- お役立ち記事
- Measuring the Effectiveness of QFD in Manufacturing: How to Maximize Results
Measuring the Effectiveness of QFD in Manufacturing: How to Maximize Results
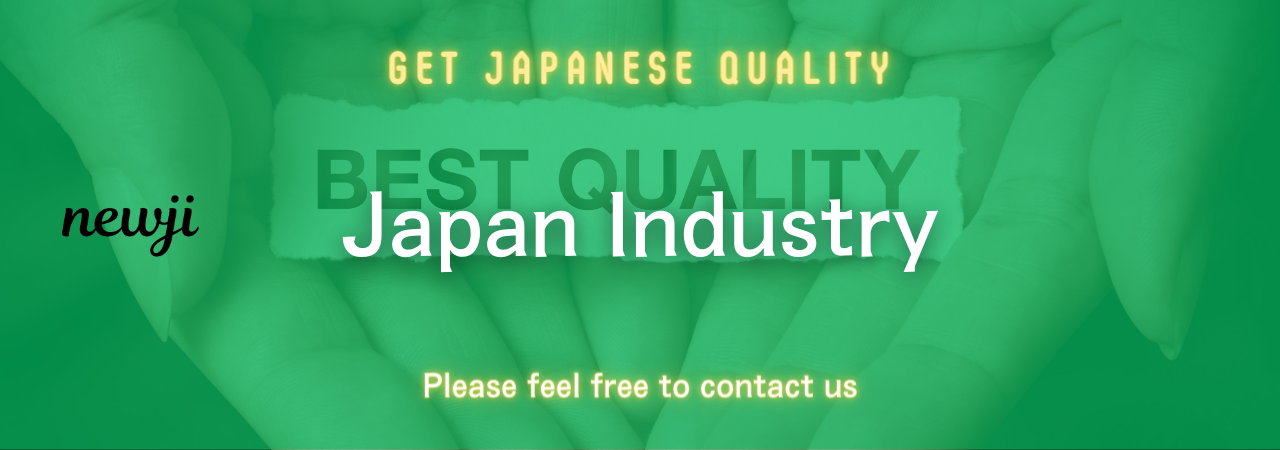
When it comes to manufacturing, ensuring that customer requirements are met is crucial. One way to achieve this is through Quality Function Deployment (QFD), a structured method for translating customer needs into specific engineering and operational requirements. But how effective is QFD in improving manufacturing processes, and how can you maximize its benefits? Let’s explore this in detail.
目次
What is Quality Function Deployment (QFD)?
Quality Function Deployment (QFD) originated in Japan and has become an essential tool for many manufacturing organizations. QFD helps companies prioritize customer requirements and incorporate them into the product design and development process. By using a series of matrices, often referred to as “House of Quality,” QFD aligns different functional areas within an organization, such as marketing, engineering, and production, ensuring everyone is working toward the same goals.
The Primary Components of QFD
QFD generally involves four main phases:
1. Product Planning: This phase identifies customer needs and translates them into technical requirements.
2. Product Design: In this phase, companies design the product features that meet those technical requirements.
3. Process Planning: Here, the focus is on setting up the manufacturing process to produce the product efficiently.
4. Production Planning: The final phase involves planning for the actual production, focusing on quality control and continuous improvement.
Measuring Effectiveness of QFD
To determine how effective QFD is in manufacturing, companies usually measure its impact on a few key performance indicators (KPIs). These KPIs include customer satisfaction, product quality, and production efficiency. Let’s delve into each of these categories.
Customer Satisfaction
QFD is designed to ensure that customer needs are addressed right from the initial planning stages. This leads to higher customer satisfaction levels. Surveys and feedback forms can be effective tools for measuring the change in customer satisfaction before and after implementing QFD. A significant improvement in satisfaction levels can demonstrate the effectiveness of the QFD process.
Product Quality
Higher-quality products are another indicator of QFD’s effectiveness. By aligning engineering and manufacturing processes with customer requirements, QFD minimizes the risk of defects and improves overall product quality. Companies can measure the defect rates, return rates, and warranty claims to assess how QFD has impacted product quality.
Production Efficiency
Efficient processes often lead to faster production times, reduced waste, and lower costs. Implementing QFD can streamline operations, ensuring that manufacturing processes are tailored to produce the desired product efficiently. Companies can measure lead times, production costs, and waste reduction to evaluate the impact of QFD on production efficiency.
