- お役立ち記事
- Manufacturing Process of Vending Machine Beverage Dispensers and Temperature Control Technology
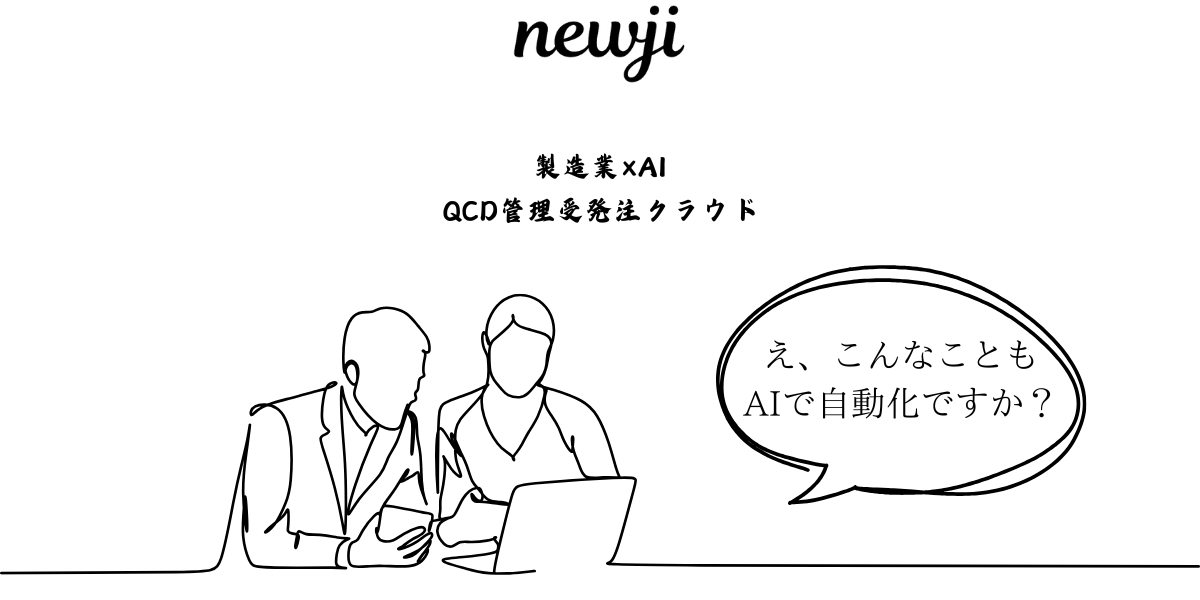
Manufacturing Process of Vending Machine Beverage Dispensers and Temperature Control Technology
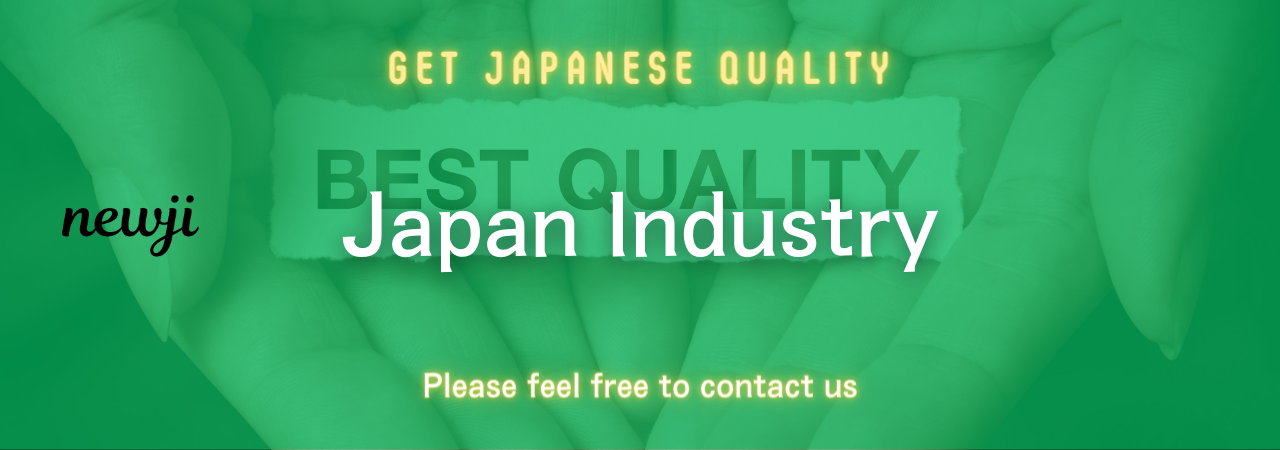
Vending machines have become an integral part of our daily lives, dispensing beverages at the press of a button.
Ever wonder how these machines work?
Let’s explore the manufacturing process of vending machine beverage dispensers and the sophisticated temperature control technology that keeps our drinks at the perfect temperature.
目次
Design and Development
The journey of a vending machine beverage dispenser begins with design and development.
Engineers and designers collaborate to create a functional and efficient machine.
This phase involves meticulous planning, as numerous factors must be considered to ensure the machine meets market demands.
First, the design team sketches prototypes and creates 3D models using computer-aided design (CAD) software.
These digital prototypes help in visualizing the machine’s appearance and functionality.
Designers focus on aspects like user interface, durability, and ease of maintenance.
