- お役立ち記事
- Manufacturing Process of Foldable Electric Irons and Improving Temperature Control Technology
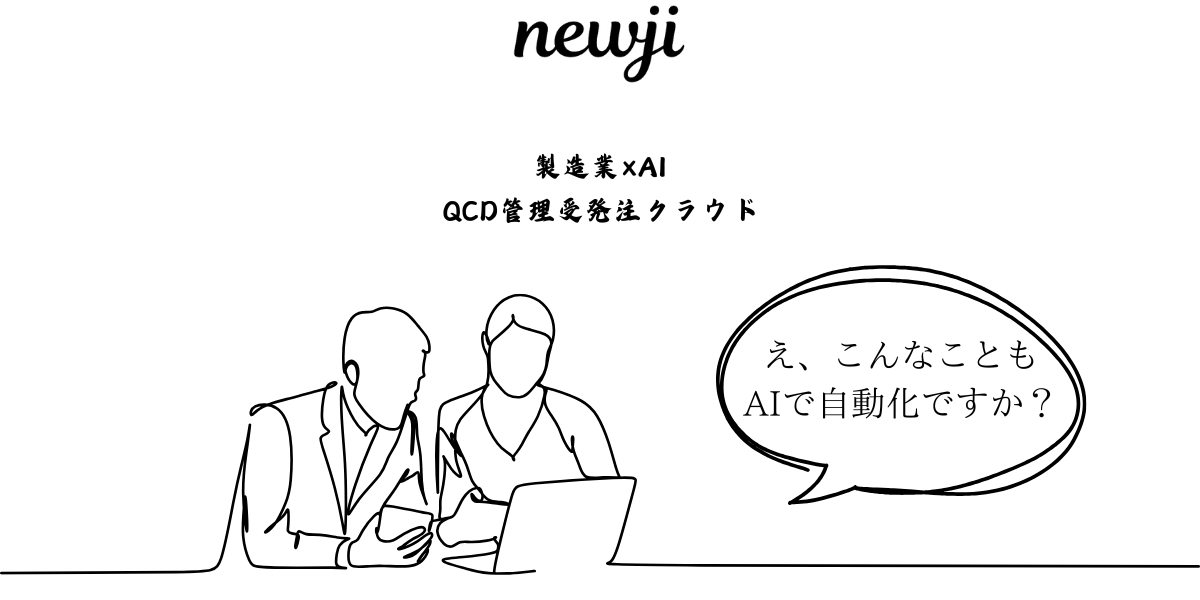
Manufacturing Process of Foldable Electric Irons and Improving Temperature Control Technology
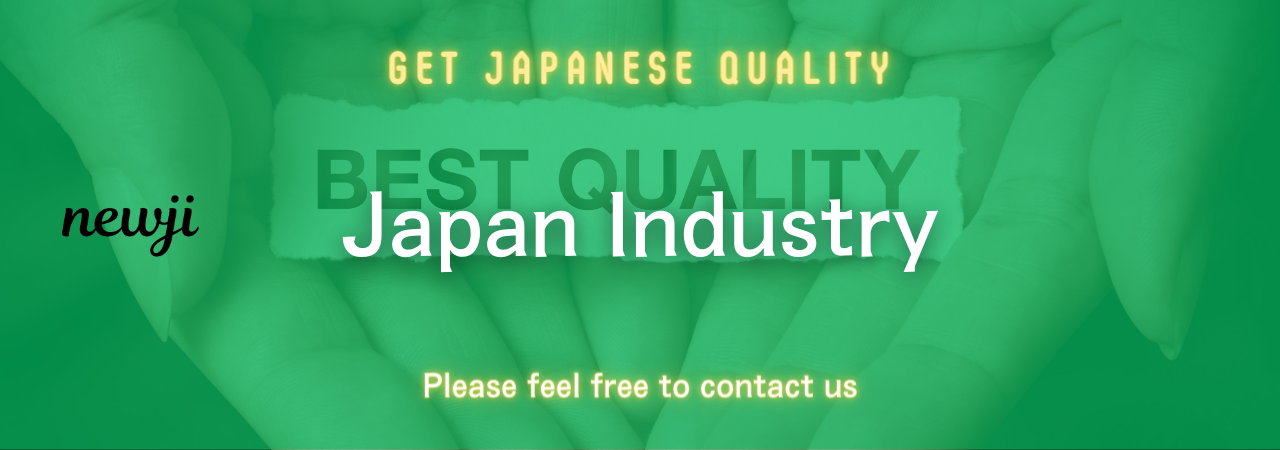
目次
The Basics of Foldable Electric Irons
Foldable electric irons are a marvel of modern engineering.
They combine the functionality of a standard electric iron with the portability of a compact design.
The ability to fold makes these irons perfect for travel or small living spaces.
Understanding their manufacturing process helps us appreciate the technology that goes into these handy devices.
Main Materials Used
The manufacturing process starts with selecting the right materials.
Plastic, metal, and electronic components are essential.
The body of the iron is usually made of heat-resistant plastic to prevent overheating.
The soleplate, the part that comes into contact with clothes, is typically crafted from stainless steel or aluminum.
These metals are chosen for their excellent heat conduction properties.
Heat-Resistant Plastic
Heat-resistant plastic forms the outer shell of the iron.
This material is chosen for its durability and ability to withstand high temperatures.
During manufacturing, the plastic is molded into the desired shape using injection molding techniques.
