- お役立ち記事
- Material sample management for process improvement Points that purchasing personnel should keep in mind
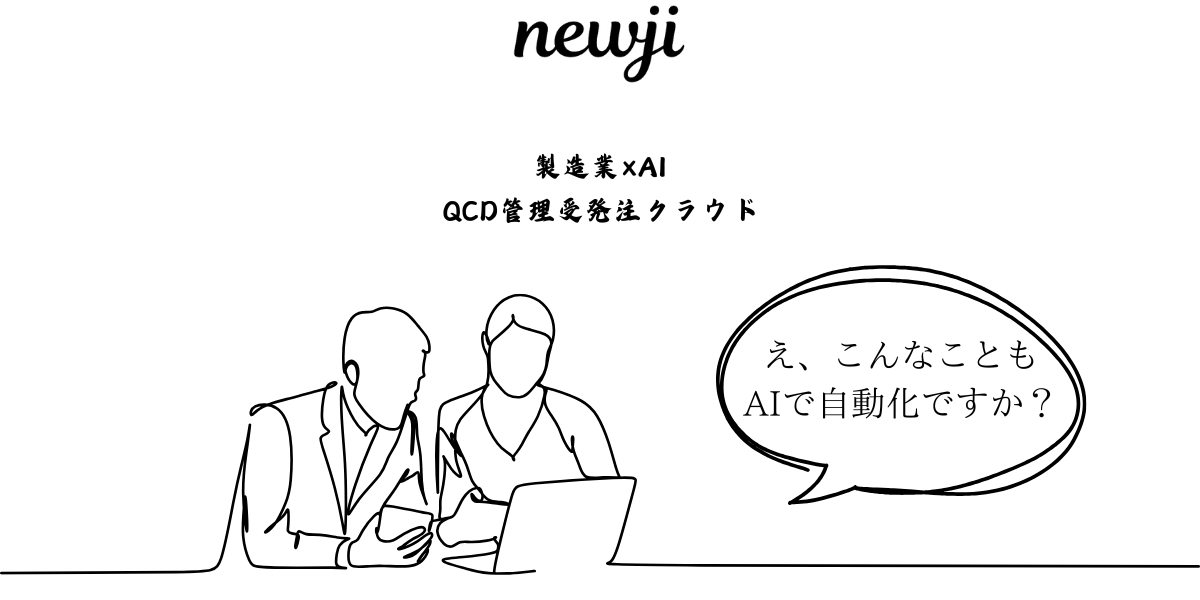
Material sample management for process improvement Points that purchasing personnel should keep in mind
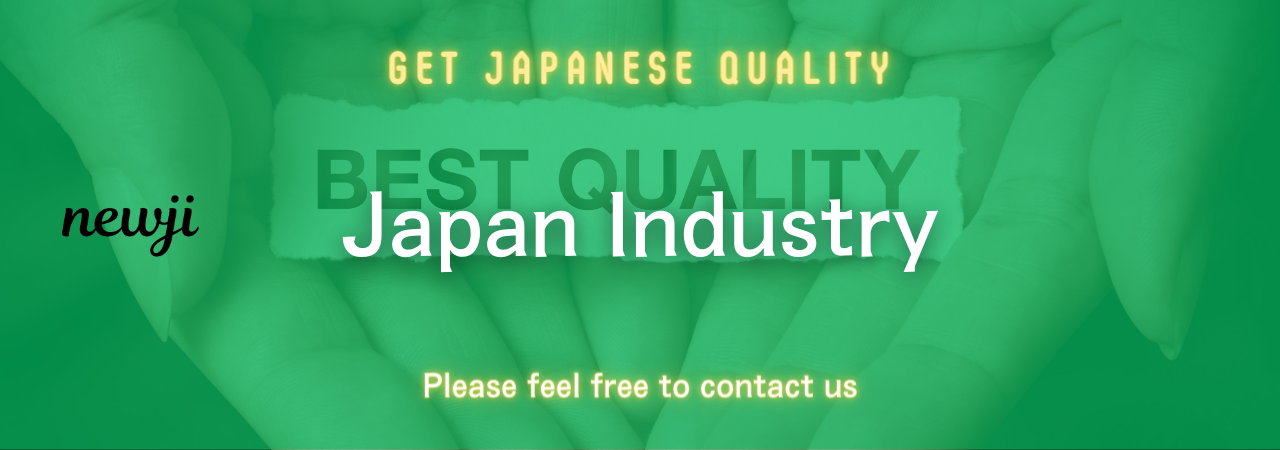
目次
Understanding Material Sample Management
Material sample management is a crucial aspect of process improvement in any manufacturing or production facility.
It involves the thorough organization, tracking, and evaluation of material samples used during the production process.
By managing samples effectively, businesses can ensure quality, optimize supply chains, and reduce costs.
For purchasing personnel, understanding and implementing efficient sample management is vital for improving overall operational efficiency.
The Importance of Sample Management
In any production environment, materials play a significant role in determining the final product’s quality.
Proper sample management allows companies to test and validate these materials thoroughly before committing to large-scale production.
