- お役立ち記事
- Mastering Precision: The Japanese Edge in Ceramic Injection Molding Technology
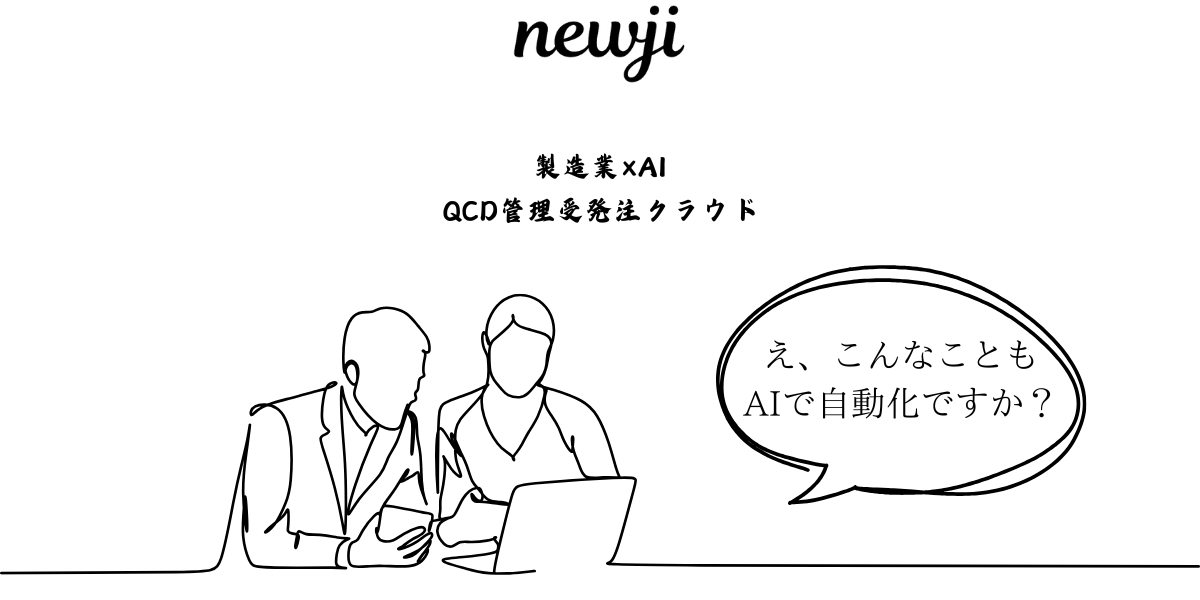
Mastering Precision: The Japanese Edge in Ceramic Injection Molding Technology
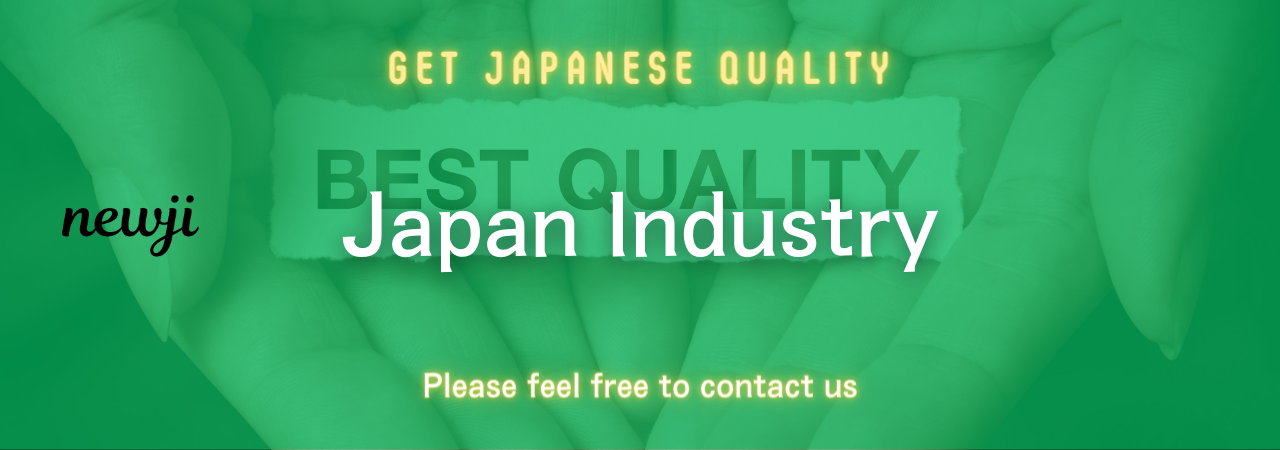
目次
Introduction to Ceramic Injection Molding
Ceramic injection molding (CIM) is a vital manufacturing process used to produce complex, high-precision ceramic parts. This technology combines the versatility of plastic injection molding with the superior material properties of ceramics. It is essential in industries such as automotive, aerospace, medical devices, and electronics, where components require high strength, thermal stability, and wear resistance.
