- お役立ち記事
- Manufacturing Process of Car Chargers and Stabilizing Power Supply
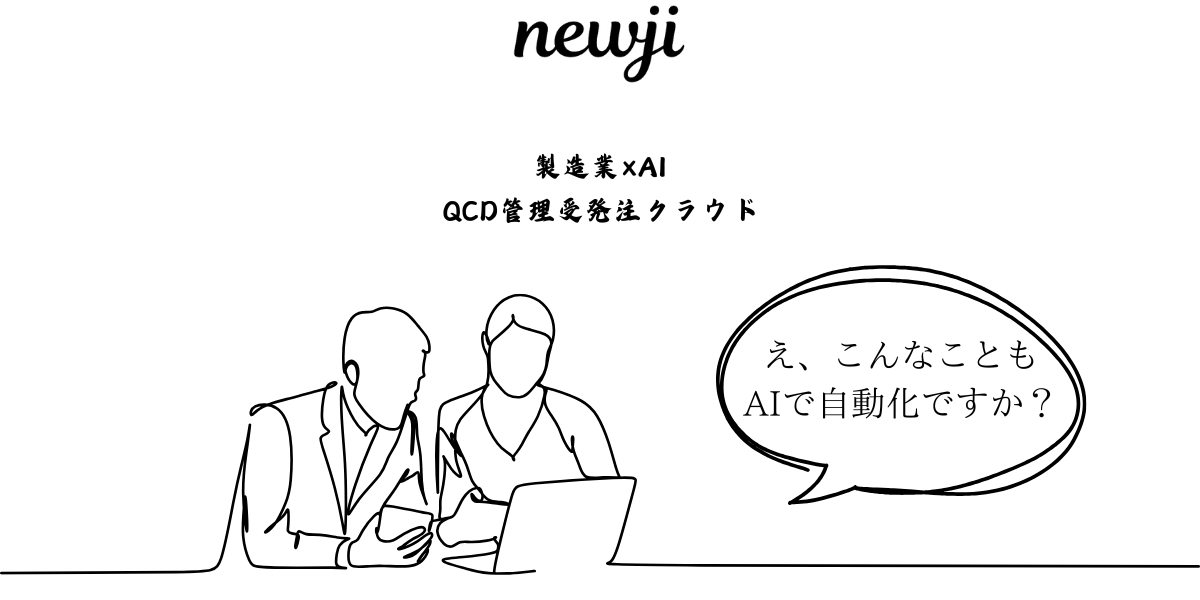
Manufacturing Process of Car Chargers and Stabilizing Power Supply
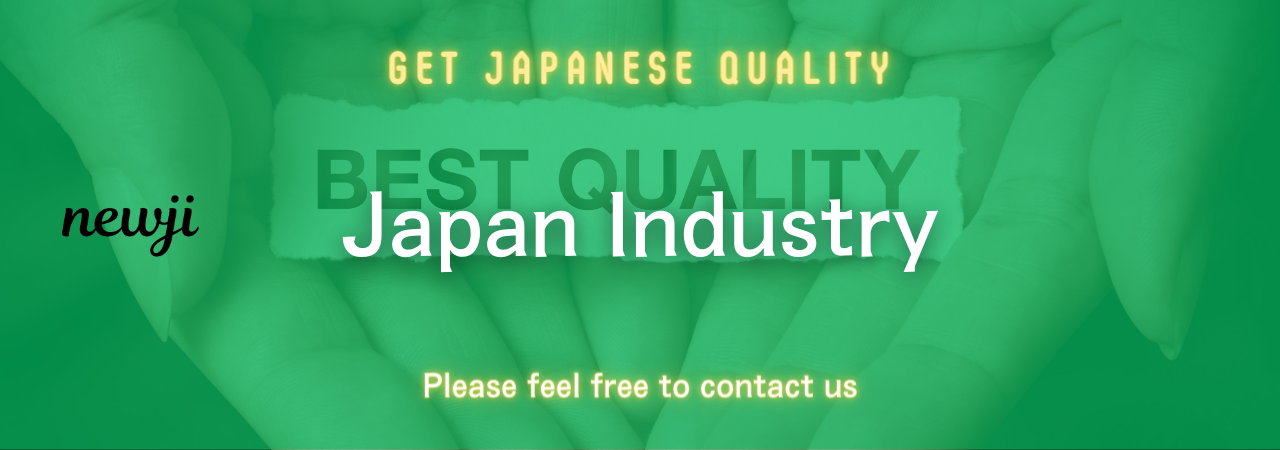
Car chargers are vital devices for modern life, ensuring that our phones, tablets, and other gadgets stay powered up on the go.
Understanding the manufacturing process of car chargers and how they stabilize power supply can enhance our appreciation of these small but essential products.
目次
Understanding Car Chargers
Car chargers are small electronic devices that plug into a vehicle’s cigarette lighter or power socket, converting the car’s electrical supply into a voltage that can safely charge our gadgets.
These devices must stabilize the power supply to ensure that our electronics receive a consistent voltage level without any damaging fluctuations.
