- お役立ち記事
- Material Selection and Optimization in Extrusion Molding: A Guide for Quality Improvement
Material Selection and Optimization in Extrusion Molding: A Guide for Quality Improvement
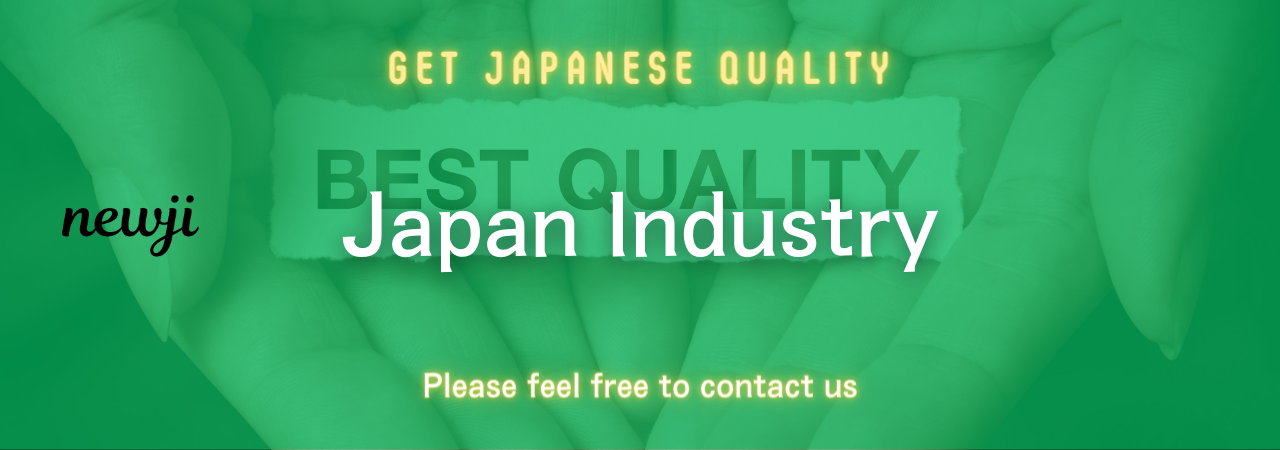
Extrusion molding is a critical process in manufacturing, used to create a wide variety of products by forcing material through a shaped die to produce long and continuous shapes.
Selecting the right material and optimizing the process are essential to ensure high-quality outcomes.
This guide will walk you through the important considerations for material selection and process optimization in extrusion molding.
目次
Understanding Extrusion Molding
Extrusion molding involves pushing material, often plastic, metal, or rubber, through a die to create objects of uniform cross-sectional shapes like pipes, tubes, sheets, and profiles.
The process relies heavily on the characteristics of the selected material and the efficiency of the equipment used.
Material Selection: Key Factors to Consider
Choosing the right material for extrusion molding is crucial for achieving the desired product quality.
Here are several key factors to keep in mind:
Mechanical Properties
When selecting materials, consider their tensile strength, flexibility, hardness, and impact resistance.
These properties will affect the durability and functionality of the final product.
Chemical Compatibility
It’s essential to ensure that the material is resistant to chemicals it might encounter during use.
For instance, if the final product will be exposed to harsh chemicals, choosing a material that can withstand corrosion is vital.
Thermal Stability
The material should tolerate the temperatures involved in the extrusion process without degrading.
Thermoplastic and thermosetting materials often offer different degrees of thermal stability, influencing your choice based on process requirements.
Cost and Availability
Balancing quality with cost is an ongoing challenge.
It’s important to select materials that are cost-effective yet do not compromise the product’s performance.
Additionally, ensure the material is readily available to avoid disruptions in the manufacturing process.
Optimizing the Extrusion Process
Once the material is chosen, optimizing the extrusion process is the next step.
Several aspects require attention to ensure efficiency and high-quality products.
Die Design
Die design directly impacts the product’s shape and dimensions.
Investing in precision die manufacturing and regular maintenance will help in getting a smoother and more precise output.
Temperature Control
Maintaining an appropriate temperature profile along the extrusion line is crucial.
Too high or too low temperatures can compromise material properties, causing defects such as warping or melting inconsistencies.
