- お役立ち記事
- Maintaining Cleanliness in Manufacturing Lines with CIP (Cleaning In Place)
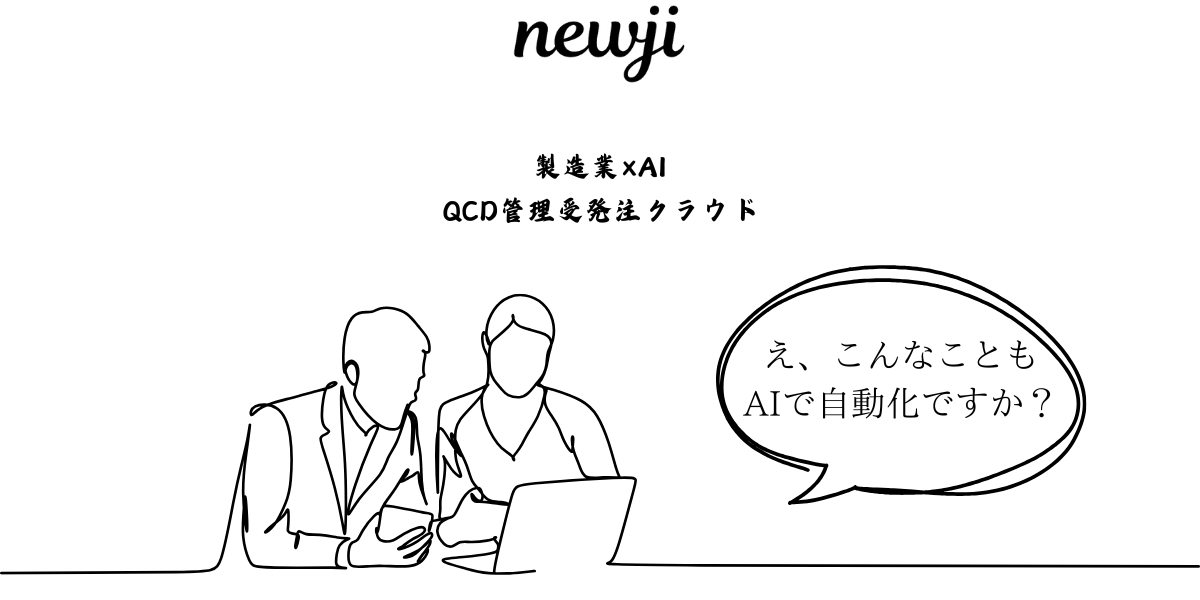
Maintaining Cleanliness in Manufacturing Lines with CIP (Cleaning In Place)
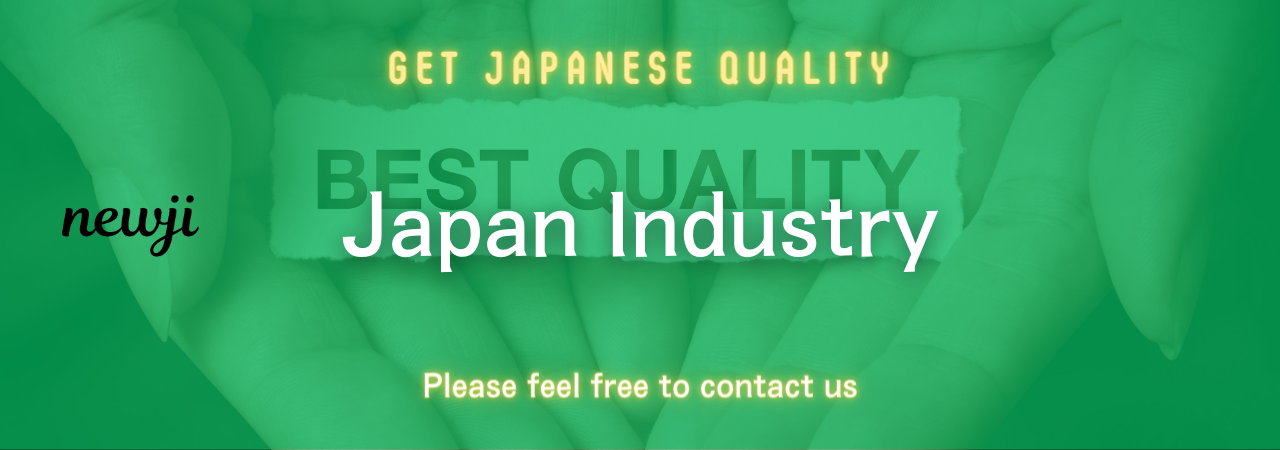
Maintaining cleanliness in manufacturing lines is crucial to ensuring product quality, safety, and consistency.
One of the most effective and efficient methods for maintaining sanitary conditions in manufacturing lines is CIP, or Cleaning In Place.
But, what exactly is CIP, and how does it help keep manufacturing lines clean?
目次
What is Cleaning In Place (CIP)?
Cleaning In Place (CIP) is a method used to clean the interior surfaces of pipes, vessels, equipment, and filters without having to disassemble them.
This rinse, wash, and sanitize system is primarily used in industries such as food and beverage, pharmaceuticals, and cosmetics.
CIP is essential in these industries because it ensures that products are manufactured in a clean, contamination-free environment.
By keeping the manufacturing lines clean, the quality and safety of the products are upheld.
Benefits of CIP in Manufacturing Lines
Reduced Downtime
One of the significant advantages of CIP is that it reduces downtime.
Since the equipment does not need to be disassembled, the cleaning process is quicker compared to traditional methods.
Reduced downtime means increased productivity, as the equipment spends more time producing and less time being cleaned.
Consistent Cleaning
CIP processes are automated and controlled, which means that the cleaning is consistent every time.