Ceramic injection molding involves mixing ceramic powders with a binder to create a feedstock that can be injected into molds. After molding, the binder is removed, and the ceramic part is sintered to achieve its final properties. The precision and efficiency of CIM make it an indispensable process for producing intricate ceramic components in large volumes.
The Japanese Mastery in Precision Molding
Japan has established itself as a global leader in precision molding technologies, including ceramic injection molding. Japanese manufacturers are renowned for their commitment to quality, innovation, and continuous improvement, often guided by principles such as Kaizen and Total Quality Management (TQM).
Japanese firms invest heavily in research and development, leading to advancements in CIM technologies. Their expertise encompasses not only the molding process but also the entire supply chain, from material sourcing to final product inspection. This comprehensive approach ensures that Japanese ceramic injection molding delivers exceptional precision and reliability.
Advantages of Japanese Ceramic Injection Molding Technology
High Precision and Quality
Japanese ceramic injection molding technology is synonymous with high precision. Advanced machinery and meticulous process controls ensure that parts meet stringent dimensional tolerances and surface finish requirements. This precision is critical for applications where even minor deviations can lead to significant performance issues.
Moreover, Japanese manufacturers adhere to rigorous quality standards, often exceeding international benchmarks. Certifications such as ISO 9001 and ISO/TS 16949 are commonly held, reflecting their dedication to maintaining consistent quality across all production stages.
Advanced Materials and Technology
Japan’s leadership in materials science contributes significantly to the superiority of its CIM technology. Japanese suppliers utilize advanced ceramic materials that offer enhanced mechanical properties, thermal stability, and chemical resistance. Innovations in binder technologies and sintering processes further improve the performance of ceramic parts.
Additionally, Japanese manufacturers employ state-of-the-art equipment, including multi-axis injection molding machines and automated handling systems. These technologies enable the production of complex geometries with minimal defects, ensuring that components meet the most demanding specifications.
Efficient Production Processes
Efficiency is a hallmark of Japanese manufacturing. Lean manufacturing principles are extensively applied to ceramic injection molding operations, minimizing waste and optimizing resource utilization. Automated processes and just-in-time (JIT) production models enhance operational efficiency, reducing lead times and lowering production costs.
Furthermore, Japanese firms emphasize continuous improvement, regularly analyzing and refining their production workflows. This focus on efficiency ensures that they can deliver high-quality ceramic parts promptly, meeting the dynamic needs of global markets.
Disadvantages and Challenges
Higher Costs
One of the primary challenges in sourcing from Japanese ceramic injection molding suppliers is the higher cost associated with their services. Superior quality and advanced technology come at a premium, which can impact the overall cost structure of manufacturing projects. For companies with tight budgets, this may pose a significant consideration.
Language and Cultural Barriers
Navigating language differences and cultural nuances can be challenging when working with Japanese suppliers. Effective communication is crucial for successful procurement, and misunderstandings may arise from differences in business practices and expectations. Building strong relationships requires patience and a willingness to bridge cultural gaps.
Lead Times and Supply Chain Issues
While Japanese manufacturers are efficient, global supply chain disruptions can still affect lead times. Factors such as natural disasters, geopolitical tensions, and transportation delays can impact the timely delivery of ceramic parts. Companies must plan for potential delays and develop contingency strategies to mitigate these risks.
Supplier Negotiation Techniques with Japanese Manufacturers
Building Long-term Relationships
In Japan, business relationships are often built on trust and mutual respect. Establishing long-term partnerships is essential for successful negotiations. Demonstrating commitment to a lasting collaboration can lead to more favorable terms, better service, and preferential treatment in times of high demand.
Understanding Japanese Business Etiquette
Respecting Japanese business etiquette can significantly enhance negotiation outcomes. This includes punctuality, exchanging business cards with both hands, and showing deference to senior representatives. Understanding and adhering to these cultural practices can foster goodwill and facilitate smoother negotiations.
Leveraging Mutual Benefits
Effective negotiations with Japanese suppliers focus on creating win-win scenarios. Highlighting how the partnership can benefit both parties encourages cooperation and flexibility. Whether it’s volume commitments, technological exchange, or collaborative innovation, emphasizing mutual advantages can lead to more successful agreements.
Market Conditions for Ceramic Injection Molding
Global Demand Trends
The demand for ceramic injection molding is influenced by the growth of industries requiring high-performance ceramic components. Sectors such as automotive, aerospace, medical devices, and electronics are driving the need for precision-engineered ceramic parts. Global trends towards miniaturization, increased performance standards, and the adoption of new technologies continue to fuel market growth.
