- お役立ち記事
- Manufacturing Process of Wooden Coasters and Waterproofing Improvement
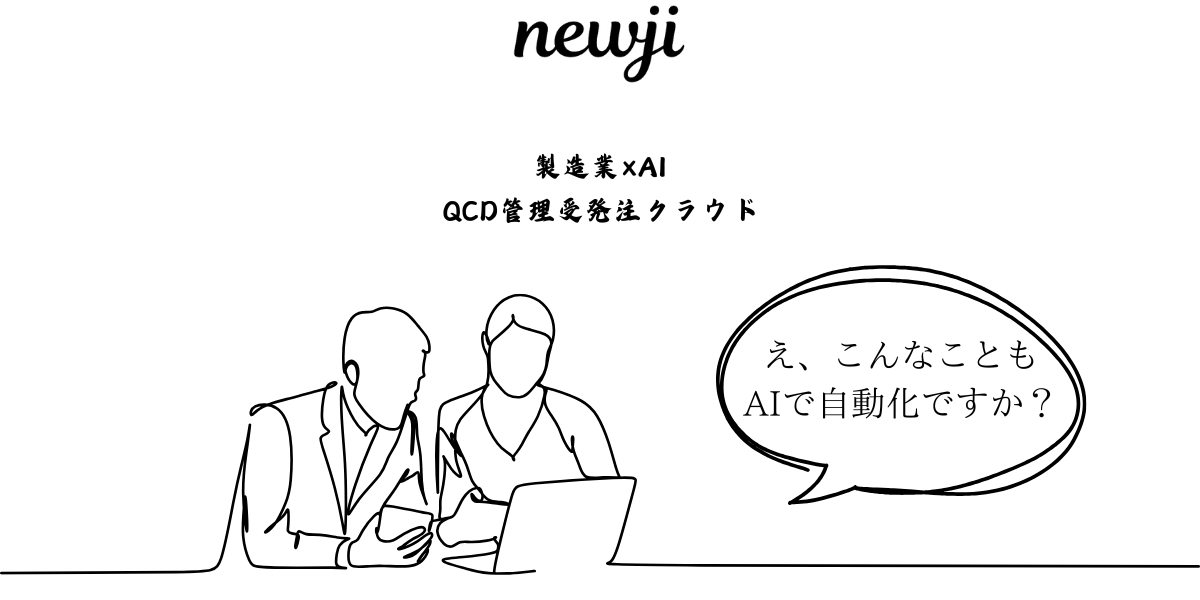
Manufacturing Process of Wooden Coasters and Waterproofing Improvement
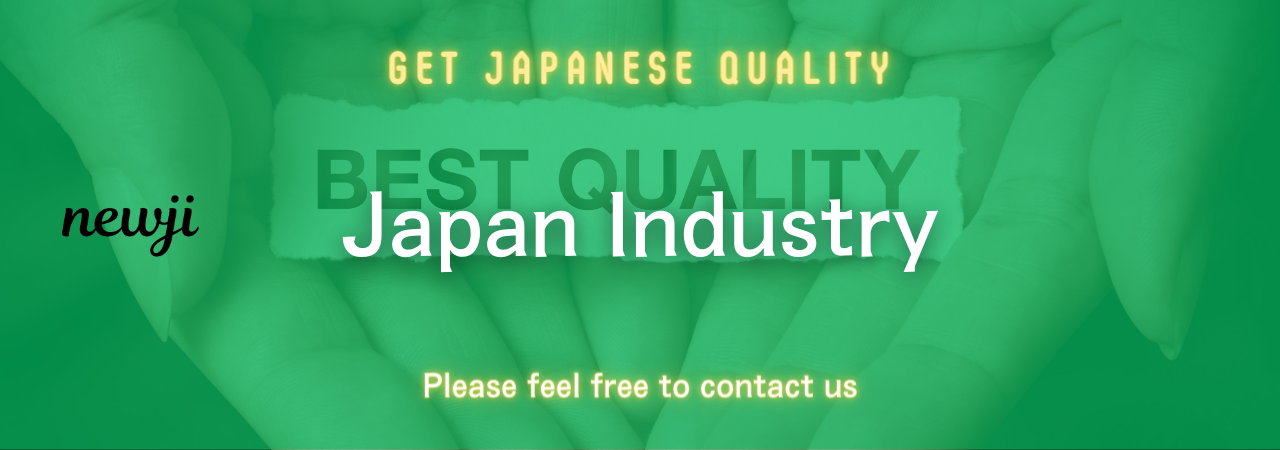
Wooden coasters are practical and charming additions to any home or office.
They offer a natural and earthy aesthetic, protecting surfaces from drink stains.
Creating these coasters involves several detailed steps, focusing on precision and material quality.
Knowing the process and how to improve their waterproofing can significantly extend their usability and visual appeal.
目次
Selecting the Right Wood
Choosing the correct type of wood is crucial for durability and appearance.
Commonly used woods include oak, maple, cherry, and walnut.
These types are favored because they are hard, dense, and have beautiful natural grains.
Softwoods like pine are less suitable because they are more prone to dents and not as water-resistant.
Selecting a seasoned piece of wood ensures it won’t warp or crack during the manufacturing process.