Manual cleaning methods can vary depending on who is performing the task, potentially leading to inconsistent results.
With CIP, you can be confident that every cleaning cycle meets the required standards.
Improved Safety
CIP minimizes the need for workers to handle hazardous cleaning chemicals or climb inside equipment.
This reduction in manual handling reduces the risk of accidents and improves overall worker safety.
Furthermore, the closed-system nature of CIP means that there’s less exposure to the cleaning agents.
Compliance with Regulations
Industries like food and pharmaceuticals are highly regulated to ensure consumer safety.
CIP systems help manufacturers comply with these stringent regulations by providing thorough and consistent cleaning.
Compliance with these regulations is critical for avoiding fines and maintaining a good market reputation.
Water and Chemical Savings
CIP systems are designed to be efficient, using less water and chemicals than manual cleaning methods.
This not only reduces costs but also lessens the environmental impact of the cleaning process.
Many modern CIP systems are equipped with sensors and feedback loops that optimize the use of cleaning agents.
How CIP Works
Understanding how CIP works helps appreciate its efficiency.
Here’s a basic breakdown of the typical CIP process:
Preparation
Before the cleaning cycle starts, the system needs to be prepared.
This includes ensuring that all valves are in the correct position and that the cleaning agents are available.
The equipment to be cleaned is also inspected to confirm it is ready for the CIP process.
Pre-Rinse
The pre-rinse phase involves flushing out any residual product from the equipment.
Water is circulated through the system to remove loose particles and residues.
This phase is crucial because it prepares the equipment surface for the application of cleaning agents.
Detergent Wash
In the detergent wash phase, a cleaning solution, usually alkaline or acidic, is circulated through the system.
This solution helps break down and remove more stubborn residues, fats, proteins, and other deposits that may be present.
The choice of detergent depends on the type of soil to be cleaned from the equipment.
Intermediate Rinse
After the detergent wash, an intermediate rinse is performed to remove any remaining cleaning solution and loosened residues.
This step ensures that no detergent is left behind, which could contaminate the next batch of product.
Sanitization
Sanitization is a crucial phase where a sanitizing agent is circulated to kill any remaining microorganisms.
This step ensures that the equipment is not only clean but also free of harmful bacteria and pathogens.
The choice of sanitizing agent depends on the specific requirements of the manufacturing process and the regulatory standards.
Final Rinse
The final rinse phase involves flushing the system with fresh water to remove any residual sanitizing agent.
This step ensures that the equipment is ready for the next production run without any risk of contamination from the cleaning agents.
Validation
After the cleaning process, it’s essential to validate that the equipment is clean.
This can involve visual inspections, swab tests, and the use of sensors to monitor the cleanliness of the equipment.
Validation is critical to ensure that the cleaning process meets the necessary standards.
Implementing CIP in Your Manufacturing Line
Assessing Your Needs
The first step in implementing a CIP system is to assess the specific needs of your manufacturing line.
This includes evaluating the types of residues typically left on the equipment, the materials used in your equipment, and the regulatory standards you must adhere to.
Understanding these factors helps in designing a CIP system that meets your unique requirements.
Designing the System
Once the needs assessment is complete, the next step is to design the CIP system.
This involves determining the best way to integrate CIP into your existing equipment and ensuring that all components, such as pumps, valves, and sensors, are correctly specified.
A well-designed CIP system optimizes the flow of cleaning agents and ensures thorough cleaning.
Selecting the Right Cleaning Agents
Choosing the right cleaning agents is crucial for the effectiveness of the CIP system.
The selection will depend on the type of residues and soils present on your equipment.
Working with a reputable supplier can help you choose the most effective and compatible cleaning agents for your needs.
Automation and Control
Modern CIP systems are often integrated with automation and control systems that monitor and adjust the cleaning process in real time.
These systems can provide valuable feedback and help identify areas for improvement.
Automation ensures that the cleaning process is efficient and consistent, reducing the risk of human error.
Training and Maintenance
Proper training of personnel is essential for the smooth operation of a CIP system.
This includes understanding how the system works, how to perform routine maintenance, and how to troubleshoot any issues that arise.
Regular maintenance of the CIP system is also crucial to ensure it continues to operate effectively.
In conclusion, CIP is an invaluable tool in maintaining cleanliness in manufacturing lines.
Its ability to provide consistent, thorough, and efficient cleaning helps ensure product quality and safety.
By understanding the benefits and implementation process, manufacturers can make informed decisions about integrating CIP into their operations.
資料ダウンロード
QCD調達購買管理クラウド「newji」は、調達購買部門で必要なQCD管理全てを備えた、現場特化型兼クラウド型の今世紀最高の購買管理システムとなります。
ユーザー登録
調達購買業務の効率化だけでなく、システムを導入することで、コスト削減や製品・資材のステータス可視化のほか、属人化していた購買情報の共有化による内部不正防止や統制にも役立ちます。
NEWJI DX
製造業に特化したデジタルトランスフォーメーション(DX)の実現を目指す請負開発型のコンサルティングサービスです。AI、iPaaS、および先端の技術を駆使して、製造プロセスの効率化、業務効率化、チームワーク強化、コスト削減、品質向上を実現します。このサービスは、製造業の課題を深く理解し、それに対する最適なデジタルソリューションを提供することで、企業が持続的な成長とイノベーションを達成できるようサポートします。
オンライン講座
製造業、主に購買・調達部門にお勤めの方々に向けた情報を配信しております。
新任の方やベテランの方、管理職を対象とした幅広いコンテンツをご用意しております。
お問い合わせ
コストダウンが利益に直結する術だと理解していても、なかなか前に進めることができない状況。そんな時は、newjiのコストダウン自動化機能で大きく利益貢献しよう!
(Β版非公開)