- お役立ち記事
- Mastering Cost Performance: The Secret Behind Japanese Manufacturing Excellence
月間77,185名の
製造業ご担当者様が閲覧しています*
*2025年2月28日現在のGoogle Analyticsのデータより
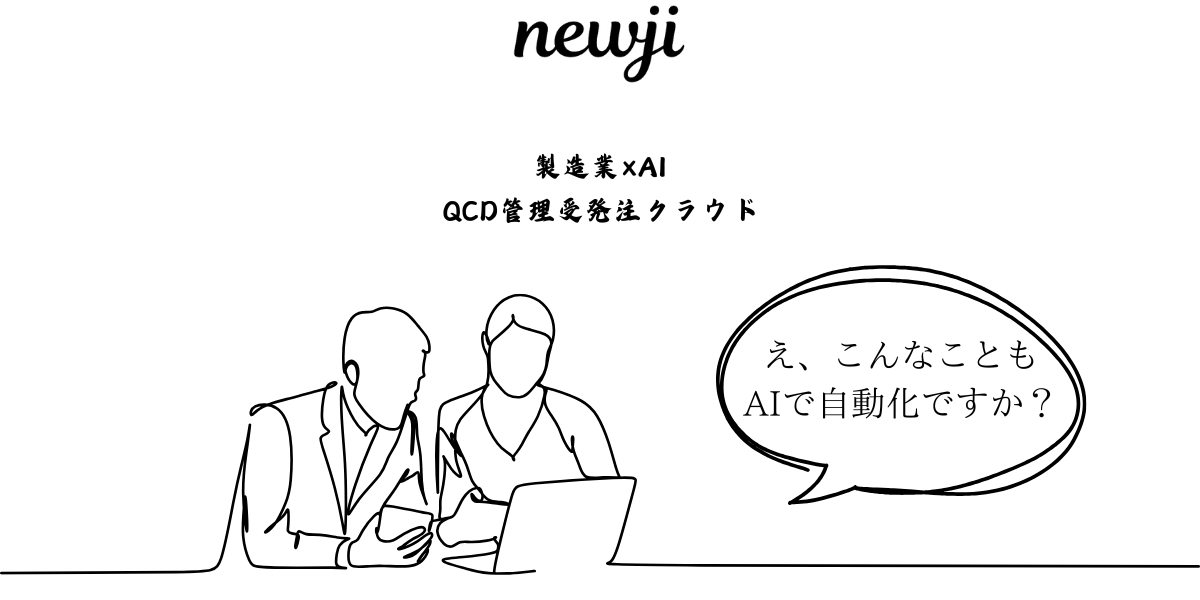
Mastering Cost Performance: The Secret Behind Japanese Manufacturing Excellence
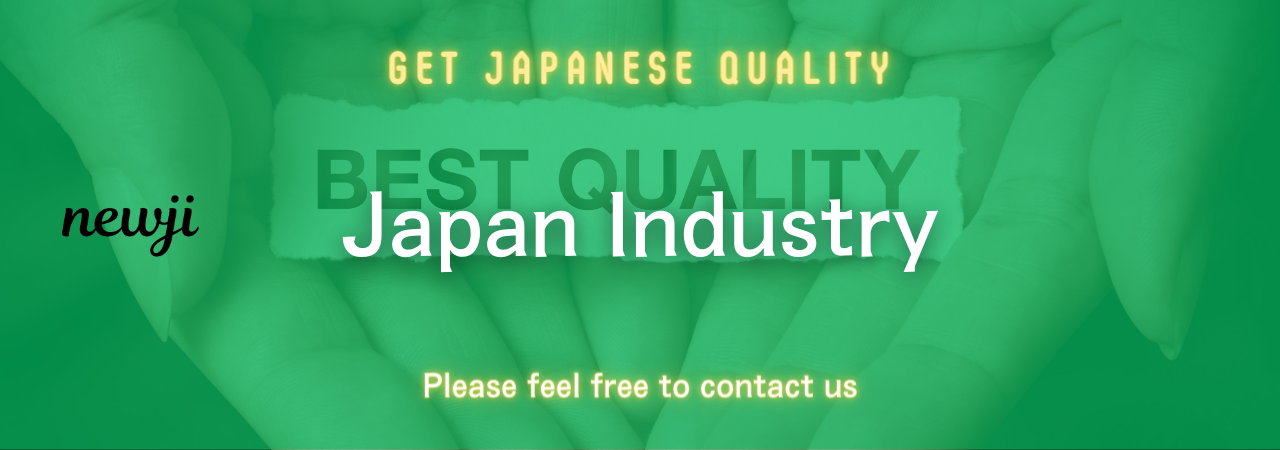
目次
Introduction to Japanese Manufacturing Excellence
Japanese manufacturing has long been synonymous with quality, efficiency, and innovation.