Injection molding allows for precise and efficient production of the iron’s exterior parts.
Metal Components
Stainless steel and aluminum are the primary metals used in the soleplate.
Stainless steel is durable and resists rust, while aluminum is lightweight and conducts heat quickly.
These materials are cut and shaped to fit the iron’s design specifications.
Once shaped, they are then polished to ensure a smooth surface that glides over fabrics.
Assembly Process
Once all the individual parts are prepared, the assembly process begins.
This step involves fitting electronic components, attaching the soleplate, and enclosing everything within the plastic body.
Placement of Electronic Components
The electronic components include temperature sensors, heating elements, and control circuits.
These elements are carefully placed within the iron’s body.
The heating element is connected to the soleplate, enabling direct heat transfer.
Temperature sensors and control circuits are installed to monitor and regulate the heat levels.
Attaching the Soleplate
The soleplate is attached to the iron’s body using screws or metal brackets.
A sealant may be applied to prevent any steam or heat from escaping.
This ensures maximum efficiency during ironing.
The attachment must be stable enough to withstand regular use yet flexible enough to allow for the iron’s foldable feature.
Final Enclosure
The last step in the assembly process is enclosing all the components within the iron’s plastic body.
Once enclosed, the iron undergoes several tests to ensure it meets safety and performance standards.
These tests include checking the iron’s ability to heat up, maintain temperature, and fold without any issues.
Improving Temperature Control Technology
One of the most critical aspects of a foldable electric iron is its temperature control technology.
Proper temperature control ensures that different types of fabrics can be ironed without damage.
Advanced Temperature Sensors
Modern foldable electric irons use advanced temperature sensors for precise control.
These sensors measure the temperature of the soleplate and relay the information to the control circuit.
If the temperature exceeds or drops below the desired level, the control circuit adjusts the power to the heating element accordingly.
Smart Control Circuits
Smart control circuits take temperature regulation a step further.
These circuits can store different temperature settings for various fabrics like cotton, silk, and synthetic materials.
Users can select the fabric type, and the iron will automatically adjust to the optimal temperature.
This feature minimizes the risk of burning or damaging clothes.
Energy Efficiency
Improved temperature control also contributes to overall energy efficiency.
By maintaining the desired temperature more consistently, the iron uses less electricity.
Energy-efficient models are better for the environment and can save users money on their electric bills.
Challenges in Manufacturing
The manufacturing of foldable electric irons comes with its own set of challenges.
These include material durability, electronic reliability, and ensuring the foldable mechanism works seamlessly.
Material Durability
Ensuring the materials can withstand regular use is vital.
Both the plastic body and metal soleplate must endure high temperatures and occasional drops.
Durable materials extend the product’s lifespan, offering more value to consumers.
Electronic Reliability
The reliability of electronic components is another concern.
Temperature sensors and control circuits must function accurately over long periods.
Manufacturers invest in high-quality components and rigorous testing to ensure reliability.
Foldable Mechanism
The foldable mechanism is a unique feature that requires precise engineering.
It must be robust enough to handle constant folding and unfolding without breaking.
Engineers design this mechanism using durable hinges and latches to ensure smooth operation.
Future Innovations
Looking ahead, several innovations could further enhance foldable electric irons.
These include smart connectivity, advanced materials, and improved energy efficiency.
Smart Connectivity
Incorporating smart connectivity features would allow users to control the iron through a mobile app.
This could include features like remote temperature control and notifications for maintenance.
Such features would add convenience and functionality.
Advanced Materials
Using advanced materials like graphene for the soleplate could revolutionize the industry.
Graphene’s exceptional heat conductivity and strength make it an ideal candidate.
This could lead to even more efficient and durable irons.
Improved Energy Efficiency
Future models will likely focus even more on energy efficiency.
This could involve better insulation, more efficient heating elements, and smarter control circuits.
These advancements would make foldable electric irons more eco-friendly and cost-effective.
The manufacturing process of foldable electric irons involves a blend of careful material selection, precise engineering, and advanced temperature control technology.
With continuous innovations, these devices are set to become even more efficient and user-friendly, making household chores a breeze.
資料ダウンロード
QCD調達購買管理クラウド「newji」は、調達購買部門で必要なQCD管理全てを備えた、現場特化型兼クラウド型の今世紀最高の購買管理システムとなります。
ユーザー登録
調達購買業務の効率化だけでなく、システムを導入することで、コスト削減や製品・資材のステータス可視化のほか、属人化していた購買情報の共有化による内部不正防止や統制にも役立ちます。
NEWJI DX
製造業に特化したデジタルトランスフォーメーション(DX)の実現を目指す請負開発型のコンサルティングサービスです。AI、iPaaS、および先端の技術を駆使して、製造プロセスの効率化、業務効率化、チームワーク強化、コスト削減、品質向上を実現します。このサービスは、製造業の課題を深く理解し、それに対する最適なデジタルソリューションを提供することで、企業が持続的な成長とイノベーションを達成できるようサポートします。
オンライン講座
製造業、主に購買・調達部門にお勤めの方々に向けた情報を配信しております。
新任の方やベテランの方、管理職を対象とした幅広いコンテンツをご用意しております。
お問い合わせ
コストダウンが利益に直結する術だと理解していても、なかなか前に進めることができない状況。そんな時は、newjiのコストダウン自動化機能で大きく利益貢献しよう!
(Β版非公開)