- お役立ち記事
- Manufacturing Lightweight Parts Using Hydroforming Technology
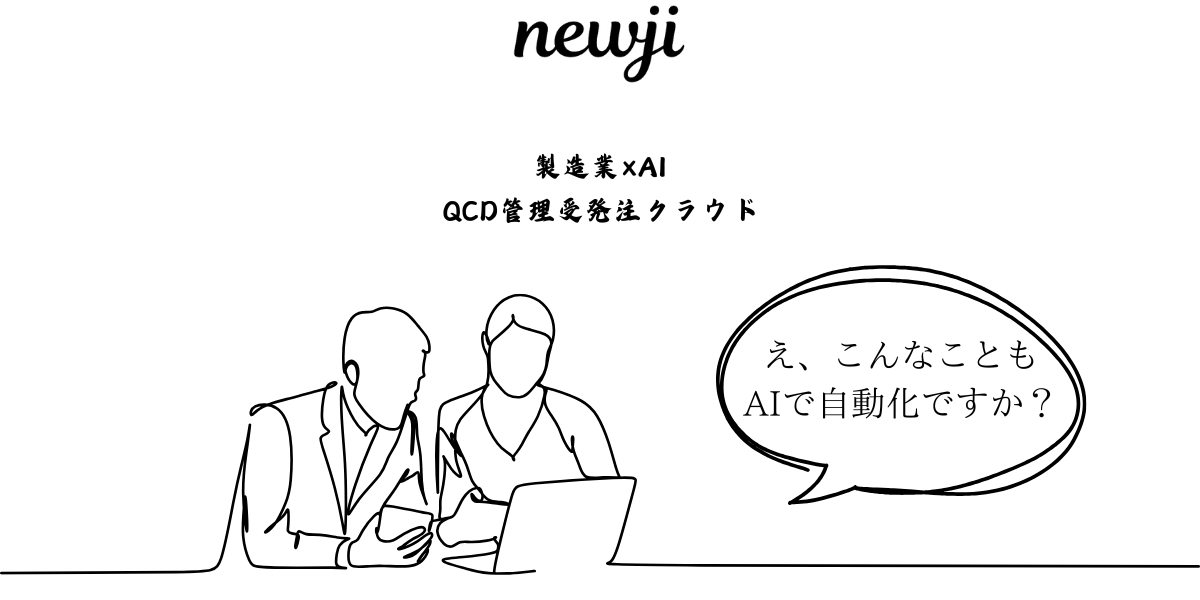
Manufacturing Lightweight Parts Using Hydroforming Technology
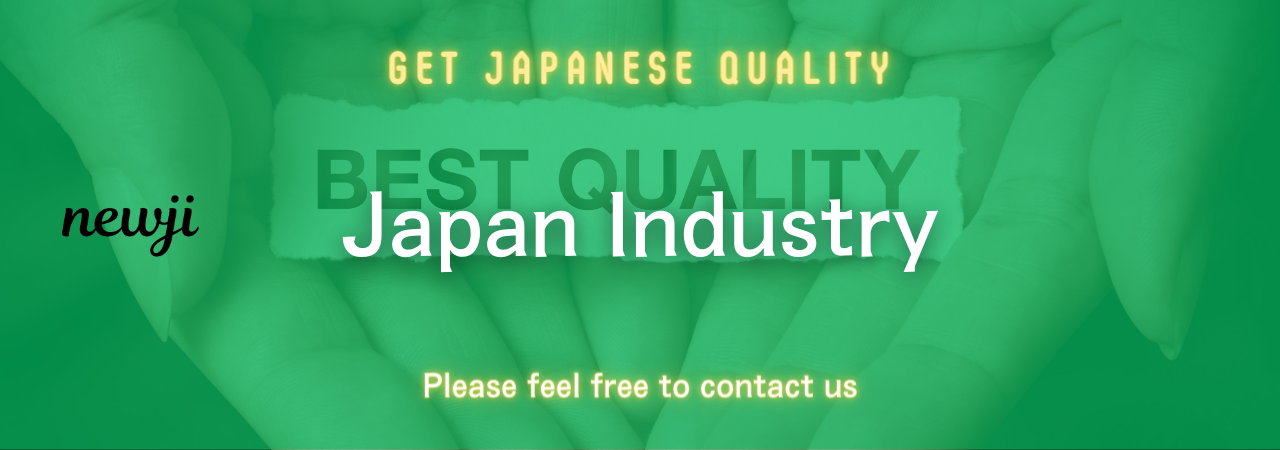
In today’s world, manufacturers are continuously seeking ways to produce stronger, lighter, and more efficient parts for various applications.
One innovative technique gaining traction is hydroforming technology.
Let’s explore what hydroforming is, how it works, and its advantages.
目次
What is Hydroforming?
Hydroforming is a manufacturing process that uses high-pressure hydraulic fluid to shape malleable metals into lightweight and structurally strong components.
This technique is particularly useful in creating intricate shapes that would be impossible to achieve using traditional stamping or welding methods.
Hydroforming is commonly used in the automotive, aerospace, and bicycle industries, where precision and durability are critical.
How Does Hydroforming Work?
The Basics of Hydroforming
The process begins with a thin sheet of metal or a tubular blank.