Understanding the secrets behind this excellence provides valuable insights for businesses worldwide.
Cost performance is a critical aspect of their success, balancing affordability with superior quality.
This article delves into the strategies and practices that underpin Japan’s manufacturing prowess.
By exploring procurement and purchasing perspectives, we uncover the elements that contribute to their remarkable cost efficiency.
We also examine the advantages and disadvantages of these approaches, offering a comprehensive view of the landscape.
Additionally, supplier negotiation techniques, market conditions, and best practices are discussed to provide a well-rounded understanding.
Whether you’re a procurement professional or a business leader, mastering these concepts can enhance your operational effectiveness.
The Japanese model serves as a benchmark for many, illustrating how strategic management can lead to sustained excellence.
Let’s embark on a journey to uncover the secrets behind Japan’s manufacturing success and how you can apply these lessons to your own endeavors.
The Pillars of Japanese Cost Performance
Lean Manufacturing: The Toyota Production System
Lean manufacturing is at the heart of Japanese manufacturing excellence.
Originating from the Toyota Production System (TPS), it emphasizes waste reduction without sacrificing productivity.
By streamlining processes, companies can achieve higher efficiency and lower costs.
The TPS focuses on continuous improvement and respect for people, fostering a culture of excellence.
This system integrates quality control at every stage, ensuring that defects are minimized.
Lean manufacturing encourages flexibility, allowing companies to adapt quickly to market changes.
The result is a production system that is both cost-effective and resilient.
Implementing lean principles requires commitment and a deep understanding of processes.
However, the benefits in cost performance and operational efficiency are substantial.
Japanese companies have mastered this approach, setting a standard for others to follow.
Just-in-Time (JIT) Inventory Management
Just-in-Time inventory management is another cornerstone of Japanese manufacturing.
JIT aims to reduce inventory levels by receiving goods only as they are needed in the production process.
This minimizes storage costs and reduces waste associated with overstocking.
By synchronizing production schedules with supplier deliveries, companies can operate more efficiently.
JIT requires precise coordination and reliable suppliers, ensuring that materials arrive exactly when needed.
This approach enhances cash flow and reduces the capital tied up in inventory.
Moreover, it promotes a more responsive and agile manufacturing system.
Japanese manufacturers excel in JIT through strong supplier relationships and effective communication.
The implementation of JIT has been instrumental in achieving high levels of cost performance.
It allows companies to maintain lean operations while meeting customer demands promptly.
Kaizen: Continuous Improvement Culture
Kaizen, meaning “continuous improvement,” is a fundamental philosophy in Japanese manufacturing.
This approach involves all employees, from top management to the shop floor, in identifying and implementing improvements.
Kaizen fosters a proactive mindset, encouraging regular evaluation of processes and practices.
By continually refining operations, companies can enhance quality and reduce costs.
This culture of incremental improvements leads to significant long-term benefits.
Employees are empowered to suggest changes, fostering a sense of ownership and accountability.
Kaizen also promotes problem-solving skills and innovation, driving overall organizational growth.
The collective effort in continuous improvement ensures that companies remain competitive and efficient.
Adopting Kaizen principles can transform an organization’s approach to cost management and operational excellence.
Procurement and Purchasing Strategies
Building Strong Supplier Relationships
Strong supplier relationships are essential for achieving cost performance.
Japanese manufacturers prioritize long-term partnerships over short-term gains.
By fostering trust and collaboration, companies can negotiate better terms and secure reliable supplies.
Stable relationships with suppliers lead to consistent quality and timely deliveries.
This reliability is crucial for maintaining efficient production schedules and minimizing disruptions.
Moreover, long-term partnerships encourage suppliers to invest in their capabilities, further enhancing quality and cost-effectiveness.
Japanese companies often involve suppliers in the design and development process, ensuring that components meet precise specifications.
This collaborative approach reduces the need for costly revisions and rework.
Building strong supplier relationships requires transparent communication and mutual respect.
The benefits extend beyond cost savings, contributing to overall operational excellence.
Supplier Negotiation Techniques
Effective negotiation with suppliers is a key component of Japanese procurement strategies.
