- お役立ち記事
- Latest Technologies in Air Tools and Their Applications in Manufacturing
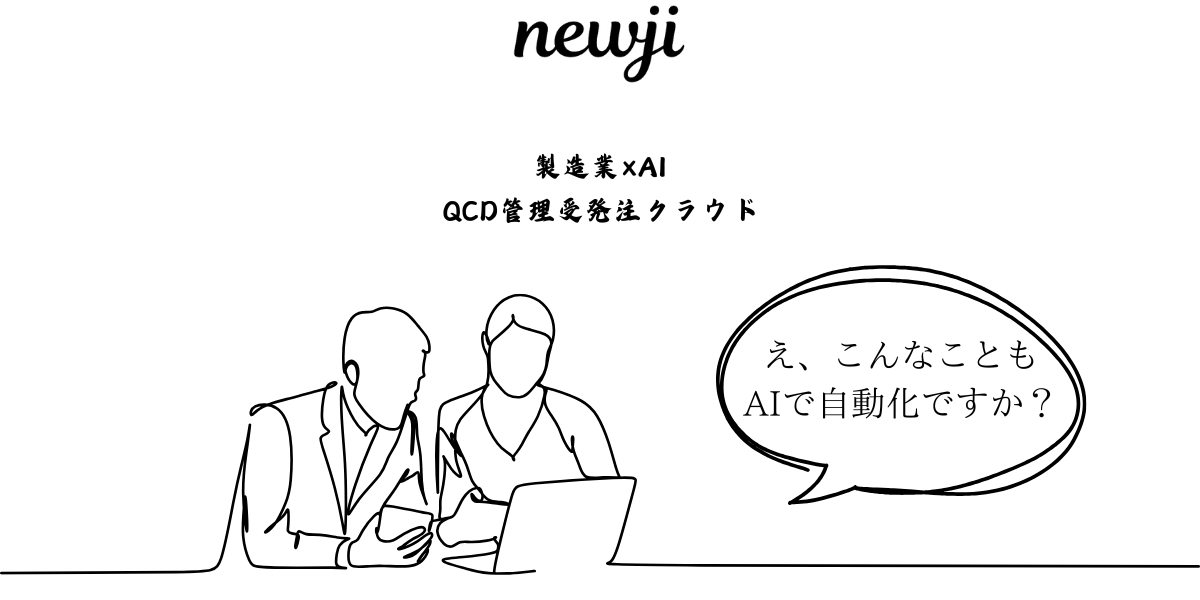
Latest Technologies in Air Tools and Their Applications in Manufacturing
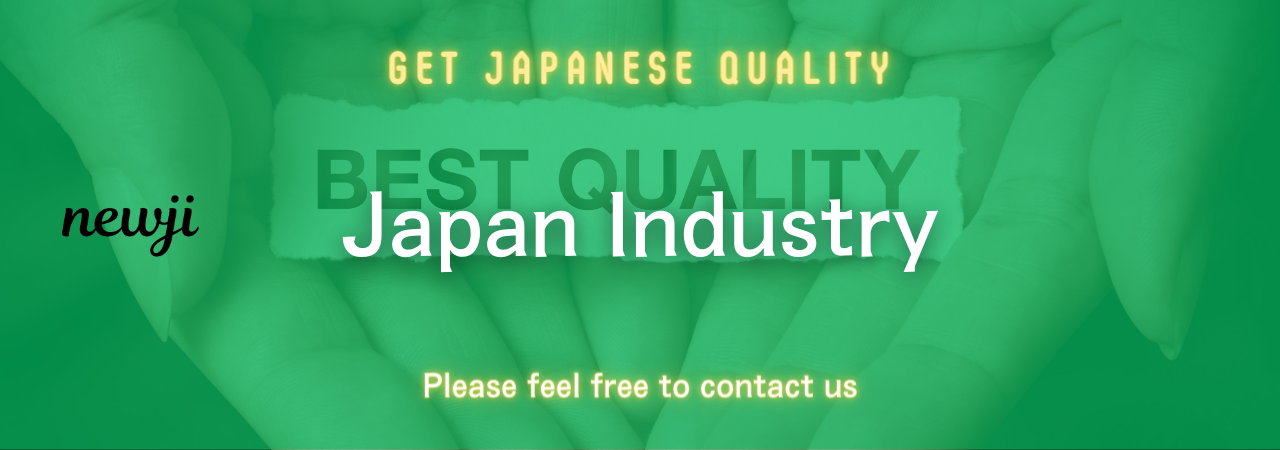
Technology is advancing at an unprecedented pace, and one area that has seen significant development is air tools. From the humble beginnings of simple manual devices, air tools have transformed into sophisticated, high-performance machines, instrumental in various industries, particularly manufacturing. In this article, we’ll explore the latest technologies in air tools and their applications in manufacturing.
目次
Understanding Air Tools
Air tools, also known as pneumatic tools, operate using compressed air. They are valued for their efficiency, power, and durability. While traditional tools rely on electricity or manual effort, air tools harness the power of compressed air to perform tasks more quickly and with greater precision.
Recent Technological Advances in Air Tools
Smart Air Tools
One of the most significant advancements in air tools is the emergence of smart air tools. These modern devices come equipped with sensors and Internet of Things (IoT) capabilities, allowing for real-time monitoring and data collection.
