- お役立ち記事
- Manufacturing Process of Acrylic Desk Organizers and Storage Capacity Enhancement
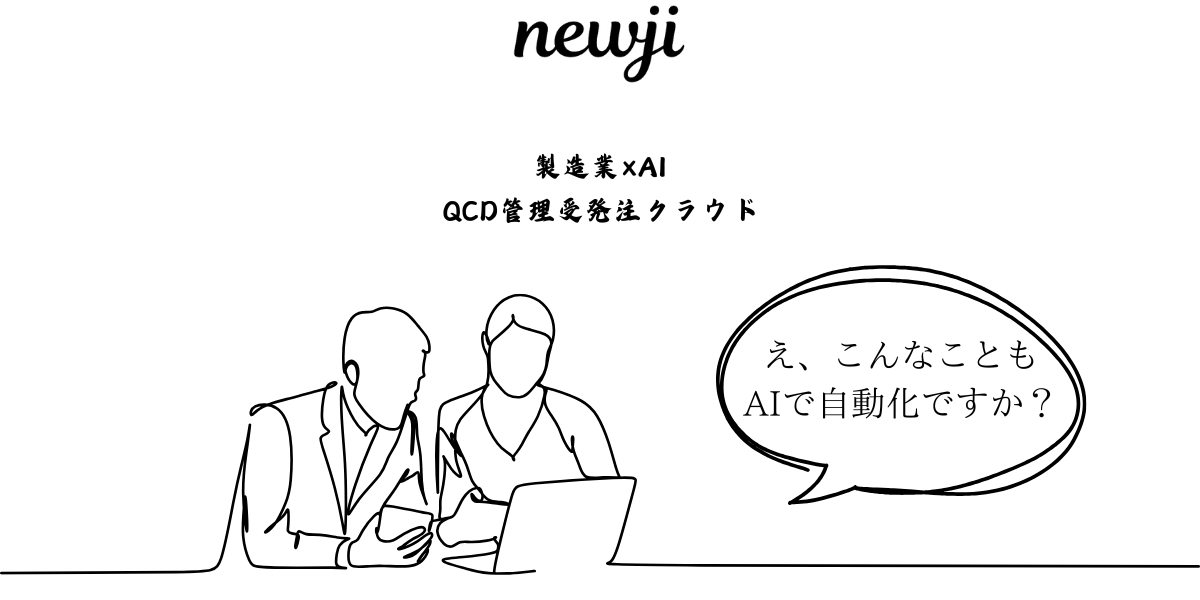
Manufacturing Process of Acrylic Desk Organizers and Storage Capacity Enhancement
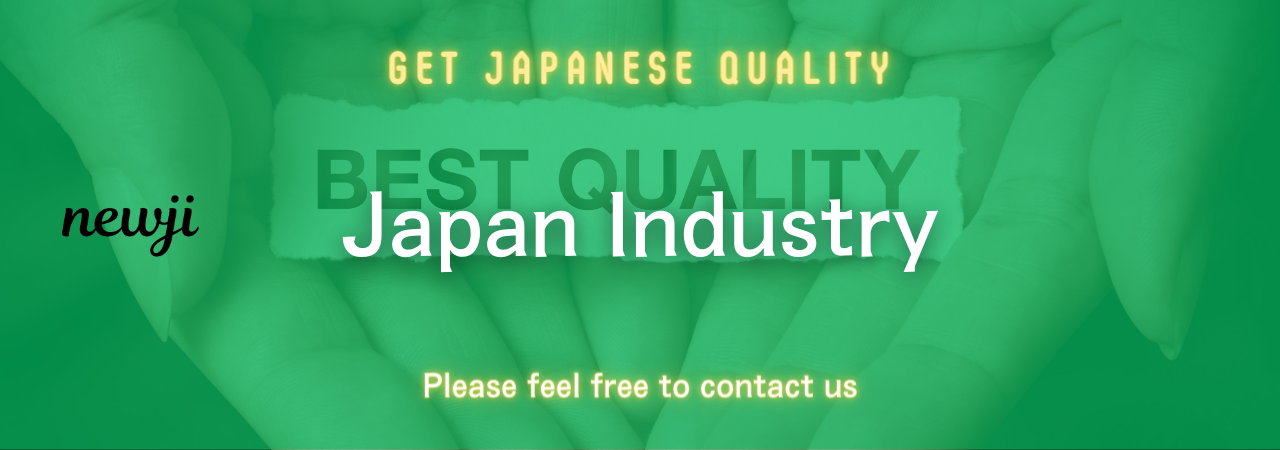
Many people use acrylic desk organizers to keep their workspaces tidy.
But how are these handy tools made?
This article will take you through the manufacturing process of acrylic desk organizers and highlight ideas for enhancing their storage capacity.
