- お役立ち記事
- Manufacturing Process of Wheel Hubs and Durability Enhancement
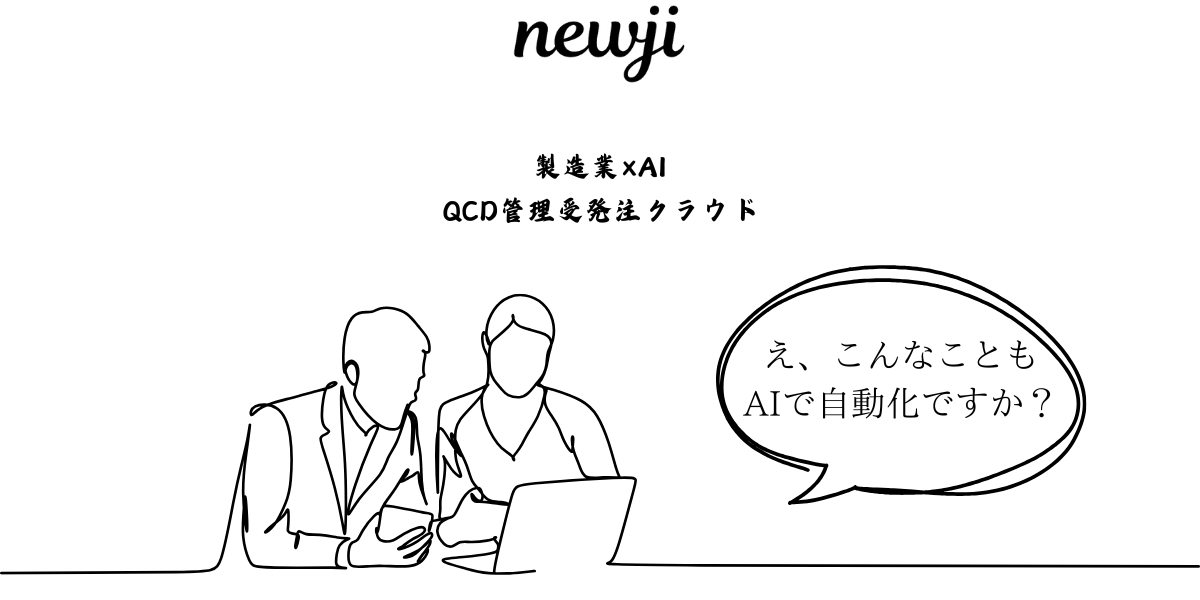
Manufacturing Process of Wheel Hubs and Durability Enhancement
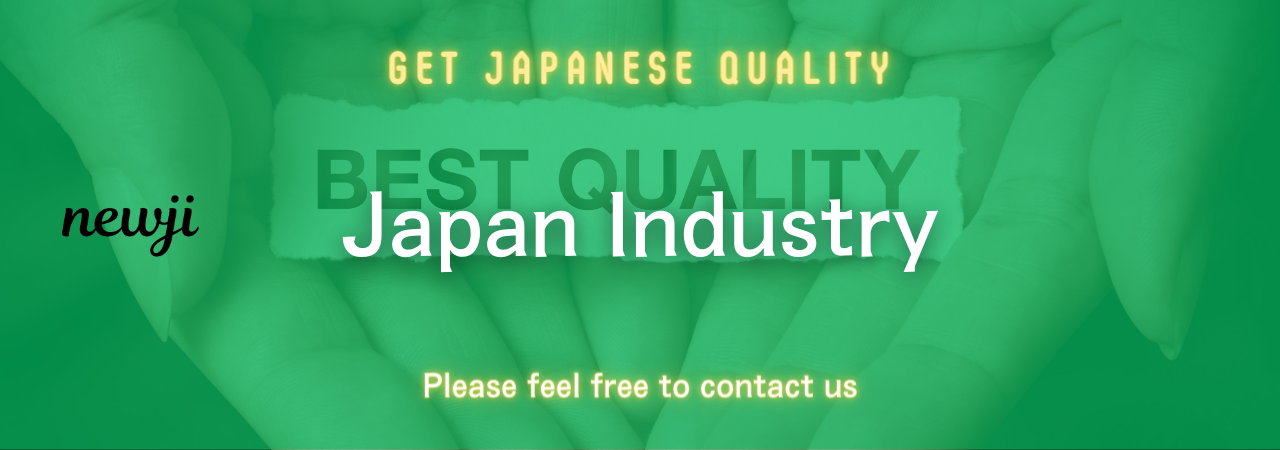
In the complex realm of automotive engineering, the wheel hub is a crucial component that connects the wheel to the vehicle’s axle and geometric centerline.
The hub plays a pivotal role in supporting the vehicle’s weight, transferring loads between the wheels, and ensuring smooth rotation.
Manufacturing wheel hubs involves a precise and intricate process aimed at enhancing durability and performance.
目次
Understanding the Materials Used
To manufacture wheel hubs, selecting the right material is paramount.
