- お役立ち記事
- Manufacturing Process of Automatic Sanitizer Dispensers and Improvement in Liquid Volume Control Functions
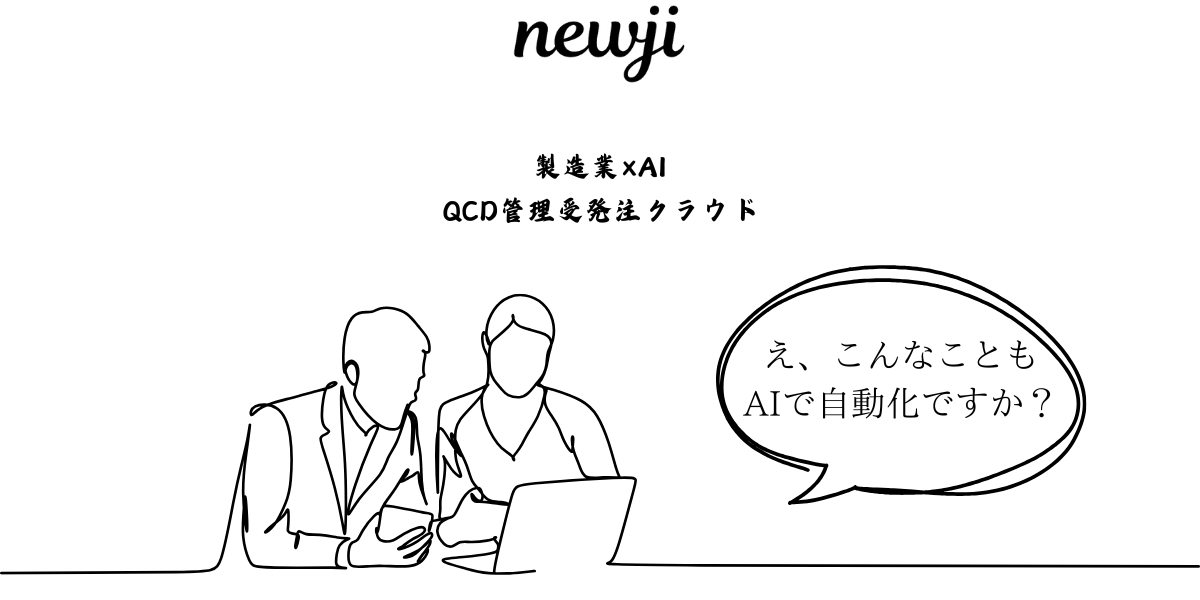
Manufacturing Process of Automatic Sanitizer Dispensers and Improvement in Liquid Volume Control Functions
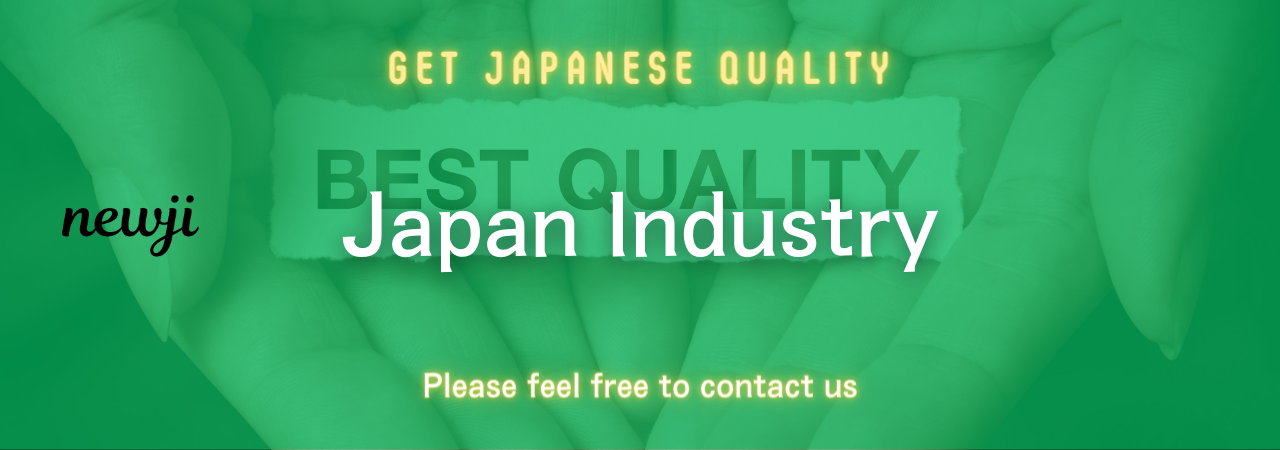
Automatic sanitizer dispensers have become a vital tool in maintaining hygiene and preventing the spread of germs.
These devices utilize advanced technology to dispense the right amount of sanitizer without any physical contact, ensuring a safer environment.
Understanding the manufacturing process and the improvement in liquid volume control functions can help consumers and businesses make informed choices.
目次
Materials and Components
The manufacturing process of automatic sanitizer dispensers starts with selecting appropriate materials and components.
High-quality plastic or stainless steel is typically used for the outer casing due to their durability and resistance to corrosion.
The internal components include sensors, motors, and control circuits, which are crucial for the dispenser’s functionality.
Outer Casing
The outer casing is designed to be robust and resistant to wear and tear.
Manufacturers use injection molding techniques to create plastic casings, ensuring precision and consistency.
