- お役立ち記事
- Manufacturing Process of Protective Glasses and Anti-fog Improvement
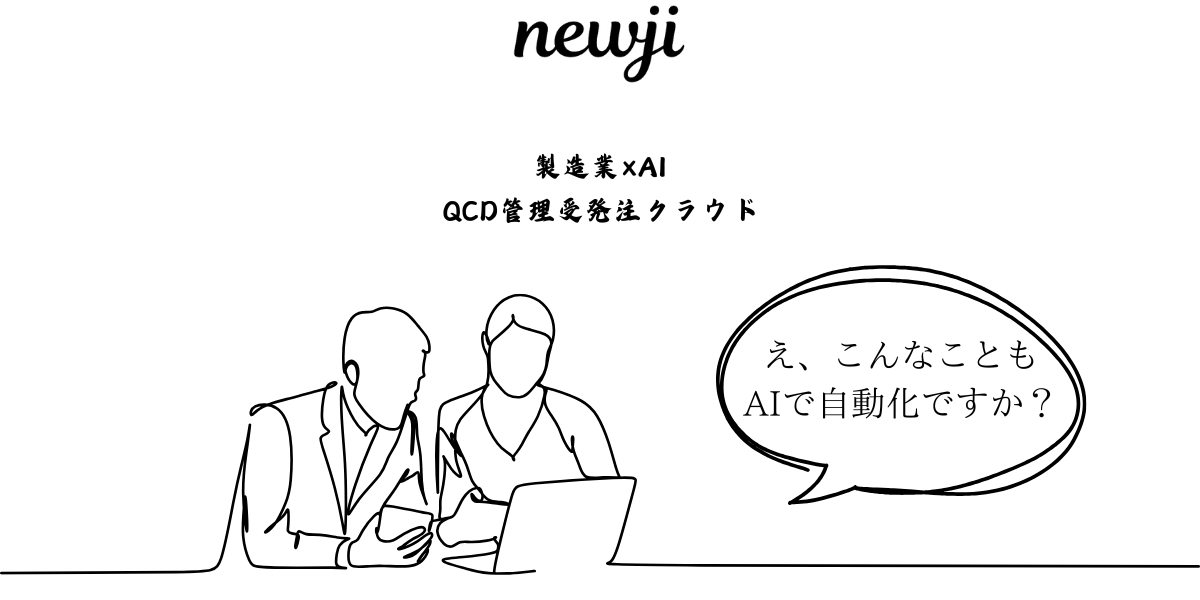
Manufacturing Process of Protective Glasses and Anti-fog Improvement
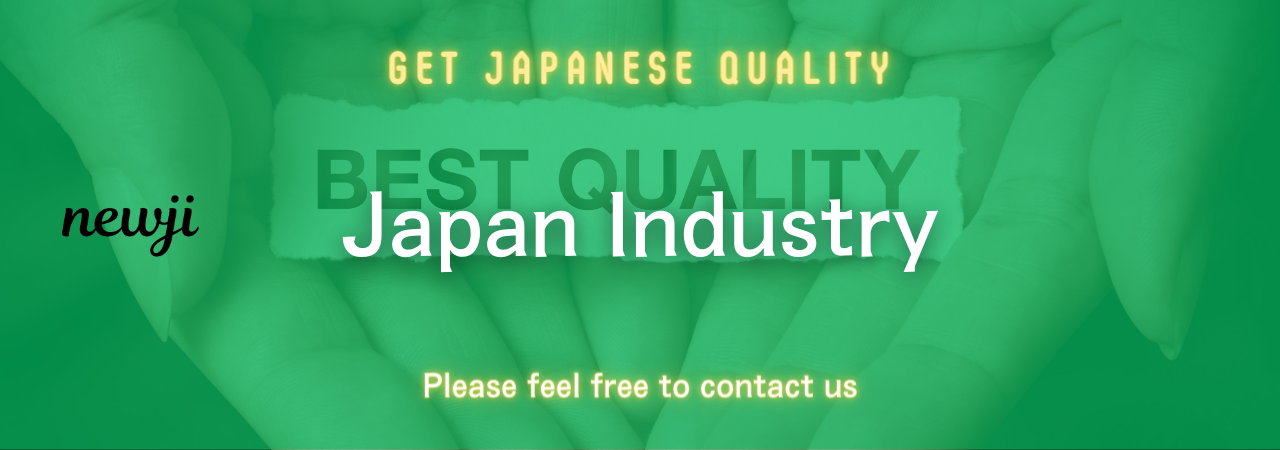
目次
Understanding Protective Glasses
Protective glasses, commonly known as safety glasses, are essential for individuals working in environments where eye safety is paramount.
These glasses are designed to protect the eyes from hazardous materials such as chemicals, debris, and impact from flying objects.
With increased use in various industries, it’s crucial to understand the manufacturing process and the methods used to improve their functionality, such as anti-fog features.
The Manufacturing Process
Raw Materials
The production of protective glasses begins with the selection of high-quality raw materials.