Once the initial design is finalized, it moves on to the development stage.
Material Selection
Choosing the right materials is crucial for the machine’s longevity and performance.
The exterior casing is typically made from durable metals such as stainless steel or reinforced plastic.
Inside, various components are made from materials suitable for their specific functions – metals for structural parts and electronics, plastics for non-conductive areas.
Component Manufacturing
After finalizing the design and material selection, the next step is manufacturing the machine’s individual components.
These components are fabricated in specialized factories that utilize advanced machinery and processes.
Metal Fabrication
Metal parts are often created using processes like cutting, bending, and welding.
Computer-controlled machines accurately cut metal sheets into the required shapes.
These pieces are then bent into specific forms and welded together to form sturdy structures such as the frame and casing.
Plastic Molding
Plastic components are produced using an injection molding process.
In this method, molten plastic is injected into molds to create parts like buttons, panels, and other intricate shapes.
Injection molding allows for high precision and repeatability, ensuring consistent quality.
Electronic Assembly
The electronic parts, including circuit boards, sensors, and wiring, are assembled in specialized electronic manufacturing facilities.
These components are meticulously tested to ensure they meet safety and performance standards.
Integration testing is conducted to verify compatibility with other parts of the vending machine.
Assembly and Integration
With all components ready, the next phase is assembly and integration.
This stage involves putting together the different parts to form the complete vending machine.
Mechanical Assembly
Technicians assemble the metal and plastic components to create the machine’s frame and housing.
They install the dispensing mechanism, which includes motors, gears, and levers that control the release of beverages.
Special attention is given to aligning and securing these parts to ensure smooth operation.
Electrical Integration
The electronic components are integrated into the vending machine’s frame.
This includes connecting sensors, control boards, and wiring systems.
Technicians follow detailed wiring diagrams to ensure accurate connections.
They also install software that controls the machine’s functions, such as dispensing timing and user interface.
Temperature Control Technology
One of the key factors in a beverage vending machine’s performance is its ability to maintain the optimal temperature for different drinks.
Modern vending machines employ sophisticated temperature control technology to achieve this.
Cooled Beverages
For cooled beverages, refrigeration units are installed within the vending machine.
These units use compressors and refrigerants to lower the temperature of the storage area.
Sensors continuously monitor the internal temperature, ensuring it remains within the desired range.
When temperatures rise above the set point, the refrigeration system activates to cool the beverages.
Heated Beverages
Vending machines that dispense hot drinks use heating elements to maintain the desired temperature.
These elements are strategically placed around the drink storage and dispensing area.
Temperature sensors again play a critical role in monitoring and adjusting the heat levels.
When a user selects a hot beverage, the machine ensures it is dispensed at the correct temperature.
Insulation
To maintain consistent temperatures, vending machines are equipped with high-quality insulation materials.
Insulation minimizes heat transfer between the inner and outer environments of the machine.
This ensures that the internal temperature remains stable, regardless of external conditions.
Testing and Quality Control
Before vending machines hit the market, they undergo rigorous testing and quality control procedures.
Functional Testing
Functional testing ensures that all parts of the vending machine work as intended.
Technicians perform tests on the dispensing mechanism, temperature control system, and user interface.
They simulate real-world usage scenarios to identify potential issues.
Temperature Stability Testing
Temperature stability is crucial for maintaining beverage quality.
Machines are tested under various conditions to verify their ability to keep drinks at the desired temperature.
Temperature sensors are monitored to ensure accurate readings and response times.
Safety Testing
Safety is paramount in automated machines.
Vending machines undergo electrical safety tests to prevent hazards such as short circuits or electric shocks.
Mechanical safety tests check for potential malfunctions in the dispensing mechanism.
Conclusion
The manufacturing process of vending machine beverage dispensers involves a series of detailed and precise steps.
From design and development to assembly and temperature control technology, each phase plays a critical role in ensuring the final product is efficient and reliable.
Next time you grab a drink from a vending machine, you’ll have a deeper appreciation for the intricate processes and technology that made it possible.
資料ダウンロード
QCD調達購買管理クラウド「newji」は、調達購買部門で必要なQCD管理全てを備えた、現場特化型兼クラウド型の今世紀最高の購買管理システムとなります。
ユーザー登録
調達購買業務の効率化だけでなく、システムを導入することで、コスト削減や製品・資材のステータス可視化のほか、属人化していた購買情報の共有化による内部不正防止や統制にも役立ちます。
NEWJI DX
製造業に特化したデジタルトランスフォーメーション(DX)の実現を目指す請負開発型のコンサルティングサービスです。AI、iPaaS、および先端の技術を駆使して、製造プロセスの効率化、業務効率化、チームワーク強化、コスト削減、品質向上を実現します。このサービスは、製造業の課題を深く理解し、それに対する最適なデジタルソリューションを提供することで、企業が持続的な成長とイノベーションを達成できるようサポートします。
オンライン講座
製造業、主に購買・調達部門にお勤めの方々に向けた情報を配信しております。
新任の方やベテランの方、管理職を対象とした幅広いコンテンツをご用意しております。
お問い合わせ
コストダウンが利益に直結する術だと理解していても、なかなか前に進めることができない状況。そんな時は、newjiのコストダウン自動化機能で大きく利益貢献しよう!
(Β版非公開)