Screw Design
The design of the screw in the extrusion machine can greatly affect the material flow and mixing.
Optimizing screw geometry, including the length-to-diameter ratio and pitch, can lead to better material homogeneity and smoother extrusion.
Cooling System
Effective cooling ensures the extruded product retains its shape as it solidifies.
Inadequate cooling can lead to deformation, so optimize the cooling rate and use appropriate cooling methods, such as air, water, or rollers.
Speed Regulation
The extrusion speed must be closely monitored and adjusted.
Too fast can result in poor material quality, while too slow can cause inefficiencies and increase production time.
Balanced speed ensures a consistent and high-quality output.
Common Challenges and Solutions
Extrusion molding comes with its set of challenges.
Knowing how to address them can significantly improve the quality and efficiency of the process.
Melt Fracture
Melt fracture occurs when the material surface becomes rough and irregular during extrusion.
This issue can be resolved by optimizing the die design, reducing extrusion speed, and controlling temperature more effectively.
Die Lines
Die lines are marks left on the product due to imperfections in the die.
Regular die maintenance and polishing can help minimize these marks, improving the product’s surface finish.
Bubble Formation
Entrapped air or gas can form bubbles in the extruded material.
To prevent this, ensure proper drying of materials before extrusion and optimize the vacuum venting in the extrusion machinery.
Inconsistent Thickness
Variations in product thickness can arise from uneven material flow or cooling inconsistencies.
Addressing these issues involves careful monitoring of screw speed, die design, and cooling systems.
Quality Control and Testing
Implementing stringent quality control measures is essential for maintaining high standards in extrusion molding.
In-line Inspection
Utilize in-line inspection tools such as laser measurement systems and camera-based monitoring to detect defects early and ensure consistent product dimensions.
Material Testing
Regularly test raw materials for properties like moisture content, melt flow index, and tensile strength.
This helps in selecting the right batches of materials for the extrusion process.
Product Testing
Conduct thorough testing of the final product, including physical, chemical, and mechanical properties.
Tests like tensile testing, impact resistance, and chemical resistance help ensure that the product meets the desired quality standards.
Environmental and Safety Considerations
Adhering to environmental and safety regulations is crucial in extrusion molding processes.
Energy Efficiency
Optimize machinery for energy efficiency to reduce production costs and environmental impact.
Consider using energy-efficient motors and heaters, and implement waste heat recovery systems.
Waste Management
Implement a robust plan for managing waste materials and by-products.
Recycling and reusing scrap materials in the extrusion process can significantly reduce waste.
Worker Safety
Ensure all safety protocols are in place for workers operating extrusion machinery.
Regular training, proper protective equipment, and emergency protocols are essential to maintain a safe working environment.
In conclusion, material selection and process optimization are vital components for enhancing the quality of products produced through extrusion molding.
By understanding the key factors involved and addressing common challenges, manufacturers can achieve superior results, ensuring efficiency, cost-effectiveness, and high standards.
資料ダウンロード
QCD調達購買管理クラウド「newji」は、調達購買部門で必要なQCD管理全てを備えた、現場特化型兼クラウド型の今世紀最高の購買管理システムとなります。
ユーザー登録
調達購買業務の効率化だけでなく、システムを導入することで、コスト削減や製品・資材のステータス可視化のほか、属人化していた購買情報の共有化による内部不正防止や統制にも役立ちます。
NEWJI DX
製造業に特化したデジタルトランスフォーメーション(DX)の実現を目指す請負開発型のコンサルティングサービスです。AI、iPaaS、および先端の技術を駆使して、製造プロセスの効率化、業務効率化、チームワーク強化、コスト削減、品質向上を実現します。このサービスは、製造業の課題を深く理解し、それに対する最適なデジタルソリューションを提供することで、企業が持続的な成長とイノベーションを達成できるようサポートします。
オンライン講座
製造業、主に購買・調達部門にお勤めの方々に向けた情報を配信しております。
新任の方やベテランの方、管理職を対象とした幅広いコンテンツをご用意しております。
お問い合わせ
コストダウンが利益に直結する術だと理解していても、なかなか前に進めることができない状況。そんな時は、newjiのコストダウン自動化機能で大きく利益貢献しよう!
(Β版非公開)