Japanese negotiators focus on creating win-win scenarios, where both parties benefit from the agreement.
This approach fosters goodwill and long-term cooperation, rather than adversarial relationships.
Negotiations typically involve detailed discussions about quality standards, delivery schedules, and pricing structures.
Japanese companies often use objective criteria and data-driven arguments to support their positions.
Flexibility and problem-solving are emphasized, allowing for adjustments that meet both parties’ needs.
Building rapport and understanding cultural nuances are also important in Japanese negotiations.
This comprehensive and respectful approach leads to agreements that are equitable and sustainable.
By mastering these negotiation techniques, companies can secure favorable terms while maintaining strong supplier alliances.
Advantages of Japanese Manufacturing Excellence
High Quality and Reliability
One of the most significant advantages of Japanese manufacturing is the high level of quality and reliability.
Japanese companies are renowned for producing durable and dependable products that meet stringent standards.
This commitment to quality reduces defects and returns, enhancing customer satisfaction.
Consistent quality also strengthens brand reputation and customer loyalty.
Moreover, high reliability translates to lower maintenance and operational costs for end-users.
Japanese manufacturers achieve this through meticulous quality control processes and continuous improvement practices.
The focus on quality is ingrained in the company’s culture, ensuring that it is maintained across all operations.
This dedication results in products that are not only cost-effective but also trusted by consumers worldwide.
Efficiency and Waste Reduction
Efficiency is a hallmark of Japanese manufacturing, driven by lean principles and waste reduction strategies.
By optimizing workflows and eliminating non-value-adding activities, companies achieve greater productivity.
This efficiency translates to lower production costs and faster turnaround times.
Waste reduction encompasses not only materials but also time, energy, and labor.
Implementing practices like JIT inventory management ensures that resources are used judiciously.
Efficient operations enable companies to respond swiftly to market changes and customer demands.
This agility is critical in today’s fast-paced business environment, where delays can lead to lost opportunities.
Japanese manufacturers excel in creating streamlined processes that maximize output while minimizing costs.
The resulting efficiency is a competitive advantage that sets them apart in the global market.
Flexibility and Responsiveness
Flexibility and responsiveness are critical attributes of Japanese manufacturing excellence.
Companies are capable of adapting quickly to changes in consumer preferences, market conditions, and technological advancements.
This adaptability is facilitated by agile production systems and a culture of continuous improvement.
Japanese manufacturers invest in versatile machinery and cross-trained employees, allowing for swift reconfiguration of production lines.
This flexibility ensures that companies can introduce new products and respond to demand fluctuations without significant delays.
Responsiveness also extends to customer service, where prompt and effective support enhances client satisfaction.
The ability to pivot and innovate in response to evolving needs is a key factor in sustaining long-term success.
Japanese manufacturers’ commitment to flexibility ensures that they remain relevant and competitive in dynamic markets.
Challenges and Disadvantages
Cultural Barriers
While Japanese manufacturing practices offer many advantages, there are challenges associated with cultural barriers.
Differences in business etiquette, communication styles, and management practices can pose obstacles for international partnerships.
Understanding and respecting these cultural nuances is essential for successful collaboration.
Misinterpretations or lack of cultural awareness can lead to misunderstandings and strained relationships.
Overcoming these barriers requires ongoing efforts in cultural training and fostering open communication.
Japanese companies often prioritize harmony and consensus, which may differ from more direct negotiation styles in other cultures.
Adapting to these cultural differences is crucial for foreign businesses seeking to engage with Japanese suppliers.
By bridging cultural gaps, companies can leverage the strengths of Japanese manufacturing while mitigating potential conflicts.
High Initial Investment
Implementing Japanese manufacturing practices often requires significant initial investment.
Adopting lean systems, advanced technologies, and continuous improvement programs can be costly upfront.
Small and medium-sized enterprises may find it challenging to allocate the necessary resources for such investments.
However, the long-term benefits, including cost savings and enhanced efficiency, typically outweigh the initial expenses.
Companies must carefully plan and budget to accommodate these investments without compromising other operational areas.
Access to financing and strategic partnerships can help alleviate the financial burden associated with implementation.
Despite the high initial costs, the return on investment from improved cost performance and operational excellence is substantial.
Japanese manufacturers demonstrate that commitment to quality and efficiency pays dividends over time.
Complexity of Implementation
The complexity of implementing Japanese manufacturing strategies is another challenge faced by many organizations.