For example, smart torque wrenches can provide real-time feedback on torque application, ensuring precision and reducing the risk of over-tightening. This functionality is crucial in industries such as aerospace and automotive manufacturing, where precision is paramount.
Energy Efficiency
Energy efficiency is becoming increasingly crucial in manufacturing. Modern air tools are designed to consume less energy while delivering the same or even greater power. Innovations such as variable-speed drives and energy-efficient motors have made it possible for these tools to operate more efficiently.
Manufacturers are now more mindful of their carbon footprint and operational costs. Using energy-efficient air tools means reduced energy consumption, which translates to cost savings and a smaller environmental impact.
Sound Reduction Technologies
Noise pollution in manufacturing plants is a significant concern. Prolonged exposure to high noise levels can lead to hearing loss and other health issues for workers. Recent advancements in air tools include sound reduction technologies that minimize noise levels while maintaining performance.
For instance, modern air drills and impact wrenches are designed with noise-reducing mechanisms that dampen sound without compromising the tools’ capabilities. This improvement not only enhances worker safety but also creates a more pleasant working environment.
Compact and Lightweight Designs
Manufacturers are continually seeking ways to make their tools more user-friendly. This demand has led to the development of compact and lightweight air tools that are easier to handle and maneuver, without sacrificing performance.
Lighter tools reduce operator fatigue, increasing productivity and minimizing the risk of injury. Compact designs are particularly beneficial in applications where space is limited, such as automotive repair and assembly lines.
Advanced Materials and Durability
The use of advanced materials has significantly improved the durability and lifespan of air tools. Materials such as high-strength alloys and composites make these tools more resistant to wear and tear, corrosion, and extreme temperatures.
Durable tools require less frequent maintenance and replacement, saving costs and reducing downtime in manufacturing processes. Enhanced durability also ensures consistent performance over prolonged periods, which is critical in high-demand industrial environments.
Applications of Modern Air Tools in Manufacturing
Automotive Industry
The automotive industry has been a significant beneficiary of advancements in air tools. Pneumatic tools are essential in various stages of vehicle production, from assembly to repair and maintenance.
For instance, air impact wrenches are used to secure bolts and fasteners with precision. The newfound efficiencies and technological advancements in these tools ensure that assembly lines are faster, safer, and more efficient, contributing to higher-quality automobile production.
Aerospace Industry
In the aerospace industry, precision and reliability are non-negotiable. The latest air tools provide the high level of accuracy needed for assembling aircraft components. Pneumatic rivet guns, torque wrenches, and drills are widely used to ensure that every component is fitted perfectly.
Smart air tools, in particular, offer immense value by providing real-time data and ensuring that each task is completed to stringent specifications. This precision ensures the safety and performance of the aircraft.
Construction Industry
Construction is another industry where air tools play a vital role. The development of more powerful and efficient pneumatic tools has transformed the construction landscape, enabling workers to perform tasks more quickly and safely.
High-performance air hammers, nail guns, and jackhammers are commonly used to carry out various construction tasks. Their reliability and efficiency mean projects are completed faster, leading to cost savings and timely project delivery.
Manufacturing and Assembly Lines
Air tools are indispensable in manufacturing and assembly lines. Their speed, reliability, and precision make them ideal for repetitive tasks such as fastening, drilling, and cutting.
With the advent of smart air tools, manufacturers can now ensure higher quality control and operational efficiency. Real-time monitoring and feedback mechanisms help in maintaining consistent output and reducing errors.
The Future of Air Tools in Manufacturing
The future of air tools in manufacturing looks promising, with continuous advancements aimed at improving performance and efficiency. Integration with IoT, artificial intelligence, and machine learning can potentially revolutionize how these tools are utilized.
Further enhancements in energy efficiency and durability will enable even more sustainable manufacturing practices. As technology evolves, we can expect air tools to become even more intelligent, adaptable, and user-friendly.
In conclusion, the latest technologies in air tools are driving significant improvements in manufacturing processes. From smart tools that offer real-time data to energy-efficient and noise-reducing designs, these innovations are making manufacturing faster, safer, and more efficient. As industries continue to evolve, air tools will remain a cornerstone of modern manufacturing, thanks to their unmatched performance and versatility.
資料ダウンロード
QCD調達購買管理クラウド「newji」は、調達購買部門で必要なQCD管理全てを備えた、現場特化型兼クラウド型の今世紀最高の購買管理システムとなります。
ユーザー登録
調達購買業務の効率化だけでなく、システムを導入することで、コスト削減や製品・資材のステータス可視化のほか、属人化していた購買情報の共有化による内部不正防止や統制にも役立ちます。
NEWJI DX
製造業に特化したデジタルトランスフォーメーション(DX)の実現を目指す請負開発型のコンサルティングサービスです。AI、iPaaS、および先端の技術を駆使して、製造プロセスの効率化、業務効率化、チームワーク強化、コスト削減、品質向上を実現します。このサービスは、製造業の課題を深く理解し、それに対する最適なデジタルソリューションを提供することで、企業が持続的な成長とイノベーションを達成できるようサポートします。
オンライン講座
製造業、主に購買・調達部門にお勤めの方々に向けた情報を配信しております。
新任の方やベテランの方、管理職を対象とした幅広いコンテンツをご用意しております。
お問い合わせ
コストダウンが利益に直結する術だと理解していても、なかなか前に進めることができない状況。そんな時は、newjiのコストダウン自動化機能で大きく利益貢献しよう!
(Β版非公開)