- お役立ち記事
- Mastering Redundant Power Supply Design: Lessons from Japanese Manufacturing Prowess
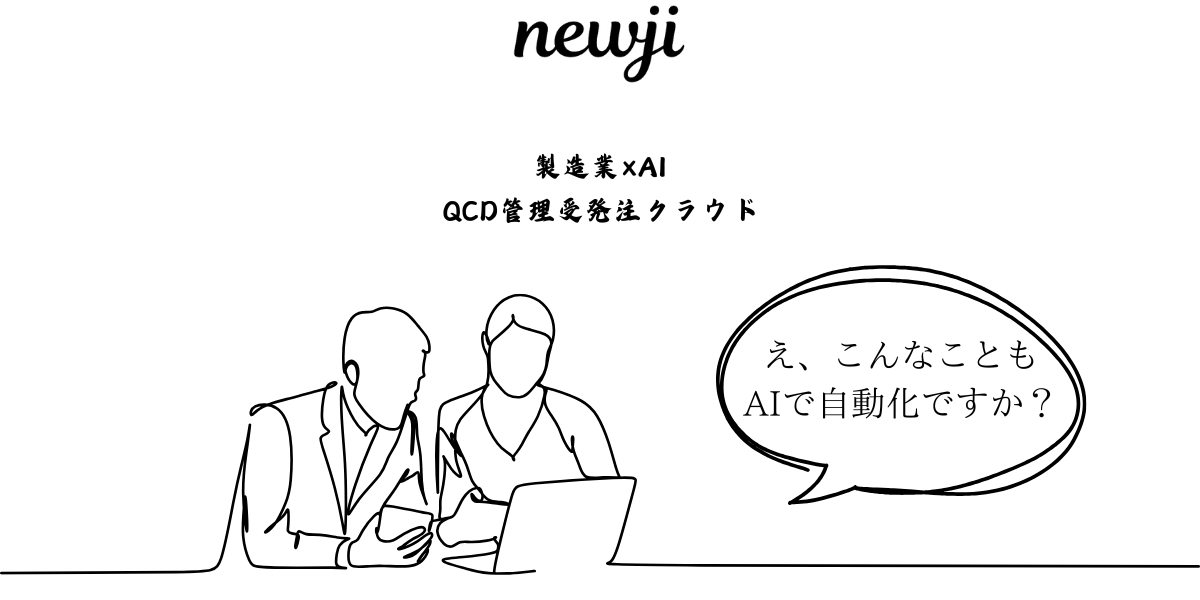
Mastering Redundant Power Supply Design: Lessons from Japanese Manufacturing Prowess
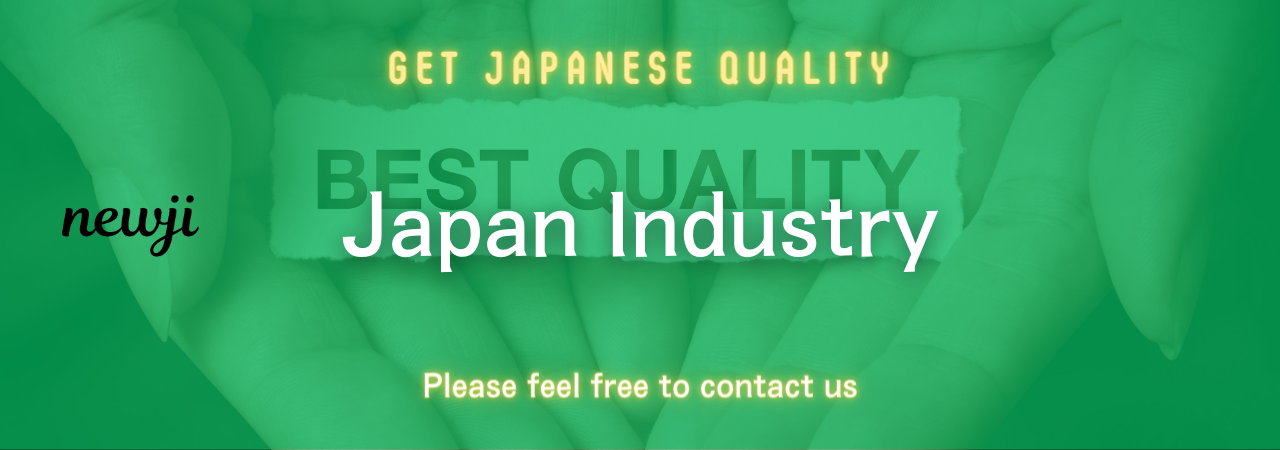
目次
Understanding Redundant Power Supply Design
Redundant power supply design is a critical aspect of ensuring the reliability and continuity of operations in various industries. By incorporating multiple power sources, systems can maintain functionality even in the event of a failure in one component. This approach is particularly vital in sectors where downtime can result in significant financial losses or safety hazards.
