- お役立ち記事
- Leveraging BI Tools for Manufacturing to Achieve Data-Driven Management
Leveraging BI Tools for Manufacturing to Achieve Data-Driven Management
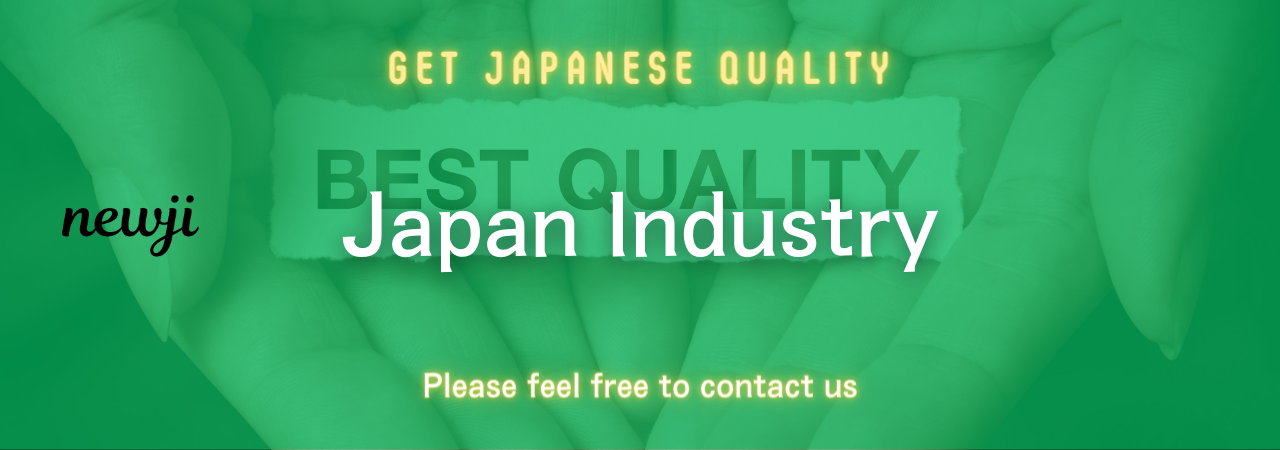
Business Intelligence (BI) tools have become essential in the modern manufacturing landscape.
They help companies make sense of vast amounts of data, providing insights that drive decision-making.
For companies aiming to adopt a data-driven management approach, leveraging BI tools is essential.
This article will explore how these tools can be used effectively in the manufacturing sector.
目次
Understanding the Basics of BI Tools
Business Intelligence tools are software applications designed to retrieve, analyze, and transform data for business insights.
They offer functionalities such as reporting, online analytical processing (OLAP), data mining, and data visualization.
Manufacturing companies can employ these tools to monitor production processes, assess their efficiency, and make informed decisions.
Benefits of BI Tools in Manufacturing
Enhanced Decision-Making
BI tools provide real-time data and historical trends, which help managers to make timely, informed decisions.
By having access to accurate data, companies can respond more swiftly to issues, improving overall efficiency.
Improved Operational Efficiency
By monitoring production metrics, manufacturers can identify bottlenecks, inefficiencies, and areas for improvement.
BI tools help to automate data collection and analysis, reducing the workload on employees while ensuring the accuracy of the data.
Cost Reduction
With effective BI tools, companies can track and reduce waste, optimize resource allocation, and implement cost-saving measures.
These insights help businesses cut down on unnecessary expenditure, resulting in substantial savings.
Better Customer Insights
Understanding customer preferences and market demand is essential for manufacturing businesses.
BI tools can analyze sales data and customer feedback, offering insights that help improve product development and customer service.
Risk Management
Manufacturing involves numerous risks, including supply chain disruptions, equipment failures, and market fluctuations.
BI tools can predict potential risks by analyzing patterns and data trends, allowing companies to take proactive measures.
Optimized Supply Chain Management
A well-managed supply chain is fundamental to manufacturing efficiency.
BI tools provide insights into inventory levels, supplier performance, and production schedules.
These insights help companies to streamline their supply chain, reduce lead times, and improve product delivery.
