- お役立ち記事
- Manufacturing Process of Heat Exchange Fins and Enhancing Durability
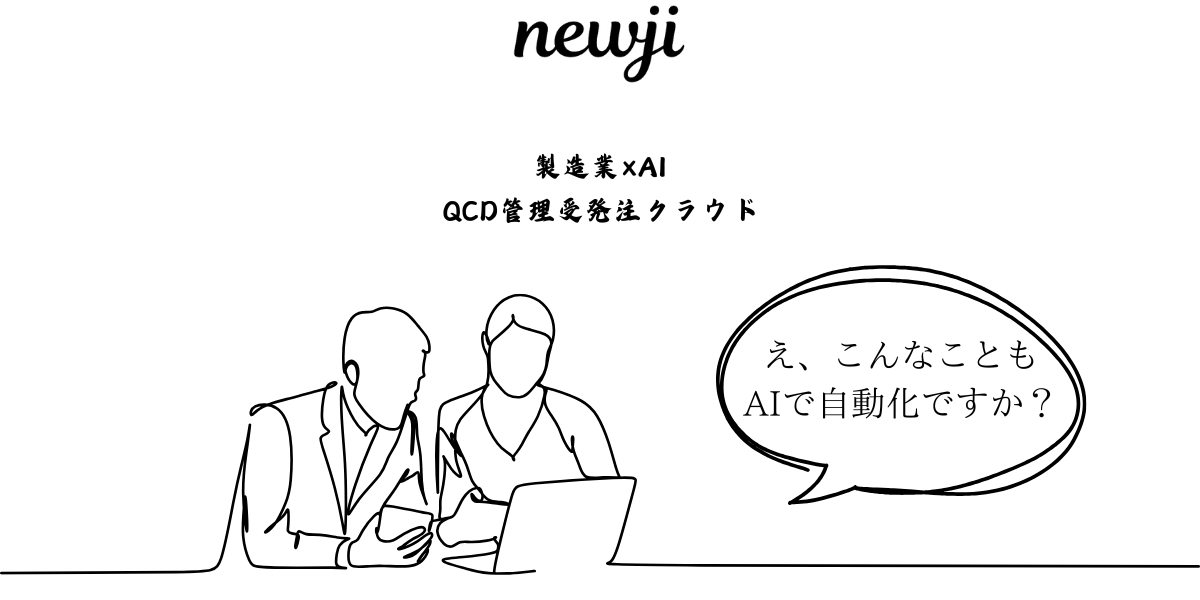
Manufacturing Process of Heat Exchange Fins and Enhancing Durability
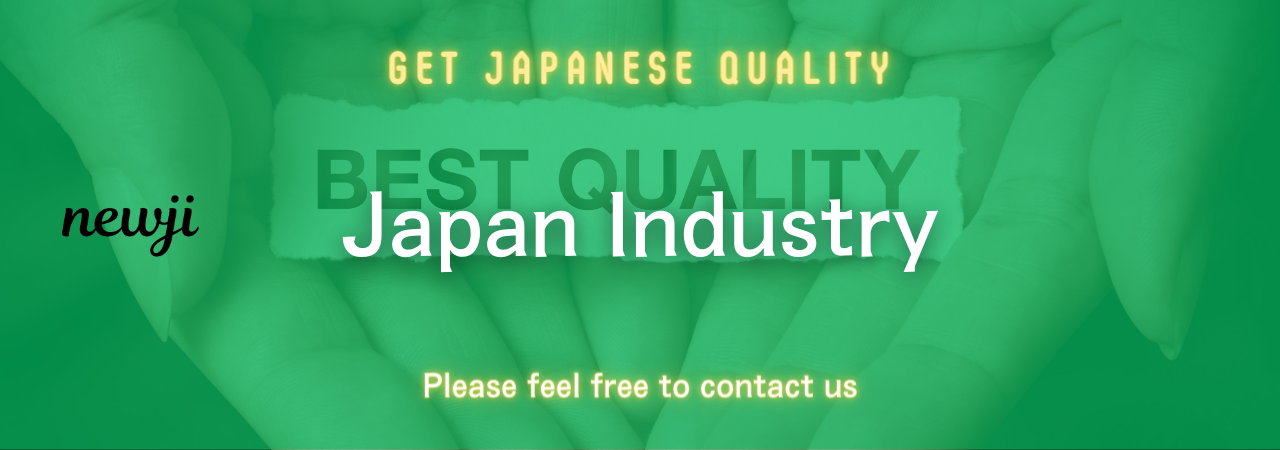
Heat exchange fins are crucial components in various applications, such as air conditioning units, refrigerators, and engines.