Practices like lean manufacturing and JIT inventory management require a deep understanding and meticulous execution.
Employees must be trained extensively, and processes need to be redesigned to align with new methodologies.
This transformation can disrupt existing operations and require a shift in organizational culture.
Furthermore, sustaining these practices demands ongoing commitment and continuous evaluation.
Companies may encounter resistance to change, necessitating effective change management strategies.
The complexity is compounded when integrating these practices with existing systems and workflows.
Overcoming these implementation challenges is essential for harnessing the full benefits of Japanese manufacturing excellence.
Market Conditions and Global Competitiveness
Adaptation to Global Markets
Japanese manufacturers have successfully adapted to diverse global markets, tailoring their products and strategies to meet local demands.
This adaptability is crucial in a world with varying consumer preferences and regulatory environments.
By customizing offerings, companies can enhance their appeal and competitiveness in different regions.
Understanding cultural and economic differences allows for more effective market penetration and expansion.
Japanese firms often conduct thorough market research to inform their strategies, ensuring alignment with local needs.
This responsiveness to market conditions fosters stronger customer relationships and brand loyalty.
Adapting to global markets also involves navigating trade policies and leveraging international trade agreements.
The ability to seamlessly adjust to various market dynamics is a testament to the resilience and versatility of Japanese manufacturing.
Competitive Pricing Strategies
Competitive pricing is a key strategy employed by Japanese manufacturers to maintain their global edge.
By optimizing production processes and reducing costs, companies can offer high-quality products at attractive prices.
This approach not only appeals to cost-conscious consumers but also enhances market share against competitors.
Japanese firms achieve competitive pricing through economies of scale, efficient supply chains, and strategic sourcing.
Moreover, lean manufacturing practices contribute to lower operational costs, which are reflected in product pricing.
Competitive pricing helps Japanese companies remain viable in markets with intense competition and price sensitivity.
Balancing affordability with quality is essential for sustaining long-term success and customer satisfaction.
Japanese manufacturers’ ability to offer value-for-money products reinforces their position as market leaders.
Technological Advancements
Technological advancements play a pivotal role in Japanese manufacturing excellence.
Investments in automation, robotics, and advanced manufacturing technologies enhance efficiency and precision.
These technologies enable higher production rates, improved quality control, and reduced labor costs.
Japanese companies are at the forefront of integrating cutting-edge technologies into their operations.
This commitment to innovation allows for the development of sophisticated products that meet evolving consumer demands.
Technological advancements also facilitate better data management and analytics, supporting informed decision-making.
By staying ahead in technology adoption, Japanese manufacturers can maintain their competitive advantage.
Continuous investment in research and development ensures that companies remain at the forefront of industry trends and advancements.
Best Practices for Mastering Cost Performance
Embracing Lean Principles
Embracing lean principles is fundamental to mastering cost performance in manufacturing.
Lean methodologies focus on eliminating waste, optimizing processes, and enhancing value for customers.
By adopting practices such as value stream mapping and continuous improvement, companies can identify and remove inefficiencies.
Streamlined operations lead to lower production costs and faster delivery times, boosting overall cost performance.
Lean principles also promote a culture of accountability and proactive problem-solving among employees.
Implementing lean practices requires comprehensive training and a commitment to ongoing evaluation.
However, the results in terms of efficiency gains and cost savings are well worth the effort.
Japanese manufacturers exemplify the successful application of lean principles, serving as models for other industries.
Investing in Employee Training and Development
Investing in employee training and development is crucial for achieving manufacturing excellence and cost performance.
Well-trained employees are more productive, produce higher quality work, and are better equipped to identify improvement opportunities.
Japanese companies prioritize continuous learning, offering regular training programs and professional development opportunities.
This investment fosters a skilled and knowledgeable workforce capable of adapting to new technologies and methodologies.
Empowered employees contribute to a culture of excellence and are more likely to engage in continuous improvement initiatives.
Moreover, training enhances employee satisfaction and retention, reducing costs associated with turnover.
By cultivating a talented workforce, companies can sustain high levels of performance and innovation.
Employee development is a strategic investment that underpins long-term success and cost efficiency.
Leveraging Technology and Automation
Leveraging technology and automation is essential for enhancing cost performance in modern manufacturing.
Automation streamlines production processes, reduces labor costs, and increases output consistency.
Advanced technologies such as robotics, artificial intelligence, and the Internet of Things (IoT) enable more precise and efficient operations.
