- お役立ち記事
- Manufacturing Process of Toothbrushes and Improvement in Brush Firmness
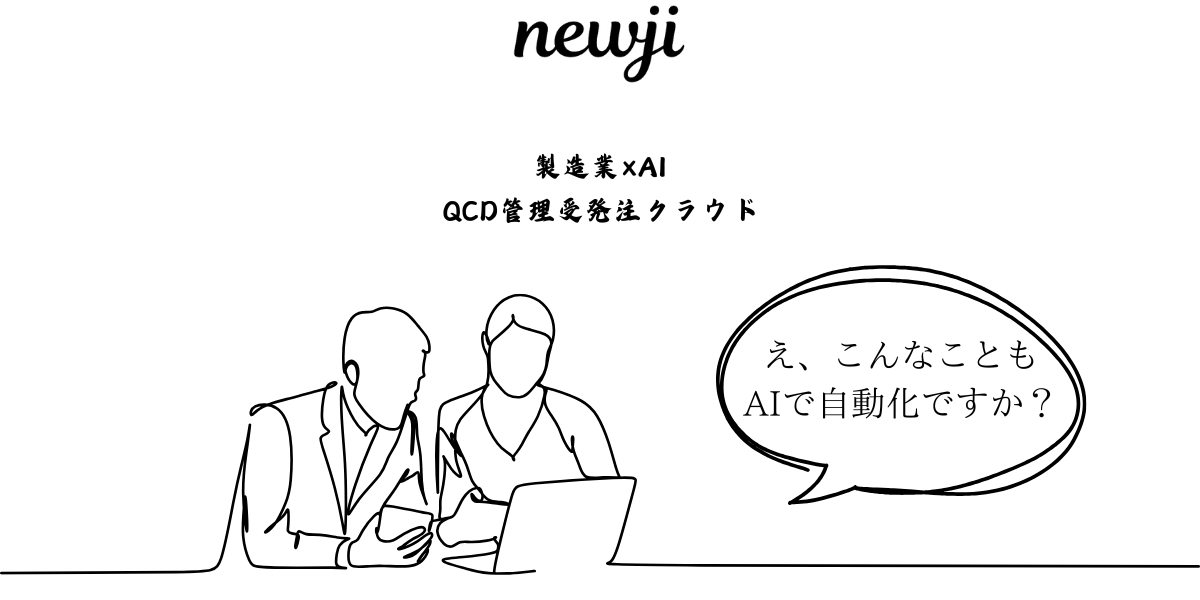
Manufacturing Process of Toothbrushes and Improvement in Brush Firmness
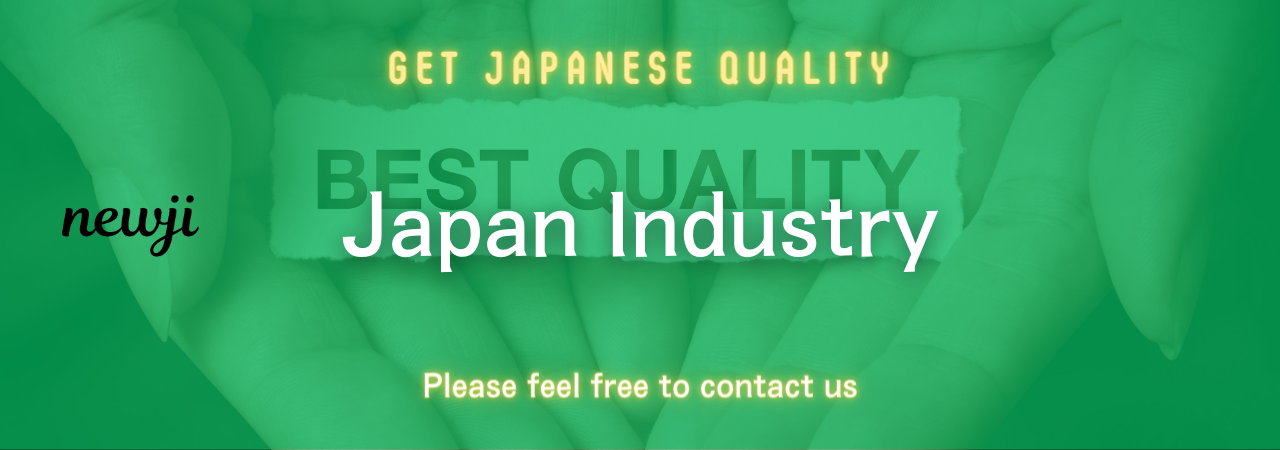
Toothbrushes are an essential part of our daily lives, helping maintain oral hygiene and bright smiles.
The manufacturing process of toothbrushes involves multiple steps, ensuring each brush is effective and safe for use.
Let’s take a closer look at the manufacturing process and explore how manufacturers improve brush firmness.
目次
Materials Used in Toothbrush Manufacturing
The process begins with selecting the right materials.
Toothbrushes typically consist of a handle and bristles.
The handle is usually made from plastic, such as polypropylene, that is lightweight and durable.
Sometimes, handles are made of bioplastics or other eco-friendly materials.
The bristles, on the other hand, are made from nylon or other synthetic fibers.
Nylon is preferred because it is resilient, flexible, and gentle on the gums.
Different types of nylon, like Nylon-6 and Nylon-6,12, offer variations in bristle firmness and durability.
Design and Mold Creation
Once the materials are selected, the next step is designing the toothbrush.
