- お役立ち記事
- Mastering the Art of Japanese Etching: Techniques and Innovations in Modern Manufacturing
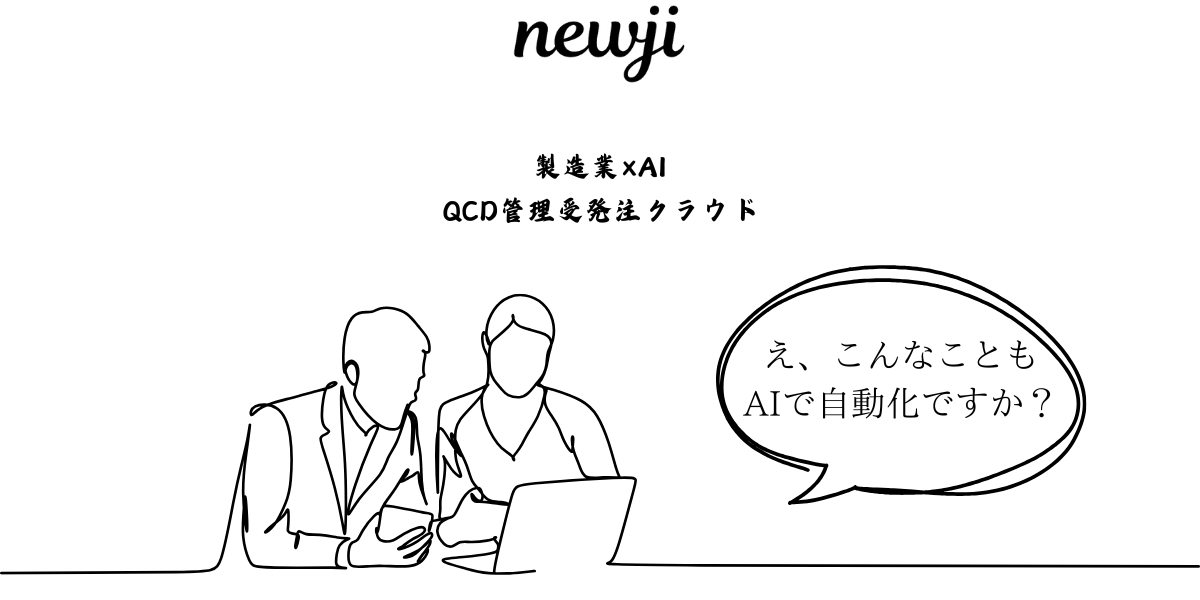
Mastering the Art of Japanese Etching: Techniques and Innovations in Modern Manufacturing
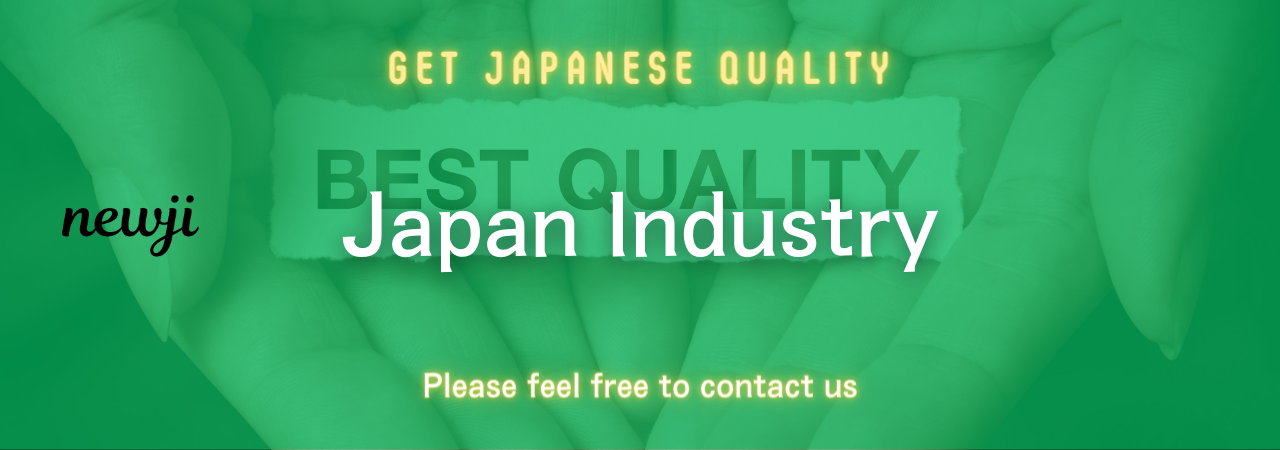
目次
Introduction to Japanese Etching
Japanese etching has a storied history, rooted in centuries-old traditions and refined through modern innovations.