Redundant power systems are commonly implemented in data centers, manufacturing plants, healthcare facilities, and other environments where uninterrupted power is essential. The primary goal is to provide a seamless transition between power sources, minimizing the risk of operational disruptions.
The Japanese Manufacturing Approach to Redundant Power Supply
Japanese manufacturing has long been recognized for its precision, efficiency, and reliability. These principles extend to the design and implementation of redundant power supply systems. By leveraging advanced engineering practices and a culture of continuous improvement, Japanese manufacturers have developed robust power systems that serve as benchmarks in the industry.
One of the key aspects of the Japanese approach is the emphasis on quality control. Every component of the power supply system is meticulously tested to ensure it meets stringent performance standards. This attention to detail minimizes the likelihood of component failures and enhances the overall reliability of the system.
Lean Manufacturing and Redundancy
Lean manufacturing, a methodology pioneered in Japan, focuses on eliminating waste and optimizing processes. When applied to redundant power supply design, lean principles ensure that the system is both efficient and effective. By streamlining the design process and reducing unnecessary components, manufacturers can create power systems that are not only reliable but also cost-effective.
Kaizen and Continuous Improvement
The Kaizen philosophy, central to Japanese manufacturing, promotes continuous improvement in all aspects of production. In the context of power supply design, this means regularly evaluating and enhancing system performance. Through iterative testing and feedback, manufacturers can identify potential weaknesses and implement upgrades to bolster system reliability.
Advantages of Redundant Power Supply Systems
Implementing redundant power supply systems offers numerous benefits that contribute to the overall efficiency and resilience of an organization.
Enhanced Reliability
The primary advantage of redundant power systems is the increased reliability they provide. By having multiple power sources, organizations can ensure that operations continue smoothly even if one source fails. This redundancy is crucial for maintaining consistent performance and avoiding costly downtimes.
Improved Safety
In environments where power failures can pose safety risks, redundant systems offer an added layer of protection. For example, in healthcare facilities, uninterrupted power supply is critical for the operation of life-saving equipment. Redundant power systems help mitigate the risk of power outages, ensuring that essential services remain operational.
Scalability and Flexibility
Redundant power systems can be designed to accommodate future growth and changing needs. As organizations expand, additional power sources can be integrated seamlessly, allowing the system to scale without compromising reliability or performance.
Disadvantages of Redundant Power Supply Systems
While redundant power systems offer significant benefits, there are also some drawbacks to consider.
Increased Initial Costs
Implementing a redundant power supply system typically involves higher upfront costs compared to single-source systems. The need for additional components and more complex infrastructure can result in increased capital expenditure during the initial setup phase.
Higher Maintenance Requirements
With more components in the system, maintenance becomes more complex and time-consuming. Regular inspections and testing are necessary to ensure that all power sources are functioning correctly and are ready to take over in the event of a failure.
Space Constraints
Redundant power systems often require more physical space to accommodate the additional components. This can be a significant consideration in facilities where space is limited, necessitating careful planning and design to optimize the layout.
Supplier Negotiation Techniques for Redundant Power Systems
Effective supplier negotiation is essential for securing high-quality components at competitive prices. Drawing from Japanese manufacturing practices, several strategies can enhance negotiation outcomes.
