- お役立ち記事
- Mold Design and Molding Conditions to Minimize Weld Lines
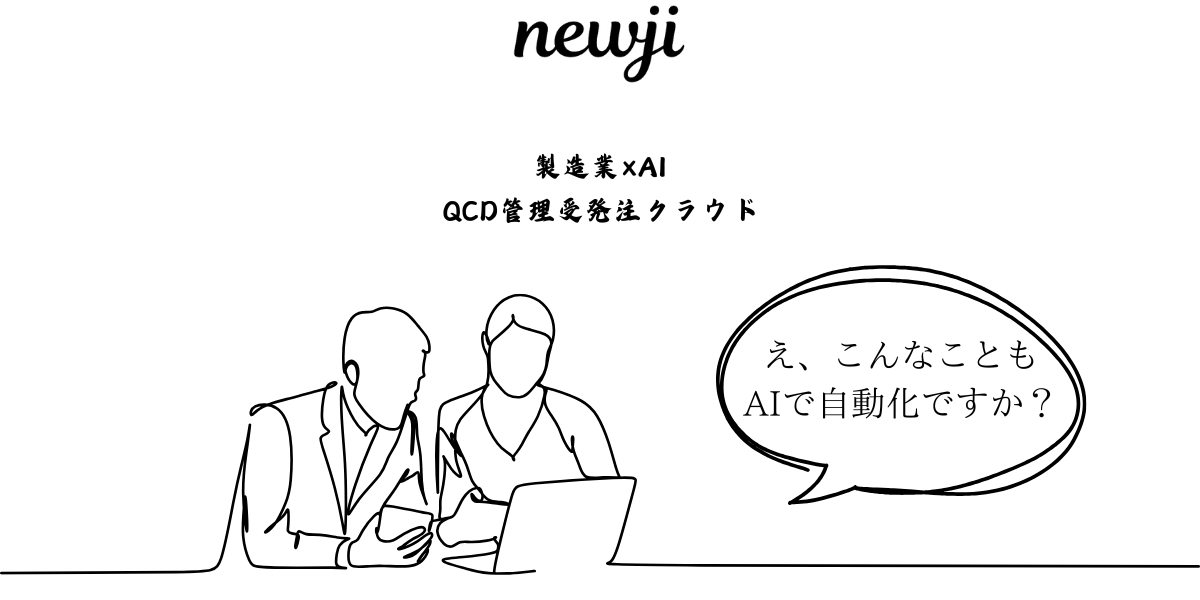
Mold Design and Molding Conditions to Minimize Weld Lines
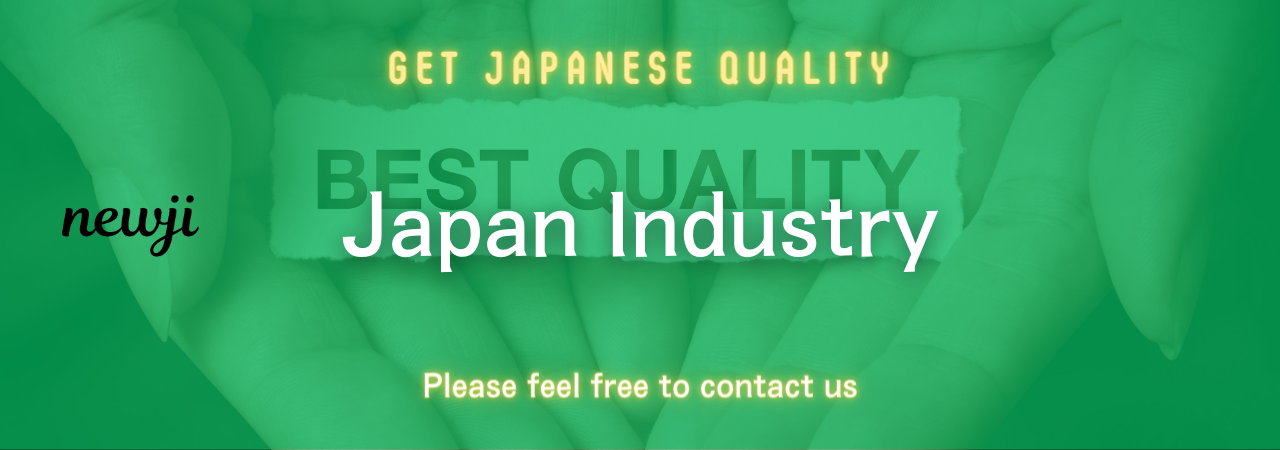
Mold design and molding conditions play a crucial role in minimizing weld lines, which are a common issue in the production of plastic parts.
Understanding the intricacies of these elements not only ensures better product quality but also enhances the efficiency of the manufacturing process.
Let’s delve into some key strategies to reduce weld lines through effective mold design and optimal molding conditions.
目次
Understanding Weld Lines in Molding
Before exploring the strategies, it’s essential to understand what weld lines are.
Weld lines, also known as knit lines, occur when two or more flow fronts in the molten plastic meet during the molding process.