Japanese manufacturers are pioneers in integrating these technologies into their production lines.
Automation also improves safety and reduces the risk of human error, contributing to higher quality standards.
Furthermore, technology facilitates better data collection and analysis, supporting informed decision-making and process optimization.
Investing in the latest technologies ensures that companies remain competitive and capable of meeting evolving market demands.
By harnessing the power of technology and automation, businesses can achieve significant improvements in cost performance and operational efficiency.
Case Studies: Success Stories in Japanese Manufacturing
Toyota: A Benchmark in Lean Manufacturing
Toyota stands as a paragon of Japanese manufacturing excellence, renowned for its implementation of the Toyota Production System (TPS).
TPS embodies lean manufacturing principles, emphasizing waste reduction, continuous improvement, and respect for people.
Toyota’s commitment to quality and efficiency has propelled it to the forefront of the global automotive industry.
The company’s ability to produce reliable vehicles at competitive prices demonstrates the effectiveness of its cost performance strategies.
Toyota’s success is attributed to its robust supplier relationships, innovative production techniques, and a culture of continuous improvement.
The company’s adaptability and responsiveness to market changes have ensured its sustained competitiveness.
Toyota’s practices serve as a model for manufacturers worldwide seeking to enhance cost performance and operational excellence.
Through its unwavering dedication to lean principles, Toyota continues to set industry standards and inspire best practices.
Sony: Innovating for Cost Efficiency
Sony exemplifies how innovation can drive cost performance in the competitive electronics industry.
The company’s focus on research and development has led to the creation of cutting-edge products that meet diverse consumer needs.
Sony’s investment in technology and automation has streamlined production processes, reducing costs and increasing efficiency.
By integrating advanced manufacturing techniques, Sony ensures high quality and reliability in its products.
The company’s strategic sourcing and supplier partnerships contribute to cost savings and operational effectiveness.
Sony’s ability to innovate while maintaining cost performance has enabled it to stay ahead in a fast-paced market.
The company’s diverse product portfolio and adaptability to changing trends demonstrate its commitment to excellence.
Sony’s success underscores the importance of balancing innovation with cost management to achieve sustained growth and competitiveness.
Conclusion: The Future of Japanese Manufacturing Excellence
Japanese manufacturing excellence, underpinned by mastery in cost performance, continues to influence global industries.
The principles of lean manufacturing, just-in-time inventory, and continuous improvement remain relevant and adaptable.
As markets evolve and new challenges emerge, Japanese companies demonstrate resilience and adaptability.
Investments in technology, employee development, and strong supplier relationships ensure sustained competitiveness.
However, overcoming cultural barriers and managing implementation complexities are essential for leveraging these strategies effectively.
The future of Japanese manufacturing lies in balancing tradition with innovation, maintaining high standards while embracing new methodologies.
Global businesses can learn valuable lessons from Japan’s approach to cost performance, applying these insights to enhance their own operations.
As the manufacturing landscape becomes increasingly dynamic, the secrets behind Japanese excellence will continue to offer guidance and inspiration.
Mastering cost performance through these proven strategies is a path to achieving operational excellence and sustained success in the global marketplace.
資料ダウンロード
QCD管理受発注クラウド「newji」は、受発注部門で必要なQCD管理全てを備えた、現場特化型兼クラウド型の今世紀最高の受発注管理システムとなります。
ユーザー登録
受発注業務の効率化だけでなく、システムを導入することで、コスト削減や製品・資材のステータス可視化のほか、属人化していた受発注情報の共有化による内部不正防止や統制にも役立ちます。
NEWJI DX
製造業に特化したデジタルトランスフォーメーション(DX)の実現を目指す請負開発型のコンサルティングサービスです。AI、iPaaS、および先端の技術を駆使して、製造プロセスの効率化、業務効率化、チームワーク強化、コスト削減、品質向上を実現します。このサービスは、製造業の課題を深く理解し、それに対する最適なデジタルソリューションを提供することで、企業が持続的な成長とイノベーションを達成できるようサポートします。
製造業ニュース解説
製造業、主に購買・調達部門にお勤めの方々に向けた情報を配信しております。
新任の方やベテランの方、管理職を対象とした幅広いコンテンツをご用意しております。
お問い合わせ
コストダウンが利益に直結する術だと理解していても、なかなか前に進めることができない状況。そんな時は、newjiのコストダウン自動化機能で大きく利益貢献しよう!
(β版非公開)