- お役立ち記事
- Leveraging Digital Twin Technology and Product Quality Assurance Strategies for Manufacturing Sales
Leveraging Digital Twin Technology and Product Quality Assurance Strategies for Manufacturing Sales
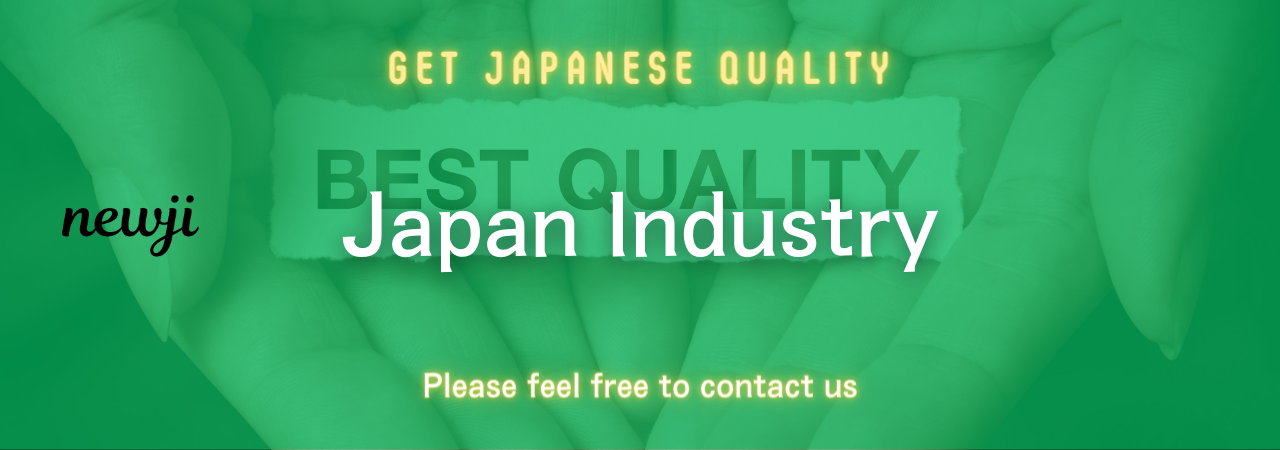
In today’s rapidly evolving manufacturing landscape, businesses continually search for innovative ways to streamline processes and ensure exceptional product quality. One such groundbreaking innovation is digital twin technology. Coupled with effective product quality assurance strategies, digital twin technology is transforming the way manufacturers operate and boosting sales.
目次
Understanding Digital Twin Technology
Digital twin technology refers to the creation of a virtual replica of physical assets, systems, or processes. This virtual model is used for simulation, analysis, and optimization. By leveraging real-time data and advanced analytics, digital twins can emulate the behavior of their physical counterparts with remarkable accuracy.
How Digital Twins Work
Digital twins utilize a combination of sensors, IoT devices, and advanced computing to collect and analyze data from physical entities. This information is fed into a virtual model, enabling manufacturers to monitor and control operations remotely. The continuous feedback loop between the physical and virtual worlds allows for ongoing improvements and real-time decision-making.
The Role of Digital Twins in Product Quality Assurance
Quality assurance in manufacturing is critical to maintaining high standards, reducing defects, and boosting customer satisfaction. Digital twin technology enhances quality assurance strategies in several ways:
1. Improved Design and Prototyping
Digital twins allow manufacturers to create and test virtual prototypes before committing to physical production. By simulating various scenarios, engineers can identify potential design flaws and make adjustments early in the development process. This not only saves time and resources but also ensures that the final product meets quality expectations.
2. Real-Time Monitoring and Predictive Maintenance
With digital twin technology, manufacturers can continuously monitor the condition of their equipment and predict potential failures. By analyzing real-time data, they can identify patterns and trends that indicate wear and tear. This proactive approach enables timely maintenance, reducing the risk of unexpected breakdowns and ensuring consistent product quality.
3. Enhanced Process Optimization
Digital twins provide valuable insights into every stage of the manufacturing process. By monitoring and analyzing data from production lines, manufacturers can identify bottlenecks, inefficiencies, and deviations from quality standards. This data-driven approach facilitates continuous process improvements and helps maintain high-quality output.