Competitive Landscape in Japan
Japan’s ceramic injection molding market is highly competitive, with numerous firms striving for excellence. Leading companies invest in cutting-edge technologies and specialize in niche areas to differentiate themselves. This competitive environment drives continuous innovation and improvement, ensuring that Japanese suppliers remain at the forefront of the CIM industry.
Technological Innovations
Technological advancements are shaping the future of ceramic injection molding. Innovations in materials science, such as the development of high-performance ceramics, are expanding the applications of CIM. Additionally, the integration of digital technologies, including Industry 4.0 and smart manufacturing, enhances process control, quality assurance, and supply chain management.
Best Practices in Procuring from Japanese Suppliers
Conducting Thorough Supplier Evaluations
Before partnering with Japanese ceramic injection molding suppliers, conduct comprehensive evaluations to assess their capabilities, quality standards, and financial stability. Site visits, audits, and reviews of certifications and customer testimonials provide valuable insights into a supplier’s reliability and performance.
Establishing Clear Communication Channels
Effective communication is critical for successful procurement. Establish clear and open channels for exchanging information, addressing issues, and providing feedback. Utilizing bilingual personnel or professional translation services can help overcome language barriers and ensure that technical specifications and requirements are accurately conveyed.
Implementing Quality Assurance Protocols
Maintaining high-quality standards requires robust quality assurance protocols. Collaborate with Japanese suppliers to define quality metrics, inspection criteria, and testing procedures. Regular quality audits and performance reviews help ensure that the ceramic parts meet the required specifications and that any issues are promptly addressed.
The Future of Japanese Ceramic Injection Molding Technology
The future of Japanese ceramic injection molding technology is poised for significant advancements driven by innovation and evolving market demands. Emerging trends such as additive manufacturing, automation, and sustainable practices are set to transform the CIM landscape.
Japanese manufacturers are likely to continue investing in research and development to enhance material properties, reduce production costs, and improve process efficiencies. The integration of artificial intelligence and machine learning into CIM processes can further optimize production, predict maintenance needs, and minimize defects.
Additionally, the increasing focus on sustainability will drive the adoption of eco-friendly materials and energy-efficient manufacturing practices. Japanese firms are at the forefront of developing green CIM technologies, ensuring that ceramic injection molding remains both high-performance and environmentally responsible.
Conclusion
Mastering precision in ceramic injection molding is essential for producing high-quality ceramic components that meet the demands of various industries. Japan’s leadership in CIM technology is a testament to its commitment to quality, innovation, and continuous improvement. By leveraging the advantages of Japanese suppliers, including their superior precision, advanced materials, and efficient production processes, companies can enhance their procurement strategies and achieve exceptional manufacturing outcomes.
However, navigating the challenges of higher costs, cultural differences, and supply chain uncertainties requires strategic planning and effective negotiation techniques. Building long-term relationships, understanding Japanese business etiquette, and focusing on mutual benefits are key to successful collaborations.
As the CIM market continues to evolve, Japanese manufacturers are well-positioned to drive future advancements and meet the growing global demand for high-performance ceramic parts. Embracing best practices in procurement and staying attuned to technological innovations will enable companies to fully harness the Japanese edge in ceramic injection molding technology, ensuring sustained growth and competitive advantage in their respective industries.
資料ダウンロード
QCD調達購買管理クラウド「newji」は、調達購買部門で必要なQCD管理全てを備えた、現場特化型兼クラウド型の今世紀最高の購買管理システムとなります。
ユーザー登録
調達購買業務の効率化だけでなく、システムを導入することで、コスト削減や製品・資材のステータス可視化のほか、属人化していた購買情報の共有化による内部不正防止や統制にも役立ちます。
NEWJI DX
製造業に特化したデジタルトランスフォーメーション(DX)の実現を目指す請負開発型のコンサルティングサービスです。AI、iPaaS、および先端の技術を駆使して、製造プロセスの効率化、業務効率化、チームワーク強化、コスト削減、品質向上を実現します。このサービスは、製造業の課題を深く理解し、それに対する最適なデジタルソリューションを提供することで、企業が持続的な成長とイノベーションを達成できるようサポートします。
オンライン講座
製造業、主に購買・調達部門にお勤めの方々に向けた情報を配信しております。
新任の方やベテランの方、管理職を対象とした幅広いコンテンツをご用意しております。
お問い合わせ
コストダウンが利益に直結する術だと理解していても、なかなか前に進めることができない状況。そんな時は、newjiのコストダウン自動化機能で大きく利益貢献しよう!
(Β版非公開)