- お役立ち記事
- Mastering Japanese Manufacturing: The Role of “Powder” in Technological Innovation
Mastering Japanese Manufacturing: The Role of “Powder” in Technological Innovation
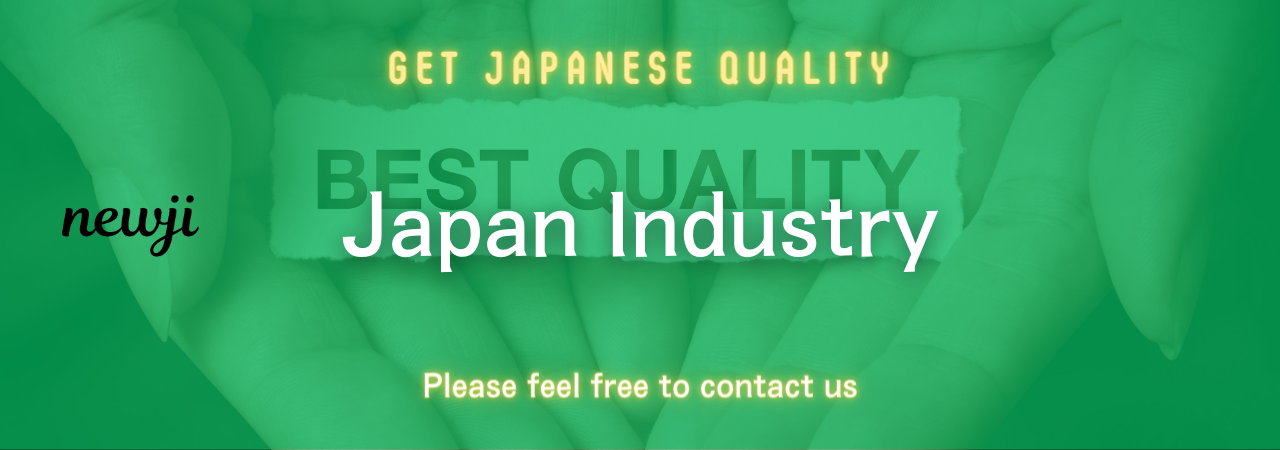
目次
Understanding the Importance of “Powder” in Japanese Manufacturing
Japanese manufacturing is renowned worldwide for its precision, quality, and innovation. Central to many technological advancements within this sector is the often-overlooked element of “powder.” Powdered materials play an essential role in various industrial applications, from electronics to automotive, driven by their unique properties and transformative potential.
The Role of Powders in Manufacturing
Powders provide a versatile and efficient solution for creating advanced materials. Their fine particle size helps in producing even, consistent surfaces and contributes to the enhanced strength and durability of final products.
In sectors such as electronics, powders are crucial in forming conductive and non-conductive layers. In automotive, they are used to create light yet strong components. Ceramics, pharmaceuticals, and metallurgy also heavily rely on the unique characteristics of different powders.
The Advantages of Using Powders
Enhanced Material Properties
One of the key benefits of using powders in manufacturing is achieving unparalleled material properties. Powders can be engineered to provide exceptional hardness, wear resistance, and thermal stability. This is particularly important in high-precision industries such as aerospace and automotive, where material reliability and longevity are paramount.
Improved Manufacturing Process
Powders facilitate more efficient manufacturing processes. They can be compacted and sintered to create complex shapes that would be challenging to achieve using traditional solid-state methods. This not only reduces machinery wear and tear but also decreases the time required for production cycles.
Cost Efficiency
While the initial cost of high-quality powders might be higher, their long-term benefits outweigh the investment. The reduction in material waste and the enhanced durability of powder-based components lead to significant cost savings over time.
Challenges and Disadvantages
High Initial Investment
One of the primary drawbacks is the high initial cost associated with powder materials and the specialized equipment needed for processing them. This can be a significant barrier for smaller enterprises looking to adopt this technology.
Quality Control Issues
Ensuring the consistent quality of powders can be challenging. Variations in particle size, shape, and purity can significantly impact the final product’s performance, making strict quality control measures essential.
Environmental Concerns
The production and handling of powders can pose environmental risks. Fine particles can become airborne, leading to respiratory hazards for workers and contributing to environmental pollution. Therefore, proper safety and environmental protection protocols are crucial.
Procurement and Purchasing Strategies for Japanese Powders
Supplier Selection
Choosing the right supplier is critical when procuring powders from Japan. It’s vital to research and select suppliers with a track record of producing high-quality materials. Look for certifications and affiliations with industry bodies as indicators of reliability.