They help transfer heat efficiently, ensuring optimal performance and energy savings.
Understanding their manufacturing process and ways to enhance their durability can help in selecting the best products and improving their lifespan.
目次
Material Selection for Heat Exchange Fins
The first step in the manufacturing process is material selection.
Common materials used for heat exchange fins include aluminum, copper, and stainless steel.
Aluminum is lightweight and offers excellent thermal conductivity.
Copper, although more expensive, provides superior thermal performance.
Stainless steel is chosen for its corrosion resistance and strength, making it ideal for harsh environments.
Aluminum Fins
Aluminum fins are widely used due to their favorable properties.
They are cost-effective and suitable for various applications.
Aluminum is also easy to work with, making it a preferred choice for many manufacturers.
Copper Fins
Copper fins are used when higher thermal conductivity is required.
They are often found in high-performance systems where optimal heat transfer is crucial.
Although more expensive than aluminum, copper’s benefits often outweigh the cost.
Stainless Steel Fins
Stainless steel fins are chosen for their durability and resistance to corrosion.
They are ideal for applications where the fins will be exposed to harsh environments or require additional strength.
Manufacturing Techniques
Manufacturing heat exchange fins involves several techniques, including stamping, extrusion, and folding.
Each method has its advantages and is chosen based on the application’s requirements.
Stamping
Stamping is a popular method for producing heat exchange fins.
It involves pressing metal sheets into the desired shape using a stamping press.
This technique is suitable for mass production, as it allows for high-speed manufacturing and consistent quality.
Extrusion
Extrusion involves forcing metal through a die to create long, continuous shapes.
This method is ideal for producing fins with complex cross-sections and ensures uniformity throughout the fin.
Extruded fins are often used in applications requiring precise dimensions and consistent performance.
Folding
Folding is another technique used to create heat exchange fins.
It involves bending metal sheets into the desired shape, creating a series of parallel fins.
This method is suitable for producing various fin shapes and sizes, making it versatile for different applications.
Enhancing Durability of Heat Exchange Fins
Durability is a key factor in the performance and lifespan of heat exchange fins.
Several methods can be employed to enhance their durability, ensuring they function effectively for longer periods.
Coating and Surface Treatments
Applying coatings and surface treatments can significantly enhance the durability of heat exchange fins.
Coatings such as epoxy, polyester, and anodizing can protect the fins from corrosion and physical damage.
These treatments create a protective barrier, ensuring the fins remain in good condition even in harsh environments.
Material Selection
As previously mentioned, choosing the right material can enhance the durability of heat exchange fins.
Materials like stainless steel and copper offer better resistance to corrosion and wear, ensuring a longer lifespan.
Selecting the appropriate material based on the application’s requirements is crucial in enhancing durability.
Regular Maintenance
Regular maintenance is essential for ensuring the longevity of heat exchange fins.
This includes cleaning the fins to remove dust and debris, which can impede heat transfer and reduce efficiency.
Regular inspections can help identify any signs of wear or damage, allowing for timely repairs and replacements.
Conclusion
Understanding the manufacturing process and methods to enhance the durability of heat exchange fins is crucial for selecting the right products and maintaining their performance.
Choosing the appropriate material and manufacturing technique, along with applying coatings and conducting regular maintenance, can significantly extend the lifespan of heat exchange fins.
By implementing these practices, you can ensure optimal performance and energy efficiency in various applications.
資料ダウンロード
QCD調達購買管理クラウド「newji」は、調達購買部門で必要なQCD管理全てを備えた、現場特化型兼クラウド型の今世紀最高の購買管理システムとなります。
ユーザー登録
調達購買業務の効率化だけでなく、システムを導入することで、コスト削減や製品・資材のステータス可視化のほか、属人化していた購買情報の共有化による内部不正防止や統制にも役立ちます。
NEWJI DX
製造業に特化したデジタルトランスフォーメーション(DX)の実現を目指す請負開発型のコンサルティングサービスです。AI、iPaaS、および先端の技術を駆使して、製造プロセスの効率化、業務効率化、チームワーク強化、コスト削減、品質向上を実現します。このサービスは、製造業の課題を深く理解し、それに対する最適なデジタルソリューションを提供することで、企業が持続的な成長とイノベーションを達成できるようサポートします。
オンライン講座
製造業、主に購買・調達部門にお勤めの方々に向けた情報を配信しております。
新任の方やベテランの方、管理職を対象とした幅広いコンテンツをご用意しております。
お問い合わせ
コストダウンが利益に直結する術だと理解していても、なかなか前に進めることができない状況。そんな時は、newjiのコストダウン自動化機能で大きく利益貢献しよう!
(Β版非公開)