Preparation and Cutting
First, the wood needs to be cut down to the desired size and shape for the coasters.
Typically, coasters are between 3.5 to 4 inches in diameter and around 0.25 to 0.5 inches thick.
Using a band saw or a circular saw, these measurements are adhered to strictly for consistency.
After cutting, the edges may need rounding or bevelling, which can be done using a router or sandpaper to smooth out any rough edges.
Sanding and Smoothing
Sanding is a critical step to ensure the coaster’s surface is even and smooth.
Starting with a coarse-grit sandpaper, work your way to a fine-grit for a polished finish.
This step may involve multiple rounds of sanding, particularly if there are noticeable imperfections.
A smooth surface not only looks appealing but also provides a better area for finishing applications later on.
It’s also essential for the absorbent and protective properties of the coaster.
Designing and Engraving
Adding designs or engravings can provide a personal touch to wooden coasters.
This can be done either manually with carving tools or through the use of laser engravers for precision.
Popular designs include monograms, floral patterns, or simple geometric shapes.
Fans of DIY projects might prefer hand-drawn designs, which add a unique charm.
For commercial production, laser engraving offers consistency and can handle intricate patterns with ease.
Always ensure the surface is cleaned before moving on to the next step.
Applying a Finish
Once your design is complete, it’s time to apply a finish to protect the wood and enhance its appearance.
Common finishes include oil, varnish, polyurethane, and shellac.
Linseed oil and tung oil are popular for highlighting the wood’s natural grain while providing basic moisture resistance.
Polyurethane is a more robust option offering better protection against water and stains.
Apply the finish with a brush or cloth, ensuring an even coat, and allow it to dry completely before handling.
Improving Waterproofing
To keep wooden coasters in excellent condition, improving their waterproofing is essential.
A highly effective method involves the use of a sealant like waterproof polyurethane.
This type of sealant creates a hard, water-resistant layer on the coaster’s surface.
Steps for Waterproofing
1. **Clean the Surface**: Ensure the coaster is free of dust and debris.
This is critical for the sealant to adhere properly.
2. **Apply Sealant**: Using a brush, apply an even layer of waterproof polyurethane.
Ensure you cover every part of the surface and the edges.
3. **Drying Time**: Allow sufficient time for the first layer to dry, generally 24 hours.
Ensuring the first coat is fully dry prevents streaks and bubbles in the finish.
4. **Additional Coats**: For best results, apply at least two to three coats.
Each layer adds more protection and durability.
Sand lightly between coats with a fine-grit sandpaper for a smoother finish.
5. **Final Drying**: Allow the final coat to cure completely, which might take several days.
This ensures maximum hardness and water resistance.
Polishing for Final Touch
After the final coat of sealant has dried, a light polish can enhance the appearance.
Using fine steel wool or a high-grit sandpaper, rub gently over the surface.
This step removes any minor imperfections and provides a lovely sheen.
Then, use a soft cloth to buff the coaster, bringing out a polished glow.
Maintaining polished coasters is crucial for preserving their look and functionality.
Maintenance Tips
Even with excellent waterproofing, wooden coasters require some care to remain in top shape.
Avoid soaking the coasters in water; instead, wipe them with a damp cloth when cleaning.
Periodic re-application of a sealant every six months to a year can help maintain their waterproof qualities.
If you notice any wear or scratches, a quick sanding and re-sealing can restore their original beauty.
With these care tips, your wooden coasters will remain a beautiful and practical part of your décor for years to come.
Creating wooden coasters and ensuring they are adequately waterproofed involves careful selection and preparation of materials, precise cutting, detailed design work, and multiple finishing stages.
By following these steps diligently, you can produce coasters that are not only aesthetically pleasing but also durable and functional.
Maintaining them with proper cleaning and occasional re-sealing will keep them looking fresh and new, providing long-lasting protection for your surfaces.
資料ダウンロード
QCD調達購買管理クラウド「newji」は、調達購買部門で必要なQCD管理全てを備えた、現場特化型兼クラウド型の今世紀最高の購買管理システムとなります。
ユーザー登録
調達購買業務の効率化だけでなく、システムを導入することで、コスト削減や製品・資材のステータス可視化のほか、属人化していた購買情報の共有化による内部不正防止や統制にも役立ちます。
NEWJI DX
製造業に特化したデジタルトランスフォーメーション(DX)の実現を目指す請負開発型のコンサルティングサービスです。AI、iPaaS、および先端の技術を駆使して、製造プロセスの効率化、業務効率化、チームワーク強化、コスト削減、品質向上を実現します。このサービスは、製造業の課題を深く理解し、それに対する最適なデジタルソリューションを提供することで、企業が持続的な成長とイノベーションを達成できるようサポートします。
オンライン講座
製造業、主に購買・調達部門にお勤めの方々に向けた情報を配信しております。
新任の方やベテランの方、管理職を対象とした幅広いコンテンツをご用意しております。
お問い合わせ
コストダウンが利益に直結する術だと理解していても、なかなか前に進めることができない状況。そんな時は、newjiのコストダウン自動化機能で大きく利益貢献しよう!
(Β版非公開)