4. Streamlined Supply Chain Management
Effective supply chain management is crucial for ensuring that raw materials and components meet quality standards. Digital twins enable manufacturers to track and trace every element of the supply chain, from suppliers to final assembly. By having a comprehensive view of the entire process, they can quickly address issues and ensure that only high-quality materials are used in production.
Strategies for Leveraging Digital Twins for Sales Growth
Implementing digital twin technology can significantly enhance a manufacturer’s ability to improve product quality and drive sales. Here are some strategies to leverage this technology for sales growth:
1. Reducing Time-to-Market
The ability to create and test digital prototypes accelerates the product development cycle. By minimizing the need for physical prototypes and extensive testing, manufacturers can bring new products to market faster. This speed-to-market advantage can be a critical differentiator in a competitive landscape, attracting more customers and boosting sales.
2. Enhancing Collaboration and Communication
Digital twins facilitate seamless collaboration between different departments, such as design, engineering, and production. By providing a shared virtual model, teams can work together more effectively, reducing misunderstandings and ensuring alignment. This improved communication translates to better product development and higher customer satisfaction, ultimately driving sales.
3. Offering Product Customization
Today’s consumers demand personalized products that cater to their specific needs and preferences. Digital twin technology enables manufacturers to offer customized solutions by tailoring the virtual model to individual requirements. This capability allows for rapid adjustments and modifications, resulting in products that resonate with customers and drive sales.
The Future of Digital Twin Technology in Manufacturing
As digital twin technology continues to evolve, its impact on the manufacturing industry will only grow stronger. Here are some future trends to watch for:
1. Integration with Artificial Intelligence (AI)
The integration of digital twins with AI will unlock even greater potential for predictive analytics and automation. AI algorithms can analyze vast amounts of data generated by digital twins to provide more accurate predictions and recommendations. This enhanced intelligence will further optimize processes, improve product quality, and drive sales growth.
2. Expansion to New Industries
While digital twin technology is already making significant strides in manufacturing, its applications are not limited to this industry. Sectors such as healthcare, construction, and transportation can also benefit from digital twins. As the technology becomes more accessible and versatile, its adoption will spread across various fields, driving innovation and efficiency.
3. Increased Adoption of IoT
The Internet of Things (IoT) plays a crucial role in enabling digital twin technology. As more devices become interconnected, the volume of data available for digital twins will increase exponentially. This abundance of data will enhance the accuracy and effectiveness of virtual models, leading to better decision-making and improved product quality.
Digital twin technology and product quality assurance strategies are revolutionizing the manufacturing industry. By creating virtual replicas of physical assets, manufacturers can optimize processes, predict maintenance needs, and ensure consistent product quality. These advancements not only enhance customer satisfaction but also drive sales growth.
As the technology continues to evolve and integrate with other innovations, its impact on the manufacturing landscape will be profound and far-reaching. Now is the time for manufacturers to embrace digital twin technology and stay ahead in an increasingly competitive market.
資料ダウンロード
QCD調達購買管理クラウド「newji」は、調達購買部門で必要なQCD管理全てを備えた、現場特化型兼クラウド型の今世紀最高の購買管理システムとなります。
ユーザー登録
調達購買業務の効率化だけでなく、システムを導入することで、コスト削減や製品・資材のステータス可視化のほか、属人化していた購買情報の共有化による内部不正防止や統制にも役立ちます。
NEWJI DX
製造業に特化したデジタルトランスフォーメーション(DX)の実現を目指す請負開発型のコンサルティングサービスです。AI、iPaaS、および先端の技術を駆使して、製造プロセスの効率化、業務効率化、チームワーク強化、コスト削減、品質向上を実現します。このサービスは、製造業の課題を深く理解し、それに対する最適なデジタルソリューションを提供することで、企業が持続的な成長とイノベーションを達成できるようサポートします。
オンライン講座
製造業、主に購買・調達部門にお勤めの方々に向けた情報を配信しております。
新任の方やベテランの方、管理職を対象とした幅広いコンテンツをご用意しております。
お問い合わせ
コストダウンが利益に直結する術だと理解していても、なかなか前に進めることができない状況。そんな時は、newjiのコストダウン自動化機能で大きく利益貢献しよう!
(Β版非公開)