- お役立ち記事
- Manufacturing Process of Oil Filters and Filtration Precision Enhancement
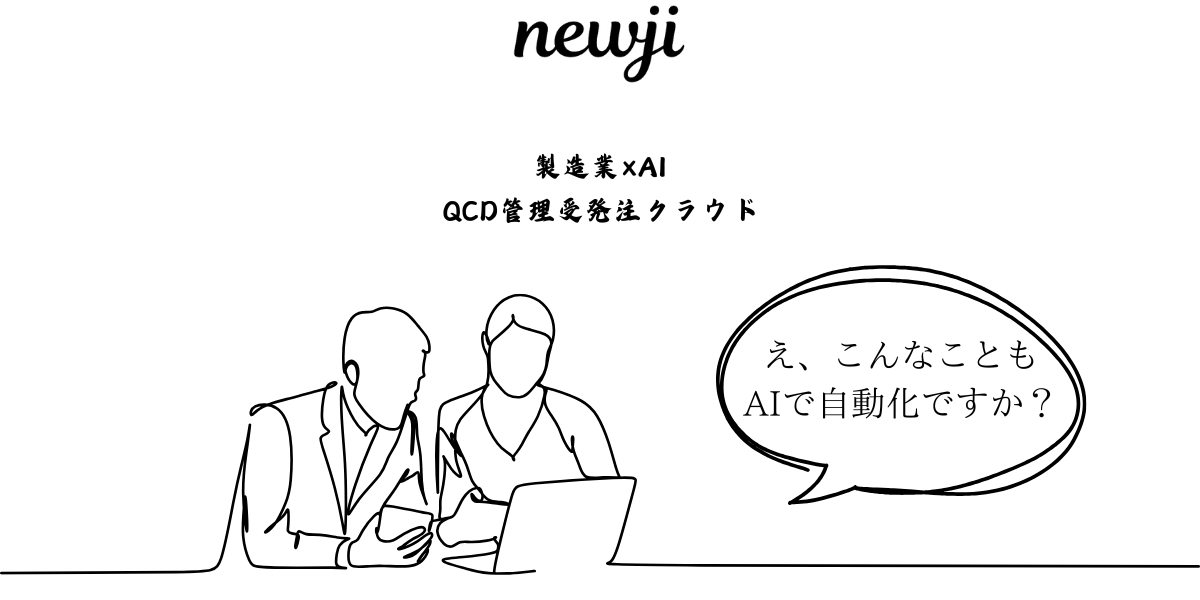
Manufacturing Process of Oil Filters and Filtration Precision Enhancement
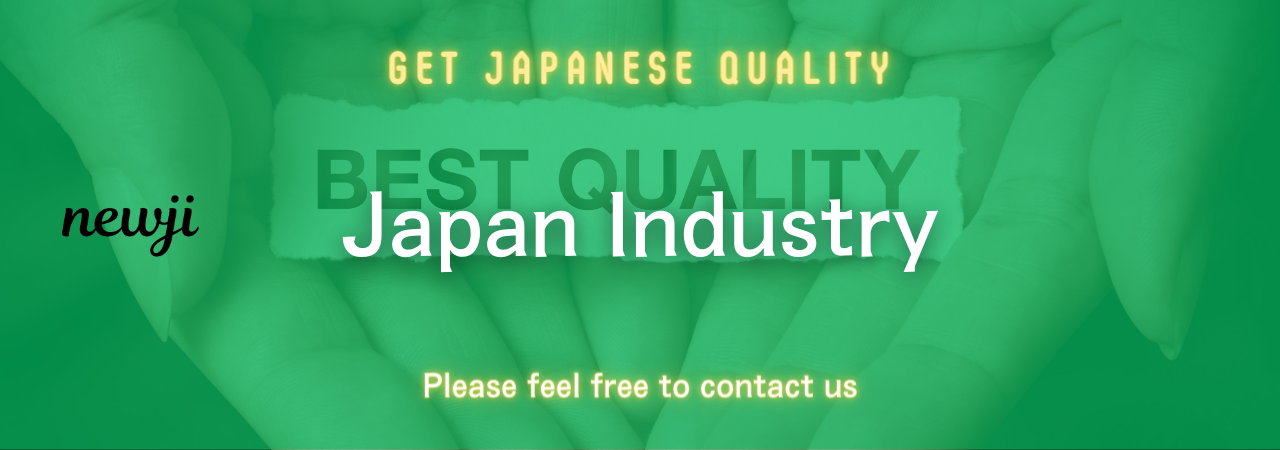
Understanding the manufacturing process of oil filters and enhancing filtration precision is essential for ensuring efficient engine performance and longevity.
Oil filters play a crucial role in maintaining the cleanliness of engine oil, thereby protecting the engine’s internal components from excessive wear and tear caused by contaminants.
目次
The Importance of Oil Filters
Oil filters are vital in automotive engines, industrial machinery, and other mechanical systems where lubrication is necessary.
Their primary function is to remove contaminants such as dirt, metal particles, and other debris that accumulate in the oil over time.
A well-functioning oil filter ensures that the engine operates smoothly, reducing the risk of damage and extending the life of the engine.
Manufacturing Process of Oil Filters
The production of oil filters involves several critical steps that ensure their efficiency and reliability.