Typically, wheel hubs are crafted from high-strength steel, aluminum alloys, or a combination of both.
Steel is preferred for its strength and toughness, offering excellent load-bearing capacity and resistance to wear and tear.
Aluminum, on the other hand, is lighter, which contributes to better fuel efficiency and overall vehicle performance.
Manufacturing Process
1. Designing and Planning
The manufacturing process begins with designing the wheel hub using advanced computer-aided design (CAD) software.
Engineers take into account various factors such as load distribution, rotational forces, and thermal expansion.
The design phase also includes simulations to predict the hub’s performance under different conditions.
2. Material Procurement
Once the design is finalized, the next step is procuring high-quality materials.
Suppliers provide steel billets or aluminum ingots that meet the specified standards and requirements.
Quality control checks ensure that only the best materials proceed to the next stage.
3. Forging
Forging is a crucial step in the manufacturing of wheel hubs.
The raw materials are heated to a very high temperature and then shaped using powerful presses and dies.
Forging refines the grain structure of the material, enhancing its strength and fatigue resistance.
4. Machining
After forging, the hubs undergo machining to achieve the final dimensions and tolerances.
CNC (Computer Numerical Control) machines are used for precise cutting, drilling, and shaping.
This stage also involves creating holes for bolts, bearing seats, and other necessary configurations.
5. Heat Treatment
Heat treatment further enhances the mechanical properties of the wheel hub.
Different heat treatment processes such as annealing, quenching, and tempering are employed to achieve the desired hardness and toughness.
This step is vital to ensure that the hub can withstand the stresses and strains during operation.
6. Surface Treatment
Surface treatment is done to protect the wheel hub from corrosion and improve its aesthetic appeal.
Common surface treatments include shot peening, which increases fatigue resistance, and coating or painting to prevent rusting.
Anodizing is often used for aluminum hubs to provide a durable oxide layer.
7. Quality Control
Quality control is an ongoing process throughout the manufacturing stages.
Every wheel hub undergoes rigorous inspection using advanced testing equipment.
Parameters such as dimensional accuracy, surface finish, and material properties are checked to ensure compliance with industry standards.
Durability Enhancement Techniques
1. High-Precision Machining
Achieving high precision in machining processes ensures tighter tolerances and better fitting parts.
This reduces unnecessary stresses and wear, contributing to the overall durability of the wheel hub.
2. Material Selection and Alloying
Choosing the right alloy composition enhances the wheel hub’s strength and resistance to environmental factors.
Advanced alloys often incorporate elements such as chromium, molybdenum, and vanadium to improve performance.
3. Advanced Heat Treatment
Utilizing advanced heat treatment techniques can significantly increase the fatigue resistance and mechanical strength of the hub.
Processes like induction hardening are specifically tailored to improve the longevity of the component.
4. Regular Maintenance and Inspection
Beyond manufacturing, regular maintenance and inspection are crucial for preserving the durability of wheel hubs.
Periodic checks help identify potential issues before they escalate, ensuring the hubs remain in optimal condition.
5. Stress Relieving Techniques
Stress relieving techniques, such as shot peening, help in reducing residual stresses within the wheel hub.
This process improves the hub’s fatigue life and resistance to crack propagation.
Conclusion
The manufacturing process of wheel hubs combines meticulous design, material selection, and sophisticated engineering techniques.
From forging to heat treatment and stringent quality control, each step plays a crucial role in ensuring the hub’s durability and performance.
By implementing advanced manufacturing practices and durability enhancement techniques, manufacturers produce wheel hubs that meet the high demands of modern vehicles.
As technology continues to evolve, wheel hub manufacturing will become even more precise and efficient, paving the way for safer and more reliable automotive components.
資料ダウンロード
QCD調達購買管理クラウド「newji」は、調達購買部門で必要なQCD管理全てを備えた、現場特化型兼クラウド型の今世紀最高の購買管理システムとなります。
ユーザー登録
調達購買業務の効率化だけでなく、システムを導入することで、コスト削減や製品・資材のステータス可視化のほか、属人化していた購買情報の共有化による内部不正防止や統制にも役立ちます。
NEWJI DX
製造業に特化したデジタルトランスフォーメーション(DX)の実現を目指す請負開発型のコンサルティングサービスです。AI、iPaaS、および先端の技術を駆使して、製造プロセスの効率化、業務効率化、チームワーク強化、コスト削減、品質向上を実現します。このサービスは、製造業の課題を深く理解し、それに対する最適なデジタルソリューションを提供することで、企業が持続的な成長とイノベーションを達成できるようサポートします。
オンライン講座
製造業、主に購買・調達部門にお勤めの方々に向けた情報を配信しております。
新任の方やベテランの方、管理職を対象とした幅広いコンテンツをご用意しております。
お問い合わせ
コストダウンが利益に直結する術だと理解していても、なかなか前に進めることができない状況。そんな時は、newjiのコストダウン自動化機能で大きく利益貢献しよう!
(Β版非公開)