- お役立ち記事
- Manufacturing Process of Batteries and Energy Efficiency Improvement
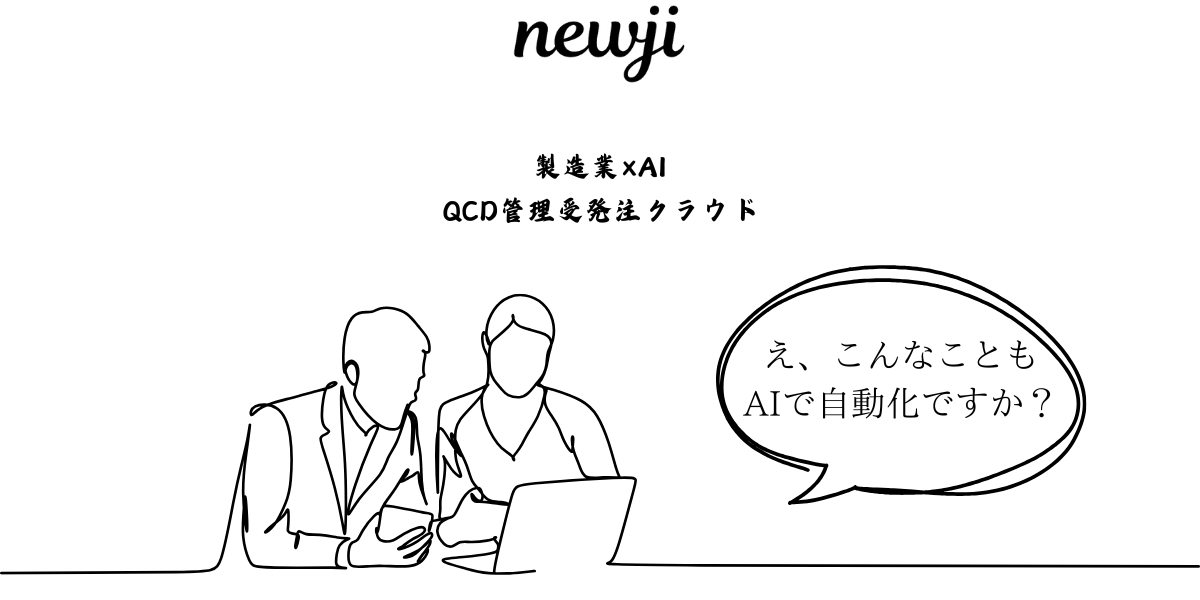
Manufacturing Process of Batteries and Energy Efficiency Improvement
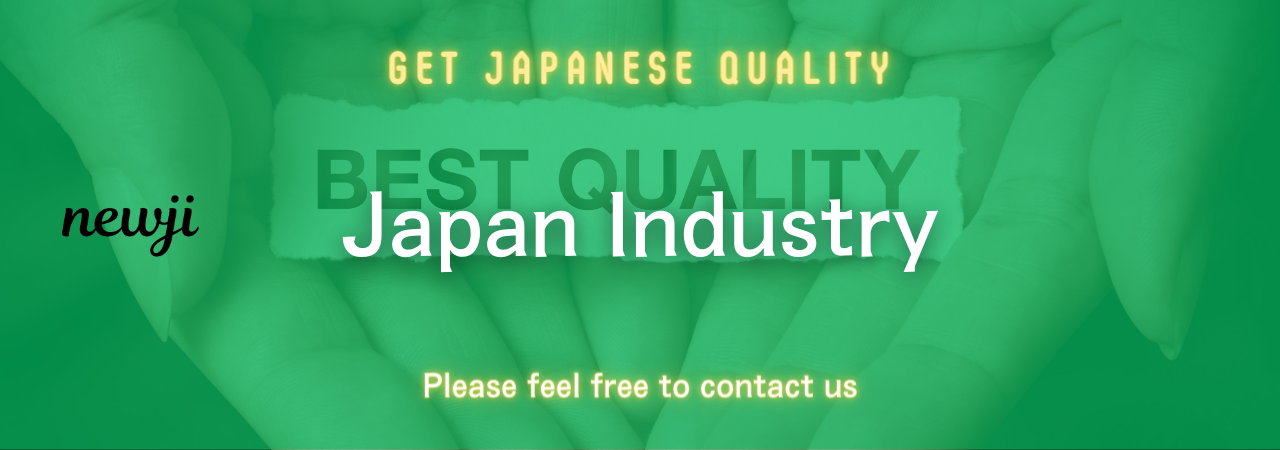
Batteries are an integral part of our everyday lives, powering everything from small electronics like smartphones to large-scale applications such as electric vehicles and grid energy storage.
To comprehend the efficiency improvements in battery technology, it is fundamental to understand the manufacturing process of batteries and how advancements in this area can lead to better energy efficiency.
The journey of a battery from raw materials to a functional energy storage device is complex and involves several stages.
目次
Raw Material Extraction
The first step in battery manufacturing is the extraction of raw materials.
Depending on the type of battery being produced, materials like lithium, cobalt, nickel, and graphite are mined.
These raw materials typically come from regions rich in mineral resources and then transported to processing plants for refinement.
The extraction process itself can impact the overall energy efficiency of the batteries because of the energy-intensive methods often employed.