Known for its meticulous craftsmanship and unparalleled detail, etching in Japan has evolved to encompass modern manufacturing techniques.
Incorporating both traditional methods and state-of-the-art technological advancements, Japanese manufacturers continue to set the benchmark for precision and quality in etching.
The Origins of Japanese Etching
The roots of Japanese etching can be traced back to the Edo period, where intricate designs were crafted using manual techniques.
These designs often adorned metal surfaces, woodblocks, and other materials and were intricately detailed, reflecting a deep understanding of both art and precision.
Over centuries, this craft has been honed and adapted to meet the demands of various industries, from decorative arts to high-tech sectors.
Modern Innovations in Japanese Etching
Japan is renowned for marrying tradition with innovation.
This dual approach is evident in the etching processes used today, which incorporate cutting-edge technology without sacrificing craftsmanship.
Laser Etching
One of the significant advancements is laser etching.
Using high-powered lasers, manufacturers can achieve extraordinary precision, even on the most delicate materials.
This method reduces the risk of damage and ensures a consistent quality across all outputs, making it perfect for high-volume production.
Electrical Discharge Machining (EDM)
Another groundbreaking technology is Electrical Discharge Machining (EDM).
This non-contact method employs electrical discharges to etch fine details into conductive materials.
It is particularly useful for creating complex geometries and is widely used in aerospace and medical device manufacturing.
Photoresist Etching
Photoresist techniques have also seen significant advancements.
Utilizing UV light and chemical processes, this method allows for detailed and highly accurate designs to be transferred onto various substrates.
It is especially prevalent in the production of electronic components, such as printed circuit boards (PCBs).
Practical Applications in Manufacturing
Japanese etching techniques are not just confined to artistic pursuits but extend to a variety of manufacturing applications.
These methods are integral to producing high-precision components critical to sectors such as automotive, electronics, and aerospace.
Automotive Industry
In the automotive industry, etching is used to create components that require high-tolerance finishes.
From intricate dashboard designs to essential engine parts, etching ensures durability and precision, contributing to the overall performance and aesthetic appeal of vehicles.
Electronics
In electronics, miniaturization is key.
Japanese etching techniques are crucial for producing micro-scale components, such as semiconductors and microprocessors.
The precision required in these components is immense, and Japanese etching methods provide the necessary accuracy.
Aerospace
Aerospace applications demand components that can withstand extreme conditions.
Etched parts, thanks to their fine tolerances and reliable performance, are indispensable in the manufacturing of aircraft and spacecraft.
Advantages of Japanese Etching
Japanese etching techniques offer several advantages, making them highly sought after in manufacturing sectors worldwide.
Precision and Accuracy
One of the hallmarks of Japanese etching is its unparalleled precision.
Whether using traditional handcrafted methods or modern laser technology, the outcome is consistently accurate and finely detailed.
Quality Control
Quality control is deeply embedded in Japanese manufacturing culture.
Stringent checks and balances ensure that each piece meets the highest standards, reducing the likelihood of defects and ensuring customer satisfaction.
Versatility
From metal to plastic, the versatility of Japanese etching methods is remarkable.
They can be applied to a vast range of materials, making them adaptable to different industry needs.
Challenges and Disadvantages
While Japanese etching offers many benefits, there are challenges and disadvantages to consider.
Cost
High precision and quality come at a cost.
Japanese etching techniques, especially when using advanced technology, can be more expensive than other methods.