Specialized software is used to create precise and ergonomic designs that ensure comfortable and effective brushing.
After finalizing the design, manufacturers create molds for the handle and bristle components.
The molds for the handles are usually made from metal and designed to form multiple handles simultaneously.
These metal molds are placed in injection molding machines that shape the plastic into the desired form.
Handle Production
In the injection molding process, plastic pellets are heated until they turn into a liquid.
This liquid plastic is then injected into the pre-designed molds under high pressure.
Once the plastic cools and solidifies, the molded handles are ejected from the molds, ready for the next step.
Sometimes, handles may require additional features like rubber grips or decorations.
In such cases, different materials are used, and a second injection molding process is carried out.
This process is called over-molding and helps improve the grip and feel of the toothbrush handle.
Bristle Production and Tapering
While handles are being produced, the bristle manufacturing process begins.
Nylon filaments are extruded and cut to the required length.
These straight-cut nylon filaments are then grouped together to form bundles.
One crucial step in this process is tapering.
Tapered bristles have thinner tips, which are gentle on the gums and provide effective cleaning.
The tapering is achieved by using special heating and stretching techniques that make the tips finer while retaining the firmness at the base of the bristles.
Anchoring the Bristles
Anchoring the bristles onto the handle is a complex process that requires precision.
There are two main methods: staple-set and anchor-free tufting.
Staple-Set Tufting
In the staple-set method, small metal staples are used to anchor the bristle bundles into pre-drilled holes on the brush head.
The ends of the bristle bundles are folded in half and inserted into the holes along with the metal staples.
The staples are then pressed into the handle, securing the bristles firmly.
Anchor-Free Tufting
The anchor-free tufting process uses sonic welding or adhesive bonding to secure the bristles.
This method eliminates the need for metal staples, resulting in a lighter and more eco-friendly toothbrush.
The bristle bundles are placed into tiny slots, and ultrasonic waves or special adhesives bond the filaments to the handle.
Trimming and End-Rounding
After securing the bristles, the brush heads undergo trimming to achieve the desired length and shape.
This step is crucial for the performance and comfort of the toothbrush.
Next, end-rounding is performed to smoothen the tips of the bristles.
Rough, sharp bristle ends can irritate the gums and damage tooth enamel.
End-rounding machines grind and polish the bristle tips to make them smooth and rounded, ensuring a gentle brushing experience.
Quality Control and Sterilization
Quality control is a vital part of toothbrush manufacturing.
Each toothbrush is inspected for defects like bent handles, loose bristles, or uneven trimming.
Brushing performance, durability, and bristle firmness are also tested.
Sterilization is another essential step to ensure the brushes are free from harmful bacteria.
This can be achieved using various methods, such as ultraviolet (UV) sterilization, heat treatment, or chemical treatment.
Improving Brush Firmness
Brush firmness plays a crucial role in the effectiveness and user experience of a toothbrush.
Manufacturers use several techniques to enhance the firmness of toothbrushes, ensuring they are neither too hard nor too soft.
Bristle Material and Diameter
The choice of bristle material and diameter directly influences firmness.
Thicker bristles are generally firmer than thinner ones.
Manufacturers can select a specific grade of nylon or blend different materials to achieve the desired stiffness.
Bristle Arrangement
The arrangement of bristles on the brush head also affects firmness.
Denser bristle patterns tend to be firmer because there is less space between individual filaments.
This arrangement provides better resistance while brushing.
Tapered and Textured Bristles
Tapering and texturing techniques can improve brush firmness without compromising on gentleness.
Tapered bristles with fine tips can be firm at the base and gentle at the tips.
Textured bristles with ridges or patterns can add firmness and enhance cleaning efficiency.
Packaging and Distribution
Once the toothbrushes pass quality control and sterilization, they are ready for packaging.
Toothbrushes are individually packed in protective shells or blister packs to keep them hygienic.
Manufacturers often include instructions and branding information on the packaging.
The packed toothbrushes are then stored in bulk and distributed to retailers and consumers worldwide.
Toothbrush manufacturing is a meticulous process that ensures each brush is effective, safe, and enjoyable to use.
Advancements in materials, design, and technology continue to improve our brushing experience, making sure that smiles stay bright and healthy.
資料ダウンロード
QCD調達購買管理クラウド「newji」は、調達購買部門で必要なQCD管理全てを備えた、現場特化型兼クラウド型の今世紀最高の購買管理システムとなります。
ユーザー登録
調達購買業務の効率化だけでなく、システムを導入することで、コスト削減や製品・資材のステータス可視化のほか、属人化していた購買情報の共有化による内部不正防止や統制にも役立ちます。
NEWJI DX
製造業に特化したデジタルトランスフォーメーション(DX)の実現を目指す請負開発型のコンサルティングサービスです。AI、iPaaS、および先端の技術を駆使して、製造プロセスの効率化、業務効率化、チームワーク強化、コスト削減、品質向上を実現します。このサービスは、製造業の課題を深く理解し、それに対する最適なデジタルソリューションを提供することで、企業が持続的な成長とイノベーションを達成できるようサポートします。
オンライン講座
製造業、主に購買・調達部門にお勤めの方々に向けた情報を配信しております。
新任の方やベテランの方、管理職を対象とした幅広いコンテンツをご用意しております。
お問い合わせ
コストダウンが利益に直結する術だと理解していても、なかなか前に進めることができない状況。そんな時は、newjiのコストダウン自動化機能で大きく利益貢献しよう!
(Β版非公開)