目次
What is Acrylic?
Acrylic is a clear, strong plastic that looks like glass but is much lighter and tougher.
Often called plexiglass, it is known for its durability and clarity.
Acrylic is also weather-resistant, which makes it a popular choice for many uses.
Raw Materials Needed
Before making an acrylic desk organizer, manufacturers need a few essential raw materials.
These include:
* Acrylic Sheets
* Adhesives and Solvents
* Cutting Tools and Molds
* Protective Gear
Now, let’s dive into the step-by-step process.
Step 1: Designing the Organizer
The first step is to design the desk organizer.
Professional designers use specialized software to create a 3D model of the organizer.
This digital blueprint includes the dimensions, compartments, and overall shape.
Once approved, it guides the subsequent manufacturing steps.
Step 2: Cutting the Acrylic Sheets
With the blueprint in hand, the next step is to cut the acrylic sheets.
Manufacturers use laser cutting machines for precise results.
The laser cutter follows the design closely, ensuring that each piece fits perfectly together.
This step requires extreme accuracy to avoid material waste.
Step 3: Assembling the Pieces
After cutting, the individual pieces need to be assembled.
This is where adhesives and solvents come into play.
Acrylic adhesives create strong bonds, making the organizer durable and sturdy.
Technicians apply the adhesive to the edges and carefully join the pieces.
They often use clamps to hold the pieces together until the adhesive dries.
Step 4: Smoothing and Polishing
The next step is to smooth and polish the assembled organizer.
Even the smallest imperfections can make the organizer look unprofessional.
Manufacturers use sandpaper and polishing tools to make the surfaces smooth and clear.
This step enhances the final product’s appearance and makes it more user-friendly.
Step 5: Adding Additional Features
Some acrylic organizers come with extra features like drawers or dividers.
These add-ons are also made of acrylic and follow the same cutting, assembling, and polishing steps.
Including additional features makes the organizer more functional and versatile.
Step 6: Quality Control
Quality control is a critical part of the manufacturing process.
Each organizer undergoes a thorough inspection to ensure it meets the required standards.
Inspectors check for any flaws or weak points.
If an organizer does not meet the standards, it is either fixed or discarded.
Final Packaging
Once the organizer passes quality control, it goes through the final packaging stage.
Manufacturers use protective packaging materials to ensure the organizer reaches the customer in perfect condition.
They also add labels and instructions for use.
Enhancing Storage Capacity
Acrylic desk organizers are fantastic for keeping things in order, but what if you need more space?
Here are some ideas for enhancing storage capacity:
Use Modular Designs
Modular organizers allow you to add or remove compartments as needed.
These designs are incredibly flexible, letting you customize your storage solution to fit your needs.
Add Drawers
Adding drawers can significantly increase an organizer’s storage capacity.
These can store smaller items out of sight but within easy reach, keeping your desk looking neat.
Incorporate Vertical Space
Another effective way to enhance storage is to use vertical space.
Tall organizers or stackable units take up less desk space while providing ample storage.
Utilize Dividers
Dividers are a simple yet effective addition.
They can create multiple compartments within a single drawer or section, making it easier to organize smaller items like pins, clips, or pens.
Conclusion
The manufacturing process of acrylic desk organizers involves several precise steps, from designing to quality control.
Understanding this process can give you an appreciation for these handy items.
If you need more storage space, consider modular designs, extra drawers, vertical solutions, and dividers.
These simple enhancements can make a significant difference in organizing your workspace effectively.
資料ダウンロード
QCD調達購買管理クラウド「newji」は、調達購買部門で必要なQCD管理全てを備えた、現場特化型兼クラウド型の今世紀最高の購買管理システムとなります。
ユーザー登録
調達購買業務の効率化だけでなく、システムを導入することで、コスト削減や製品・資材のステータス可視化のほか、属人化していた購買情報の共有化による内部不正防止や統制にも役立ちます。
NEWJI DX
製造業に特化したデジタルトランスフォーメーション(DX)の実現を目指す請負開発型のコンサルティングサービスです。AI、iPaaS、および先端の技術を駆使して、製造プロセスの効率化、業務効率化、チームワーク強化、コスト削減、品質向上を実現します。このサービスは、製造業の課題を深く理解し、それに対する最適なデジタルソリューションを提供することで、企業が持続的な成長とイノベーションを達成できるようサポートします。
オンライン講座
製造業、主に購買・調達部門にお勤めの方々に向けた情報を配信しております。
新任の方やベテランの方、管理職を対象とした幅広いコンテンツをご用意しております。
お問い合わせ
コストダウンが利益に直結する術だと理解していても、なかなか前に進めることができない状況。そんな時は、newjiのコストダウン自動化機能で大きく利益貢献しよう!
(Β版非公開)