Building Long-Term Relationships
Japanese manufacturers prioritize long-term partnerships with their suppliers. By fostering trust and mutual respect, organizations can negotiate better terms and ensure a steady supply of high-quality components. Building these relationships involves regular communication, collaboration on quality improvements, and shared commitment to excellence.
Emphasizing Quality and Reliability
When negotiating with suppliers, emphasizing the importance of quality and reliability can lead to more favorable agreements. Japanese suppliers are renowned for their meticulous attention to detail, and by highlighting these priorities, organizations can ensure they receive components that meet stringent performance standards.
Leveraging Bulk Purchasing
Purchasing components in bulk can provide significant cost advantages. Japanese manufacturers often engage in bulk buying to benefit from economies of scale, reducing the per-unit cost and securing better pricing terms from suppliers.
Market Conditions in Japanese Power Supply Components
Understanding the market conditions for power supply components in Japan is crucial for effective procurement and purchasing strategies.
Technological Advancements
Japan is at the forefront of technological innovation, particularly in the field of electronics and power systems. This leads to a dynamic market where suppliers continuously develop advanced components that offer improved performance and efficiency.
Competitive Landscape
The Japanese market is highly competitive, with numerous suppliers vying for market share. This competition drives suppliers to maintain high standards of quality and innovation, benefiting organizations seeking reliable power supply components.
Regulatory Environment
Japan has stringent regulations governing the manufacturing and quality standards of power supply components. Suppliers must comply with these regulations, ensuring that components meet strict safety and performance criteria. Organizations procuring these components can be confident in their reliability and compliance.
Best Practices in Procuring Redundant Power Supply Components from Japan
Adhering to best practices can enhance the efficiency and effectiveness of procuring redundant power supply components from Japanese suppliers.
Thorough Supplier Evaluation
Before establishing a partnership with a supplier, conduct a comprehensive evaluation of their capabilities, quality standards, and reliability. Assess their track record, certifications, and client testimonials to ensure they meet your organization’s requirements.
Clear Communication of Requirements
Clearly articulate your organization’s specific needs and expectations to potential suppliers. Providing detailed specifications and performance criteria helps suppliers understand your requirements and deliver components that meet your standards.
Collaborative Design Process
Engage in a collaborative design process with suppliers to ensure that power supply systems are tailored to your organization’s unique needs. This collaboration can lead to innovative solutions and optimized system performance.
Regular Performance Monitoring
Implement a robust performance monitoring system to track the reliability and efficiency of the power supply components. Regular monitoring helps identify potential issues early, allowing for timely maintenance and minimizing the risk of system failures.
Investing in Training and Development
Invest in training and development programs for your procurement and engineering teams. Enhancing their knowledge of Japanese manufacturing practices and power supply design can lead to more informed decision-making and improved system performance.
Integrating Japanese Manufacturing Techniques into Redundant Power Supply Design
Incorporating Japanese manufacturing techniques can significantly enhance the design and implementation of redundant power supply systems.
Precision Engineering
Japanese manufacturing is synonymous with precision engineering. Applying these principles to power supply design ensures that each component fits perfectly and functions optimally within the system. This precision minimizes the risk of failures and enhances overall system reliability.
Just-In-Time (JIT) Inventory Management
JIT inventory management, a hallmark of Japanese manufacturing, involves maintaining minimal inventory levels and receiving components only as needed. This approach reduces storage costs and minimizes the risk of excess inventory, which can lead to obsolete components.
Total Quality Management (TQM)
TQM is a comprehensive approach to quality management, emphasizing continuous improvement and customer satisfaction. By implementing TQM principles, organizations can ensure that every aspect of the power supply system meets the highest quality standards.
Case Studies: Success Stories from Japanese Manufacturing
Examining real-world examples of successful redundant power supply implementations in Japanese manufacturing provides valuable insights into best practices and effective strategies.
Case Study 1: Automotive Manufacturing Plant
An automotive manufacturing plant in Japan implemented a redundant power supply system to ensure uninterrupted production. By partnering with a local supplier renowned for their high-quality components, the plant achieved a 99.99% uptime. The implementation of precision engineering and regular performance monitoring contributed to the system’s reliability, resulting in increased production efficiency and reduced downtime.
