方やベテランの方、管理職を対象とした幅広いコンテンツをご用意しております。
お問い合わせ
コストダウンが利益に直結する術だと理解していても、なかなか前に進めることができない状況。そんな時は、newjiのコストダウン自動化機能で大きく利益貢献しよう!
(Β版非公開)