Implementing BI Tools in Manufacturing
Identify Key Metrics
The first step is to identify the key performance indicators (KPIs) that are crucial to your business.
These can include production output, quality control metrics, downtime, and inventory levels.
Focusing on these metrics ensures that the BI tools provide relevant insights.
Data Integration
BI tools need access to accurate data from various sources, such as ERP systems, production databases, and supply chain management software.
Integrating these data sources ensures comprehensive analysis and accurate insights.
Choose the Right BI Tool
Not all BI tools are created equal.
It is essential to choose a tool that suits your specific needs, offers scalability, and integrates with your existing systems.
Features such as customizable dashboards, advanced analytics, and user-friendly interfaces should also be considered.
Train Your Team
Even the most advanced BI tools are ineffective if the team members do not know how to use them.
Training is essential to ensure that staff can effectively utilize the tools to gain insights and make data-driven decisions.
Start Small and Scale Up
Starting with a smaller pilot project can help to identify potential issues and fine-tune the implementation process.
Once successful, these practices can be scaled up to cover the entire manufacturing process.
Case Study: Successful Implementation of BI Tools
To illustrate the impact of BI tools, let’s look at a case study of a mid-sized manufacturing company that successfully implemented BI tools to achieve data-driven management.
The Challenge
This company faced issues with production inefficiencies, high operational costs, and poor supply chain management.
Despite having data, they lacked the tools and expertise to analyze it and make informed decisions.
The Solution
They decided to implement BI tools to address these challenges.
First, they identified their key metrics, including production efficiency, downtime, and inventory levels.
Next, they integrated their data sources, ensuring that the BI tools had access to comprehensive and accurate data.
The company chose a BI tool that suited their needs, focusing on features like customizable dashboards and advanced analytics.
They invested in training their team, ensuring that everyone could use the tools effectively.
They started with a pilot project, focusing on a single production line to identify and resolve any issues before scaling up.
The Results
The implementation of BI tools transformed their operations.
Production efficiency improved by 15%, and operational costs were reduced by 10%.
The company gained better control over their inventory, reducing excess stock and cutting down on storage costs.
Supply chain management improved, with lead times reduced and on-time deliveries increased.
The company could make data-driven decisions, leading to overall improved performance and profitability.
Conclusion
Leveraging BI tools for manufacturing is essential for companies striving to achieve data-driven management.
These tools provide valuable insights that enhance decision-making, improve operational efficiency, reduce costs, and optimize supply chain management.
By carefully identifying key metrics, integrating data sources, choosing the right tools, training staff, and adopting a phased implementation approach, manufacturing companies can harness the full potential of BI tools.
With the right approach and commitment, BI tools can transform manufacturing operations, driving growth, and ensuring long-term success.
資料ダウンロード
QCD調達購買管理クラウド「newji」は、調達購買部門で必要なQCD管理全てを備えた、現場特化型兼クラウド型の今世紀最高の購買管理システムとなります。
ユーザー登録
調達購買業務の効率化だけでなく、システムを導入することで、コスト削減や製品・資材のステータス可視化のほか、属人化していた購買情報の共有化による内部不正防止や統制にも役立ちます。
NEWJI DX
製造業に特化したデジタルトランスフォーメーション(DX)の実現を目指す請負開発型のコンサルティングサービスです。AI、iPaaS、および先端の技術を駆使して、製造プロセスの効率化、業務効率化、チームワーク強化、コスト削減、品質向上を実現します。このサービスは、製造業の課題を深く理解し、それに対する最適なデジタルソリューションを提供することで、企業が持続的な成長とイノベーションを達成できるようサポートします。
オンライン講座
製造業、主に購買・調達部門にお勤めの方々に向けた情報を配信しております。
新任の方やベテランの方、管理職を対象とした幅広いコンテンツをご用意しております。
お問い合わせ
コストダウンが利益に直結する術だと理解していても、なかなか前に進めることができない状況。そんな時は、newjiのコストダウン自動化機能で大きく利益貢献しよう!
(Β版非公開)