Case Study 2: Data Center Operations
A leading data center operator in Japan adopted a redundant power supply design to maintain continuous server operations. Collaborating with suppliers specializing in advanced power systems, the data center achieved enhanced reliability and scalability. The incorporation of lean manufacturing principles and continuous improvement processes ensured that the power supply system remained efficient and adaptable to changing demands.
Case Study 3: Healthcare Facility
A major healthcare facility in Japan integrated a redundant power supply system to secure critical medical equipment. By leveraging Japanese suppliers’ expertise in quality control and reliability, the facility ensured that life-saving equipment remained operational during power outages. The successful implementation of the system improved patient safety and operational continuity.
Future Trends in Redundant Power Supply Design
The field of redundant power supply design is continually evolving, with emerging trends shaping the future of the industry.
Integration of Renewable Energy Sources
Incorporating renewable energy sources, such as solar and wind power, into redundant power supply systems is becoming increasingly popular. This integration enhances sustainability and reduces dependence on traditional energy sources, aligning with global efforts to promote environmental responsibility.
Advancements in Battery Technology
Advancements in battery technology, including higher energy densities and longer lifespans, are revolutionizing redundant power supply systems. Improved batteries offer more reliable backup power, enhancing system resilience and reducing maintenance requirements.
Smart Power Management Systems
The development of smart power management systems allows for more efficient monitoring and control of power supply components. These systems use advanced algorithms and real-time data to optimize power distribution, detect potential issues, and automate maintenance processes.
Internet of Things (IoT) Integration
Integrating IoT technologies into redundant power supply systems enables greater connectivity and data sharing. IoT-enabled components can communicate seamlessly, providing valuable insights into system performance and facilitating predictive maintenance.
Conclusion
Mastering redundant power supply design is essential for ensuring the reliability and continuity of operations across various industries. By drawing lessons from Japanese manufacturing prowess, organizations can implement robust and efficient power systems that withstand unforeseen challenges.
The Japanese approach, characterized by precision engineering, lean manufacturing, and continuous improvement, offers valuable strategies for enhancing the design and implementation of redundant power supply systems. By focusing on quality, building strong supplier relationships, and adhering to best practices, organizations can achieve greater system reliability and operational excellence.
As the industry continues to evolve, embracing emerging trends such as renewable energy integration, advancements in battery technology, and smart power management systems will further enhance the effectiveness of redundant power supply designs. By staying informed and adaptable, organizations can ensure that their power systems remain resilient and capable of supporting their long-term goals.
Investing in the principles and practices exemplified by Japanese manufacturing not only strengthens the reliability of power supply systems but also contributes to overall operational efficiency and sustainability. As organizations navigate the complexities of modern power demands, leveraging these insights will be instrumental in achieving success and maintaining a competitive edge in the global market.
資料ダウンロード
QCD調達購買管理クラウド「newji」は、調達購買部門で必要なQCD管理全てを備えた、現場特化型兼クラウド型の今世紀最高の購買管理システムとなります。
ユーザー登録
調達購買業務の効率化だけでなく、システムを導入することで、コスト削減や製品・資材のステータス可視化のほか、属人化していた購買情報の共有化による内部不正防止や統制にも役立ちます。
NEWJI DX
製造業に特化したデジタルトランスフォーメーション(DX)の実現を目指す請負開発型のコンサルティングサービスです。AI、iPaaS、および先端の技術を駆使して、製造プロセスの効率化、業務効率化、チームワーク強化、コスト削減、品質向上を実現します。このサービスは、製造業の課題を深く理解し、それに対する最適なデジタルソリューションを提供することで、企業が持続的な成長とイノベーションを達成できるようサポートします。
オンライン講座
製造業、主に購買・調達部門にお勤めの方々に向けた情報を配信しております。
新任の方やベテランの方、管理職を対象とした幅広いコンテンツをご用意しております。
お問い合わせ
コストダウンが利益に直結する術だと理解していても、なかなか前に進めることができない状況。そんな時は、newjiのコストダウン自動化機能で大きく利益貢献しよう!
(Β版非公開)