Improving the extraction process to reduce energy consumption and environmental impact is a pivotal area of focus within the industry.
Material Refinement
Once the raw materials are extracted, they undergo a refinement process.
This step purifies the materials, ensuring they meet the quality and safety standards required for battery production.
Refinement processes again consume a considerable amount of energy.
At this stage, innovative techniques such as using renewable energy sources and recycling materials can enhance energy efficiency.
For instance, implementing solar or wind energy in processing plants can significantly cut down on fossil fuel consumption.
Cathode and Anode Production
The heart of a battery lies in its cathode and anode components.
These are produced by combining the refined materials with other elements to form a slurry.
This slurry is then spread onto thin metal foils, typically aluminum for the cathode and copper for the anode.
To ensure optimal performance, these coated foils must be dried, calendared (a process for reducing thickness and smoothing the surface), and cut into precise shapes.
Improving the drying and calendaring process can result in significant energy savings.
For example, replacing conventional thermal drying methods with more efficient alternatives such as vacuum or microwave drying can enhance energy efficiency.
Electrolyte Filling and Cell Assembly
Next is the assembly of the battery cells.
The anode, cathode, separator, and electrolyte come together in this phase.
The electrolyte is a liquid or gel that facilitates the movement of ions between the anode and cathode, thus enabling the storage and release of energy.
During cell assembly, precision is critical.
Automated machinery usually handles this step to minimize human error and ensure high efficiency.
Energy efficiency improvements in this stage can include optimizing machine operations to reduce idle times and using lubrication-free machinery to decrease energy requirements.
Formation and Aging
Formation and aging are crucial steps where the assembled cells are charged and discharged multiple times to form a stable solid-electrolyte interphase (SEI) layer that improves performance and longevity.
This stage also involves rigorous testing to ensure the cells meet safety and performance standards.
Though formation and aging steps are inherently energy-intensive due to repeated charging and discharging cycles, implementing rapid formation techniques and improving battery management systems can lead to reduced energy consumption.
Battery Module and Pack Assembly
Once the individual cells are ready, they are grouped into modules and then assembled into battery packs.
These packs are what we use in actual applications, like in electric vehicles or as backup power sources.
Battery packs also contain management systems that monitor and regulate the operation of the battery to ensure safety and longevity.
Energy efficiency improvements in this stage can come from better thermal management systems that prevent overheating without extensive energy use.
Utilizing advanced software for precise battery management and integrating lightweight materials for the battery casing can further improve efficiency.
Recycling and Second-Life Applications
Battery manufacturing doesn’t end when a battery reaches the end of its lifecycle.
Recycling batteries can recover a significant amount of the materials, reducing the need for new raw material extraction and thereby conserving energy.
Additionally, second-life applications where batteries that are no longer efficient enough for their original purpose are repurposed can extend the utility of these energy storage devices.
Advancements in recycling techniques and developing efficient methods for repurposing spent batteries are vital for improving the overall energy efficiency of battery technology.
Energy Efficiency Improvements through Innovation
Continuous research and development in battery technology are crucial for future energy efficiency improvements.
Efforts such as developing solid-state batteries, which can store more energy and boast a longer lifespan, and improving the energy density of battery materials can drastically enhance the efficiency of batteries.
Furthermore, integrating AI and machine learning in the battery manufacturing process can optimize various stages, from material extraction to final assembly.
These technologies can predict inefficiencies, propose optimizations, and automate decision-making processes to conserve energy.
In addition to technological advancements, supportive policies and investments in renewable energy sources can foster a more sustainable and energy-efficient battery manufacturing industry.
In summary, the manufacturing process of batteries is comprehensive and multi-faceted, involving raw material extraction, refinement, component production, assembly, testing, and recycling.
Each stage presents unique opportunities for enhancing energy efficiency.
By focusing on innovation and sustainable practices, the battery industry continues to progress toward more efficient and eco-friendly energy storage solutions.
資料ダウンロード
QCD調達購買管理クラウド「newji」は、調達購買部門で必要なQCD管理全てを備えた、現場特化型兼クラウド型の今世紀最高の購買管理システムとなります。
ユーザー登録
調達購買業務の効率化だけでなく、システムを導入することで、コスト削減や製品・資材のステータス可視化のほか、属人化していた購買情報の共有化による内部不正防止や統制にも役立ちます。
NEWJI DX
製造業に特化したデジタルトランスフォーメーション(DX)の実現を目指す請負開発型のコンサルティングサービスです。AI、iPaaS、および先端の技術を駆使して、製造プロセスの効率化、業務効率化、チームワーク強化、コスト削減、品質向上を実現します。このサービスは、製造業の課題を深く理解し、それに対する最適なデジタルソリューションを提供することで、企業が持続的な成長とイノベーションを達成できるようサポートします。
オンライン講座
製造業、主に購買・調達部門にお勤めの方々に向けた情報を配信しております。
新任の方やベテランの方、管理職を対象とした幅広いコンテンツをご用意しております。
お問い合わせ
コストダウンが利益に直結する術だと理解していても、なかなか前に進めることができない状況。そんな時は、newjiのコストダウン自動化機能で大きく利益貢献しよう!
(Β版非公開)