- お役立ち記事
- Manufacturing Techniques to Improve the Quality of Nylon Products for SMEs
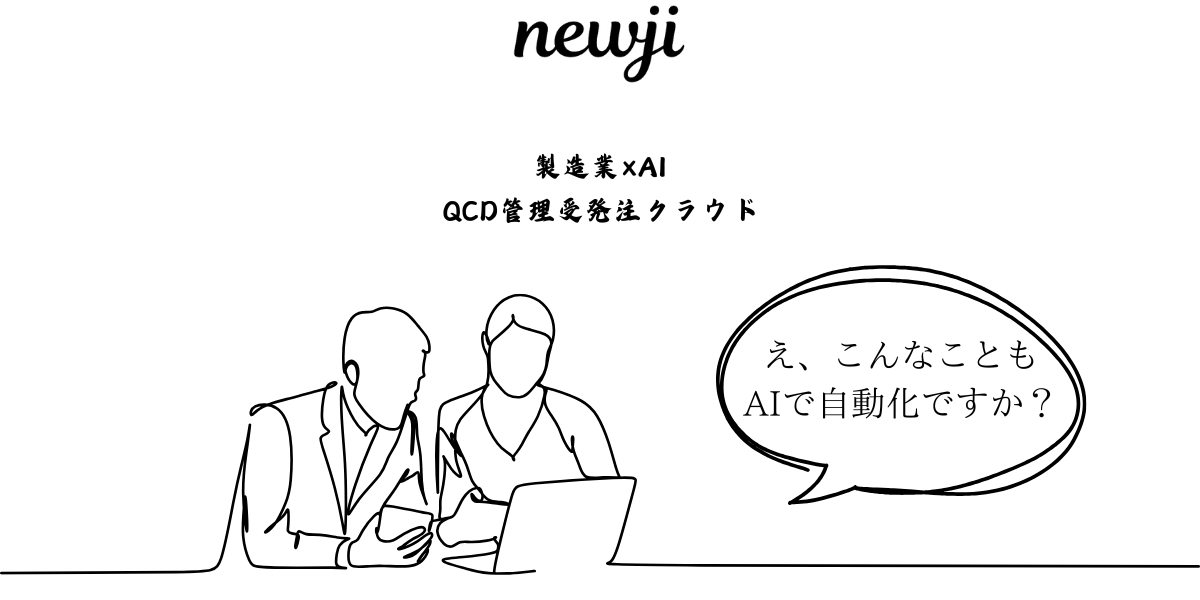
Manufacturing Techniques to Improve the Quality of Nylon Products for SMEs
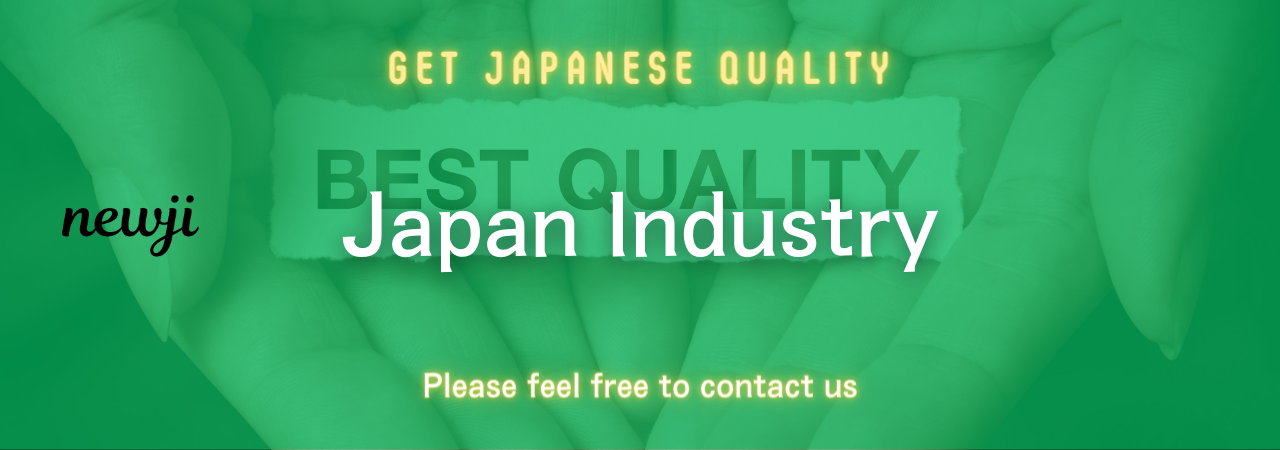
目次
Introduction to Nylon Product Manufacturing
Nylon, a synthetic polymer, has become a staple in the textile and manufacturing industries due to its strength, flexibility, and resistance to wear and tear.
Small and Medium Enterprises (SMEs) involved in producing nylon goods face unique challenges.
They must balance cost-efficiency with the need for high-quality output to remain competitive in the marketplace.
Understanding the various manufacturing techniques available can significantly enhance the quality and durability of nylon products.
In this guide, we will explore several methods and strategies that SMEs can employ to improve the quality of their nylon products.
Raw Material Selection
The first step in manufacturing high-quality nylon products is selecting the right raw materials.
Nylon comes in various grades, including Nylon 6 and Nylon 6,6, each with specific properties suitable for different applications.
SMEs should carefully evaluate their product requirements and choose the appropriate nylon type.