Negotiation Techniques
Negotiating with Japanese suppliers requires an understanding of their business etiquette and culture. Building a relationship based on trust and mutual respect can significantly enhance the negotiation process. Be prepared for detailed discussions and ensure clarity on product specifications, delivery schedules, and quality control measures.
Market Conditions
Stay informed about market conditions affecting powder availability and prices. Global events, regulatory changes, and advancements in technology can influence the supply chain. Having up-to-date market intelligence can help in making informed procurement decisions.
Best Practices in Using Powders in Manufacturing
Rigorous Testing and Quality Control
Implement rigorous testing standards to ensure the quality of powders before they enter the production process. Use advanced analytical techniques such as scanning electron microscopy (SEM) and X-ray diffraction (XRD) to verify particle size, shape, and composition.
Optimized Processing Conditions
Establish optimal processing conditions for handling and utilizing powders. This includes determining the best temperature, pressure, and atmosphere for sintering processes and adjusting them as necessary to maintain product consistency.
Continuous Improvement
Continuously seek ways to improve powder handling and processing techniques. Invest in research and development to keep up with advances in powder technology, and regularly review and update standard operating procedures to align with industry best practices.
Technological Innovations Enabled by Powders
Advanced Ceramics
Powders are essential in the creation of advanced ceramics used in electronics, medical devices, and automotive components. These ceramics offer high strength, chemical resistance, and thermal stability, making them ideal for demanding applications.
3D Printing
The advent of 3D printing technologies has been significantly bolstered by the use of powdered materials. This additive manufacturing process allows for the creation of complex geometries and bespoke designs, revolutionizing industries from aerospace to healthcare.
Nanotechnology
Nanopowders have paved the way for innovations in nanotechnology, leading to the development of materials with unique properties such as increased reactivity, improved magnetic properties, and enhanced electrical conductivity. These advancements are crucial in fields like energy storage, drug delivery, and environmental protection.
Leveraging Japanese Expertise in Powder Manufacturing
Collaborative Research and Development
Engage in collaborative research and development initiatives with Japanese manufacturers. This can lead to the co-creation of novel materials and processes tailored to specific industry needs. Joint ventures and partnerships can help in leveraging Japanese expertise while sharing costs and risks.
Training and Knowledge Transfer
Invest in training programs to transfer knowledge and skills related to powder technology from Japanese manufacturers to your teams. This can include hands-on training sessions, workshops, and participation in industry seminars and conferences.
Adopting Lean Manufacturing Principles
Incorporate lean manufacturing principles when working with powders to enhance efficiency and reduce waste. Japanese manufacturers are known for their lean practices, which can be adapted and implemented to improve production workflows.
Conclusion
The role of powders in Japanese manufacturing cannot be overstated. These materials enable significant technological innovations and contribute to the superior quality and performance of Japanese products.
However, successfully integrating powders into manufacturing processes requires a deep understanding of their properties, meticulous quality control, and strategic procurement practices. By leveraging the expertise and proven practices of Japanese manufacturers, companies around the globe can benefit from the advancements in powder technology, driving their own innovations and maintaining a competitive edge in the market.
資料ダウンロード
QCD調達購買管理クラウド「newji」は、調達購買部門で必要なQCD管理全てを備えた、現場特化型兼クラウド型の今世紀最高の購買管理システムとなります。
ユーザー登録
調達購買業務の効率化だけでなく、システムを導入することで、コスト削減や製品・資材のステータス可視化のほか、属人化していた購買情報の共有化による内部不正防止や統制にも役立ちます。
NEWJI DX
製造業に特化したデジタルトランスフォーメーション(DX)の実現を目指す請負開発型のコンサルティングサービスです。AI、iPaaS、および先端の技術を駆使して、製造プロセスの効率化、業務効率化、チームワーク強化、コスト削減、品質向上を実現します。このサービスは、製造業の課題を深く理解し、それに対する最適なデジタルソリューションを提供することで、企業が持続的な成長とイノベーションを達成できるようサポートします。
オンライン講座
製造業、主に購買・調達部門にお勤めの方々に向けた情報を配信しております。
新任の方やベテランの方、管理職を対象とした幅広いコンテンツをご用意しております。
お問い合わせ
コストダウンが利益に直結する術だと理解していても、なかなか前に進めることができない状況。そんな時は、newjiのコストダウン自動化機能で大きく利益貢献しよう!
(Β版非公開)