The Manufacturing Process
The production of car chargers involves several precise steps, ensuring efficiency, safety, and effectiveness.
Each phase demands meticulous attention to detail, from design to assembly.
Design and Planning
The first step in manufacturing a car charger is designing the product.
Engineers and designers collaborate to create a blueprint that considers safety features, voltage requirements, and compatibility with various devices.
They use computer-aided design (CAD) software to produce detailed schematics.
Component Selection
Once the design is finalized, the next step involves selecting the appropriate components.
A standard car charger includes several key parts:
– **PCB (Printed Circuit Board):** This is the brain of the charger, where all the electronic components are mounted.
– **Capacitors and Resistors:** These regulate the flow of electricity and ensure voltage consistency.
– **Voltage Regulator:** This component helps maintain a stable voltage level.
– **Casing:** The outer shell that protects the internal components from dust, heat, and physical damage.
Prototyping and Testing
Before full-scale production, a prototype is built based on the design specifications.
This prototype undergoes rigorous testing to ensure it meets safety standards and performance criteria.
Engineers test for things like voltage regulation, heat dissipation, and overall durability.
Assembly Line Production
When the prototype passes all tests, the manufacturing process moves to the assembly line.
Component Placement
The assembly process typically begins with the placement of electronic components onto the PCB.
Automated machines place capacitors, resistors, and other tiny parts with high precision.
After placement, these components are soldered onto the board to ensure electrical connectivity.
Mounting the PCB
Once the PCB is populated with components, it is mounted inside the charger’s casing.
The PCB must be securely attached to avoid any movement that could damage the connections.
Wires are carefully connected from the PCB to the charger’s plug and USB ports.
Final Assembly
After the PCB is installed, the final assembly involves closing the casing and securing it with screws or adhesives.
The casing often has additional features such as LED indicators, which show whether the charger is functioning correctly.
Quality Control
Before the chargers are packaged and shipped, they must undergo a series of quality control tests.
These tests include checking for electrical safety, verifying voltage output, and ensuring that there are no manufacturing defects.
Quality control is crucial for maintaining the reliability and safety of the car chargers.
Stabilizing Power Supply
One of the critical functions of a car charger is to stabilize the power supply.
Car electrical systems generate voltage that can fluctuate widely, especially when starting the engine or using various electrical equipment.
Unstable voltage can damage sensitive electronics.
Role of Voltage Regulators
The voltage regulator in a car charger ensures that the output voltage remains consistent.
It compensates for any fluctuations in the car’s electrical system, providing a stable voltage to charge your devices safely.
This prevents overcharging, overheating, and potential damage to your gadgets.
Heat Dissipation
Car chargers must handle the heat generated by both the car’s electrical system and the charger itself.
Manufacturers use heat sinks and thermal management techniques to ensure that excess heat is dissipated efficiently.
This helps maintain the charger’s longevity and performance.
Environmental Considerations
Efficient and environmentally friendly manufacturing processes are becoming more critical in the electronics industry.
Material Selection
Manufacturers are increasingly choosing sustainable materials for their products.
For instance, recyclable plastics and metals are being used for the casing.
Additionally, lead-free solder is often utilized to reduce environmental impact.
Energy Efficiency
Modern manufacturing plants strive to minimize energy consumption.
Automated machinery is often more energy-efficient and can work continuously without significant downtime.
This not only reduces costs but also lessens the carbon footprint of the production process.
Conclusion
The manufacturing process of car chargers is a complex and intricate procedure that involves careful planning, precise component selection, and rigorous testing.
These devices play a crucial role in stabilizing power supply, ensuring that our electronic gadgets receive safe and reliable charging while on the move.
As technology advances, manufacturers continue to innovate, creating safer, more efficient, and environmentally-friendly car chargers.
Understanding this process helps us appreciate the sophisticated engineering behind these everyday products.
資料ダウンロード
QCD調達購買管理クラウド「newji」は、調達購買部門で必要なQCD管理全てを備えた、現場特化型兼クラウド型の今世紀最高の購買管理システムとなります。
ユーザー登録
調達購買業務の効率化だけでなく、システムを導入することで、コスト削減や製品・資材のステータス可視化のほか、属人化していた購買情報の共有化による内部不正防止や統制にも役立ちます。
NEWJI DX
製造業に特化したデジタルトランスフォーメーション(DX)の実現を目指す請負開発型のコンサルティングサービスです。AI、iPaaS、および先端の技術を駆使して、製造プロセスの効率化、業務効率化、チームワーク強化、コスト削減、品質向上を実現します。このサービスは、製造業の課題を深く理解し、それに対する最適なデジタルソリューションを提供することで、企業が持続的な成長とイノベーションを達成できるようサポートします。
オンライン講座
製造業、主に購買・調達部門にお勤めの方々に向けた情報を配信しております。
新任の方やベテランの方、管理職を対象とした幅広いコンテンツをご用意しております。
お問い合わせ
コストダウンが利益に直結する術だと理解していても、なかなか前に進めることができない状況。そんな時は、newjiのコストダウン自動化機能で大きく利益貢献しよう!
(Β版非公開)