Why Quality Raw Materials Matter
Using high-quality raw materials can prevent issues such as brittleness or inconsistent texture in the final product.
Raw material suppliers should be selected based on their reputation, consistency, and the quality of their offerings.
Performing thorough quality checks during the procurement process can save time and resources in the long run.
Optimizing the Production Process
Once the right materials are selected, attention should turn to optimizing the production process.
Several techniques can enhance manufacturing efficiency and product quality.
Injection Molding Expertise
Injection molding is a popular method for producing nylon products due to its precision and efficiency.
For optimal results, SMEs should ensure that they have skilled operators who understand the nuances of the injection molding process.
Adjusting parameters like temperature, pressure, and mold design can significantly impact the quality of the final product.
Maintaining Equipment
Regular maintenance of manufacturing equipment is crucial for consistent production quality.
Malfunctioning machinery can lead to defects and waste.
SMEs should implement a routine maintenance schedule and train staff to identify early signs of equipment wear and tear.
Quality Control Measures
Implementing stringent quality control measures throughout the production process is essential in ensuring high-quality products.
In-Process Inspections
Conducting inspections at various stages of the production process can help identify defects early.
These checks can range from visual inspections to more advanced methods, such as ultrasonic testing or computer tomography, depending on the product’s complexity and requirements.
Quality control measures should ensure that any defects are caught and rectified promptly before products move further along the production line.
Final Product Testing
The final testing phase should verify that the products meet predetermined quality standards and specifications.
Testing should include checks for strength, flexibility, and resistance to environmental factors like heat and moisture.
Furthermore, SMEs should maintain comprehensive records of test results for analysis and continuous improvement.
Staff Training and Development
Well-trained staff are vital to maintaining and improving the quality of nylon products.
Providing ongoing training helps workers stay updated with the latest manufacturing techniques and industry best practices.
Training Programs
SMEs should invest in comprehensive training programs for all their employees involved in the production process.
These programs should cover up-to-date information on material properties, machinery operation, safety protocols, and quality control procedures.
Encouraging Skill Development
Encouraging staff to develop their skills can foster a culture of continuous improvement.
Providing incentives for innovation and excellence can motivate employees to enhance product quality.
Regular workshops or seminars by industry experts can expose staff to fresh perspectives and techniques.
Collaborative Product Development
Working closely with designers and engineers during the product development phase can lead to significant improvements in product quality.
Collaboration ensures that the design is efficient for manufacturing and meets customer expectations.
Prototyping and Testing
Creating prototypes can provide valuable insights into potential design flaws or manufacturing challenges.
Prototypes allow teams to test products in real-world conditions and make necessary adjustments before full-scale production begins.
This proactive approach helps in refining products and minimizing the risk of defects.
Client and Supplier Feedback
Actively seeking feedback from clients and suppliers can also enhance product quality.
Suppliers may offer insights into material properties or alternative materials that can improve product performance, while clients can provide feedback on the product’s functionality and aesthetics.
Using this feedback effectively allows SMEs to adapt their manufacturing techniques to better meet market demands.
Environmental Considerations
As sustainability becomes increasingly important, SMEs must adapt their manufacturing practices to reduce environmental impact while maintaining high product quality.
Sustainable Materials
Exploring eco-friendly alternatives and recycling practices can help SMEs reduce their carbon footprint.
For example, using recycled nylon or developing bio-based alternatives can contribute to sustainability goals.
Waste Reduction
Implementing waste reduction strategies in the manufacturing process can improve overall efficiency.
Strategies such as reusing scrap material or optimizing production to minimize off-cuts can significantly reduce waste and improve quality.
Conclusion
Manufacturing high-quality nylon products is a multifaceted challenge for SMEs.
By focusing on the selection of raw materials, optimizing production processes, enforcing rigorous quality control, investing in staff development, promoting collaboration, and considering environmental factors, these enterprises can enhance the durability and performance of their nylon products.
Adopting these approaches not only boosts product quality but also strengthens the competitiveness of SMEs in the global market.
Through continuous improvement and adaptation, SMEs can secure their position as leaders in nylon product manufacturing.
資料ダウンロード
QCD調達購買管理クラウド「newji」は、調達購買部門で必要なQCD管理全てを備えた、現場特化型兼クラウド型の今世紀最高の購買管理システムとなります。
ユーザー登録
調達購買業務の効率化だけでなく、システムを導入することで、コスト削減や製品・資材のステータス可視化のほか、属人化していた購買情報の共有化による内部不正防止や統制にも役立ちます。
NEWJI DX
製造業に特化したデジタルトランスフォーメーション(DX)の実現を目指す請負開発型のコンサルティングサービスです。AI、iPaaS、および先端の技術を駆使して、製造プロセスの効率化、業務効率化、チームワーク強化、コスト削減、品質向上を実現します。このサービスは、製造業の課題を深く理解し、それに対する最適なデジタルソリューションを提供することで、企業が持続的な成長とイノベーションを達成できるようサポートします。
オンライン講座
製造業、主に購買・調達部門にお勤めの方々に向けた情報を配信しております。
新任の方やベテランの方、管理職を対象とした幅広いコンテンツをご用意しております。
お問い合わせ
コストダウンが利益に直結する術だと理解していても、なかなか前に進めることができない状況。そんな時は、newjiのコストダウン自動化機能で大きく利益貢献しよう!
(Β版非公開)