- お役立ち記事
- Manufacturing Process of Turbochargers and Boost Efficiency Enhancement
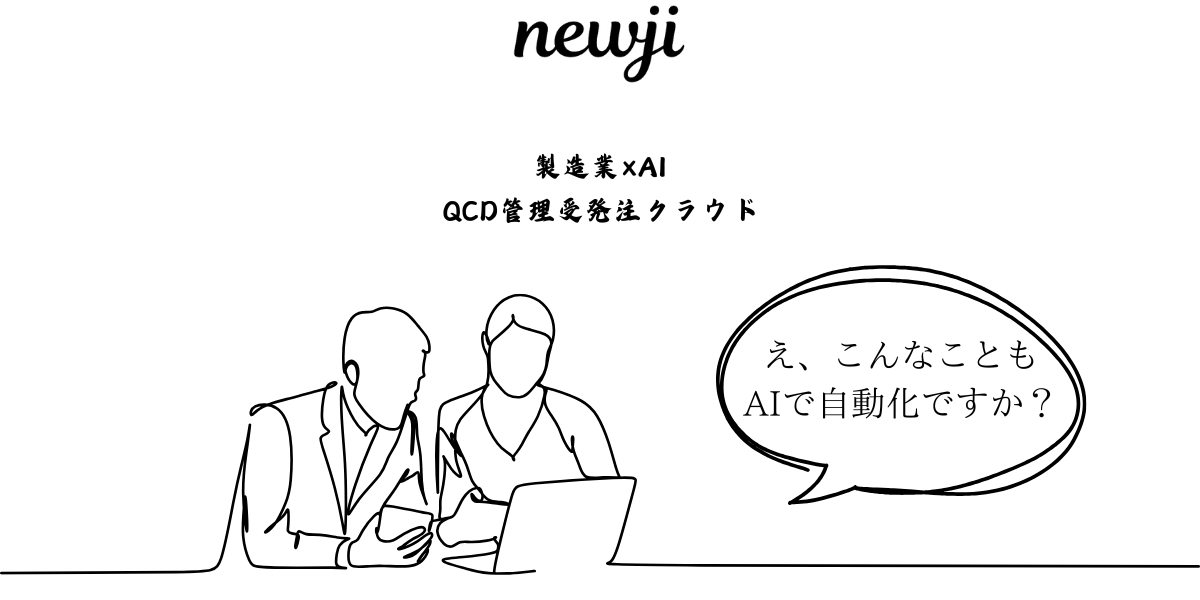
Manufacturing Process of Turbochargers and Boost Efficiency Enhancement
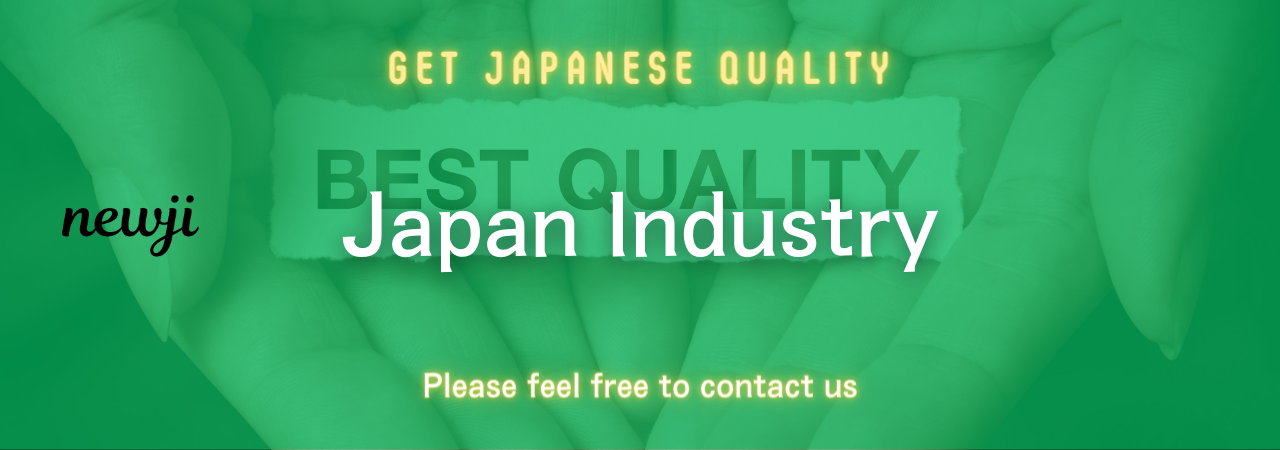
Turbochargers are powerful components that breathe new life into engines, enhancing their efficiency and performance.
In this article, we will delve into the manufacturing process of turbochargers and explore how they enhance boost efficiency.
Understanding these processes provides insight into the importance of sustainable techniques and advanced engineering in turbocharger production.
目次
What is a Turbocharger?
A turbocharger is a device fitted to an engine, designed to increase the engine’s efficiency and power output.
It does this by forcing extra compressed air into the combustion chamber.
The main components of a turbocharger include the turbine, compressor, central housing, and intercooler.
This intricate device maximizes engine performance by boosting the air-to-fuel ratio.
The Manufacturing Process of Turbochargers
The creation of a turbocharger involves several precise steps.
Each step in the manufacturing process is critical to ensure high efficiency and durability.
Design and Engineering
The first step in the manufacturing process is the design and engineering phase.