This can be a barrier for smaller companies or those with limited budgets.
Time-Consuming
Achieving the level of detail and accuracy that Japanese etching is known for can be time-consuming.
This can lead to longer lead times, which may not be suitable for industries requiring rapid turnaround.
Complexity
The complexity associated with some Japanese etching techniques requires specialized knowledge and expertise.
Training and maintaining a skilled workforce can be challenging, particularly in regions outside Japan.
Supplier Negotiation Techniques
Dealing with Japanese suppliers requires a specific approach, respecting cultural nuances and business practices.
Building Relationships
In Japanese business culture, relationships matter.
Long-term partnerships are favored over short-term gains.
Invest time in building trust and understanding with your Japanese suppliers.
Clear Communication
Clear and precise communication is critical.
Ensure that expectations, specifications, and terms are clearly articulated and understood by both parties.
Using detailed contracts can help avoid misunderstandings.
Respect and Professionalism
Respect and professionalism are ingrained in Japanese business interactions.
Adhering to these values can foster a positive and productive partnership.
Market Conditions and Trends
Understanding the current market conditions and trends in Japanese etching can help businesses make informed decisions.
Technological Advancements
Japan continues to be at the forefront of technological advancements in etching, with ongoing research and development.
Staying updated with these innovations can provide a competitive edge.
Global Demand
The global demand for precision and high-quality components is on the rise, benefiting Japanese etching industry.
This trend is expected to continue, driven by advancements in various sectors like electronics, automotive, and aerospace.
Sustainability
There is a growing emphasis on sustainability in manufacturing.
Japanese etching methods are increasingly incorporating eco-friendly practices, such as reducing waste and using non-toxic chemicals.
Best Practices in Procurement and Purchasing
For companies looking to procure etched components from Japanese suppliers, following best practices can lead to successful outcomes.
Supplier Research
Conduct thorough research to identify reputable suppliers with a track record of quality and reliability.
Supplier directories, industry reports, and networking events can be valuable resources.
Quality Assurance
Establish robust quality assurance processes to ensure that the components meet your specifications.
Consider conducting on-site visits and audits to assess the supplier’s capabilities.
Negotiation Strategies
Apply effective negotiation strategies, balancing cost efficiency with quality.
Being flexible and open to discussions can lead to mutually beneficial agreements.
Conclusion
Mastering the art of Japanese etching requires a deep understanding of both traditional techniques and modern innovations.
By leveraging these methods in manufacturing, businesses can achieve exceptional precision and quality, setting themselves apart in the competitive landscape.
With careful consideration of market trends, supplier relationships, and best practices in procurement, companies can fully harness the benefits of Japanese etching.
The legacy of craftsmanship combined with cutting-edge technology ensures that Japanese etching will continue to play a critical role in global manufacturing for years to come.
資料ダウンロード
QCD調達購買管理クラウド「newji」は、調達購買部門で必要なQCD管理全てを備えた、現場特化型兼クラウド型の今世紀最高の購買管理システムとなります。
ユーザー登録
調達購買業務の効率化だけでなく、システムを導入することで、コスト削減や製品・資材のステータス可視化のほか、属人化していた購買情報の共有化による内部不正防止や統制にも役立ちます。
NEWJI DX
製造業に特化したデジタルトランスフォーメーション(DX)の実現を目指す請負開発型のコンサルティングサービスです。AI、iPaaS、および先端の技術を駆使して、製造プロセスの効率化、業務効率化、チームワーク強化、コスト削減、品質向上を実現します。このサービスは、製造業の課題を深く理解し、それに対する最適なデジタルソリューションを提供することで、企業が持続的な成長とイノベーションを達成できるようサポートします。
オンライン講座
製造業、主に購買・調達部門にお勤めの方々に向けた情報を配信しております。
新任の方やベテランの方、管理職を対象とした幅広いコンテンツをご用意しております。
お問い合わせ
コストダウンが利益に直結する術だと理解していても、なかなか前に進めることができない状況。そんな時は、newjiのコストダウン自動化機能で大きく利益貢献しよう!
(Β版非公開)