- お役立ち記事
- Manufacturing Process of Acrylic Floor Mats and Anti-slip Performance Enhancement
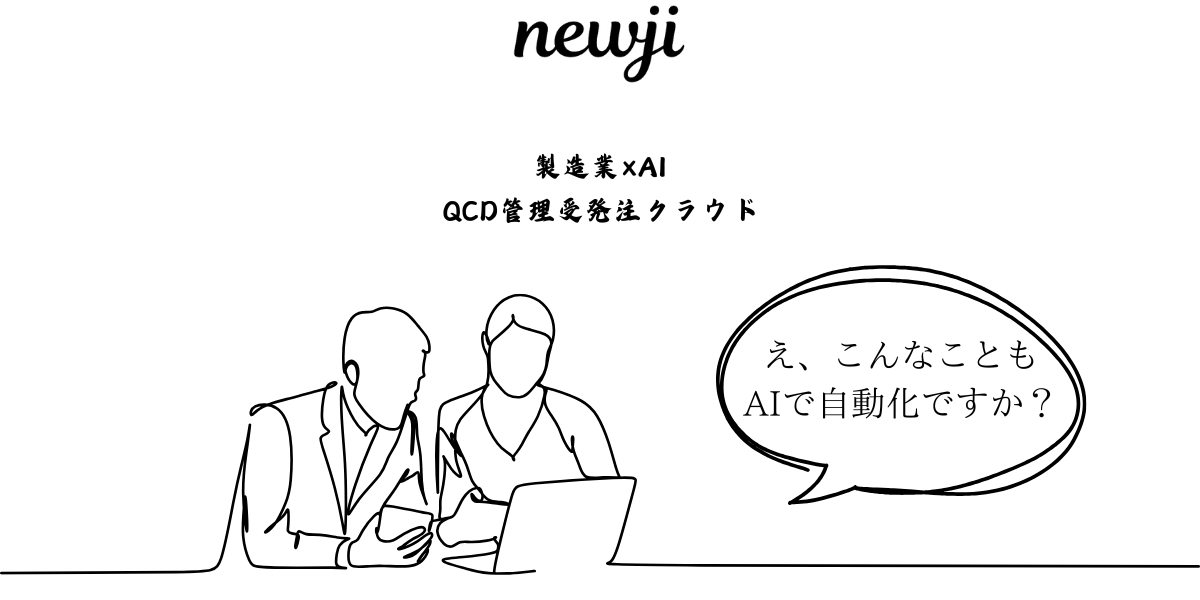
Manufacturing Process of Acrylic Floor Mats and Anti-slip Performance Enhancement
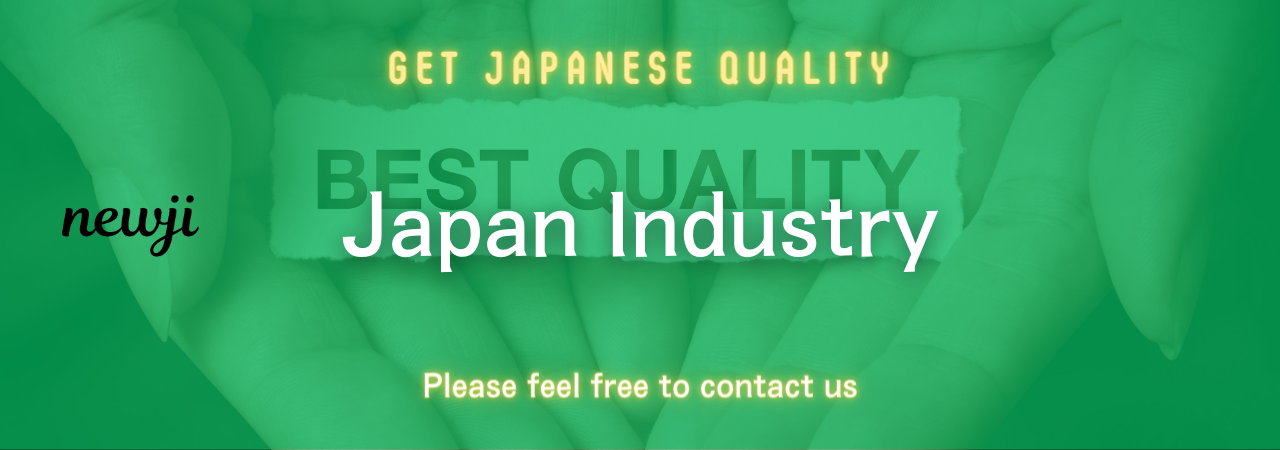
Acrylic floor mats are a popular choice for many households and businesses due to their durability, vibrant colors, and ease of maintenance.
They are known for adding aesthetic value while protecting the underlying floor from dirt, moisture, and wear.
In this article, we’ll explore the manufacturing process of acrylic floor mats and delve into how their anti-slip performance can be enhanced.
目次
Understanding Acrylic as a Material
Acrylic is a synthetic fiber derived from polymers, known for being lightweight, soft, and colorful.
It has the added advantage of being resistant to various environmental factors, making it a preferred choice for floor mats.
Properties of Acrylic
Acrylic fibers are renowned for their high durability and elastic recovery, which means they can withstand considerable wear and tear without deforming.
They are also resistant to sunlight, mildew, and most chemicals, which makes them ideal for both indoor and outdoor use.
Moreover, acrylic fibers wick away moisture efficiently, ensuring that the floor mats stay dry and comfortable underfoot.
