- お役立ち記事
- Management of changes in purchased product specifications to adapt to production processes Responsibilities and roles of purchasing department
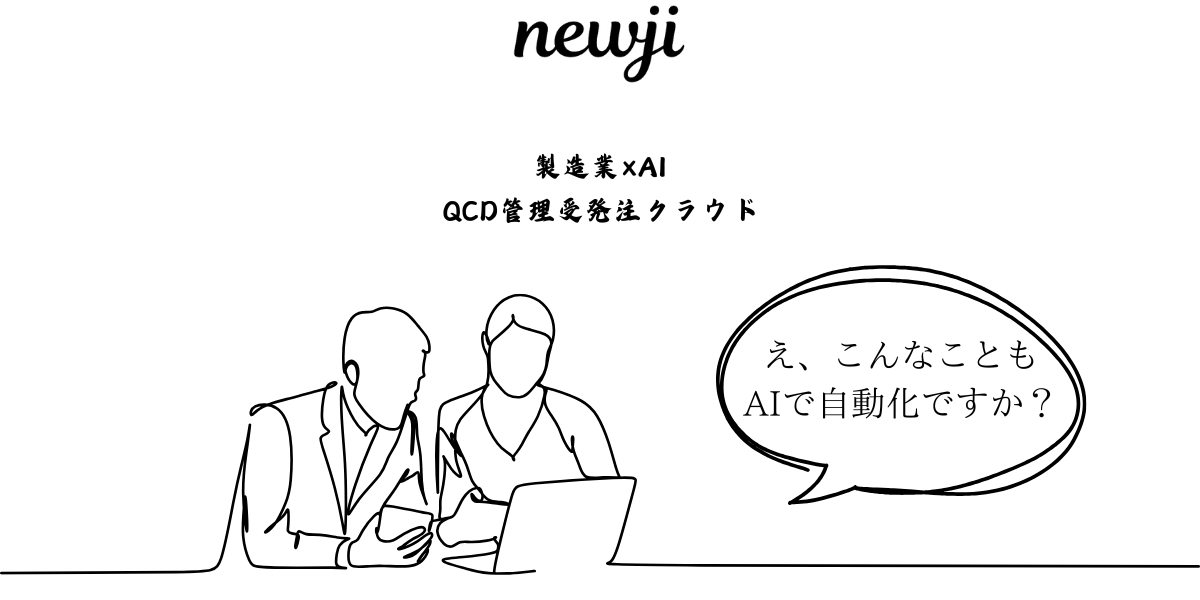
Management of changes in purchased product specifications to adapt to production processes Responsibilities and roles of purchasing department
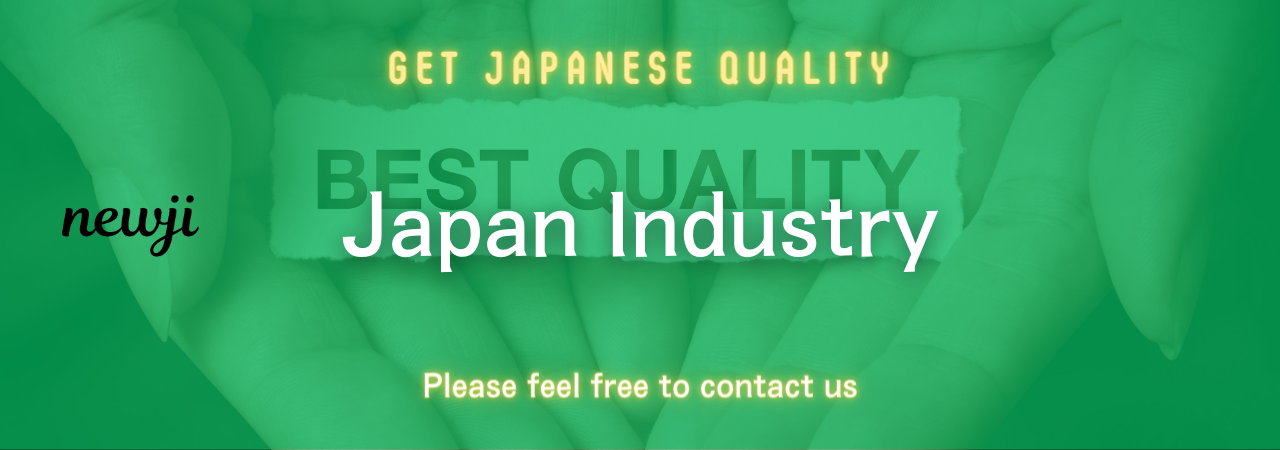
目次
Understanding the Importance of Change Management in Product Specifications
In any manufacturing business, the specifications of purchased products are crucial as they define how these products will fit into the existing production processes.