This blank is placed into a specialized die that matches the desired final shape of the part.
Hydraulic fluid is then pumped into the die at extremely high pressure, forcing the metal to conform to the shape of the die.
Once the metal has been formed, it is cooled and removed from the die, resulting in a part that boasts a high strength-to-weight ratio.
Sheet Hydroforming vs. Tube Hydroforming
There are two main types of hydroforming: sheet hydroforming and tube hydroforming.
Sheet hydroforming involves forming metal sheets, which is ideal for creating parts like automotive body panels and structural components.
Tube hydroforming, on the other hand, involves forming metal tubes and is commonly used for producing components like chassis frames and exhaust systems.
Both techniques use similar principles but are suited to different types of parts.
The Advantages of Hydroforming
Weight Reduction
One of the primary benefits of hydroforming is the ability to create lightweight parts without compromising structural integrity.
This is particularly important in industries like automotive and aerospace, where reducing the weight of a vehicle can lead to significant improvements in fuel efficiency and performance.
Enhanced Structural Strength
Hydroformed parts often exhibit superior strength compared to those made using traditional manufacturing methods.
The high-pressure forming process ensures that the metal grains align in beneficial ways, enhancing the overall durability and longevity of the component.
Design Flexibility
Hydroforming allows for the creation of complex shapes and intricate geometries that would be difficult or impossible to achieve with conventional techniques.
This flexibility enables designers to optimize parts for specific applications, improving functionality and reducing the need for additional components or assemblies.
Cost Efficiency
While the initial setup costs for hydroforming equipment can be high, the long-term benefits often outweigh these expenses.
Hydroforming can reduce material waste, lower the need for secondary operations like welding, and speed up production times, all of which contribute to cost savings in the long run.
Applications of Hydroforming Technology
Automotive Industry
In the automotive sector, hydroforming technology is used to create various components, including engine cradles, chassis frames, and body panels.
The ability to produce lightweight, strong parts helps manufacturers meet stringent fuel efficiency and safety standards while maintaining high performance and durability.
Aerospace Industry
The aerospace industry relies on hydroforming to produce complex, lightweight parts for aircraft and spacecraft.
These components, such as structural frames, brackets, and fuselage sections, benefit from the enhanced strength and reduced weight provided by hydroforming.
This, in turn, contributes to improved fuel efficiency and overall performance.
Sports and Recreational Equipment
Hydroforming is also widely used in the production of sports and recreational equipment, particularly in the cycling industry.
Tubular bike frames made through hydroforming are lightweight yet incredibly strong, providing cyclists with superior performance and durability.
Additionally, hydroformed components are used in other sports equipment, such as golf clubs and hockey sticks, where strength and precision are essential.
The Future of Hydroforming
As technology continues to advance, the potential applications and benefits of hydroforming are likely to expand.
Researchers are exploring new materials and techniques to further enhance the capabilities of hydroforming, such as the use of advanced alloys and composites.
These innovations could lead to even lighter, stronger, and more efficient components for a wide range of industries.
Furthermore, the integration of digital technologies, such as computer-aided design and manufacturing (CAD/CAM) systems, is streamlining the hydroforming process.
These tools allow manufacturers to design and test components virtually, reducing the need for physical prototypes and speeding up the development cycle.
Hydroforming technology is also playing a crucial role in sustainable manufacturing practices.
By minimizing material waste and enabling the production of lightweight components, hydroforming contributes to reduced energy consumption and lower emissions.
As industries continue to prioritize sustainability, hydroforming is poised to become an increasingly valuable tool in the quest for environmentally friendly manufacturing solutions.
In conclusion, hydroforming technology offers a powerful and versatile approach to manufacturing lightweight, strong, and complex components.
Its numerous advantages, including weight reduction, enhanced structural strength, design flexibility, and cost efficiency, make it an attractive option for a wide range of industries.
As the technology continues to evolve, hydroforming is set to play an even more significant role in the future of manufacturing, driving innovation and sustainability across the globe.
資料ダウンロード
QCD調達購買管理クラウド「newji」は、調達購買部門で必要なQCD管理全てを備えた、現場特化型兼クラウド型の今世紀最高の購買管理システムとなります。
ユーザー登録
調達購買業務の効率化だけでなく、システムを導入することで、コスト削減や製品・資材のステータス可視化のほか、属人化していた購買情報の共有化による内部不正防止や統制にも役立ちます。
NEWJI DX
製造業に特化したデジタルトランスフォーメーション(DX)の実現を目指す請負開発型のコンサルティングサービスです。AI、iPaaS、および先端の技術を駆使して、製造プロセスの効率化、業務効率化、チームワーク強化、コスト削減、品質向上を実現します。このサービスは、製造業の課題を深く理解し、それに対する最適なデジタルソリューションを提供することで、企業が持続的な成長とイノベーションを達成できるようサポートします。
オンライン講座
製造業、主に購買・調達部門にお勤めの方々に向けた情報を配信しております。
新任の方やベテランの方、管理職を対象とした幅広いコンテンツをご用意しております。
お問い合わせ
コストダウンが利益に直結する術だと理解していても、なかなか前に進めることができない状況。そんな時は、newjiのコストダウン自動化機能で大きく利益貢献しよう!
(Β版非公開)