These lines can weaken the structure of the part, leading to potential failures and aesthetic defects.
The occurrence of weld lines can be attributed to various factors, such as the part’s geometry, the type of material being used, and the conditions under which the molding is conducted.
Awareness of these factors can significantly help in designing molds and setting conditions to minimize these defects.
Impact of Mold Design on Weld Lines
Optimizing Gate Location
The position of the gate, where the molten plastic enters the mold, is crucial in determining the flow pattern of the material.
Optimal placement of gates can help in preventing the flow fronts from meeting, thereby reducing the chance of forming weld lines.
Gates should be positioned so that the flow path of the plastic avoids areas where weld lines are likely to be visible or affect functionality.
Additionally, multiple gates can be used to control the flow direction and merge points.
Designing for Uniform Wall Thickness
Ensuring uniform wall thickness across the part design can also reduce the formation of weld lines.
Variable thickness can lead to irregular flow and cooling rates, increasing the likelihood of weld lines.
Designing the part with consistent wall thickness allows for a steady flow of material, which in turn reduces flow interruptions and minimizes weld lines.
Using Proper Venting
Mold venting is an often-overlooked aspect that can significantly impact weld lines.
Trapped air in the mold can interfere with the flow of the plastic and lead to imperfect weld lines.
Incorporating vents strategically can allow air to escape, ensuring a smoother flow of material and reducing the formation of weld lines.
Proper vent design can drastically improve the quality of the final product by allowing for better flow and fill.
Molding Conditions to Minimize Weld Lines
Adjusting Injection Speed and Pressure
The speed and pressure at which material is injected into the mold are critical parameters in managing weld lines.
A slower injection speed can sometimes alleviate issues of weld lines by allowing the plastic to fill the mold more uniformly.
However, too slow an injection speed can also cause other defects, so balance is key.
Adjusting the pressure can also ensure that the material flows correctly, reducing areas where flow front intersections might occur.
Optimizing Melt Temperature
The temperature of the molten plastic can have a profound effect on the formation of weld lines.
A higher melt temperature can improve the flow of the material, helping it to knit together more effectively when flow fronts meet.
However, operating at excessively high temperatures can degrade the material, so it’s crucial to find an optimum temperature that permits smooth flow without compromising material integrity.
Managing Mold Temperature
Consistent mold temperature aids in reducing weld lines by ensuring that the material cools uniformly as it fills the mold.
Mismatched mold temperatures can result in sections of material cooling too quickly or slowly, which can exacerbate weld line issues.
Employing mold temperature controls and uniform heating can lead to more consistent cooling, enhancing the weld lines’ quality.
Material Selection and Its Influence
The choice of material can significantly influence the likelihood and severity of weld lines.
Some materials, like filled or reinforced plastics, are more susceptible to weld lines due to their flow characteristics.
Choosing a material with better flow properties or using additives to help with flow can assist in reducing weld lines.
Additionally, modifying the viscosity of the resin by using the right grades and blends can further optimize the flow and reduce weld line formation.
Simulation Analysis for Weld Line Prediction
Before proceeding to production, simulation software can be an invaluable tool for predicting where weld lines might occur.
Using computer simulations to model how the material will fill the mold can provide critical insights and allow engineers to tweak the design or conditions to address potential issues before they arise.
Simulation analysis not only helps to identify and solve weld line issues but can also be beneficial in optimizing other production parameters, ultimately saving time and resources.
Conclusion
Minimizing weld lines involves a holistic approach that includes thoughtful mold design, careful consideration of molding conditions, material selection, and even simulation analysis.
By implementing an optimal combination of these strategies, manufacturers can significantly enhance the overall quality and durability of their plastic components while reducing waste and improving production efficiency.
Through ongoing development and responsiveness to specific project requirements, the chances of weld lines can be minimized, leading to superior product outcomes.
資料ダウンロード
QCD調達購買管理クラウド「newji」は、調達購買部門で必要なQCD管理全てを備えた、現場特化型兼クラウド型の今世紀最高の購買管理システムとなります。
ユーザー登録
調達購買業務の効率化だけでなく、システムを導入することで、コスト削減や製品・資材のステータス可視化のほか、属人化していた購買情報の共有化による内部不正防止や統制にも役立ちます。
NEWJI DX
製造業に特化したデジタルトランスフォーメーション(DX)の実現を目指す請負開発型のコンサルティングサービスです。AI、iPaaS、および先端の技術を駆使して、製造プロセスの効率化、業務効率化、チームワーク強化、コスト削減、品質向上を実現します。このサービスは、製造業の課題を深く理解し、それに対する最適なデジタルソリューションを提供することで、企業が持続的な成長とイノベーションを達成できるようサポートします。
オンライン講座
製造業、主に購買・調達部門にお勤めの方々に向けた情報を配信しております。
新任の方やベテランの方、管理職を対象とした幅広いコンテンツをご用意しております。
お問い合わせ
コストダウンが利益に直結する術だと理解していても、なかなか前に進めることができない状況。そんな時は、newjiのコストダウン自動化機能で大きく利益貢献しよう!
(Β版非公開)