1. Designing and Prototyping
The manufacturing process begins with the design and prototyping phase.
Engineers design the oil filter according to the specifications needed for the particular application.
Prototypes are then created and tested to ensure they meet the required standards for filtration performance and durability.
2. Material Selection
Choosing the right materials is fundamental to the filter’s performance.
The filter media, which traps the contaminants, is typically made from cellulose, synthetic fibers, or a blend of both.
The choice of material depends on the intended use of the filter and the types of contaminants it needs to capture.
Other components, such as the casing, end caps, and center tube, are often made from metal or high-strength plastic to withstand the pressure and temperature conditions within the engine.
3. Manufacturing the Filter Media
The filter media is produced by forming the chosen materials into a continuous sheet, which is then pleated to increase its surface area.
Pleating the media allows for a larger filtration surface within a compact space, enhancing the filter’s efficiency.
The pleated media is then cut to the required size and shape.
4. Assembling the Filter
The next step is the assembly of the filter components.
The pleated filter media is placed inside the filter casing.
End caps are attached to the edges of the media to maintain its shape and seal the ends.
The center tube is inserted to provide structural support and ensure uniform flow of oil through the media.
Finally, the assembled filter is sealed and crimped to ensure a tight fit and prevent leaks.
5. Quality Control and Testing
Quality control is an integral part of the manufacturing process.
Each oil filter undergoes rigorous testing to ensure it meets the required standards for performance and durability.
Tests typically include checks for structural integrity, filtration efficiency, and pressure resistance.
Only filters that pass these stringent tests are approved for distribution.
6. Packaging and Distribution
Once the filters have passed quality control, they are packaged for distribution.
Packaging is designed to protect the filters from damage during transportation and storage.
Oil filters are then distributed to retailers, automotive service centers, and other end-users.
Enhancing Filtration Precision
Improving the precision of oil filtration is crucial for maximizing the performance and lifespan of engines and machinery.
Enhanced filtration reduces the frequency of oil changes and helps maintain optimal engine conditions.
1. Advanced Filter Media Technology
The development of advanced filter media technology has significantly improved filtration precision.
Synthetic media, for example, offers superior filtration efficiency compared to traditional cellulose materials.
These synthetic fibers can capture smaller particles and have a higher dirt-holding capacity, ensuring cleaner oil for longer periods.
2. Multi-Layered Filtration
Multi-layered filtration systems can greatly enhance the precision of oil filters.
By incorporating multiple layers of different materials, filters can capture a wider range of particle sizes.
Each layer targets specific size ranges, ensuring that even the smallest contaminants are removed from the oil.
3. Enhanced Filter Design
Innovations in filter design also contribute to better filtration precision.
Spiral or zigzag pleats, for instance, can provide better flow dynamics and higher filtration efficiency.
The design of the filter’s bypass valve, which allows oil to bypass the filter in case of clogging, has also seen improvements to ensure that unfiltered oil does not enter the engine under normal operating conditions.
4. Improved Manufacturing Techniques
Improvements in manufacturing techniques have allowed for tighter control over the production processes, resulting in more consistent and reliable filters.
Automated assembly lines, precision cutting equipment, and better quality control measures ensure that each filter meets the highest standards of filtration performance.
5. Regular Maintenance and Replacement
Even with the best oil filters, regular maintenance and timely replacement are essential for maintaining filtration precision.
Over time, filters can become clogged with contaminants, reducing their efficiency.
Following the manufacturer’s recommended oil filter replacement intervals is crucial for ensuring optimal engine performance and longevity.
Conclusion
The manufacturing process of oil filters involves meticulous steps to ensure their quality and reliability.
From designing and prototyping to material selection, assembly, and rigorous testing, each phase contributes to producing a filter that effectively protects engines from contaminants.
Enhancing filtration precision through advanced materials, multi-layered systems, improved designs, and better manufacturing techniques plays a vital role in maintaining clean oil and extending engine life.
Regular maintenance and replacement of oil filters are essential practices for preserving their effectiveness and ensuring the smooth operation of engines and machinery.
資料ダウンロード
QCD調達購買管理クラウド「newji」は、調達購買部門で必要なQCD管理全てを備えた、現場特化型兼クラウド型の今世紀最高の購買管理システムとなります。
ユーザー登録
調達購買業務の効率化だけでなく、システムを導入することで、コスト削減や製品・資材のステータス可視化のほか、属人化していた購買情報の共有化による内部不正防止や統制にも役立ちます。
NEWJI DX
製造業に特化したデジタルトランスフォーメーション(DX)の実現を目指す請負開発型のコンサルティングサービスです。AI、iPaaS、および先端の技術を駆使して、製造プロセスの効率化、業務効率化、チームワーク強化、コスト削減、品質向上を実現します。このサービスは、製造業の課題を深く理解し、それに対する最適なデジタルソリューションを提供することで、企業が持続的な成長とイノベーションを達成できるようサポートします。
オンライン講座
製造業、主に購買・調達部門にお勤めの方々に向けた情報を配信しております。
新任の方やベテランの方、管理職を対象とした幅広いコンテンツをご用意しております。
お問い合わせ
コストダウンが利益に直結する術だと理解していても、なかなか前に進めることができない状況。そんな時は、newjiのコストダウン自動化機能で大きく利益貢献しよう!
(Β版非公開)