The most critical materials include polycarbonate and Trivex.
These materials offer superior impact resistance and optical clarity.
Polycarbonate is favored for its lightweight and shatterproof properties, making it ideal for safety glasses.
Molding the Lenses
Once the raw materials are obtained, the next step is molding the lenses.
Polycarbonate and Trivex are heated until they become pliable.
They are then injected into molds to create lenses of the desired shape and thickness.
The molds are precisely designed to ensure uniformity and optical precision.
After cooling, the lenses are removed from the molds and undergo a series of inspections to check for defects.
Surface Coating
Protective glasses must withstand various environmental conditions, and this is where surface coating comes in.
Coatings are applied to enhance the durability, clarity, and functionality of the lenses.
Common coatings include scratch-resistant, UV protection, and anti-fog.
Each coating serves a distinct purpose and is applied using advanced techniques to ensure even distribution and adherence to the lens material.
Frame Production
The frames of protective glasses are manufactured separately from the lenses.
Materials used for frames include plastic, metal, and composite materials, all chosen for their strength and flexibility.
The manufacturing process involves cutting, bending, and assembling the frame components.
Comfort features such as adjustable nose pads and temple tips are incorporated to ensure a secure and comfortable fit.
Assembly
The final step in the manufacturing process is the assembly of the lenses and frames.
Technicians carefully fit the lenses into the frames, ensuring perfect alignment.
The glasses are then subjected to a series of tests to verify their performance and safety standards.
Once passed, the completed protective glasses are packaged and ready for distribution.
Improving Anti-fog Features
Fogging is a common issue faced by users of protective glasses, especially in environments with temperature variations or high humidity.
Anti-fog features are therefore crucial for maintaining clear vision.
Several methods are used to improve the anti-fog characteristics of protective glasses.
Anti-fog Coatings
One of the most effective ways to combat fog is to apply anti-fog coatings to the lenses.
These coatings work by minimizing the surface tension of water vapor, preventing it from condensing into fog.
The application process involves spraying or dipping the lenses in an anti-fog solution, followed by curing to ensure longevity.
Advanced coatings can last longer and are more resistant to wear and tear.
Vented Frames
Another method to reduce fogging is the incorporation of vented frames.
Vents are strategically placed on the frame to allow air circulation around the lenses.
This airflow helps to dissipate moisture and maintain a consistent temperature, thus reducing the chances of fog formation.
Vented frames are particularly useful in hot and humid conditions.
Hydrophilic Treatments
Hydrophilic treatments are chemical processes that make the lens surface attract water.
Instead of forming droplets, the water spreads evenly across the lens, forming a thin, clear layer.
This technique ensures that the user’s vision remains unobstructed.
Hydrophilic treatments are often used in conjunction with anti-fog coatings to provide superior performance.
Cleaning and Maintenance
Proper cleaning and maintenance of protective glasses also play a vital role in preventing fogging.
Using specialized cleaning solutions and microfiber cloths can help maintain the integrity of anti-fog coatings.
Regular cleaning ensures that oils and dirt do not build up on the lenses, which can interfere with the anti-fog properties.
The Future of Protective Glasses
The manufacturing process of protective glasses and the improvements in anti-fog technology are continuously evolving.
Researchers and manufacturers are exploring new materials and techniques to enhance the safety and functionality of protective glasses.
Innovations such as self-cleaning lenses and integrated smart technology are on the horizon, promising even better performance and user experience.
By understanding the detailed manufacturing process and the advancements in anti-fog technology, users can appreciate the effort that goes into producing high-quality protective glasses.
These advancements not only ensure eye safety but also enhance the comfort and convenience for users in various demanding environments.
資料ダウンロード
QCD調達購買管理クラウド「newji」は、調達購買部門で必要なQCD管理全てを備えた、現場特化型兼クラウド型の今世紀最高の購買管理システムとなります。
ユーザー登録
調達購買業務の効率化だけでなく、システムを導入することで、コスト削減や製品・資材のステータス可視化のほか、属人化していた購買情報の共有化による内部不正防止や統制にも役立ちます。
NEWJI DX
製造業に特化したデジタルトランスフォーメーション(DX)の実現を目指す請負開発型のコンサルティングサービスです。AI、iPaaS、および先端の技術を駆使して、製造プロセスの効率化、業務効率化、チームワーク強化、コスト削減、品質向上を実現します。このサービスは、製造業の課題を深く理解し、それに対する最適なデジタルソリューションを提供することで、企業が持続的な成長とイノベーションを達成できるようサポートします。
オンライン講座
製造業、主に購買・調達部門にお勤めの方々に向けた情報を配信しております。
新任の方やベテランの方、管理職を対象とした幅広いコンテンツをご用意しております。
お問い合わせ
コストダウンが利益に直結する術だと理解していても、なかなか前に進めることができない状況。そんな時は、newjiのコストダウン自動化機能で大きく利益貢献しよう!
(Β版非公開)