This phase involves detailed computer-aided design (CAD) to create a 3D model of the turbocharger.
Engineers consider factors like aerodynamic efficiency, material strength, and thermal properties during this stage.
Material Selection
Material selection is crucial as turbochargers operate under extreme temperatures and pressures.
Manufacturers typically use high-grade steel or alloys, such as Inconel, for the turbine and compressor wheels.
These materials are chosen for their durability and ability to withstand high stress and heat.
Precision Casting and Machining
Precision casting is used to create the turbine and compressor wheels.
In this process, a wax model of the component is created and coated with ceramic material.
Once the ceramic hardens, the wax is melted out, leaving a mold that can be filled with molten metal.
After casting, the components undergo machining to ensure they meet exact specifications.
Computer numerical control (CNC) machines are used to achieve the required precision.
Balancing and Assembly
Balancing is a critical step to ensure smooth operation and longevity of the turbocharger.
Both the turbine and compressor wheels must be perfectly balanced to avoid vibration and wear.
State-of-the-art balancing machines are used for this purpose.
Following balancing, the components are assembled into the central housing.
Seals and bearings are fitted to minimize friction and ensure the turbocharger runs smoothly.
Quality Control and Testing
Once assembled, turbochargers undergo rigorous quality control and testing.
These tests check for performance parameters such as air and oil flow, pressure, and temperature.
Any defects detected are rectified before the turbochargers are deemed fit for use.
How Turbochargers Enhance Boost Efficiency
Turbochargers significantly enhance an engine’s boost efficiency.
Let’s explore the various ways in which they achieve this.
Forced Induction
The primary function of a turbocharger is forced induction.
It compresses the incoming air, increasing its density before it enters the engine’s combustion chamber.
This means more air and fuel can be burned, resulting in greater power output and efficiency.
Reducing Lag
One potential downside of turbochargers is turbo lag, the delay in power delivery.
Innovative designs and advanced materials reduce this lag, providing a more immediate boost in engine performance.
Twin-scroll turbochargers and variable geometry turbochargers are some examples of technology developed to minimize lag.
Intercooling
Intercooling is another crucial aspect of boost efficiency.
As air is compressed by the turbocharger, it heats up.
Intercoolers cool this air before it reaches the engine, increasing air density and further enhancing power output.
Effective intercooling systems play a pivotal role in optimizing performance.
Exhaust Gas Utilization
Turbochargers utilize exhaust gases to drive the turbine that compresses the intake air.
This not only improves boost efficiency but also reduces engine temperature and emissions.
By harnessing energy from the exhaust gases, turbochargers make engines more environmentally friendly.
The Evolution of Turbocharger Technology
The development of turbocharger technology has come a long way.
Advancements in materials, engineering, and computational methods have all contributed to shattering performance benchmarks.
Material Improvements
The use of high-temperature-resistant materials like ceramic and titanium has allowed turbochargers to operate at higher temperatures and pressures.
These materials enhance the durability and efficiency of turbochargers, making them more reliable.
Design Innovations
Thanks to computer-aided design and advanced simulation tools, modern turbochargers are more efficient than ever.
New designs focus on minimizing turbo lag while maximizing airflow and pressure.
Variable geometry turbochargers, for example, adjust the air intake based on engine speed, providing optimal performance across a range of conditions.
Electric Turbochargers
The rise of electric turbochargers is one of the most exciting developments in recent years.
These devices use electric motors to spin the compressor wheel, reducing lag and providing instant boost.
Electric turbochargers are paving the way for even more efficient and responsive engines.
Conclusion
The manufacturing process of turbochargers is a complex and meticulous affair.
From design and material selection to precision casting and quality control, each step plays a crucial role in producing a high-performance component.
Turbochargers significantly boost engine efficiency through forced induction, reduced lag, intercooling, and exhaust gas utilization.
Advancements in materials and design continue to push the boundaries of what’s possible, making turbochargers a vital element in modern engine technology.
Understanding these processes and innovations gives us an appreciation for the engineering marvels that enhance our driving experiences and make engines more efficient than ever.
資料ダウンロード
QCD調達購買管理クラウド「newji」は、調達購買部門で必要なQCD管理全てを備えた、現場特化型兼クラウド型の今世紀最高の購買管理システムとなります。
ユーザー登録
調達購買業務の効率化だけでなく、システムを導入することで、コスト削減や製品・資材のステータス可視化のほか、属人化していた購買情報の共有化による内部不正防止や統制にも役立ちます。
NEWJI DX
製造業に特化したデジタルトランスフォーメーション(DX)の実現を目指す請負開発型のコンサルティングサービスです。AI、iPaaS、および先端の技術を駆使して、製造プロセスの効率化、業務効率化、チームワーク強化、コスト削減、品質向上を実現します。このサービスは、製造業の課題を深く理解し、それに対する最適なデジタルソリューションを提供することで、企業が持続的な成長とイノベーションを達成できるようサポートします。
オンライン講座
製造業、主に購買・調達部門にお勤めの方々に向けた情報を配信しております。
新任の方やベテランの方、管理職を対象とした幅広いコンテンツをご用意しております。
お問い合わせ
コストダウンが利益に直結する術だと理解していても、なかなか前に進めることができない状況。そんな時は、newjiのコストダウン自動化機能で大きく利益貢献しよう!
(Β版非公開)