This process reduces the risk of defects and ensures that the materials meet necessary quality standards.
Moreover, effective sample management provides valuable insights into supplier performance and material consistency.
These insights allow purchasing personnel to make informed decisions when sourcing materials.
By keeping track of sample data, companies can identify trends, monitor supplier reliability, and minimize the risk of costly production delays.
Key Points for Purchasing Personnel
1. Establish Clear Procedures
For efficient material sample management, it’s essential to establish clear, standardized procedures for handling samples.
This includes setting guidelines for the collection, storage, and testing of materials.
These procedures help maintain consistency and reliability, making it easier to compare samples over time.
Purchasing personnel should work closely with quality assurance teams to develop these procedures, ensuring they align with both organizational goals and regulatory requirements.
2. Use a Centralized System
A centralized data management system is crucial for effective sample management.
This system should allow easy access to sample data and facilitate accurate tracking throughout the entire lifecycle of a sample.
By using a centralized system, purchasing personnel can quickly assess supplier performance and material quality.
This level of transparency ensures that all stakeholders have access to up-to-date information and can make data-driven decisions.
3. Collaborate with Suppliers
Maintaining good relationships with suppliers is a critical component of effective sample management.
Purchasing personnel should engage in regular communication with suppliers to discuss material specifications, performance expectations, and any issues that may arise during the sampling process.
Collaboration is key to resolving discrepancies swiftly and ensuring that materials meet both company and industry standards.
By fostering a cooperative relationship, purchasing teams can also negotiate better terms and secure consistent material supplies.
4. Prioritize Quality Control
Quality control is an integral part of material sample management.
It is imperative to implement robust quality control measures to test and evaluate material samples thoroughly.
Purchasing personnel should ensure that samples undergo rigorous testing protocols, including physical and chemical analyses, to verify their suitability for production use.
A strong focus on quality control helps identify potential issues early, preventing them from escalating into costly production problems.
5. Document and Analyze Results
Meticulous documentation of sample test results is vital for process improvement.
Purchasing personnel should maintain detailed records of all sample tests, including dates, materials tested, test results, and any corrective actions taken.
Documenting these results allows for easy reference and helps identify patterns or issues with specific suppliers or materials.
This analytical approach aids in making informed purchasing decisions and enhances the organization’s ability to implement continuous process improvements.
6. Embrace Technology
In today’s digital age, technology plays an essential role in material sample management.
Software solutions specifically designed for sample management can streamline the entire process, from sample collection to analysis.
These tools offer enhanced features such as automated data entry, real-time tracking, and powerful analytics capabilities.
Purchasing personnel should embrace these technological innovations to improve efficiency and accuracy.
Challenges in Material Sample Management
Though effective sample management is essential, it does come with its set of challenges.
These challenges can include issues such as inconsistent sampling methods, human error during data entry, or a lack of standardized testing procedures.
Purchasing personnel must be diligent in addressing these challenges by implementing robust systems, providing staff training, and ensuring continuous process evaluation and improvement.
Benefits of Effective Sample Management
Successfully managing material samples brings numerous benefits to an organization.
These benefits include improved product quality, reduced production costs, and optimized supply chain management.
By ensuring quality materials are used, companies can maintain high production standards and minimize waste.
Effectively managed samples also lead to better supplier relationships, which can result in more favorable contracts and consistent material availability.
Ultimately, by focusing on sample management, purchasing personnel contribute significantly to the overall process improvement and operational success of their organizations.
Conclusion
Material sample management is a vital component of process improvement for any production facility.
For purchasing personnel, understanding the principles of sample management and implementing effective strategies is essential.
By prioritizing quality, establishing clear procedures, and leveraging technology, purchasing teams can streamline operations and drive continuous improvement.
The benefits of well-executed sample management extend beyond immediate cost savings and quality assurance, contributing to long-term organizational success and sustainability.
資料ダウンロード
QCD調達購買管理クラウド「newji」は、調達購買部門で必要なQCD管理全てを備えた、現場特化型兼クラウド型の今世紀最高の購買管理システムとなります。
ユーザー登録
調達購買業務の効率化だけでなく、システムを導入することで、コスト削減や製品・資材のステータス可視化のほか、属人化していた購買情報の共有化による内部不正防止や統制にも役立ちます。
NEWJI DX
製造業に特化したデジタルトランスフォーメーション(DX)の実現を目指す請負開発型のコンサルティングサービスです。AI、iPaaS、および先端の技術を駆使して、製造プロセスの効率化、業務効率化、チームワーク強化、コスト削減、品質向上を実現します。このサービスは、製造業の課題を深く理解し、それに対する最適なデジタルソリューションを提供することで、企業が持続的な成長とイノベーションを達成できるようサポートします。
オンライン講座
製造業、主に購買・調達部門にお勤めの方々に向けた情報を配信しております。
新任の方やベテランの方、管理職を対象とした幅広いコンテンツをご用意しております。
お問い合わせ
コストダウンが利益に直結する術だと理解していても、なかなか前に進めることができない状況。そんな時は、newjiのコストダウン自動化機能で大きく利益貢献しよう!
(Β版非公開)