- お役立ち記事
- Material Selection and Optimization in Extrusion Molding: A Guide to Improving Quality
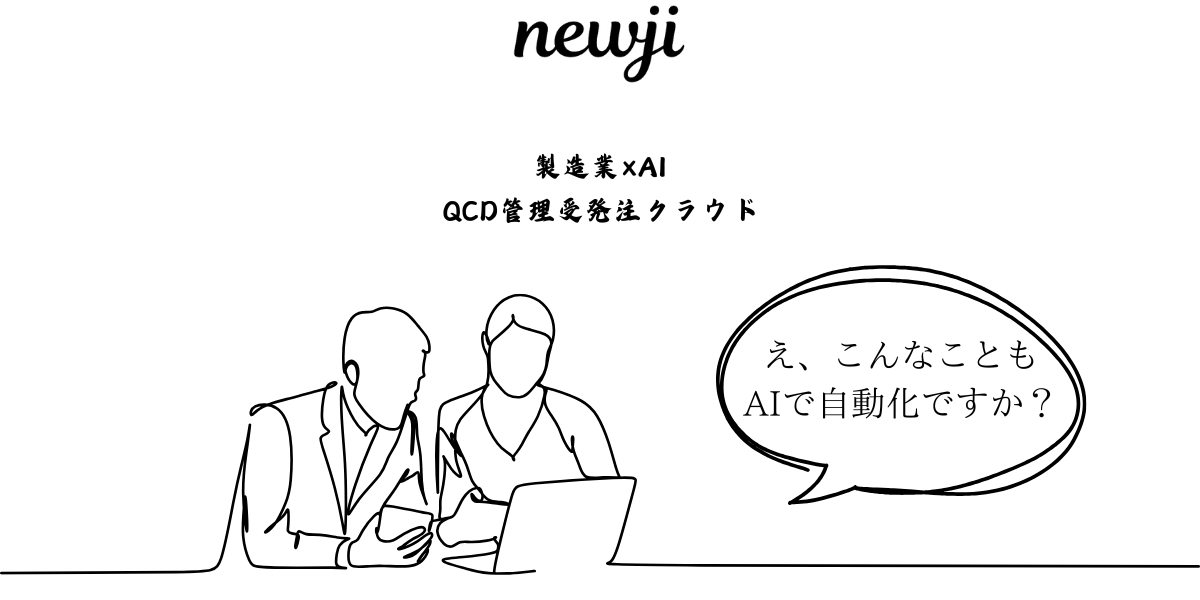
Material Selection and Optimization in Extrusion Molding: A Guide to Improving Quality
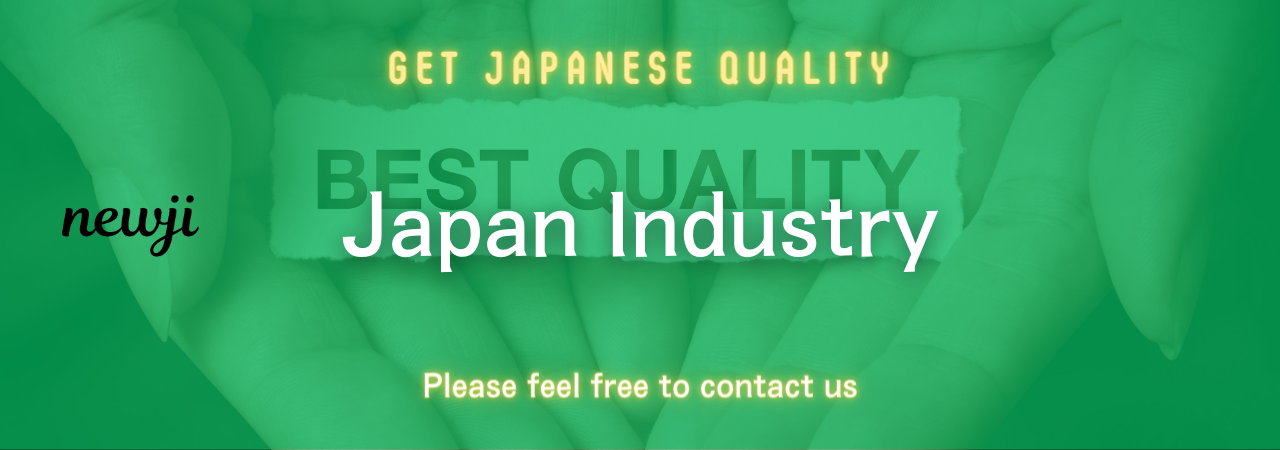
Extrusion molding is a widely used manufacturing process where materials, often polymers, are pushed through a die to create objects of a fixed cross-sectional profile.
This method is popular due to its efficiency and cost-effectiveness.
However, the quality of the final product depends significantly on the materials chosen and the optimization of the process parameters.
目次
Understanding Extrusion Molding
Extrusion molding begins with raw materials, such as plastic pellets or granules, being fed into a hopper.
These pellets then travel through a heated barrel, where they are melted and homogenized.
Once in a molten state, the material is forced through a die to shape it into the desired profile.
Cooling and solidification occur after the die, producing the final product.
Material Selection: The Foundation of Quality
Choosing the right material is crucial for producing high-quality extruded products.
Various factors, including mechanical properties, thermal stability, and compatibility with the extrusion process, must be considered.