Manufacturing Process of Acrylic Floor Mats
The creation of acrylic floor mats involves several key steps:
polymerization, spinning, blending, tufting, dyeing, backing, and finishing.
Each step ensures that the final product is both functional and aesthetically pleasing.
Step 1: Polymerization
The process begins with the polymerization of acrylonitrile, the primary raw material.
Acrylonitrile is mixed with other chemicals and subjected to heat and pressure, causing it to polymerize and form a viscous solution known as polyacrylonitrile.
This solution is then extruded through a spinneret to form long threads of acrylic fiber.
Step 2: Spinning
These fibers are gathered and spun into yarn.
There are two primary spinning methods used: wet spinning and dry spinning.
Wet spinning involves dissolving the polymer in a solvent and extruding it into a coagulating bath, while dry spinning uses a heated chamber for solvent evaporation.
Both methods result in the formation of strong, flexible yarn that is ready for further use.
Step 3: Blending
At this stage, acrylic fibers can be blended with other types of fibers to enhance specific properties.
For example, blending with nylon can increase durability, while blending with wool can add softness and luxury.
The blended fibers are then spun together to create the desired final yarn.
Step 4: Tufting
After blending, the yarn is tufted into a backing material.
This involves sewing the yarn into a base fabric using a tufting machine.
The yarn is fed through a series of needles, which punch the fibers into loops or cut them according to the mat’s design.
The type of tufting used can affect the texture and thickness of the final product.
Step 5: Dyeing
Next, the tufted mat is dyed to achieve the desired color.
The dyeing process can be done before or after tufting.
Pre-dyeing the yarn ensures a consistent color, while post-dyeing can allow for more intricate designs and patterns.
High-quality dyes are used to ensure long-lasting vibrancy and resistance to fading.
Step 6: Backing
The next critical step is to apply a secondary backing to the mat.
This backing material is typically made from latex or other synthetic compounds and is applied to the underside of the tufted mat.
The purpose of the backing is to provide stability, durability, and a foundation for anti-slip treatments.
Step 7: Finishing
Finally, the mat undergoes a series of finishing processes to enhance its look and lifespan.
These processes can include shearing to create a uniform pile height, steaming to set the fibers, and applying additional coatings for stain and water resistance.
Once all finishing touches are completed, the mats are cut to size, inspected for quality assurance, and packaged for distribution.
Enhancing Anti-slip Performance
One of the major concerns with floor mats is ensuring that they remain securely in place, minimizing the risk of slips and falls.
Specialized Backing Materials
The most straightforward enhancement method involves using specialized non-slip backing materials such as rubber or latex.
These materials create friction between the mat and the floor, preventing unwanted movement.
The backing material should be chosen based on the type of floor surface it will be used on; for instance, rubber works well on wooden floors, while latex is effective on tiles.
Textured Surfaces
In addition to backing materials, the surface texture of the mat can also play a crucial role in preventing slips.
Some acrylic floor mats are designed with raised patterns or embossed textures that add extra grip.
These patterns can trap dirt and moisture, ensuring that the mat remains dry and safe to walk on.
Anti-slip Coatings and Sprays
There are also anti-slip treatments available in the form of sprays and coatings.
These products can be applied to the backside of the mat to enhance grip.
They create a tacky surface that adheres to the floor, reducing the likelihood of movement.
It’s important to reapply these coatings regularly to maintain their effectiveness.
Proper Placement and Maintenance
Ensuring acrylic floor mats remain in place also involves proper placement and regular maintenance.
Positioning the mats away from high-traffic areas or using additional anchors such as carpets or rugs can provide extra stability.
Regular cleaning and inspection are vital to ensure that both the mat and the backing material remain in good condition.
Conclusion
In summary, the manufacturing process of acrylic floor mats involves several detailed steps, from polymerization to finishing.
Understanding these steps helps in appreciating the quality and functionality of the mats.
Enhancing anti-slip performance is equally important, and this can be achieved through specialized backing materials, textured surfaces, anti-slip coatings, and proper maintenance.
By investing in high-quality, well-made acrylic floor mats, you can enjoy both their aesthetic and safety benefits for years to come.
資料ダウンロード
QCD調達購買管理クラウド「newji」は、調達購買部門で必要なQCD管理全てを備えた、現場特化型兼クラウド型の今世紀最高の購買管理システムとなります。
ユーザー登録
調達購買業務の効率化だけでなく、システムを導入することで、コスト削減や製品・資材のステータス可視化のほか、属人化していた購買情報の共有化による内部不正防止や統制にも役立ちます。
NEWJI DX
製造業に特化したデジタルトランスフォーメーション(DX)の実現を目指す請負開発型のコンサルティングサービスです。AI、iPaaS、および先端の技術を駆使して、製造プロセスの効率化、業務効率化、チームワーク強化、コスト削減、品質向上を実現します。このサービスは、製造業の課題を深く理解し、それに対する最適なデジタルソリューションを提供することで、企業が持続的な成長とイノベーションを達成できるようサポートします。
オンライン講座
製造業、主に購買・調達部門にお勤めの方々に向けた情報を配信しております。
新任の方やベテランの方、管理職を対象とした幅広いコンテンツをご用意しております。
お問い合わせ
コストダウンが利益に直結する術だと理解していても、なかなか前に進めることができない状況。そんな時は、newjiのコストダウン自動化機能で大きく利益貢献しよう!
(Β版非公開)