- お役立ち記事
- Manufacturing Process of Residential Barrier-Free Handrails and Enhancing Safety
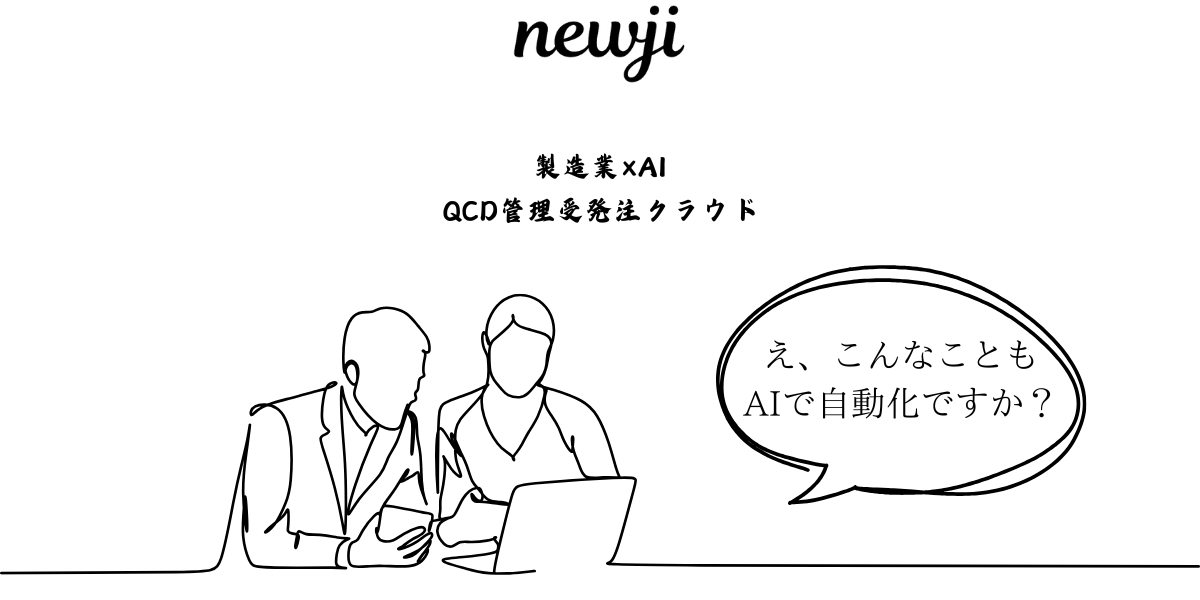
Manufacturing Process of Residential Barrier-Free Handrails and Enhancing Safety
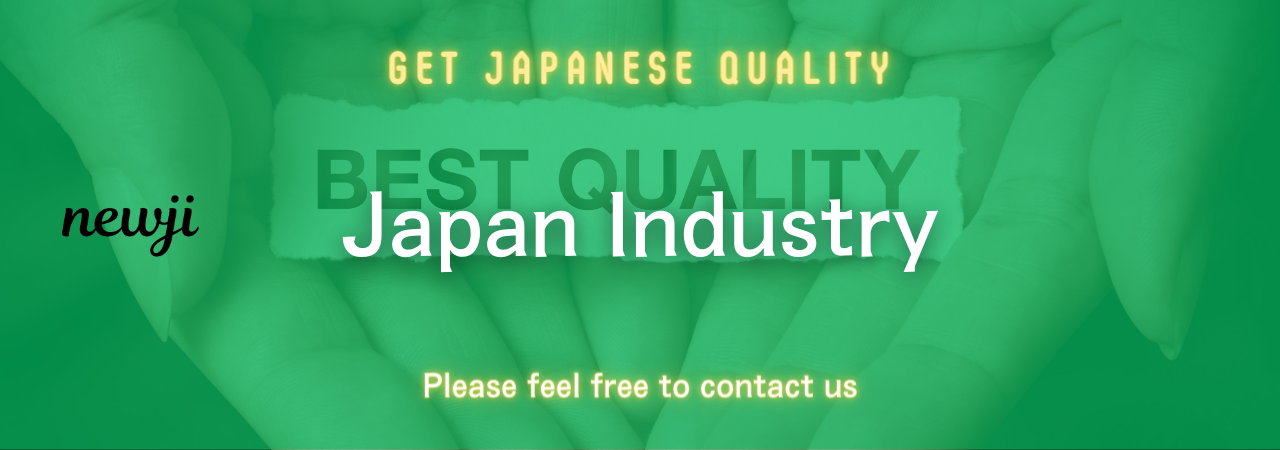
Barrier-free handrails play a crucial role in ensuring the safety and mobility of people with physical disabilities or the elderly.
Understanding the manufacturing process of residential barrier-free handrails is essential for homeowners, caregivers, and anyone interested in making their homes more accessible.
This article delves into the comprehensive manufacturing process of these vital safety tools and explores ways to enhance their functionality and effectiveness.
目次
Design and Material Selection
The first step in manufacturing barrier-free handrails is designing them to meet specific safety standards and accessibility needs.
Designers consider various factors such as ergonomics, durability, and aesthetic appeal when creating handrail designs.
The design phase also involves working closely with regulatory agencies to ensure compliance with safety standards.
Choosing the Right Materials
Selecting the appropriate materials is critical to the success of the manufacturing process.
Common materials used for barrier-free handrails include stainless steel, aluminum, and wood.
Stainless steel and aluminum are popular choices due to their strength and corrosion resistance, making them suitable for both indoor and outdoor use.
Wood handrails, while less common, offer a warm and aesthetically pleasing option, especially for indoor installations.
Fabrication Process
Once the design and materials are selected, the fabrication process begins.
This phase involves cutting, shaping, and assembling the materials to create the final product.