How to Maximize QFD Results
Effective implementation of QFD requires careful planning and execution. Here are a few ways to maximize the results:
Involve Cross-Functional Teams
One of the strengths of QFD is its ability to bring together different departments within an organization. Involving cross-functional teams ensures that various perspectives are considered, leading to more comprehensive solutions. Make sure to include representatives from marketing, engineering, production, and quality assurance to create a well-rounded QFD process.
Conduct Thorough Customer Research
The foundation of QFD lies in understanding customer needs. Conducting detailed customer research is crucial for identifying exact requirements and preferences. Use surveys, focus groups, and direct interviews to gather comprehensive data, which will form the basis of your QFD process.
Focus on Critical-to-Quality (CTQ) Elements
Not all customer requirements carry the same weight. Some are more critical to the customer’s perception of quality than others. Identifying and prioritizing these Critical-to-Quality (CTQ) elements ensures that the most important features are the focus of your product development process.
Use Robust QFD Software
Software tools can simplify the QFD process, making it easier to create and analyze the intricate matrices involved. There are various QFD software solutions available that offer features like matrix generation, data analysis, and collaborative workspaces. Utilizing these tools can streamline your QFD efforts and improve accuracy.
Ongoing Training and Development
The QFD process can be complex, requiring specialized skills and knowledge. Regular training sessions and workshops can help improve the team’s understanding and execution of QFD principles. Keeping the team updated on the latest advancements and methodologies ensures that your QFD process remains effective over time.
Continual Improvement
Finally, the effectiveness of QFD can be maximized through a commitment to continual improvement. Collect feedback on the QFD process itself and identify areas for enhancement. Updating and refining the QFD process based on lessons learned will yield better outcomes in future projects.
Real-World Applications of QFD
Numerous companies have successfully implemented QFD to improve their manufacturing processes. Toyota, for instance, has been a long-time proponent of QFD, using it to enhance product design and meet customer expectations. The company’s systematic approach to integrating QFD in its processes has been a key contributor to its reputation for high-quality, reliable vehicles.
Similarly, tech companies like Apple have embedded QFD into their development processes. By closely aligning product features with customer desires, Apple consistently delivers products that resonate well with users. The company’s focus on quality and user satisfaction can be attributed to its effective use of QFD principles.
Quality Function Deployment (QFD) is a powerful tool for ensuring that customer needs are translated into meaningful technical and operational requirements in manufacturing. By measuring its effectiveness through customer satisfaction, product quality, and production efficiency, companies can gain valuable insights into their processes. To maximize the benefits, involve cross-functional teams, conduct thorough customer research, focus on critical-to-quality elements, use robust software, invest in ongoing training, and commit to continual improvement. Real-world examples from leading companies like Toyota and Apple underscore the effectiveness of QFD in achieving manufacturing excellence. Implementing QFD conscientiously can yield significant improvements in both product and process quality, helping your organization stay competitive in today’s ever-evolving market.
資料ダウンロード
QCD調達購買管理クラウド「newji」は、調達購買部門で必要なQCD管理全てを備えた、現場特化型兼クラウド型の今世紀最高の購買管理システムとなります。
ユーザー登録
調達購買業務の効率化だけでなく、システムを導入することで、コスト削減や製品・資材のステータス可視化のほか、属人化していた購買情報の共有化による内部不正防止や統制にも役立ちます。
NEWJI DX
製造業に特化したデジタルトランスフォーメーション(DX)の実現を目指す請負開発型のコンサルティングサービスです。AI、iPaaS、および先端の技術を駆使して、製造プロセスの効率化、業務効率化、チームワーク強化、コスト削減、品質向上を実現します。このサービスは、製造業の課題を深く理解し、それに対する最適なデジタルソリューションを提供することで、企業が持続的な成長とイノベーションを達成できるようサポートします。
オンライン講座
製造業、主に購買・調達部門にお勤めの方々に向けた情報を配信しております。
新任の方やベテランの方、管理職を対象とした幅広いコンテンツをご用意しております。
お問い合わせ
コストダウンが利益に直結する術だと理解していても、なかなか前に進めることができない状況。そんな時は、newjiのコストダウン自動化機能で大きく利益貢献しよう!
(Β版非公開)