Stainless steel casings, on the other hand, are fabricated using techniques like cutting, welding, and polishing.
Sensors and Motors
Sensors are the heart of automatic dispensers as they detect the presence of hands and trigger the motor to dispense the sanitizer.
Infrared sensors are commonly used due to their accuracy and reliability.
The motors, usually small and efficient, drive the pump mechanisms to control the flow of the liquid.
Design and Prototyping
Once the materials and components are selected, the design phase begins.
Engineers and designers collaborate to create models and prototypes, ensuring the dispenser is both functional and aesthetically pleasing.
Computer-aided design (CAD) software is often used to visualize the dispenser and simulate its operation.
Rapid Prototyping
Rapid prototyping techniques, such as 3D printing, allow manufacturers to quickly create physical models.
These prototypes help in testing the design and making necessary adjustments before mass production.
This step is crucial for identifying potential issues and ensuring the dispenser works as intended.
Assembly and Production
After finalizing the design and prototype, the assembly and production stage begins.
This process involves assembling all the components in a systematic manner, followed by rigorous quality checks.
Component Assembly
The assembly process starts with fitting the sensors and motors into the casing.
Automated machinery and skilled workers ensure that each part is placed accurately.
Circuit boards are then installed, connecting the sensors and motors to the control unit.
Quality Control
Quality control is vital in the manufacturing process.
Each dispenser undergoes multiple inspections to ensure it meets the required standards.
These checks include testing the sensors, verifying the liquid flow, and inspecting the casing for defects.
Improvement in Liquid Volume Control Functions
One of the significant advancements in automatic sanitizer dispensers is the improvement in liquid volume control functions.
This enhancement ensures that the right amount of sanitizer is dispensed every time, avoiding wastage and ensuring effective hand sanitation.
Precision Pump Mechanisms
Modern dispensers use precision pump mechanisms that can be calibrated to dispense a specific volume of liquid.
This technology allows manufacturers to set the desired amount of sanitizer, ensuring consistency with every use.
Precision pumps reduce wastage and enhance the overall efficiency of the dispenser.
Adjustable Settings
Many automatic sanitizer dispensers now come with adjustable settings, allowing users to customize the volume of sanitizer dispensed.
This feature is particularly useful in different environments where varying amounts of sanitizer might be required.
Adjustable settings also contribute to cost savings by minimizing unnecessary usage.
Sensor Sensitivity
Improving the sensitivity of the sensors has a direct impact on liquid volume control.
High-sensitivity sensors can detect hand presence more accurately, ensuring the dispenser activates only when necessary.
This feature helps in reducing false activations and conserving sanitizer.
Future Trends in Automatic Sanitizer Dispensers
The advancements in technology continue to drive innovation in automatic sanitizer dispensers.
Future trends suggest a focus on improving efficiency, user experience, and integration with smart technologies.
Smart Integration
Integrating automatic dispensers with smart technologies, such as IoT (Internet of Things), can enhance their functionality.
Smart dispensers can be monitored and controlled remotely, providing real-time data on usage and maintenance needs.
This integration helps facility managers optimize resource allocation and maintain hygiene standards efficiently.
Eco-friendly Designs
With growing environmental concerns, manufacturers are focusing on creating eco-friendly designs.
Using biodegradable materials and energy-efficient components can reduce the environmental impact of automatic dispensers.
Eco-friendly designs appeal to environmentally conscious consumers and businesses.
Enhanced User Experience
User experience is becoming a critical factor in the design of automatic sanitizer dispensers.
Manufacturers are incorporating features like touchless operation, easy refilling mechanisms, and aesthetically pleasing designs.
These enhancements ensure that the dispensers are user-friendly and align with modern interior designs.
Automatic sanitizer dispensers play a crucial role in maintaining hygiene and preventing the spread of germs.
The manufacturing process involves several stages, from material selection to assembly and quality control.
The advancements in liquid volume control functions ensure efficient use of sanitizer and enhance user experience.
Future trends indicate a move towards smart integration, eco-friendly designs, and improved user experience, making automatic dispensers an essential tool in various settings.
資料ダウンロード
QCD調達購買管理クラウド「newji」は、調達購買部門で必要なQCD管理全てを備えた、現場特化型兼クラウド型の今世紀最高の購買管理システムとなります。
ユーザー登録
調達購買業務の効率化だけでなく、システムを導入することで、コスト削減や製品・資材のステータス可視化のほか、属人化していた購買情報の共有化による内部不正防止や統制にも役立ちます。
NEWJI DX
製造業に特化したデジタルトランスフォーメーション(DX)の実現を目指す請負開発型のコンサルティングサービスです。AI、iPaaS、および先端の技術を駆使して、製造プロセスの効率化、業務効率化、チームワーク強化、コスト削減、品質向上を実現します。このサービスは、製造業の課題を深く理解し、それに対する最適なデジタルソリューションを提供することで、企業が持続的な成長とイノベーションを達成できるようサポートします。
オンライン講座
製造業、主に購買・調達部門にお勤めの方々に向けた情報を配信しております。
新任の方やベテランの方、管理職を対象とした幅広いコンテンツをご用意しております。
お問い合わせ
コストダウンが利益に直結する術だと理解していても、なかなか前に進めることができない状況。そんな時は、newjiのコストダウン自動化機能で大きく利益貢献しよう!
(Β版非公開)