When these specifications change, it’s vital to manage this transition smoothly to avoid disruptions, increased costs, or reduced product quality.
Managing changes in product specifications is not just about adapting to new requirements; it’s also about ensuring that these changes are communicated clearly and that all relevant departments are aligned.
The Role of the Purchasing Department
The purchasing department plays a key role in managing changes in product specifications.
They act as the primary contact between suppliers and the internal teams.
They are responsible for ensuring that changes in specifications are clearly understood and implemented without hindering production.
Supplier Communication
Effective communication with suppliers is the first step in managing changes in specifications.
The purchasing department should have strong relationships with suppliers to facilitate open discussions about any upcoming changes.
This communication ensures that they receive timely information and can prepare accordingly.
Evaluating New Specifications
Once changes are communicated, the purchasing department must evaluate the new specifications to determine their impact on production.
This evaluation includes understanding the technical aspects of the changes and their implications for production processes.
Adapting Production Processes
Adapting to new specifications often requires changes in production processes.
The purchasing department must work closely with the production team to ensure that these adaptations are implemented smoothly.
This might involve modifying machinery, updating software, or retraining staff.
Responsibilities in Ensuring Quality and Cost Efficiency
One of the primary responsibilities of the purchasing department is to ensure that changes in product specifications do not compromise product quality or increase costs unnecessarily.
Ensuring Consistent Quality
When specifications change, there’s always a risk of quality variations.
The purchasing department should collaborate with quality control teams to conduct thorough testing and evaluations of products made with new specifications.
Cost Management
Changes in specifications may lead to changes in costs.
The purchasing department must analyze these changes to ensure they remain within budget constraints.
They should negotiate with suppliers to manage costs effectively.
Collaborative Efforts with Other Departments
Managing changes in product specifications successfully requires collaborative efforts across various departments.
Working with the Engineering Team
The engineering team is crucial in assessing the feasibility of integrating new specifications.
The purchasing department should coordinate with them to ensure that changes can be implemented within the current production capabilities.
Liaising with the Logistics Team
Changes in specifications may affect logistics, such as shipping methods or storage needs.
The purchasing department should work with the logistics team to plan for any adjustments required.
Implementing a Change Management Framework
To effectively manage changes, companies should implement a structured change management framework.
Establishing Clear Procedures
Having clear, documented procedures for managing changes ensures that everyone understands their roles and responsibilities.
This includes protocols for communication, evaluation, and adaptation processes.
Training and Development
Continuous training and development for purchasing staff ensure that they are equipped to handle changes efficiently.
This might include training in negotiation, communication, and technical skills related to new specifications.
Conclusion: Ensuring Smooth Transitions
Managing changes in purchased product specifications is a complex task requiring careful coordination and collaboration.
By focusing on effective communication, evaluating impacts, ensuring quality, and working within a structured framework, the purchasing department can ensure a smooth transition.
This ensures that production processes remain efficient and uninterrupted, maintaining the overall health and success of the business.
資料ダウンロード
QCD調達購買管理クラウド「newji」は、調達購買部門で必要なQCD管理全てを備えた、現場特化型兼クラウド型の今世紀最高の購買管理システムとなります。
ユーザー登録
調達購買業務の効率化だけでなく、システムを導入することで、コスト削減や製品・資材のステータス可視化のほか、属人化していた購買情報の共有化による内部不正防止や統制にも役立ちます。
NEWJI DX
製造業に特化したデジタルトランスフォーメーション(DX)の実現を目指す請負開発型のコンサルティングサービスです。AI、iPaaS、および先端の技術を駆使して、製造プロセスの効率化、業務効率化、チームワーク強化、コスト削減、品質向上を実現します。このサービスは、製造業の課題を深く理解し、それに対する最適なデジタルソリューションを提供することで、企業が持続的な成長とイノベーションを達成できるようサポートします。
オンライン講座
製造業、主に購買・調達部門にお勤めの方々に向けた情報を配信しております。
新任の方やベテランの方、管理職を対象とした幅広いコンテンツをご用意しております。
お問い合わせ
コストダウンが利益に直結する術だと理解していても、なかなか前に進めることができない状況。そんな時は、newjiのコストダウン自動化機能で大きく利益貢献しよう!
(Β版非公開)