The fabrication process can be broken down into several key steps:
Cutting
The first step in fabrication is cutting the raw materials to the required dimensions.
This is typically done using advanced cutting machines such as laser cutters or water jet cutters.
Precision cutting ensures that each piece of the handrail fits together seamlessly, contributing to the overall strength and safety of the final product.
Shaping
After cutting, the next step is shaping the materials to match the design specifications.
This may involve bending, forming, or machining the materials to create the desired shape and contours.
Shaping is a critical step that ensures the handrails are comfortable to hold and provide the necessary support for users.
Assembling
Once the individual components are cut and shaped, they are assembled to form the complete handrail.
This can involve welding, bolting, or gluing the pieces together, depending on the materials used and the design requirements.
High-quality assembly is crucial for ensuring the handrail’s structural integrity and long-term durability.
Surface Finishing
After the handrails are fabricated and assembled, the next step is surface finishing.
This process involves treating the surface of the handrails to enhance their appearance and protect them from wear and corrosion.
Polishing and Painting
For metal handrails, polishing is often used to create a smooth, attractive finish.
Polishing can also help remove any sharp edges or burrs that could pose a safety hazard.
In some cases, the handrails may be painted or coated with a protective layer to enhance their durability and resistance to the elements.
Sealing and Staining
For wooden handrails, sealing and staining are essential surface finishing steps.
Sealing protects the wood from moisture and other environmental factors, while staining enhances the wood’s natural beauty and provides additional protection.
Proper surface finishing ensures that the handrails remain safe, attractive, and functional for years to come.
Quality Control and Testing
Ensuring the quality and safety of barrier-free handrails is paramount.
The final step in the manufacturing process involves rigorous quality control and testing to verify that the handrails meet all safety standards and performance requirements.
Structural Integrity Testing
One of the most critical aspects of quality control is testing the structural integrity of the handrails.
This involves subjecting the handrails to various stress tests to ensure they can support the weight and pressure they will encounter in everyday use.
Structural integrity testing helps identify any weaknesses or defects that could compromise the safety and effectiveness of the handrails.
Safety Compliance Checks
In addition to structural testing, the handrails are also subjected to safety compliance checks.
These checks ensure that the handrails meet all relevant safety standards and regulations.
Compliance with safety standards is essential for ensuring that the handrails provide the necessary support and protection for users.
Installation and Maintenance
The final phase of the process involves the installation and maintenance of the handrails.
Proper installation is crucial for ensuring that the handrails provide the intended safety and support.
Regular maintenance is also essential for preserving the handrails’ functionality and appearance.
Professional Installation
While some homeowners may choose to install handrails themselves, professional installation is recommended to ensure optimal safety and performance.
Professional installers have the expertise and equipment to securely attach the handrails to walls, floors, or other surfaces, ensuring that they can withstand the required loads and stresses.
Routine Maintenance
Routine maintenance of barrier-free handrails involves regular inspections to check for any signs of wear or damage.
Cleaning the handrails periodically can also help maintain their appearance and prevent the buildup of dirt and grime.
For metal handrails, checking for signs of rust or corrosion and addressing them promptly is essential.
Wooden handrails may require periodic resealing or staining to protect them from moisture and other environmental factors.
Enhancing Safety with Additional Features
To further enhance the safety and functionality of barrier-free handrails, additional features and accessories can be incorporated into the design.
Anti-Slip Grips
Anti-slip grips can be added to handrails to provide additional traction and prevent slips and falls.
These grips can be made from various materials, including rubber or textured coatings, and are especially useful in areas prone to moisture, such as bathrooms or outdoor spaces.
Integrated Lighting
Integrated lighting is another valuable feature that can enhance the safety of barrier-free handrails.
LED lights can be installed along the length of the handrails to provide illumination in low-light conditions.
This can help users navigate stairs, hallways, or outdoor pathways more safely.
Customizable Options
Offering customizable options allows homeowners to tailor the handrails to their specific needs and preferences.
Customizable options may include different colors, finishes, or decorative elements that match the home’s decor while maintaining safety and functionality.
Barrier-free handrails are essential tools for promoting safety and accessibility in residential settings.
By understanding the comprehensive manufacturing process, from design and material selection to quality control and installation, homeowners and caregivers can make informed decisions about the best handrails for their needs.
Incorporating additional safety features and performing regular maintenance can further enhance the effectiveness and longevity of these vital safety tools.
資料ダウンロード
QCD調達購買管理クラウド「newji」は、調達購買部門で必要なQCD管理全てを備えた、現場特化型兼クラウド型の今世紀最高の購買管理システムとなります。
ユーザー登録
調達購買業務の効率化だけでなく、システムを導入することで、コスト削減や製品・資材のステータス可視化のほか、属人化していた購買情報の共有化による内部不正防止や統制にも役立ちます。
NEWJI DX
製造業に特化したデジタルトランスフォーメーション(DX)の実現を目指す請負開発型のコンサルティングサービスです。AI、iPaaS、および先端の技術を駆使して、製造プロセスの効率化、業務効率化、チームワーク強化、コスト削減、品質向上を実現します。このサービスは、製造業の課題を深く理解し、それに対する最適なデジタルソリューションを提供することで、企業が持続的な成長とイノベーションを達成できるようサポートします。
オンライン講座
製造業、主に購買・調達部門にお勤めの方々に向けた情報を配信しております。
新任の方やベテランの方、管理職を対象とした幅広いコンテンツをご用意しております。
お問い合わせ
コストダウンが利益に直結する術だと理解していても、なかなか前に進めることができない状況。そんな時は、newjiのコストダウン自動化機能で大きく利益貢献しよう!
(Β版非公開)