Thermoplastics: A Popular Choice
Thermoplastics are commonly used in extrusion molding due to their ability to be melted and re-melted multiple times without significant degradation.
Common thermoplastics used in extrusion include polyethylene (PE), polyvinyl chloride (PVC), and polystyrene (PS).
Polyethylene (PE)
Polyethylene is a versatile material with excellent chemical resistance and low friction.
It is widely used in applications such as pipes, films, and tubing.
The low melting point of PE makes it easy to process, but attention must be given to the cooling rates to avoid warping.
Polyvinyl Chloride (PVC)
PVC is known for its durability and rigidity.
It is commonly used for pipes, window frames, and cable insulation.
However, processing PVC requires stabilizers to prevent degradation at high temperatures.
Thus, selecting appropriate additives is essential for maintaining material integrity during extrusion.
Polystyrene (PS)
Polystyrene is a moderate-cost material with good clarity and rigidity.
It is often used in packaging, disposable utensils, and other consumer goods.
During extrusion, the material’s flow properties must be carefully managed to avoid surface imperfections and ensure uniform thickness.
Process Parameters: Fine-Tuning for Excellence
Optimizing extrusion molding parameters is as critical as selecting the right material.
Key variables include temperature, pressure, and screw speed.
Fine-tuning these parameters can significantly enhance the quality of the extruded product.
Temperature Control
Maintaining proper temperature across the barrel zones is vital.
Each material has an optimal temperature range for processing.
For example, polyethylene typically melts around 130°C to 160°C, while PVC requires a higher range of 160°C to 190°C.
Die Temperature
The temperature of the die also plays a crucial role.
Too low, and the material may not flow smoothly, resulting in a rough surface texture.
Too high, and there could be issues with degradation or excessive melt.
Ensuring a uniform temperature across the die improves product consistency and surface finish.
Pressure Regulation
Extrusion pressure impacts the material flow and end product quality.
High pressure can lead to overheating and degradation, while low pressure may result in incomplete filling of the die.
Monitoring and adjusting pressure helps in achieving the desired shape and avoiding defects.
Screw Speed
The speed at which the screw rotates should be optimized to balance the flow rate and residence time of the material.
Too slow, and the production rate drops.
Too fast, and there may be issues with shear heating or incomplete melting.
Finding the right screw speed is essential for efficient and high-quality extrusion.
Additives: Enhancing Performance
Certain additives can be incorporated into the base material to improve its properties.
Additives such as stabilizers, plasticizers, and colorants can enhance durability, flexibility, and aesthetic appeal.
Stabilizers
Stabilizers are critical for materials like PVC, which can degrade when exposed to high heat during extrusion.
They help in maintaining polymer stability and longevity.
Plasticizers
Plasticizers are added to improve the flexibility and workability of certain polymers.
They are particularly useful for applications where the material needs to bend or flex without breaking.
Colorants
Colorants provide visual appeal and can be introduced into the material during the extrusion process.
They must be compatible with the base polymer to ensure smooth integration and consistent coloration.
Quality Control: Ensuring Excellence
Maintaining high quality in extrusion molding involves consistent monitoring and control of both materials and processes.
Regular inspection and testing are essential to identify any deviations early and implement corrective actions.
Dimensional Testing
Checking the dimensions of the extruded product ensures it meets the specified tolerances.
Tools like calipers, micrometers, and optical measurement systems can be used for precise measurements.
Surface Quality Inspection
Surface quality is vital for many extruded products.
Visual inspection and surface roughness testing can detect imperfections like scratches, pits, or uneven textures.
Physical Property Testing
Physical properties such as tensile strength, impact resistance, and hardness are crucial for performance.
Testing these properties regularly helps in maintaining product quality and functionality.
Conclusion
Material selection and process optimization are fundamental to achieving high-quality extrusion molding products.
By understanding the properties of different materials and fine-tuning the extrusion parameters, manufacturers can produce consistent and superior products.
Regular quality control further ensures that the final product meets or exceeds the required standards.
Through diligent attention to these factors, the extrusion molding process can achieve remarkable efficiency and reliability.
資料ダウンロード
QCD調達購買管理クラウド「newji」は、調達購買部門で必要なQCD管理全てを備えた、現場特化型兼クラウド型の今世紀最高の購買管理システムとなります。
ユーザー登録
調達購買業務の効率化だけでなく、システムを導入することで、コスト削減や製品・資材のステータス可視化のほか、属人化していた購買情報の共有化による内部不正防止や統制にも役立ちます。
NEWJI DX
製造業に特化したデジタルトランスフォーメーション(DX)の実現を目指す請負開発型のコンサルティングサービスです。AI、iPaaS、および先端の技術を駆使して、製造プロセスの効率化、業務効率化、チームワーク強化、コスト削減、品質向上を実現します。このサービスは、製造業の課題を深く理解し、それに対する最適なデジタルソリューションを提供することで、企業が持続的な成長とイノベーションを達成できるようサポートします。
オンライン講座
製造業、主に購買・調達部門にお勤めの方々に向けた情報を配信しております。
新任の方やベテランの方、管理職を対象とした幅広いコンテンツをご用意しております。
お問い合わせ
コストダウンが利益に直結する術だと理解していても、なかなか前に進めることができない状況。そんな時は、newjiのコストダウン自動化機能で大きく利益貢献しよう!
(Β版非公開)